Pierwsza z wymienionych oznacza, że nie wdrożono żadnej strategii utrzymania ruchu, a zamiast tego reaguje się wyłącznie doraźnie dopiero kiedy już dojdzie do awarii, na przykład naprawiając urządzenie, które się właśnie zepsuło. Podejmowane działania są więc nieplanowanymi skutkami niespodziewanych zdarzeń. Za podejściem reakcyjnym przemawia brak kosztów początkowych i konieczności planowania, co z kolei oznacza oszczędność czasu. Niestety zazwyczaj nie sprawdza się w dłuższej perspektywie, przede wszystkim dlatego, że jest drogie, liczyć się trzeba bowiem ze stratami z powodu przestojów i rekompensat opóźnień w realizacji zleceń, jak również z kosztami niewymiernymi w postaci uszczerbku na reputacji. Przez nieprzewidywalność awarii należy się także spodziewać dodatkowych opłat za części zamienne oraz robociznę, jeżeli chcąc szybko naprawić usterkę zamawiamy trudno dostępną część albo potrzebujemy wsparcia serwisu producenta poza godzinami jego pracy. Pierwszych wprawdzie można uniknąć zawczasu zaopatrując się w zamienniki, ale to z kolei oznacza, że ich koszt trzeba ponieść z góry.
Gdzie się sprawdzi podejście reakcyjne?
Sprzęt, który nie jest regularnie konserwowany, a jedynie naprawiany doraźnie nie będzie też pracował optymalnie, szybciej się zużywając. Przez to inwestycja w jego zakup może się nie zdążyć zwrócić. Trzeba również pamiętać, że brak regularności w zakresie pewnych czynności jak smarowanie, czy wymiana filtrów, jest źródłem strat energii. Warto wspomnieć o zagrożeniu bezpieczeństwa – w razie nagłej awarii technicy mogą nie znać procedur postępowania, a pracując pod presją czasu chętniej podejmują ryzyko, niż wykonując zadania zaplanowane. Łatwiej jest wtedy o wypadek. Ponadto naprawy awaryjne mają przeważnie priorytet kosztem prac planowych, co w przypadku przesunięcia albo anulowania tych drugich może negatywnie wpłynąć na działanie innych urządzeń.
Oczywiście nieplanowanych awarii nie można uniknąć. Generalnie jednak zaleca się, by nie więcej, niż 20% działań działu utrzymania ruchu miało charakter reakcyjny. Naturalnie są od tej zasady wyjątki, jeżeli na przykład ze względu na zdalny charakter zasobów wdrożenie innych strategii byłoby zbyt kosztowne. Poza tym podejście reakcyjne powinno być zarezerwowane dla tych elementów systemu, które są niedrogie, łatwe do wymiany i których awaria nie powoduje poważniejszych konsekwencji.
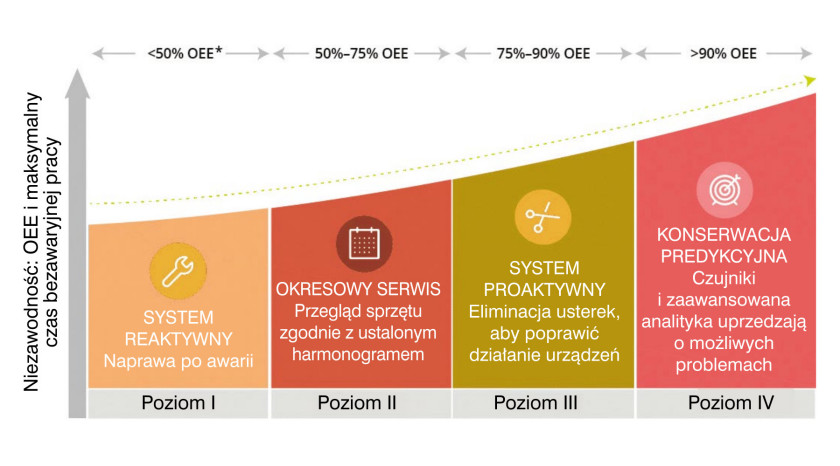
Czym jest RTF?
