Firma Risomat z siedzibą w Baienfurt (Niemcy) buduje specjalistyczne maszyny do produkcji silników elektrycznych, generatorów, pomp, komponentów samochodowych i silników liniowych, będąc jednym z europejskich liderów technologicznych w tej dziedzinie. Linia z suwnicą bramową została zaprojektowana na potrzeby elastycznej i wydajnej produkcji stojanów o różnych średnicach i długościach – w małych ilościach.
Nowa koncepcja produkcji stojanów do silników elektrycznych realizowana w tej firmie opiera się na zastosowaniu opatentowanej suwnicy bramowej. Ten rodzaj suwnicy umożliwia realizację funkcji wymaganych na różnych stanowiskach pracy, takich jak obracanie, odwracanie, zaciskanie i pozycjonowanie, a wyposażenie suwnicy we własne narzędzia umożliwia jej również wykonywanie zadań będących częścią procesu technologicznego.
- Upraszcza to projektowanie stacji roboczych i sprawia, że cała linia jest znacznie bardziej elastyczna - twierdzi dyrektor zarządzający firmy Risomat, Hubert Halder, opisując kluczową cechę nowej linii produkcyjnej.
OKREŚLENIE POTRZEB I DOBÓR DOSTAWCY
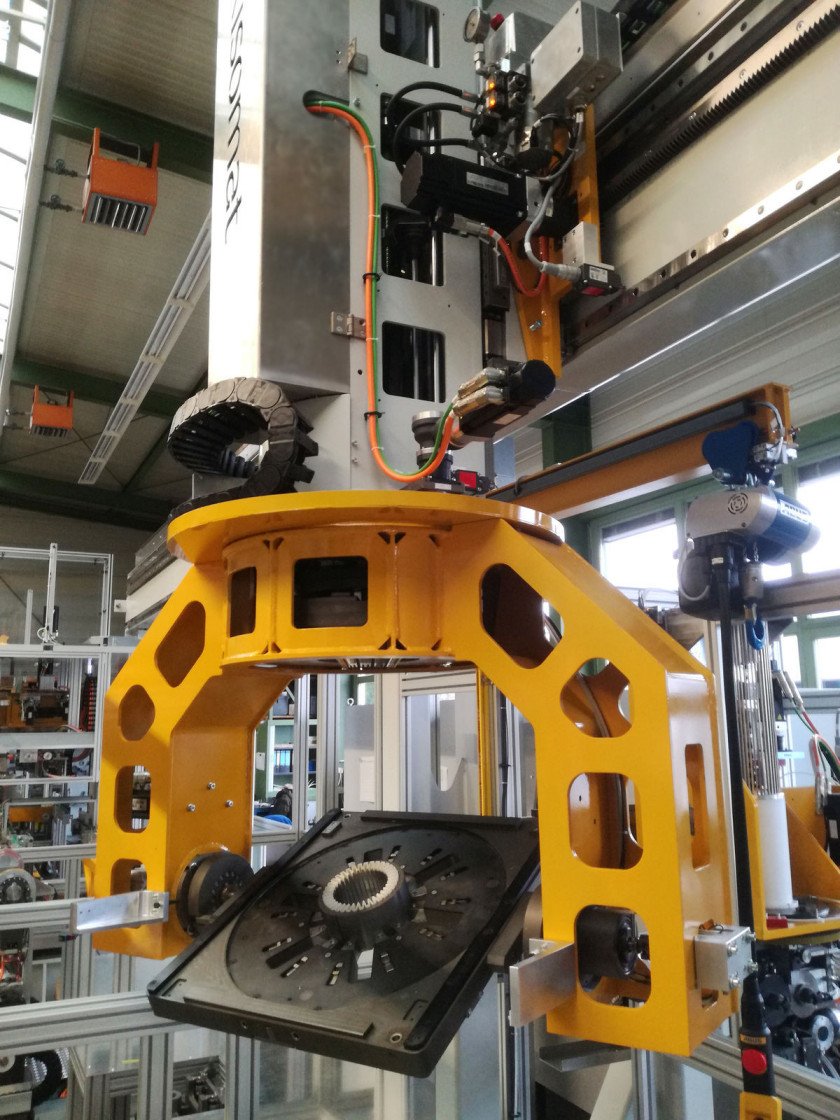
Zastosowanie suwnicy bramowej przyniosło firmie Risomat wiele korzyści. Pełne wykorzystanie możliwości systemu wymagało jednak stworzenia inteligentnego rozwiązania kwestii bezpieczeństwa.
