Przykładem są pomiary temperatury w dużych zbiornikach, w których magazynuje się płynne lub sypkie substancje i w tych, w których zachodzą różne reakcje chemiczne, wykorzystywanych m.in. w rolnictwie, branży farmaceutycznej, chemicznej czy naftowej (reaktory, kolumny rektyfikacyjne). Rozkład wartości tej wielkości w całej objętości zasobnika jest w nich najczęściej nierównomierny, dlatego, żeby móc ocenić stan zawartości kontenera albo przebieg zachodzących w nim procesów, trzeba znać temperaturę w więcej niż w jednym punkcie. Pozwala to na wykrywanie gorących miejsc, które mogą świadczyć o anomaliach i/albo wyznaczanie profili temperatury w głąb zbiornika czy panującej w nim temperatury średniej.
W tym zadaniu najlepiej sprawdzają się czujniki wielopunktowe, mierzące temperaturę w kilku–kilkudziesięciu miejscach jednocześnie. Przyrządy pomiarowe tego typu zbudowane są z wielu sensorów, termopar lub czujników rezystancyjnych, umieszczonych we wspólnej obudowie. Kompaktowa konstrukcja ma wiele zalet. Przede wszystkim pozwala na wprowadzenie do kontenerów, które mają ograniczoną liczbę wejść, wszystkich sensorów razem. Ponadto zapewnia redundancję oraz zmniejsza koszty – jeden przyrząd pomiarowy może okazać się tańszy niż wiele pojedynczych czujników.
Sensory wielopunktowe
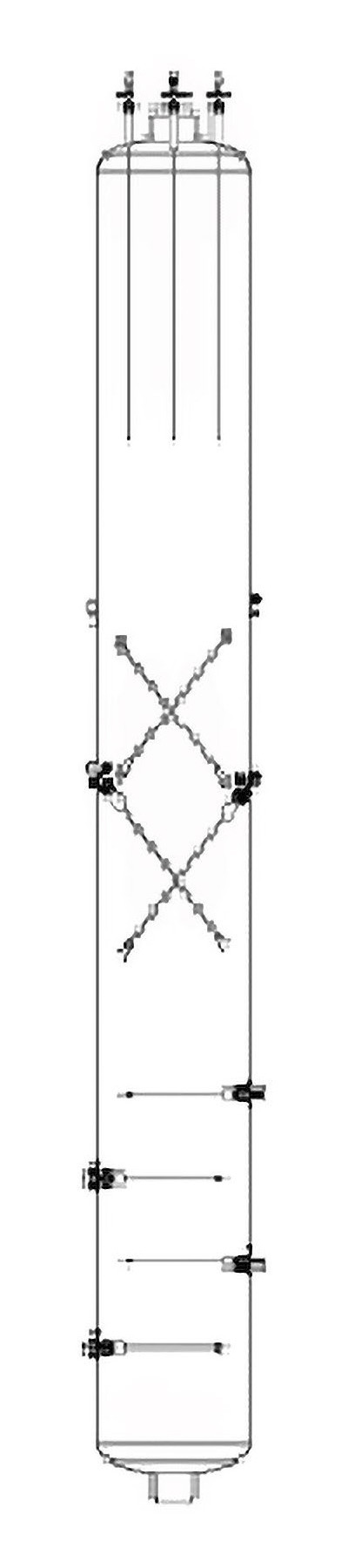
Czujniki wielopunktowe umieszcza się w sztywnych osłonach termometrycznych. Montuje się je w poprzek zbiornika, pionowo od góry do dołu lub pod kątem. Jeśli osłona rozciąga się na szerokość kontenera, po przeciwnej stronie otworu wlotowego bywa przykręcana do wspornika. Sensory w sztywnych osłonach są mocowane za pomocą kołnierzy. Wyprowadzenie kabli poszczególnych czujników jest uszczelnione, co zapobiega wydostawaniu się płynów i gazów procesowych do skrzynki przyłączeniowej. Sensory wielopunktowe są zazwyczaj konstruowane tak, żeby bez konieczności demontażu całej osłony można było wymienić każdy element pomiarowy (wraz z okablowaniem) niezależnie, wyjmując go przez kołnierz.
