Inspekcję z wykorzystaniem ultradźwięków zalicza się do kategorii metod nieniszczących (Non-Destructing Test, NDT). Standardowo sprzęt do ich pomiaru składa się z następujących bloków funkcyjnych: nadajnika / odbiornika, przetwornika, ekranu, na którym wyświetlane są wyniki pomiarów i/lub słuchawek, w których osoba dokonująca pomiaru może usłyszeć zmierzone ultradźwięki przetworzone na sygnał dźwiękowy w zakresie częstotliwości słyszalnych, i elementów interfejsu użytkownika.
Zasada pomiaru
Fale ultradźwiękowe generowane są w przetworniku przez element (płytkę) wykonaną z materiału, w którym zachodzi odwrócone zjawisko piezoelektryczne – przykładem takiego jest kwarc. Polega ono na rozszerzaniu i kurczeniu się płytki pod wpływem napięcia z nadajnika, czemu towarzyszy emisja ultradźwięków. Po przyłożeniu sondy do obiektu inspekcji fala rozchodzi się w badanym materiale. Jeżeli napotka na jakąś nieciągłość albo inny defekt, odbija się od niego i wraca do przetwornika. Tam jest przetwarzana na sygnał elektryczny. Wynik pomiaru jest prezentowany na ekranie miernika i/albo zostaje odtworzony w słuchawkach. Defekty są widoczne i/lub słyszalne jako odstępstwa od spodziewanego profilu ultradźwiękowego obiektu badania.
Spotyka się dwie konfiguracje układu pomiarowego. W pierwszej korzysta się z pojedynczej sondy, która zarówno wysyła, jak i odbiera ultradźwięki. Charakteryzuje ją duża dokładność. Szczególnie sprawdza się w wykrywaniu pęknięć, szczelin i innych braków. Jest popularna m.in. w badaniach części samochodowych, samolotowych, spawów, rurociągów. W drugiej konfiguracji korzysta się z dwóch sond, nadawczej i odbiorczej, które są umieszczone naprzeciwko siebie po obu stronach obiektu inspekcji. Jest ona zalecana w pomiarach materiałów wielowarstwowych.
Zalety i ograniczenia
Inspekcja ultradźwiękowa ma szereg zalet. Wśród najważniejszych wymienia się: możliwość wykrywania defektów powierzchniowych i pod powierzchnią, głębokość penetracji (zakres pomiaru) większą w porównaniu z innymi metodami NDT, wymaganie dostępu do obiektu inspekcji wyłącznie z jednej strony w przypadku techniki z pojedynczą sondą, bardzo duża dokładność w określaniu położenia defektów oraz szacowaniu ich rozmiarów i kształtów, minimalne wymagania w zakresie przygotowania obiektu do inspekcji, natychmiastową dostępność wyników pomiarów, możliwość ich graficznej i dźwiękowej prezentacji, możliwość, poza detekcją braków, również dokonywania pomiarów grubości.
Oprócz zalet należy się również liczyć z pewnymi ograniczeniami inspekcji ultradźwiękowej. Przykładowo przedmioty o szorstkiej powierzchni, o nieregularnym kształcie, bardzo cienkie, niejednorodne są trudne do testowania tą metodą podobnie jak m.in. te wykonane z żeliwa lub innych gruboziarnistych materiałów, które charakteryzuje słaba transmisja dźwięków i wysoki poziom szumów sygnału. Oprócz tego defekty zorientowane równolegle do wiązki pomiarowej mogą pozostać niewykryte.
Ultradźwięki w utrzymaniu ruchu
Pomiary ultradźwięków są również przeprowadzane w ramach inspekcji przez pracowników działu utrzymania ruchu, różnego typu anomalie i problemy w działaniu sprzętu i wyposażenia zakładów przemysłowych mogą bowiem być źródłem fal dźwiękowych tego typu. Wykrycie ich nadmiernej emisji pozwala na podjęcie dalszych działań opóźniających albo zapobiegających awarii.
