Strategie konserwacji
Jednym z najważniejszych aspektów maksymalizacji czasu pracy linii jest ustalenie odpowiednich strategii konserwacji. Zazwyczaj inżynierowie stosują dwa podejścia – reaktywne oraz zapobiegawcze. Oba mają swoje zalety i ograniczenia, które powinny być wzięte pod uwagę przy decyzji, jaką strategię powinno się obrać.
W ramach konserwacji reaktywnej maszyny są naprawiane dopiero w momencie wystąpienia awarii, a wymiana poszczególnych komponentów następuje wtedy, gdy przestają one działać. Taki typ konserwacji wydaje się najtańszy, jednak inżynier nie wie, kiedy awaria nastąpi. W dużym zakładzie prawdopodobieństwo, że jakiś element wyposażenia będzie wymagać w danym momencie jakiegoś rodzaju działań konserwacyjnych, jest bardzo duże. W wyniku nieplanowanego przestoju związanego z takimi pracami produktywność i przepustowość linii może się znacznie obniżyć, co może słono kosztować. Sytuacja jeszcze się pogarsza, jeśli dana część zamienna nie jest dostępna od ręki. W takim wypadku przestój może przedłużyć się, powodować większe koszty, a nawet – działając z efektem domina – generować opóźnienia na dalszych etapach produkcji.
Konserwacja zapobiegawcza, w przeciwieństwie do konserwacji reaktywnej, jest podejściem planowanym. Obejmuje ona regularne kontrole sprzętu, podczas których można wychwycić zbliżające się zużycie części przed powstaniem kosztownych uszkodzeń. Taka strategia pozwala inżynierom zaplanować konserwację z odpowiednim wyprzedzeniem i zadbać o dostępność części zamiennych. Prowadzenie zaplanowanej, rutynowej konserwacji w oparciu na średnich cyklach życia maszyn zmniejsza również koszty napraw awaryjnych i wydłuża okres eksploatacji urządzeń o krytycznym znaczeniu dla zakładu. W przeciwieństwie do konserwacji reaktywnej, podejście zapobiegawcze poprawia wydajność, ale za to generuje koszty związane z wcześniejszą wymianą części.
Nowoczesne technologie automatyki, które wykorzystują przemysłowy Internet Rzeczy (IIoT) i praktyki Przemysłu 4.0, umożliwiają konserwację prognostyczną – znaną również jako konserwacja inteligentna (fot. 1). Podejście to opiera się na czujnikach umieszczonych na krytycznych komponentach i systemach, które w sposób ciągły monitorują stan urządzeń. Dzięki wdrożeniu strategii prognostycznej w całym zakładzie, inżynierowie mogą śledzić w czasie rzeczywistym wydajność każdej maszyny i prognozować, kiedy i gdzie niezbędne będzie przeprowadzenie konserwacji. Wydłuża to również cykl życia i czas sprawności maszyn, umożliwiając inżynierom bardziej efektywne zarządzanie zespołami serwisowymi, częściami zamiennymi i daje związane z tym oszczędności kosztów.
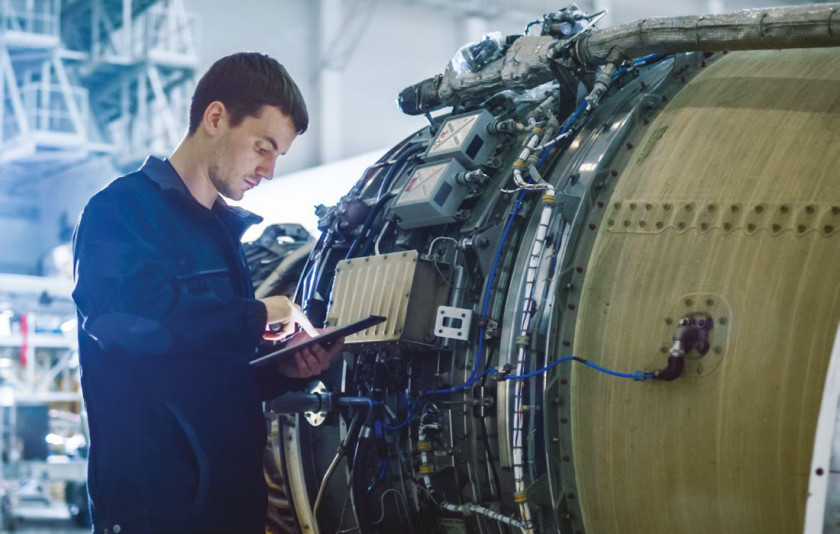
Zapasowe źródła zasilania
Zapasowe źródła zasilania w formie zasilaczy bezprzerwowych (UPS) są nieodzowne w zakładach przemysłowych, zwłaszcza jeśli warunki zasilania są niepewne. Nagłe przerwy w zasilaniu, zaniki lub spadki napięcia sieciowego mogą prowadzić do nieplanowanych przestojów. Zasilacze UPS, na przykład produkowane przez firmę Eaton, pomagają chronić systemy wykorzystywane do krytycznych zastosowań przed przestojem, utratą czy uszkodzeniem danych. Są one powszechnie używane do zasilania wrażliwych komponentów automatyki i sterowania, stacji roboczych, centrów zarządzania procesami technologicznymi lub do przemysłowego przetwarzania danych. Pozwalają one na bezpieczne wyłączanie linii i urządzeń, chroniąc jednocześnie kluczowe dane przed nagłą awarią zasilania dzięki temu, że gwarantują czas niezbędny do stworzenia ich kopii zapasowej online.