Oprócz czujników w sztywnych osłonach dostępne są także wielopunktowe sensory bez nich. Ich elementy pomiarowe, które są umieszczone w elastycznych prowadnicach, są złączone na jednym końcu w wiązkę. Dzięki temu rozchodzą się w zbiorniku jak macki ośmiornicy. Brak wspólnej obudowy skraca czas reakcji na zmiany temperatury, uzyskuje się to jednak kosztem trudności w wymianie czujników i ich ograniczonej ochrony przed czynnikami niszczącymi.
Materiały osłon termometrycznych
Te ostatnie to ekstremalnie wysokie temperatury i czynniki mechaniczne. Wytrzymałość materiału osłony na takie warunki jest kluczowym kryterium jej doboru w zależności od warunków pracy. Wybierać można spośród metali i niemetali.
Przykładem drugich jest ceramika. Osłony termometryczne wykonane z tego materiału są odporne na temperatury przekraczające +1600°C. Charakteryzują się dobrą wytrzymałością na ścieranie. Z drugiej strony ceramika jest krucha i mniej odporna na obciążenia mechaniczne niż większość metali. Ważną jej zaletą jest natomiast nieprzepuszczalność dla gazów.
Metalowe osłony termometryczne, w porównaniu z ceramicznymi, wyróżnia lepsza wytrzymałość mechaniczna, ale mają zwykle niższą temperaturę pracy oraz mniejszą odporność na ścieranie. Przykłady materiałów przystosowanych do użytku w bardzo wysokich temperaturach to stopy: inconel 601 (+1175°C) i incoloy 800HT, odporny na temperatury do +1100°C.
Osłony termometryczne odporne na ścieranie
Niektóre zastosowania wymagają wzmocnionych osłon termometrycznych. Przykład to czujniki mierzące temperaturę w strumieniu przepływu granulatów, wiór, proszków – jej wartość podczas transportu takich produktów musi być monitorowana, żeby nie dopuścić do przekroczenia granicy zapłonu. W tej aplikacji obudowa sensora jest narażona na bardzo silne ścieranie. Aby jego skutki ograniczyć, osłony termometryczne zabezpiecza się specjalnymi, odpornymi na tarcie, powłokami.
Dużą wytrzymałość na ścieranie uzyskuje się przykładowo przez powlekanie stellitem. Jest to stop kobaltu, chromu i wolframu, zawierający często domieszki węgla, żelaza, molibdenu. Wyróżnia się bardzo dużą twardością.
Powłoki stellitowe na osłony termometryczne można nanosić na kilka sposobów, na przykład przez roztapianie i zgrzewanie sproszkowanego stopu z materiałem bazowym. Tworzy to szczelną, ściśle przylegającą warstwę. Dzięki niej obudowa jest wytrzymała na ścieranie nawet w najtrudniejszych warunkach. Powłoki takie wykonuje się m.in. przez napawanie laserowe. W procesie tym proszek stellitowy zostaje stopiony przez wiązkę lasera i przyspawany do osłony. Możliwość regulowania mocy lasera w szerokim zakresie zapewnia dobrą jakość powłoki. Nanosząc wiele warstw, jedna na drugą, można uzyskać powłoki dowolnej grubości.
Specjalne konstrukcje osłon termometrycznych
Inne przykłady to: konstrukcje z przedmuchiwaniem gazem obojętnym albo sprężonym powietrzem i osłony z uszczelnieniem ciśnieniowym. Pierwsze zapewniają usuwanie agresywnych gazów, które przedostając się z procesu do wnętrza osłony, mogłyby uszkodzić element pomiarowy.
Nie zawsze jest możliwe zanurzenie końcówki pomiarowej w osłonie termometrycznej w mierzonym produkcie przez wprowadzenie jej do wnętrza zbiornika. Przeważnie jest to spowodowane tym, że mogłaby negatywnie wpływać na przebieg procesów, które w nim zachodzą albo odwrotnie – to ich specyfika lub konstrukcja zbiornika mogłyby działać destrukcyjnie na czujnik. Przykładem jest wyposażenie dodatkowe jak mieszacze, używane do zapewnienia jednorodności zawartości, które dla osłon termometrycznych są źródłem sił niszczących. Wprowadzenie czujników przez kołnierze wbudowane w ściany jest też niemożliwe, jeżeli zbiornik jest wyposażony w zgarniacze, usuwające resztki zawartości, które osadzają się w jego wnętrzu. W takich przypadkach trzeba wybrać czujnik w osłonie zmywalnej (omywalnej), która jest mocowana w ścianie kontenera, równo z jej krawędzią.