Podejście reakcyjne w utrzymaniu ruchu jest utożsamiane często z brakiem strategii. Okazuje się jednak, że do tej kategorii można zaliczyć... strategię typu RTF (Run To Failure). Polega ona na celowym przyjęciu wstępnego założenia, że dany zasób na przykład maszyna albo jakaś jej część będzie użytkowany, bez podejmowania jakichkolwiek dodatkowych działań konserwacyjnych czy monitorowania jego stanu, do momentu aż ulegnie awarii. Jednocześnie plan oraz środki do jego realizacji (personel, części zamienne) są na wypadek wystąpienia takiej sytuacji przygotowane z wyprzedzeniem. Dzięki temu dany zasób można naprawić albo go wymienić bez powodowania przestojów w produkcji, nie ponosząc przy tym żadnych dodatkowych kosztów. Przykładem z życia codziennego jest przygotowanie zapasu żarówek i drabiny w oczekiwaniu na to, kiedy żarówka aktualnie użytkowana się przepali. W przemyśle natomiast generalnie strategia ta jest zalecana w przypadku tych aktywów, które w razie awarii nie stwarzają zagrożenia bezpieczeństwa i mają mniejszy wpływ na produkcję. Przykładowo, jeżeli w kopalni pracuje dwadzieścia ciężarówek i dwie kruszarki zastosowanie tytułowego podejścia może mieć sens dla tych pierwszych, lecz z pewnością nie sprawdzi się w przypadku kruszarek ze względu na ich krytyczne znaczenie dla ciągłości produkcji.
RTF nie jest też dobrym wyjściem w przypadku aktywów, których całkowity koszt konserwacji będzie mniejszy w razie wdrożenia konserwacji zapobiegawczej lub predykcyjnej. Warto jest je natomiast rozważyć w przeciwnym razie, czyli jeżeli całkowity koszt naprawy sprzętu po awarii jest niższy, niż koszt innych rodzajów konserwacji. Przykład to maszyna, która pracuje w trybie ciągłym (24 h / dobę, 7 dni w tygodniu). Jej comiesięczny przegląd wymagający jej wyłączenia spowoduje prawdopodobnie takie same (o ile nie większe) zakłócenia w produkcji, jak awaria, która może (ale wcale nie musi) się zdarzyć przykładowo raz w roku. W takim przypadku sensowniejsze jest zatem niepodejmowanie żadnych działań i naprawienie jej dopiero wówczas, gdy się zepsuje.
Konserwacja naprawcza...
Tytułowe działanie rozwiązuje problem z zasobem, przywracając go do prawidłowego funkcjonowania. Zadania konserwacji naprawczej mogą być zarówno planowane, jak i nieplanowane. Generalnie wyróżnić można trzy sytuacje, w których ma ona miejsce. Przeprowadza się ją jeżeli: problem zostanie wykryty w ramach monitorowania stanu zasobu, rutynowa inspekcja wykryje usterkę, dojdzie do awarii. Wynika zatem z tego, że konserwacja naprawcza jest zaplanowana, jeśli w zakresie utrzymania ruchu została wdrożona strategia RTF albo jeżeli jest przeprowadzana w ramach konserwacji prewencyjnej albo monitorowania stanu, mających na celu rozpoznanie problemu, nim jeszcze spowoduje on awarię sprzętu. Można również podać dwa przykłady sytuacji, w których konserwacja naprawcza jest nieplanowana. Pierwsza to awaria, która następuje między inspekcjami zaplanowanymi w ramach konserwacji prewencyjnej – wówczas do naprawy przystępuje się zwykle od razu lub później, w zależności od dostępności narzędzi, części zamiennych, personelu. Druga występuje, gdy zasób ulega awarii albo wykazuje jej oznaki, podczas gdy nie zaplanowano dla niego żadnych działań konserwacyjnych ani rozwiązań na wypadek wystąpienia usterki.