Dobór niezawodnego sprzętu
Nie jest zaskoczeniem, że kluczowe znaczenie dla maksymalizacji czasu pracy ma ogólna niezawodność sprzętu. Wybór sprzętu klasy handlowej, który nie jest odpowiedni do danego celu lub środowiska pracy, jest niepraktyczny. Wraz z coraz powszechniejszym stosowaniem IIoT zaleca się wybór wytrzymałego komputera, który może przetwarzać duże zbiory danych i jest odporny na trudne warunki środowiskowe.
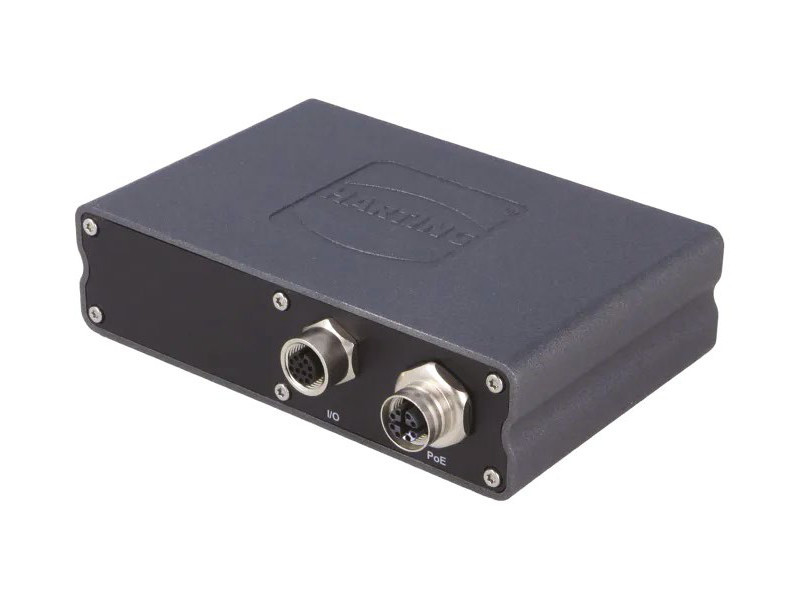
Na przykład komputer przemysłowy HARTING (zdj. 2) charakteryzuje się klasą szczelności IP67, która zapewnia doskonałą ochronę przed działaniem pyłu i wilgoci. Wyposażony w port Ethernet i 32 GB pamięci flash, dostarczany jest z fabrycznie zainstalowanymi różnymi systemami operacyjnymi i innymi przydatnymi aplikacjami.
Odpowiednie narzędzia
Oprócz właściwej konserwacji, do zminimalizowania czasu przestoju niezbędne są również odpowiednie narzędzia. Weźmy choćby zwykły śrubokręt – zamiast niego można zaopatrzyć się w elektronarzędzie, które pozwoli inżynierom na szybsze i sprawniejsze wykonanie pracy. Posiadając w zestawie do konserwacji wszystkie potrzebne narzędzia, przyrządy pomiarowe oraz inne niezbędne przedmioty, można zaoszczędzić cenny czas (zdj. 3).