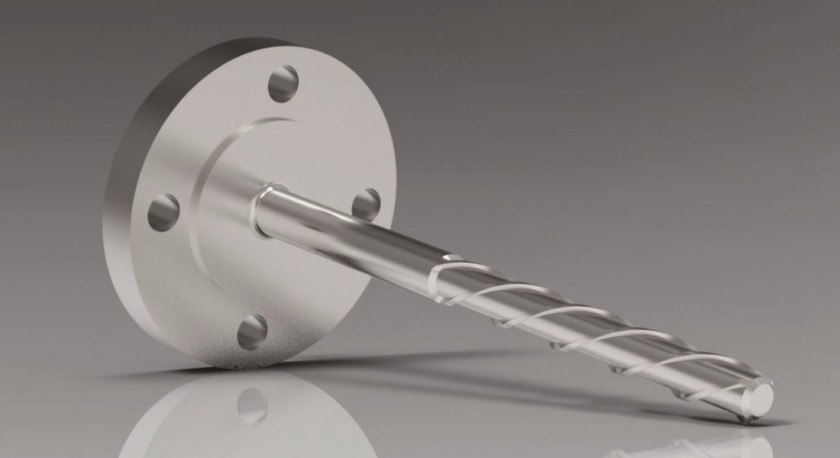
Pomiary higieniczne. Zapobieganie wibracjom
Tego typu konstrukcje są często wykorzystywane także tam, gdzie występują wysokie wymagania sterylności konstrukcji – obudów omywalnych używa się na przykład w przemyśle spożywczym i farmaceutycznym. Osłony w takich zastosowaniach muszą spełniać dodatkowe kryteria. Przede wszystkim nie mogą mieć otworów ani martwych przestrzeni, w których mogłyby się osadzać i gromadzić pozostałości produktu. Powinno być możliwe ich czyszczenie oraz sterylizacja bez konieczności ich demontowania – osłony do zastosowań higienicznych są zazwyczaj dostępne w wersjach CIP (Clean In Place) i SIP (Sterilization In Place). Ich głowice przyłączeniowe powinny mieć odpowiedni stopień szczelności. Osłony muszą być wykonywane z materiałów dopuszczonych do użytku w aplikacjach higienicznych – przykład to stal nierdzewna. Ich części zwilżane powinny charakteryzować się małą chropowatością. Są montowane przez wspawanie lub przez połączenia aseptyczne.
W przypadku, gdy spodziewane jest wystąpienie warunków, w których wiry powstające w wyniku obecności osłony termometrycznej w strumieniu przepływu cieczy wzbudzą jej nadmierne wibracje, warto z kolei wybrać obudowy, których konstrukcja to uwzględnia. Mają one przeważnie kształt spiralny. Pręty w taki sposób uformowane rozpraszają tworzące się wiry, które dzielą się na wiele mniejszych. To zapobiega wzbudzaniu się drgań osłony.
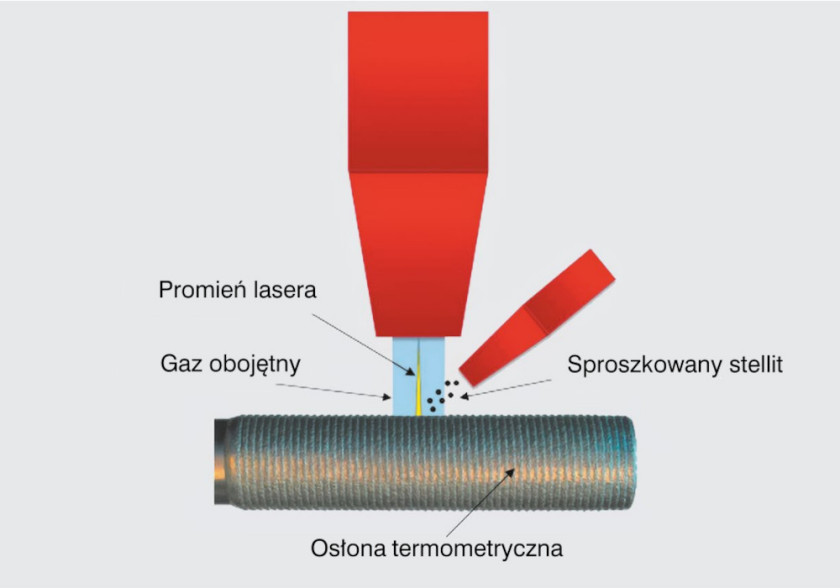
Czujniki powierzchniowe
Jeżeli nie tylko zanurzenie końcówki pomiarowej w mierzonym produkcie jest niepożądane, ale również ingerencja w rurociąg przez wstawienie osłony zmywalnej jest niewykonalna, alternatywą są pomiary bezkontaktowe (przy użyciu pirometrów albo kamer termowizyjnych) lub kontaktowe czujniki powierzchniowe.