Źródłem ultradźwięków jest z reguły jedna z następujących sytuacji: nadmierne tarcie, uderzenia medium, jego turbulencje – każda z tych anomalii ma charakterystyczny profil ultradźwiękowy, co pozwala na ich łatwe rozpoznanie. Przykładami sytuacji, których wystąpieniu towarzyszy generacja fali dźwiękowej o częstotliwości powyżej progu słyszalności są więc: nadmierne tarcie w silniku, przekładniach, obudowie łożysk, tłokach, czy wentylatorach, na rolkach przenośnika, pasach i połączeniach pasów, nieszczelności zaworów, wycieki sprężonego powietrza, wycieki pary z odwadniaczy, kawitacja w pompach.
Oprócz problemów mechanicznych, również niekorzystne zjawiska natury elektrycznej, które jonizując powietrze zaburzają ruch cząstek w otoczeniu, są źródłem ultradźwięków. Przykłady to: wyładowania niezupełnie, koronowe, łukowe.
Pomiary ultradźwięków są uznawane za najbardziej niezawodną metodę wykrywania problemów z łożyskami na bardzo wczesnym etapie ich rozwoju – fale dźwiękowe w tym zakresie częstotliwości są emitowane przez te elementy zanim jeszcze ich uszkodzenia spowodują wzrost temperatury albo wzrost poziomu drgań. Metoda ta sprawdza się w rozpoznawaniu m.in. uszkodzeń zmęczeniowych, odcisków Brinella oraz nadmiaru lub braku smaru. Odpowiednia ilość tego ostatniego ma kluczowe znaczenie.
Jeśli zostanie zaaplikowany w nadmiarze elementy toczne będą zbyt silnie dociskane do pierścieni, co przyspieszy ich zużycie. Zwykle towarzyszy temu wzrost temperatury, co sprzyja rozdzielaniu się składników smaru. Przez to traci on swoje właściwości smarne. Przy zbyt małej ilości takiego środka natomiast występuje nadmierne tarcie. To skraca żywotność łożysk.
W zakresie smarowania łożysk praktykowane są różne podejścia. Podstawowym jest stosowanie się do rekomendacji producenta urządzenia, którego częścią są łożyska. Zazwyczaj w jego specyfikacji określony jest zalecany harmonogram smarowania oraz wytyczne w zakresie doboru odpowiedniej ilości smaru. Są określane na podstawie takich kryteriów, jak czas i warunki pracy.
Smarowanie łożysk w praktyce
Lepsze rezultaty można uzyskać, jeżeli podczas okresowego smarowania łożysk ich stan będzie monitorowany za pomocą miernika ultradźwięków. Dzięki temu osoba aplikująca smar będzie miała ułatwione zadanie w zakresie oceny tego, jaka jego ilość jest wystarczająca – zapobiega to nadmiernemu smarowaniu, ale także zapewnia oszczędności środka smarnego.
Przykładowo, jeżeli łożysko rzeczywiście wymaga smarowania, poziom natężenia ultradźwięków zmniejszy się po nałożeniu smaru, ponieważ tarcie będzie dzięki temu mniejsze. Z drugiej strony, jeśli łożysko jest już wystarczająco nasmarowane i nie wymaga dalszych działań w tym zakresie, poziom natężenia ultradźwięków zacznie rosnąć po zaaplikowaniu nadmiarowego smaru. Gdy z kolei w wyniku smarowania łożysk poziom natężenia dźwięków o częstotliwości poza zakresem słyszalnym nie ulegnie zmianie ma to zwykle jedną z dwóch przyczyn. Pierwszą jest uszkodzenie łożysk, w przypadku którego dodatek smaru nie jest już w stanie pomóc, a drugą sytuacja w której uszczelnienie zostało naruszone na skutek wcześniejszej nadmiarowej aplikacji smaru, przez co gdy jest on znów podawany wycieka.