- Linie te zostały zaprojektowane w taki sposób, aby moduły technologiczne, które nie są w danej chwili obsługiwane przez suwnicę bramową, mogły być wykorzystywane jako stanowiska pracy ręcznej - wyjaśnia Halder. - Wymaga to podziału linii na strefy bezpieczeństwa i uwzględnienia pozycji suwnicy bramowej, tak aby zatrzymanie awaryjne w jednej strefie nie spowodowało zatrzymania całej maszyny. -
Firma Risomat od wielu lat korzysta z rozwiązań automatyki B&R, dlatego od początku realizacji projektu było jasne, że sterowniki dla nowej linii będą pochodzić z tego źródła. Do wdrożenia całego rozwiązania w zakresie sterowania maszynami i bezpieczeństwa został zaangażowany certyfikowany integrator B&R, firma Pantec Automation z siedzibą w Liechtensteinie ‒ producent systemów sterowania stosowanych w budowie maszyn i instalacji.
WYZWANIA W ZAKRESIE BEZPIECZEŃSTWA
Dynamiczne strefy bezpieczeństwa nie były jedynym wyzwaniem, przed którym stanęła firma.
- Ze względów technicznych musieliśmy wyposażyć zarówno suwnicę bramową, jak i moduły technologiczne w autonomiczne sterowniki PLC i sterowniki bezpieczeństwa. Oznaczało to konieczność ustanowienia wyższego poziomu komunikacji w zakresie bezpieczeństwa - wspomina Halder.
ZINTEGROWANA TECHNOLOGIA BEZPIECZEŃSTWA FIRMY B&R
Dla kierownika projektu Pantec, Floriana Hartmanna, kwestia komunikacji w zakresie bezpieczeństwa miała aspekt pragmatyczny.
- B&R oferuje kompletny zakres technologii sterowania i bezpieczeństwa, który doskonale nadaje się do tworzenia systemów modułowych - twierdzi Hartmann. Nawet w przypadku struktury hierarchicznej nigdy nie występują jakiekolwiek konflikty pomiędzy systemami, a wszystkie komponenty mogą być programowane za pomocą oprogramowania Automation Studio firmy B&R.
Sterownik bezpieczeństwa składa się z modułu bezpieczeństwa X20SL8100 SafeLOGIC oraz modułów bezpieczeństwa IP20 i IP67. Rozwiązanie B&R spełnia też wymagania PL e lub SIL 3. W suwnicy bramowej zastosowano również dwie bezpieczne osie, ponieważ pionowe i poziome położenie suwnicy ma wpływ na bezpieczeństwo pracy na poszczególnych stacjach. Inne urządzenia bezpieczeństwa wykorzystywane w zakładzie to kurtyny świetlne, skanery laserowe 2D oraz czułe na nacisk maty bezpieczeństwa.
WYZWANIE DYNAMICZNYCH STREF BEZPIECZEŃSTWA
Przy tak złożonej strukturze bezpieczeństwa zespół szybko zdał sobie sprawę, że klasyczny tekstowy opis logiki bezpieczeństwa nie sprawdza się. To było za mało, aby w pełni i przejrzyście dokonywać zapisu stanu alarmów systemu. Idealnym rozwiązaniem okazał się jednolity język modelowania (UML).
W oparciu o podejście UML opracowano trzyetapowy proces bezpieczeństwa: od zatwierdzonej koncepcji bezpieczeństwa do przetestowanego sterownika bezpieczeństwa. Proces ten jest bardzo przydatny, gdyż umożliwia opracowanie i udokumentowanie w przejrzysty sposób aplikacji bezpieczeństwa. Co więcej, funkcjonalność sterownika bezpieczeństwa może być bezproblemowo testowana i dokumentowana podczas procesu akceptacji.
