W celu zagwarantowania bezpieczeństwa funkcjonalnego kluczowe jest zatrzymanie systemu w momencie otwarcia bramki zabezpieczającej strefę zagrożenia. Stan takich bramek wykrywają czujniki bezpieczeństwa, które są często połączone szeregowo według standardowego schematu: wyjścia OSSD (Output Switching Signalling Device) jednego czujnika są podłączone do wejść następnego czujnika. Dotychczas do ustalenia tego, która bramka została otwarta, konieczne było pojedyncze dołączenie czujników do przekaźnika bezpieczeństwa, co generowało dodatkowe koszty oraz komplikowało instalację. Co więcej, takie podejście pozwalało na przesyłanie jedynie jednego bita danych, tj. stanu danego czujnika. Aby umożliwić wdrażenie bardziej elastycznych rozwiązań, powstało inteligentne rozwiązanie diagnostyczne Safety Device Diagnostic firmy Pilz, dzięki któremu można uzyskać dostęp zarówno do danych o statusie urządzenia, jak i jego konfiguracji. Zebranie i analiza danych o przyczynach przestojów pomaga podnieść produktywność, zaś wizualizacja statusu czujników ułatwia diagnostykę maszyny.
INTELIGENTNE CZUJNIKI ZAPEWNIAJĄ SZERSZY ZAKRES FUNKCJI
Ponieważ informacje diagnostyczne w tym przypadku mogą być przesyłane seriami po 300 bajtów, a nie tylko pojedynczymi bitami, jak to miało miejsce wcześniej, możliwe jest korzystanie z funkcji, które do tej pory były zarezerwowane dla bardzo złożonych czujników i programowalnych sterowników logicznych, np. przesyłanie indywidualnych numerów seryjnych, wersji urządzenia, jego aktualnego statusu, a także historycznych danych dotyczących awarii. Czujnik zapewnia dokładnie te dane i informacje, których aktualnie potrzebuje użytkownik. Na podstawie informacji diagnostycznych użytkownicy mogą na przykład wybierać między czujnikiem wysoko kodowanym i kodowanym. Oba zapewniają niezwykle wysoki poziom ochrony przed ingerencją. Jeśli użytkownik zdecyduje się na czujnik wysoko kodowany, zabezpieczenie będzie trwalsze i sztywno zaimplementowane.
MONITOROWANIE STATUSU – LOKALNIE I ZDALNIE
Dane mogą być pozyskiwane i przetwarzane za pośrednictwem magistrali Modbus lub Profibus, a w przyszłości także przez sieć Profinet lub Ethernet/IP. Następnie są one przejrzyście prezentowane na wyświetlaczu modułu magistrali Fieldbus, monitorze sterownika PLC lub – w przypadku web serwera – na ekranie komputera. Innymi słowy: dane są udostępniane zarówno operatorowi przy maszynie, jak i poprzez zdalny dostęp.
Rozwiązanie diagnostyczne jest skonfigurowane w taki sposób, aby możliwe było podłączenie do szesnastu czujników bezpieczeństwa bez względu na architekturę obwodów bezpieczeństwa. Urządzenie SDD może być używane z czujnikami bezpieczeństwa bez względu na miejsce ich montażu, również w przypadku, gdy są one podłączone do kilku przekaźników bezpieczeństwa. W ten sposób zarządzanie wszystkimi czujnikami może być prowadzone centralnie z poziomu bramki nadrzędnej w systemie diagnostycznym, co znacznie ułatwia monitorowanie wielu urządzeń bezpieczeństwa. W zależności od konfiguracji sieci bramka nadrzędna może być podłączona albo przez protokół DHCP (Dynamic Host Configuration Protocol), albo przez wcześniej zdefiniowany adres IP. Przekłada się to na dużą swobodę integracji istniejącego rozwiązania z siecią.