Obserwacja trendu i alarmy
Zdecydowanie najkorzystniejsze jest jednak wdrożenie systemu monitorowania stanu łożysk przez ciągłe zbieranie danych pomiarowych pozwalające na obserwację trendu zmian poziomu natężenia ultradźwięków i detekcję przekroczenia jego wartości uznawanej za optymalną, czyli rejestrowaną w normalnych warunkach pracy, bez zauważalnych problemów i przy odpowiednim nasmarowaniu. Można ją określić na kilka sposobów.
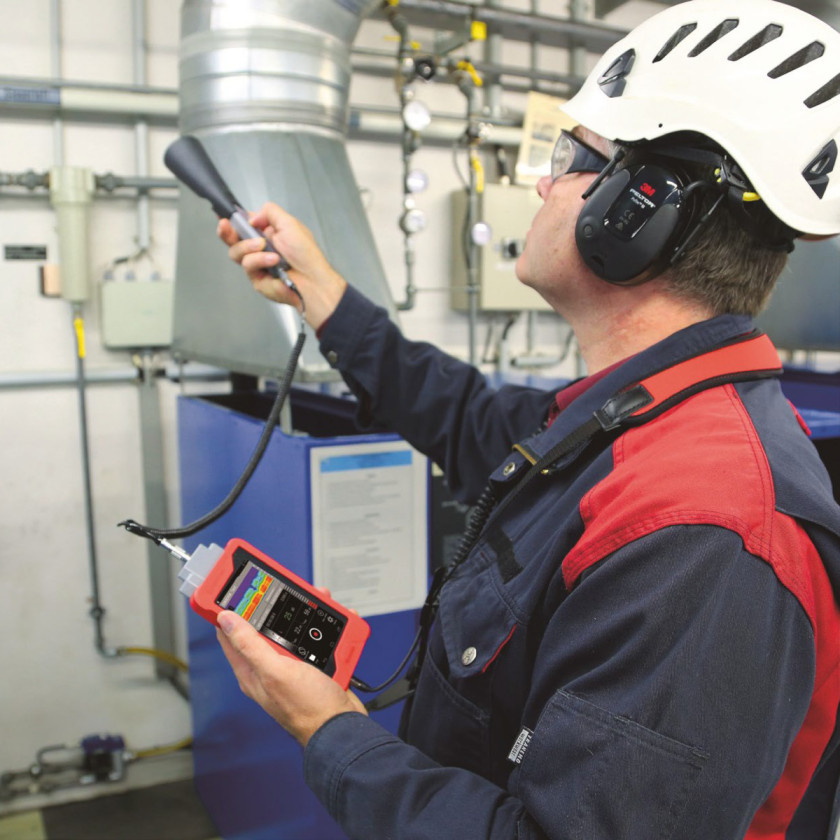
Jednym z nich jest porównanie zmierzonej w tym samym czasie emisji ultradźwięków dla kilku łożysk tego samego typu, pracujących w podobnych samych warunkach (prędkości obrotowej i obciążeniu). Jeśli wyniki pomiarów są podobne ich wartość uśrednioną uznaje się za optymalną. Można ją także ustalić podczas smarowania – technik podczas aplikacji smaru monitoruje poziom natężenia ultradźwięków, który najpierw zwykle maleje, a potem rośnie, co oznacza, że już więcej takiego środka nie potrzeba. Wartość ta jest zatem optymalna. Można też porównać poziom emisji ultradźwięków w pewnym odstępie czasu, przykładowo po miesiącu, i jeśli nie uległ on znaczącej zmianie wartość tę uznać za odniesienie dla kolejnych pomiarów.