...A konserwacja rutynowa
Tytułowe działanie z kolei obejmuje zadania konserwacyjne, które są wykonywane w sposób zaplanowany i ciągły w celu identyfikowania i zapobiegania problemom, nim spowodują one awarię sprzętu, w ramach na przykład regularnych przeglądów lub prac serwisowych. Są one zwykle dość proste i przeważnie nie wymagają specjalistycznego szkolenia, umiejętności ani sprzętu. Dzięki temu rutynowa konserwacja może być wykonywana przez pracowników spoza działu utrzymania ruchu, takich jak operatorzy maszyn, którzy codziennie, przed rozpoczęciem pracy wykonują ten sam zestaw czynności z listy kontrolnej. Przykłady czynności zaliczanych do tej kategorii to: smarowanie, czyszczenie lub regulacja maszyn, wymiana części, które wyglądają na zużyte lub uległy awarii, wymiana zanieczyszczonych filtrów.
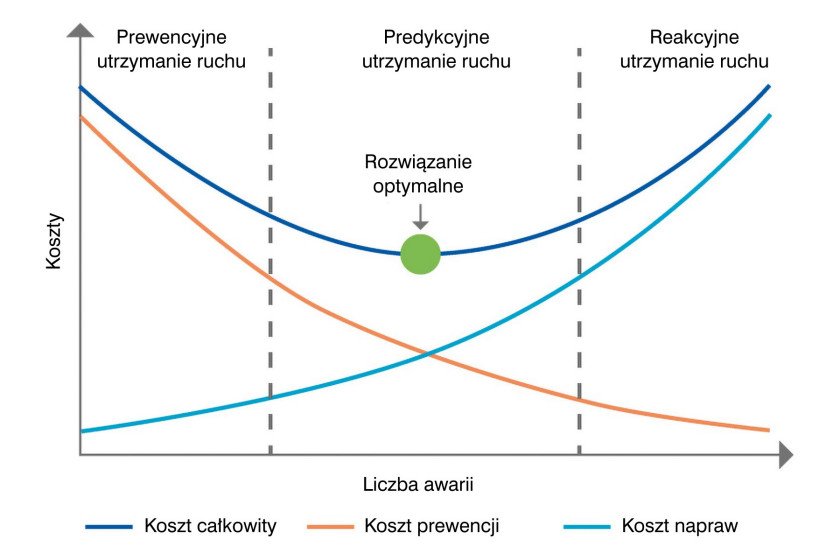
Strategia prewencyjna
W tytułowym podejściu czynności konserwacyjne są przeprowadzane regularnie, co ma na celu zmniejszenia prawdopodobieństwa awarii zasobu poddawanego tym zabiegom. Wykonuje się je kiedy jest on jeszcze w pełni sprawny, żeby nie dopuścić do jego niespodziewanego zepsucia się. Pod względem złożoności ta strategia plasuje się między podejściem reakcyjnym, a konserwacją predykcyjną. Czynności konserwacyjne można przeprowadzać według planu w czasie, co znaczy, że inspekcje są wykonywane w regularnych odstępach czasu albo też zgodnie z harmonogramem opartym na wykorzystaniu. W drugim przypadku jednostką, która wyznacza odstęp pomiędzy kolejnymi sprawdzeniami mogą być na przykład: godziny pracy, liczba cykli produkcyjnych, przebieg liczony w kilometrach.
Strategia prewencyjna jest zalecana do wdrożenia zwłaszcza w przypadku zasobów o krytycznym znaczeniu dla ciągłości produkcji, tych, o których wiadomo, że regularna konserwacja zapobiegnie usterkom oraz urządzeń, w przypadku których prawdopodobieństwo usterki rośnie wraz z upływem czasu. Nie warto jest się na nią decydować z kolei jeżeli: na wystąpienie awarii konserwacja nie ma wpływu i w stosunku do urządzeń, które nie pełnią w zakładzie krytycznej roli. Zalety oraz wady prewencji w utrzymaniu ruchu najlepiej jest przedstawiać w porównaniu do strategii konkurencyjnych prostszych i tych bardziej złożonych w realizacji.