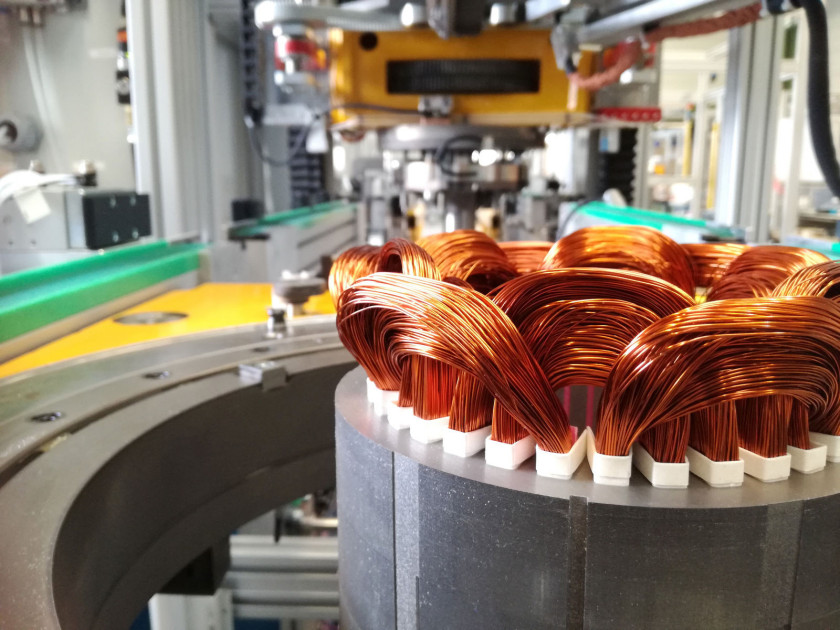
TRZY ETAPY PROCESU BEZPIECZEŃSTWA UML
I etap: komponenty bezpieczeństwa włączone do projektu elektrycznego są przedstawione w UML jako przypadki użycia. Następnie opracowywana jest logika bezpieczeństwa. Twórcy oprogramowania określają, który przypadek użycia prowadzi do danego stanu bezpieczeństwa. Ten krok wymaga ścisłej współpracy pomiędzy programistami, specjalistami ds. bezpieczeństwa i projektantami.
II etap: modelowana aplikacja bezpieczeństwa jest kodowana, a test akceptacyjny zostaje oparty bezpośrednio na przypadkach użycia. Oprócz logiki, testy akceptacyjne obejmują również cały sprzęt bezpieczeństwa i jego okablowanie.
III etap: przeprowadzane są testy akceptacyjne, a system bezpieczeństwa jest następnie zatwierdzany przez urzędnika ds. bezpieczeństwa.
KOLEJNE INNOWACJE I OPTYMALIZACJA W ZAKŁADZIE
Oprócz modelowania sterowników bezpieczeństwa za pomocą UML, firma Pantec Automation podjęła w trakcie opracowywania linii produkcyjnej stojanów dalsze działania innowacyjne na rzecz firmy Risomat. Jednym z istotnych kroków było opracowanie całkowicie modułowej struktury oprogramowania. Automatyczne generowanie kodu sterującego B&R umożliwiło znaczne skrócenie czasu i zmniejszenie wysiłku związanego z opracowaniem oprogramowania dla maszyny.
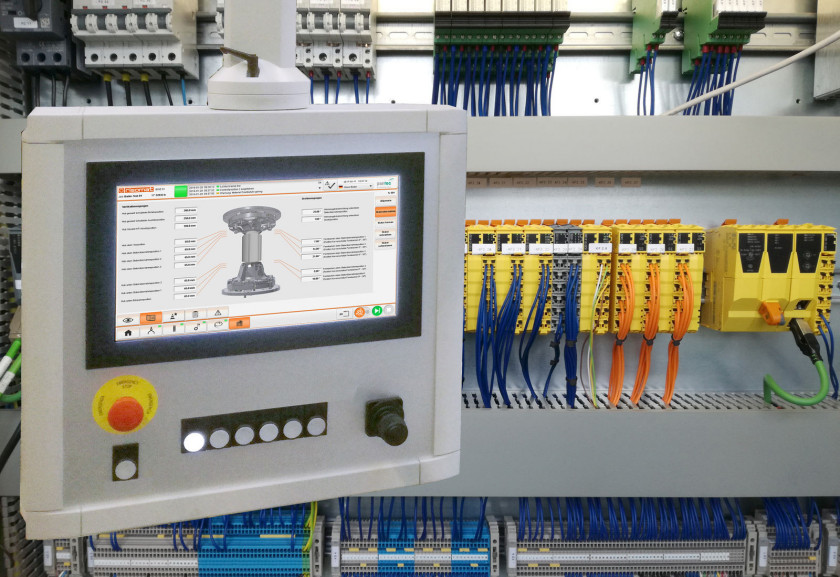
Ogólną wydajność systemu zwiększono dzięki przejściu na sterownik B&R Automation PC 2100. Interfejs HMI został zaś zmodernizowany i obecnie korzysta z panelu 15,4", z technologią połączeń SDL3 (Smart Display Link 3) firmy B&R. Ponadto, istniejąca koncepcja eksploatacji została poddana analizie użyteczności i zoptymalizowana. Wyniki włączono do wytycznych stylistycznych obowiązujących przy opracowywaniu przyszłych paneli operatorskich firmy Risomat.
B&R Automatyka Przemysłowa
www.br-automation.com