Zaleca się, aby system monitorowania stanu łożysk reagował alarmem na wzrost poziomu natężenia ultradźwięków o 8 dB względem wartości optymalnej – przyjmuje się, że oznacza to, iż smaru jest zbyt mało. W przypadku różnicy dwukrotnie większej (16 dB) liczyć się trzeba już natomiast z poważnym uszkodzeniem łożysk. Zaletą tego podejścia jest to, że smar jest aplikowany tylko jeżeli jest to niezbędne, a nie prewencyjnie dla wszystkich łożysk. Zapewnia to oszczędności środka smarnego i czasu.
Zgrzewanie ultradźwiękowe
W tytułowej technice łączenia wykorzystuje się falę ultradźwiękową do wzbudzania cząsteczek zgrzewanych materiałów do drgań. To z kolei powoduje ich nagrzewanie się na skutek tarcia. W miejscu styku zgrzewane materiały topią się i wiążą się ze sobą. Po ostygnięciu połączenie to się utrwala. Jest to popularna metoda m.in. zgrzewania elementów z tworzyw termoplastycznych. Na rys. 1 przedstawiono główne komponenty zgrzewarki ultradźwiękowej.
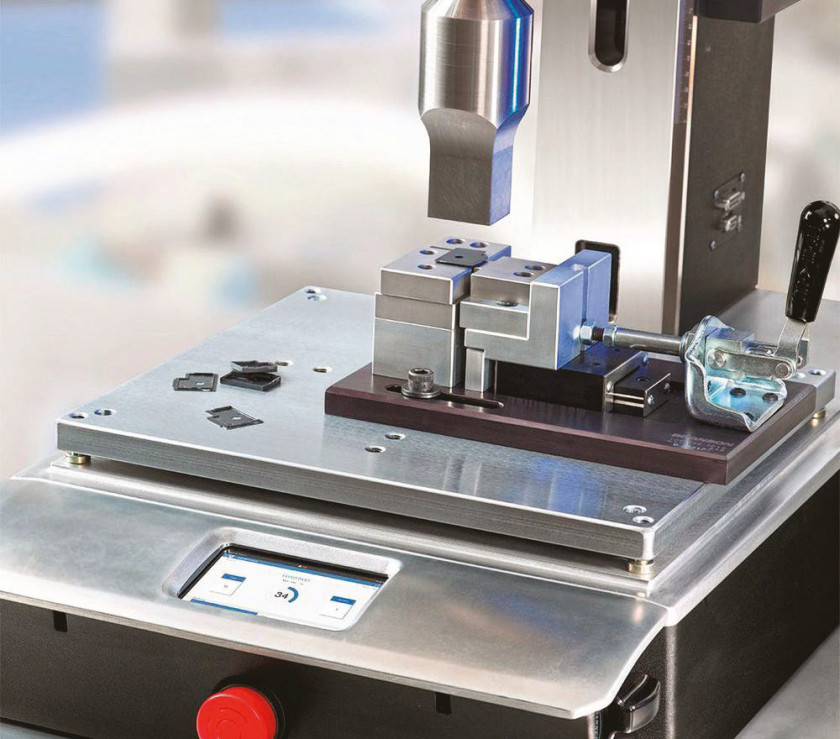
Jednym z nich jest element dociskający. Służy on do wywierania nacisku na łączone materiały. Może być napędzany pneumatycznie albo elektrycznie. Wymagany jest również uchwyt, czyli urządzenie zaciskowe, które służy do przytrzymywania i ściskania zgrzewanych elementów. Ułatwia ono naprowadzanie fali ultradźwiękowej na ich styk.
Do przetwornika z generatora doprowadzony jest prąd wysokiej częstotliwości. Element piezoelektryczny zmienia drgania elektryczne w mechaniczne o tej samej częstotliwości. Z przetwornikiem połączony jest trzpień drgający (sonotroda). Przenosi ona drgania mechaniczne na zgrzewane materiały. Pomiędzy sonotrodą, a przetwornikiem znajduje się dodatkowy komponent, który zwiększa albo zmniejsza amplitudę wibracji (booster).