Te drugie sprawdzają się szczególnie, gdy współczynnik emisyjności mierzonej powierzchni może się zmieniać w trudny do przewidzenia sposób albo generalnie jest nieokreślony, przez co wpływa na dokładność odczytów. Tego typu przyrządy pomiarowe zwykle występują w wersjach do montażu na powierzchniach płaskich albo do pomiaru temperatury rurociągów. W pierwszych element pomiarowy – termopara lub czujnik rezystancyjny, jest wbudowany w blok kontaktowy. Ten może być zamocowany do mierzonej powierzchni na różne sposoby, na przykład przez przyspawanie albo przykręcenie. Wersje sensorów do rur są zwykle przytwierdzane z wykorzystaniem opaski zaciskowej.
Pomiary temperatury łożysk
Specjalne wymagania na konstrukcje elementów pomiarowych nakładają też pomiary temperatury łożysk w pompach, turbinach, dmuchawach, silnikach. Czujniki wykorzystywane w tym zastosowaniu powinny się charakteryzować przede wszystkim kompaktowością oraz wytrzymałością na trudne warunki, zwłaszcza silne wibracje.
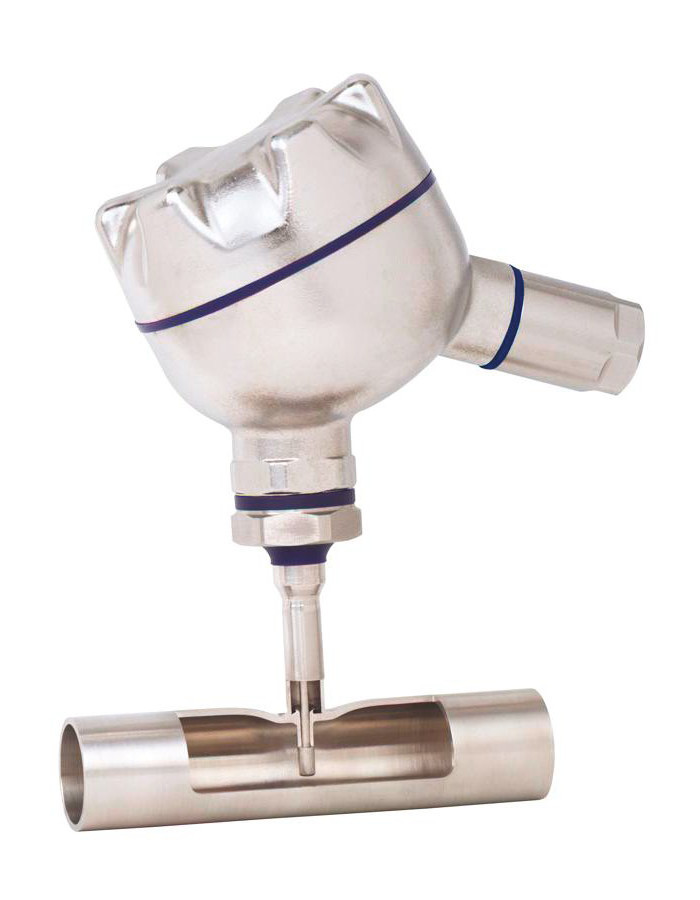
W tym zastosowaniu wykorzystuje się m.in. termopary płaszczowe. Sensory tego typu składają się z zewnętrznego płaszcza metalowego i izolowanych przewodów wewnętrznych, umieszczonych w ceramicznej powłoce – przykładowo w proszku tlenku magnezu. Dzięki takiej budowie termopary płaszczowe w porównaniu do tych w wykonaniu tradycyjnym wyróżniają się małymi rozmiarami oraz możliwością zginania. To ułatwia ich montaż w miejscach trudno dostępnych. Oprócz tego charakteryzuje je duża wytrzymałość na wibracje.