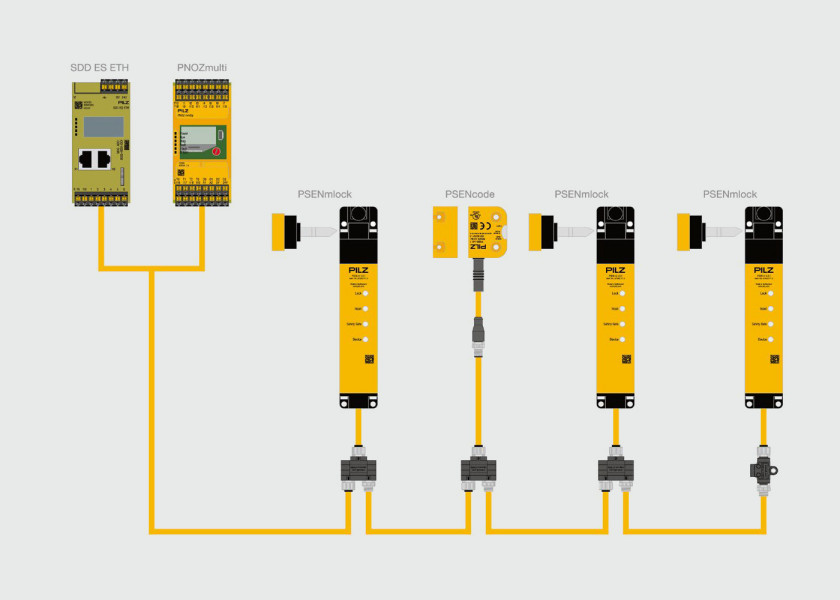
JAKIE INFORMACJE DIAGNOSTYCZNE MOŻNA REJESTROWAĆ?
Po pierwsze: stan czujników bezpieczeństwa oraz stan ich wejść i wyjść. Możliwe jest również odczytywanie ostrzeżeń o przepięciach lub spadkach napięcia, które mogą wystąpić szczególnie w przypadku długich kabli. Jest to możliwe ze względu na zdolność systemu do poprawnej pracy przy długości przewodów sięgającej 900 metrów. Dzięki temu możliwe jest wykorzystanie konfiguracji jednokablowej w dotychczas niespotykanych miejscach: magazynach wysokiego składowania, centrach logistycznych, itd.
Istnieje możliwość wywołania danych urządzenia, takich jak numer artykułu, wersja i numer seryjny produktu, co znacznie ułatwia wymianę w przypadku awarii. Informacje te mogą również być pomocne w szybkim zlokalizowaniu uszkodzonego czujnika bezpieczeństwa w skomplikowanych obiektach. Ponadto moduł magistrali Fieldbus dokumentuje wszystkie zmiany stanu, nawet po zresetowaniu napięcia. Umożliwia to wyraźną identyfikację błędów, co nie jest możliwe w oparciu jedynie na diodch LED czujników bezpieczeństwa. Jest to o tyle ważne, że podczas prac naprawczych mogą łatwo wystąpić inne błędy, np. w wyniku odłączenia wtyczek, co uniemożliwia wykrycie pierwotnego błędu.
NASZE ROZWIĄZANIE DIAGNOSTYCZNE SPRAWIA, ŻE SYSTEMY MOGĄ BYĆ SZYBCIEJ PONOWNIE URUCHAMIANE
Dodatkową korzyścią jest możliwość bezpośredniego włączenia świateł ostrzegawczych w szafie sterowniczej, np. w przypadku, gdy czujnik bezpieczeństwa wykryje otwarcie bramki bezpieczeństwa. Ta metoda nadal znajduje szerokie zastosowanie w obszarze bezpiecznej automatyzacji. Moduł magistrali Fieldbus obsługuje bezpośrednie włączanie do sześciu lamp, co ułatwia prace związane z projektowaniem i programowaniem wizualizacji. Powoduje to, że operator instalacji może korzystać z prostego okablowania, ale nadal dokładnie wie, której bramki dotyczy problem.
DOKUMENTOWANIE ZMIAN POZWALA OGRANICZYĆ PRZESTOJE
Ponieważ urządzenie SDD umożliwia gromadzenie wielu różnych danych diagnostycznych, może być również wykorzystywane do planowania konserwacji w predykcyjnym utrzymaniu ruchu, które staje się coraz popularniejsze wraz z rozwojem koncepcji Przemysłu 4.0. Dotyczy to nie tylko terminowej wymiany zużytych części, ale także utrzymania bezpieczeństwa operacyjnego. Do tej pory w razie zgłoszenia problemu po wielu latach eksploatacji producentowi trudno było ustalić, co w tym czasie zmieniło się w maszynie. Korzystając z danych przechowywanych w urządzeniu SDD, możliwe jest porównanie oryginalnego stanu ze stanem bieżącym bez dodatkowego sprzętu, który w innym przypadku byłby potrzebny na poziomie sterowania.