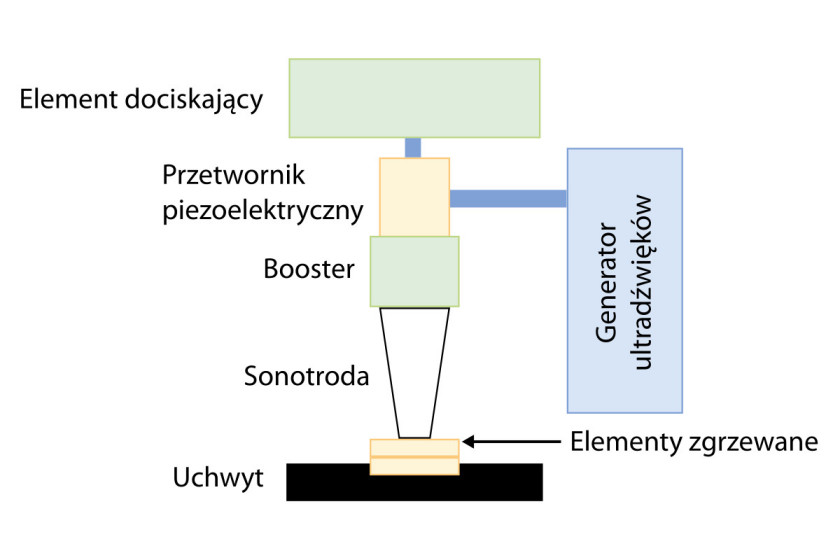
Jakie są zalety zgrzewania ultradźwiękowego?
Na rys. 2 przedstawiono kolejne etapy zgrzewania ultradźwiękowego. W pierwszym kroku elementy przeznaczone do połączenia są montowane w uchwycie. Następnie styka się z nimi trzpień i stopniowo wywiera na nie coraz większy nacisk, regulowany przez element dociskający.
W kolejnym kroku sonotroda zaczyna wibrować z dużą częstotliwością. Za jej pośrednictwem drgania przenoszą się na zgrzewane elementy, które w miejscu styku nagrzewają się i się topią. Nacisk na złącze jest wywierany przez czas wymagany do połączenia jego brzegów w spoinę, która się utrwala podczas chłodzenia i krzepnięcia. Po jej zestaleniu się sonotroda podnosi się. Spawane części jest wyjmowana z uchwytu jako całość.
Zgrzewanie ultradźwiękowe ma wiele zalet. Przede wszystkim jest to metoda szybka. Wynika to stąd, że złącza zastygają w krótkim czasie, łączone elementy można od razu wyjąć z uchwytu, ponieważ oddziaływanie termiczne jest minimalne i punktowe, a rozpraszanie ciepła szybkie, a złącza nie wymagają prac wykończeniowych. Ponadto jest to technika powtarzalna, łatwa do zautomatyzowania i wydajna. Pozwala wykonywać trwałe, jednorodne złącza, przy stosunkowo niewielkim zużyciu energii. Nie są także wymagane żadne dodatkowe materiały eksploatacyjne, jak kleje, rozpuszczalniki ani zewnętrze źródła ciepła.
Ograniczeniem zgrzewania ultradźwiękowego jest natomiast to, że nie nadaje się do wykonywania większych spoin. Poza tym można w ten sposób wykonać jedynie spawy na zakładkę.