Poza tym korzysta się z czujników, które wraz z osłoną są montowane w gwintowanym gnieździe, na przykład w łożysku lub innej części maszyny. Zestaw pomiarowy w takim przypadku składa się z czujnika rezystancyjnego albo termopary, cienkościennej rurki ochronnej wykonanej typowo ze stali, śruby dociskowej z nacięciem, przewodu przyłączeniowego. Montaż czujnika odbywa się poprzez dokręcenie śruby, która dociska rurkę ochronną do dna otworu.
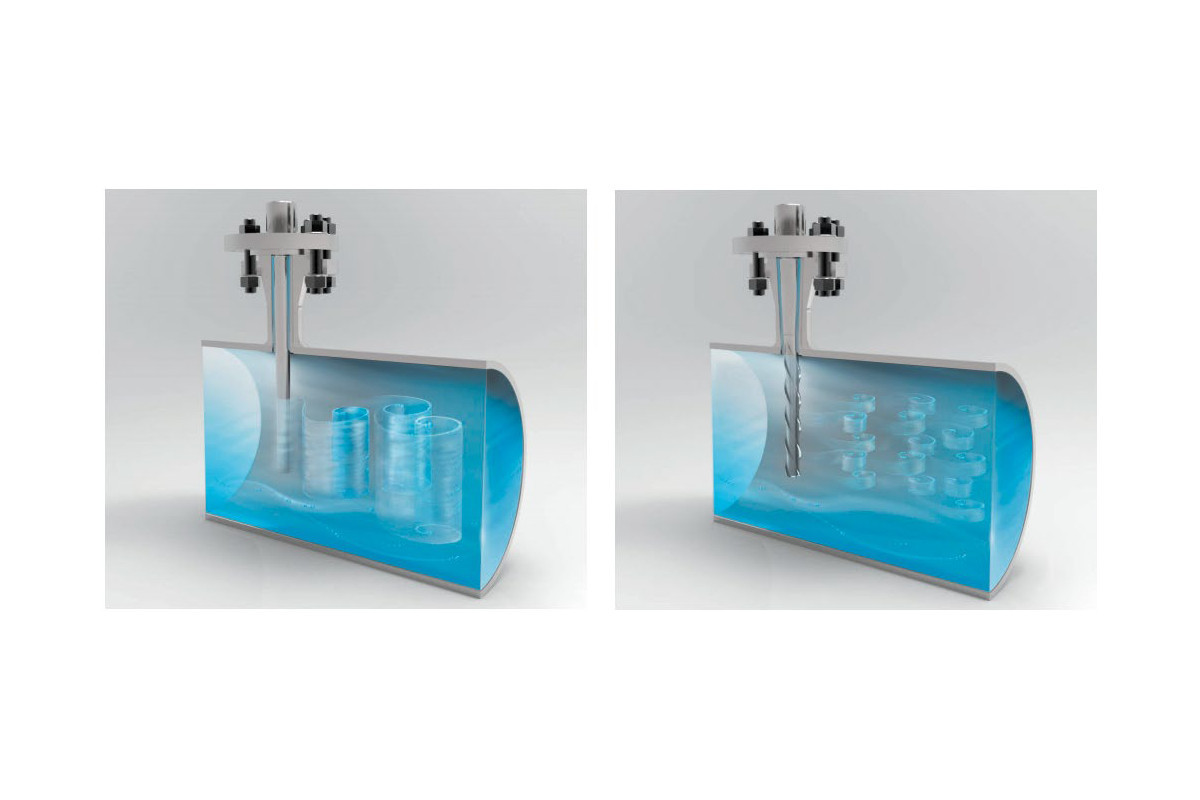
Krótki czas reakcji
Dobry kontakt termiczny między mierzoną powierzchnią, a czujnikiem zapewniają również wkłady sprężynujące. Sprężyny wykorzystuje się w sensorach w osłonach, w tym w wielopunktowych, w których poszczególne elementy pomiarowe są przez nie dociskane do wewnętrznej strony osłony.
Dobry kontakt cieplny wpływa na czas reakcji na zmianę temperatury. Krótki czas odpowiedzi zapewnia też zredukowana stożkowa końcówka osłony.
W niektórych zastosowaniach to jednak nie wystarczy. Na potrzeby aplikacji, w których zadania sterowania wymagają bardzo szybkiego reagowania na zmiany temperatury procesu, opracowuje się specjalne konstrukcje. Przykładem są sensory rezystancyjne, których element pomiarowy jest spiekany w końcówce wkładki pomiarowej z materiałem o dużej przewodności cieplnej.
Monika Jaworowska