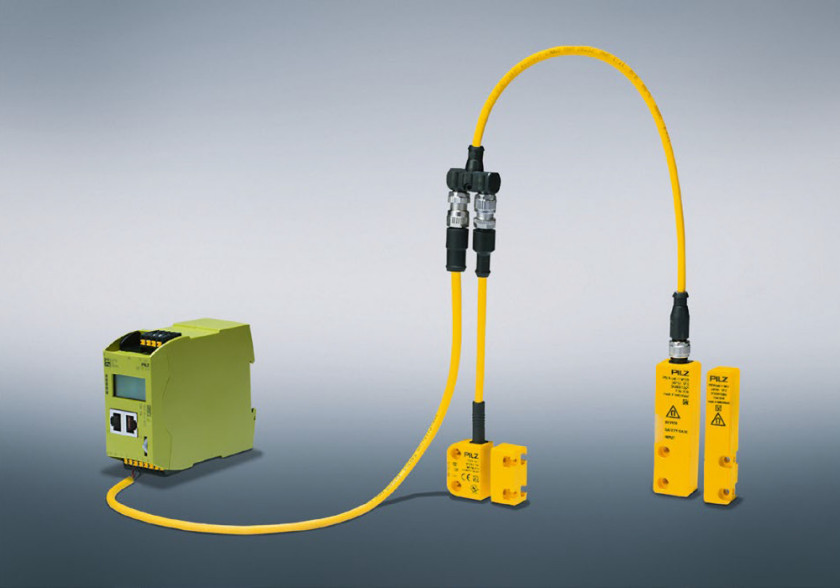
ROZWIĄZANIE DIAGNOSTYCZNE WSPIERA PODEJŚCIE MODUŁOWE
Dzięki połączeniu łańcuchowemu diagnostyki operator może stosunkowo łatwo dodać kolejny moduł. W procesie produkcyjnym, zawierającym również etapy konfekcjonowania i foliowania, nie jest wymagane wprowadzenie ani nowego okablowania, ani modyfikacji w szafie sterowniczej, ani wreszcie dodatkowych urządzeń zabezpieczających. Oprócz obwodu elektrycznego wymagane jest jedynie zainstalowanie czujników bezpieczeństwa dla prawej i lewej bramki bezpieczeństwa każdego modułu. Czujniki te powinny zostać podłączone za pośrednictwem rozdzielacza do ostatniego czujnika w łańcuchu. Dodatkowy moduł magistrali Fieldbus jest konieczny tylko wtedy, gdy do rozwiązania diagnostycznego podłączonych jest już 16 czujników. Jednak w większości przypadków połączenie szeregowe obejmuje nie więcej niż sześć, osiem lub najwyżej dziesięć czujników, a wówczas istniejąca konfiguracja jest w zupełności wystarczająca.
ALTERNATYWNY MODEL: IO-LINK SAFETY
Pełny zakres funkcji urządzenia SDD jest dostępny dopiero w przypadku wykorzystania wszystkich elementów. IO-Link Safety to alternatywny model, który znajduje się obecnie w fazie opracowywania. Gwarantuje on wzajemną kompatybilność do poziomu samych czujników, dzięki czemu może współpracować na wszystkich poziomach z urządzeniami bezpieczeństwa różnych producentów. Dane są bezpiecznie przesyłane z czujnika do sterownika PLC, co otwiera nowe możliwości aplikacji. W przypadku zastosowania rozwiązania IO-Link Safety za przełączanie odpowiada sterownik PLC, przez co emulowane są drogie architektury bezpieczeństwa i powstają nowe wzajemne zależności między czujnikiem a sterownikami PLC (np. w razie wymiany). Ponadto model ten opiera się na połączeniach point-to-point, tj. w układzie gwiazdy, w instalacji polowej lub w szafie sterowniczej. Ostatecznie koszty instalacji i prac konstrukcyjnych okazują się znacznie wyższe niż w przypadku zastosowanie urządzenia SDD. Wynika to nie tylko z większych wymogów dotyczących okablowania, ale także konieczności zastosowania bezpiecznych sterowników PLC w celu oceny danych z czujników. W zależności od aplikacji głównym kryterium wyboru systemu będzie stosunek kosztów do korzyści. IO-Link Safety to wciąż wizja przyszłości. Tymczasem rozwiązanie diagnostyczne SDD może być wykorzystywane już dziś.
Rozwiązanie Safety Device Diagnostics dzięki szczegółowej i bardziej wyczerpującej diagnostyce znacząco zmniejsza liczbę zgłoszeń serwisowych. Zarówno na miejscu, jak i w ramach zdalnego dostępu dostarczane są dokładne informacje. Oprócz tego przemyślana jednokablowa konfiguracja przesuwa granice połączenia szeregowego: innowacyjne połączenie szeregowe czujników bezpieczeństwa i bezpośrednia ocena danych z czujnika nie tylko powodują znaczący wzrost dostępności, ale także dzięki modułowej koncepcji zapewniają rozwiązanie diagnostyczne adekwatne do potrzeb fabryki przyszłości.
Pilz Polska
tel. 22 884 71 00
info@pilz.pl
www.pilz.pl