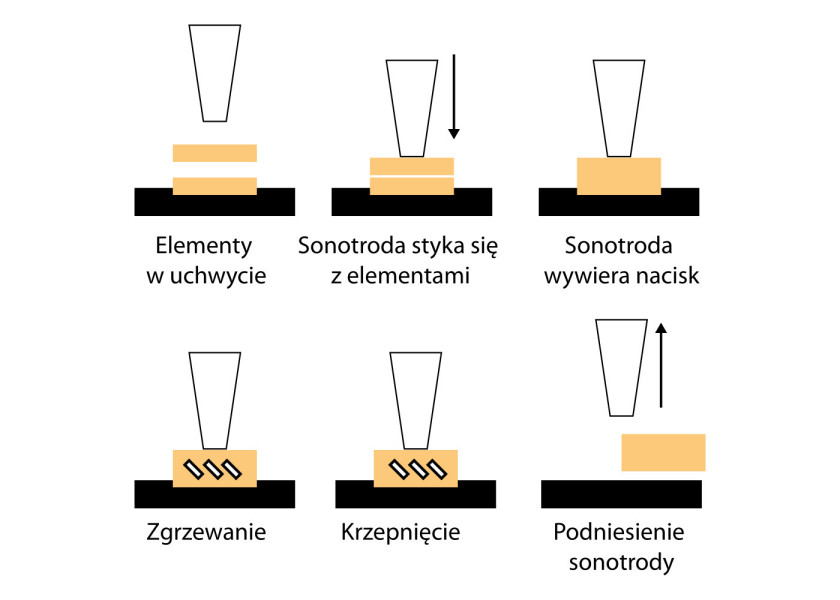
Jak działają myjki ultradźwiękowe?
W tytułowych urządzeniach fala ultradźwiękowa rozchodzi się w płynie (wodzie z dodatkiem środka czyszczącego) powodując najpierw powstawanie ogromnej liczby mikropęcherzyków, a następnie ich implozję. To ostatnie wywołuje lokalne zmiany ciśnienia, co z kolei powoduje, że cząstki brudu odrywają się od powierzchni czyszczonego przedmiotu zanurzonego w zbiorniku myjki ultradźwiękowej.
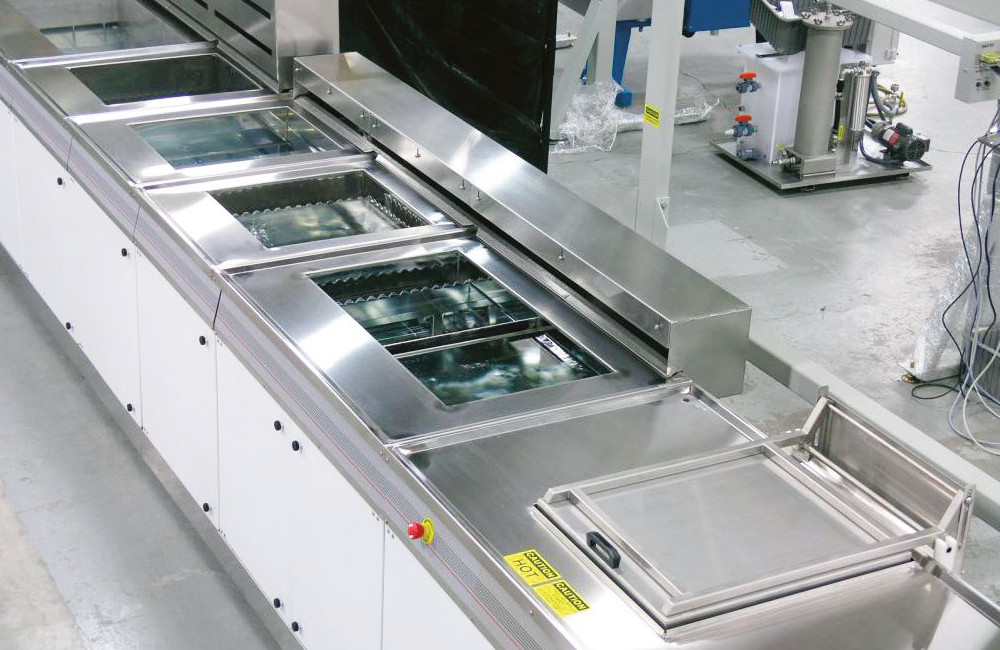
Czyszczenie ultradźwiękowe nadaje się do usuwania zabrudzeń z szerokiej gamy materiałów, w tym metali, szkła, gumy, ceramiki, niektórych twardych tworzyw sztucznych. Metoda sprawdza się szczególnie w usuwaniu ściśle przylegających zanieczyszczeń z elementów o nietypowych kształtach, z nieprzelotowymi otworami, pęknięciami, wgłębieniami. Przykłady zabrudzeń, które można usunąć korzystając z myjki ultradźwiękowej to: kurz, brud, oleje, tłuszcze, pigmenty, topniki, odciski palców.