Części zamienne
Dostęp do odpowiednich części zamiennych jest kluczowy, aby zapewnić szybką i sprawną wymianę komponentów. Do tego służy między innymi interfejs programowania aplikacji (API) wykorzystywany przez TME. Jest to łatwy w użyciu i nawigacji system składania zamówień, pozwalający inżynierom na optymalizację całego procesu. Przyjazne dla użytkownika narzędzie oznacza, że inżynierowie spędzają mniej czasu na wyborze odpowiedniej części do naprawy maszyny, dzięki czemu mogą szybko przywrócić sprawność zautomatyzowanej linii produkcyjnej. TME jest oficjalnym dystrybutorem wielu wiodących marek – są to, między innymi, Eaton, Panasonic, HARTING i Omron. API to cyfrowy katalog zawierający dane tysięcy części elektronicznych, jest dostępny w wielu językach. Ceny produktów są wyrażone w wielu walutach. Stany magazynowe są aktualizowane w czasie rzeczywistym, dzięki czemu inżynierowie wiedzą dokładnie, ile części jest aktualnie dostępnych, a ceny każdego produktu mogą również obejmować indywidualne rabaty.
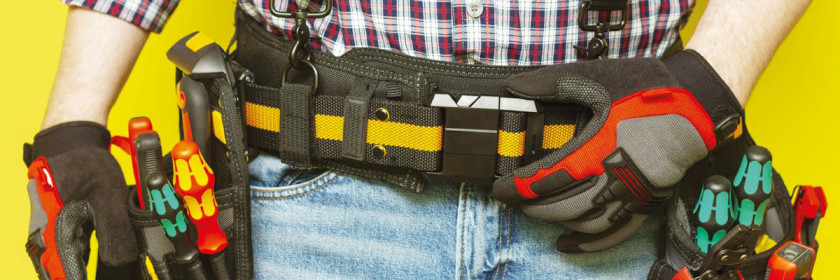
Podsumowanie
Utrzymanie ruchu jest kluczowe dla zachowania konkurencyjności nowoczesnych zautomatyzowanych linii produkcyjnych i zapewnienia, że działają one w sposób jak najbardziej efektywny i generują odpowiedni zysk dla przedsiębiorstwa. Dystrybutorzy ze sprawnie działającą siecią dostaw, tacy jak TME, zapewniają wysoką dostępność i szybkie dostawy potrzebnych elementów i materiałów eksploatacyjnych. Umożliwienie bezpośredniego zamawiania kluczowych komponentów za pomocą interfejsu programowania aplikacji (API) pozwala jeszcze bardziej zwiększyć wydajność i skrócić czas przestoju. Korzyści te mogą być jeszcze większe, jeśli wdroży się konserwację prognostyczną. Skuteczny proces minimalizujący czas przestoju przyspieszy zwrot z kosztownych inwestycji.
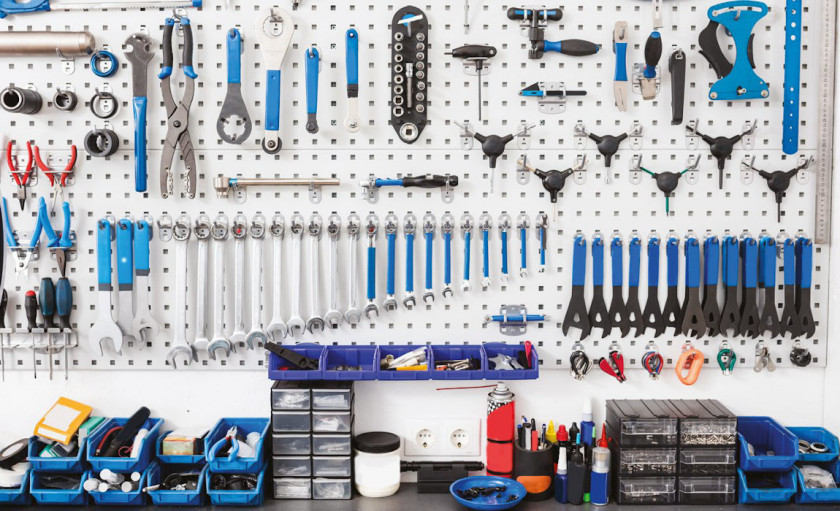
Więcej informacji na temat TME i narzędzia API można znaleźć na stronie: developers.tme.eu
TME
www.tme.eu