Zalety i ograniczenia strategii zapobiegawczej
Planowanie to największa zaleta konserwacji prewencyjnej w porównaniu z mniej złożonymi strategiami. Dzięki niemu unika się kosztów związanych z nieprzewidzianymi przerwami w produkcji, zawyżonymi kosztami części i robocizny, stratą czasu na diagnozowanie usterek, ponieważ wyłączenie danego sprzętu na czas inspekcji można zaplanować w tym samym czasie, co inny nieunikniony przestój w produkność, wcześniej gromadząc wszelkie wymagane części, materiały eksploatacyjne i rezerwując personel. Planowanie poprawia również bezpieczeństwo, gdyż sprzęt psuje się rzadziej, niż w przypadku mniej złożonych strategii.
Porównując to podejście z tymi bardziej złożonymi natomiast należy zauważyć, że ponieważ konserwacja zapobiegawcza nie wymaga monitorowania stanu zasobu, oszczędza się na urządzeniach pomiarowych oraz rozwiązaniach do gromadzenia i interpretacji danych z czujników.
Z drugiej jednak strony planowanie wymaga poświęcenia czasu i zasobów ludzkich, co nie jest wymagane w podejściu reakcyjnym. Poza tym jeżeli charakter i częstość inspekcji nie zostaną zoptymalizowane, łatwo można zawyżyć jej koszt w stosunku do rzeczywistych potrzeb. To z kolei jest łatwiejsze do uniknięcia, bez negatywnego wpływu na niezawodność, w przypadku bardziej złożonych strategii bazujących na monitorowaniu stanu. Tu warto jednak dodać, że oszczędności uzyskiwane ze zmniejszenia częstości konserwacji często są równoważone wydatkami na monitorowanie stanu.
Na czym polega monitorowania stanu?
W konserwacji opartej na tytułowej przesłance (Condition Based Maintenance, CBM) aktualny stan zasobu jest śledzony – informacje na ten temat mogą być zbierane w określonych odstępach czasu albo w sposób ciągły. Na ich podstawie podejmowana jest decyzja o tym, czy i w jaki sposób należy zainterweniować – działania podejmowane są zwykle dopiero wtedy, kiedy określone wskaźniki alarmują o zmniejszeniu się wydajności albo wskazują na zbliżającą się awarię. W porównaniu z podejściem zapobiegawczym wydłuża to czas między kolejnymi konserwacjami, ponieważ są wykonywane tylko w miarę potrzeb, jednak na tyle wcześnie, aby zapobiec usterce lub spadkowi wydajności poniżej optymalnego poziomu. Przykładowe techniki pomiarowe, które wykorzystuje się w CBM to: pomiary wibracji, termowizyjne, ultradźwięków, akustyczne, analiza oleju, pomiary wielkości elektrycznych, ciśnienia, przepływu.
Wśród zalet monitorowania stanu wymienić należy: niewpływanie na działanie sprzętu, gdyż wskaźniki muszą być śledzone podczas jego normalnej pracy, skrócenie czasu konserwacji, optymalizacja ostępów pomiędzy kolejnymi działaniami w tym zakresie. Ograniczenia to z kolei: wydatki na sprzęt pomiarowy i szkolenie specjalistów w zakresie pomiarów i analizy ich wyników, możliwa konieczność ingerencji w albo modyfikacji monitorowanego sprzętu w celu jego opomiarowania, które szczególnie w przypadku starszych urządzeń mogą się wiązać z komplikacjami i dodatkowymi kosztami oraz nieprzewidywalność odstępów pomiędzy kolejnymi konserwacjami.