Gdzie się używa myjek ultradźwiękowych?
W przemysłowych ultradźwiękowych systemach czyszczących używa się płynów na bazie wody albo rozpuszczalnika. Oba typy roztworów czyszczących zawierają surfaktanty, które dodaje się w celu zmniejszenia napięcia powierzchniowego i nasilenia zjawiska kawitacji. Wodne roztwory czyszczące charakteryzują się zwykle mniejszą skutecznością czyszczenia, ale są przyjaźniejsze środowisku, niż roztwory myjące drugiego typu.
Czas czyszczenia zależy od materiału i zabrudzenia, ale typowo wynosi kilka minut – delikatne lub bardziej zabrudzone przedmioty mogą wymagać dłuższego mycia. Wyższa temperatura przyspiesza rozpuszczanie brudu, dlatego większość przemysłowych myjek jest podgrzewana.
Ultradźwiękowe systemy czyszczące są szeroko stosowane w wielu gałęziach przemysłu. Przykładowo używa się ich do usuwania zabrudzeń z form wtryskowych, czyszczenia i odtłuszczania odlewów przed ich malowaniem, lakierowaniem, czy nakładaniem powłok galwanicznych, co ma zapewnić lepszą przyczepność nanoszonych warstw oraz usuwania podpórek detali wykonanych w technologii druku 3D.
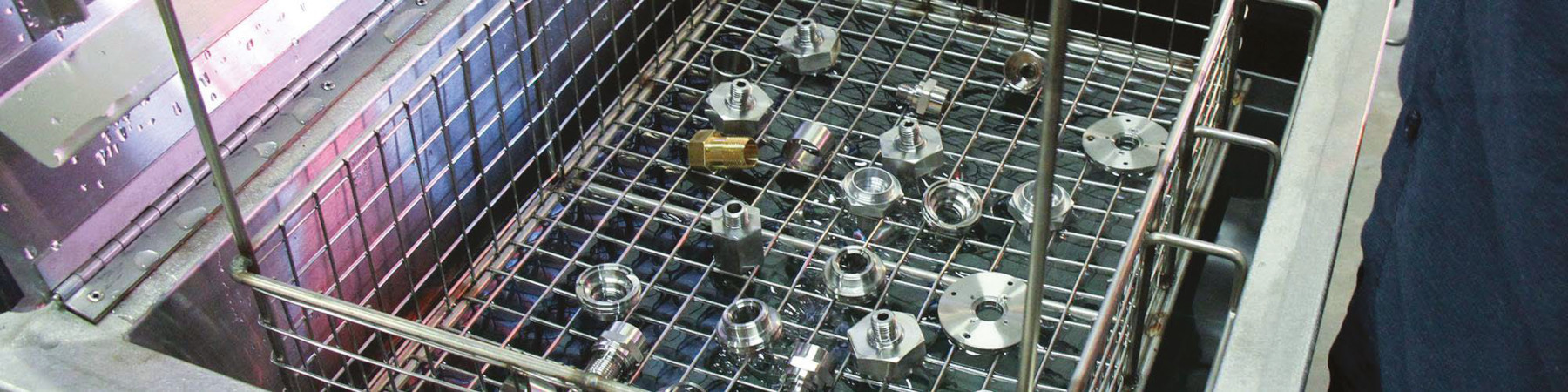
Monika Jaworowska