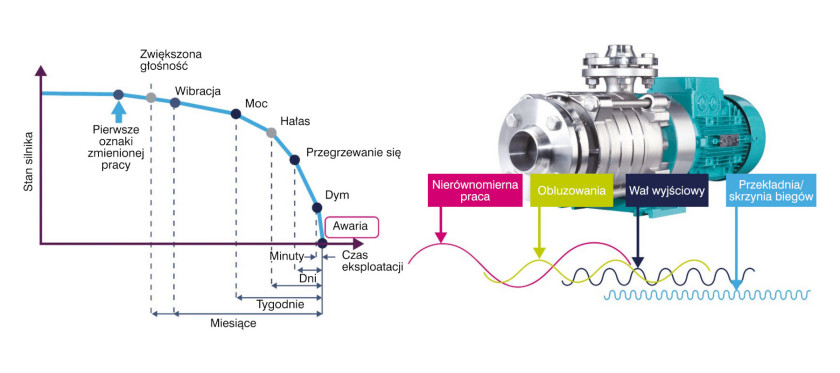
Predykcja w utrzymaniu ruchu
W strategii predykcyjnej wykorzystuje się narzędzia pomiarowe oraz techniki analizowania danych, historycznych i tych pozyskiwanych w czasie rzeczywistym, z różnych źródeł, do wykrywania i przewidywania anomalii w działaniu sprzętów i w przebiegu procesów. Dzięki temu można je usunąć zanim spowodują awarię. Zapewnia to możliwie najmniejszą częstość interwencji gwarantujących uniknięcie usterki, jednocześnie bez ponoszenia kosztów związanych z przeprowadzaniem częstej konserwacji zapobiegawczej.
Podejście to obecnie szybko się rozwija i popularyzuje, ponieważ dostępne stają się technologie, które umożliwiają uzyskiwanie coraz lepszych efektów w zakresie prognozowania awarii i spadków wydajności. Chodzi tu przede wszystkim o, poza rozwojem technik pomiarowych, upowszechnienie się Internetu Rzeczy także w przemyśle oraz rozwój technik sztucznej inteligencji. Z tego wynika oczywiście znacznie wyższy koszt początkowy (sprzętu, specjalistów), z którym trzeba się liczyć decydując się na wdrożenie tego podejścia. Z drugiej jednak strony warto je rozważyć, po pierwsze dlatego, że w miarę jak nowe technologie będą się popularyzować koszt ten będzie z pewnością malał, a po drugie, ponieważ ze względu na skuteczność podejście predykcyjne zapewnia w dłuższej perspektywie znaczące oszczędności czasu i wydatków, optymalizując wykorzystanie zasobów przedsiębiorstwa.
Podsumowanie
Granice między podtypami trzech głównych rodzajów strategii w zakresie utrzymania ruchu mogą się wydawać niewyraźne. W związku z tym najlepiej jest je rozróżnić przedstawiając je w praktyce. Wyjaśniamy to na przykładzie linii produkcyjnej, której częścią jest przenośnik taśmowy.
W razie, gdy zdecydowano się na podejście reakcyjne, jeżeli taśmociąg ulegnie awarii nie ma planu postępowania w takiej sytuacji, załoga zatem musi "na gorąco" najpierw zdiagnozować, a następnie rozwiązać problem. Jeśli z kolei zastosowano podejście RTF w takim przypadku personel postępuje według wcześniej ustalonego planu.
W razie, gdy wdrożono strategię konserwacji naprawczej z kolei do takiej sytuacji prawdopodobnie nie dojdzie, ponieważ wcześniej pracownicy podczas na przykład cotygodniowej kontroli zauważą, że problematyczna część przenośnika jest przykładowo niewłaściwie ustawiona i ją wyrównają, co zapobiegnie awarii. W przypadku konserwacji rutynowej natomiast operator linii z pewnością jak zwykle sprawdzi przenośnik przed rozpoczęciem zmiany i wykryje problem jeszcze wcześniej. W razie wdrożenia strategii zapobiegawczej taśmociąg będzie z kolei pod kątem potencjalnej awarii będzie sprawdzany na przykład co dwa tygodnie albo co dziesięć cykli produkcyjnych. W CBM natomiast konserwacja zostanie przeprowadzona, jeżeli poziom wibracji przenośnika przekroczy bezpieczny próg. W strategii prewencyjnej z kolei oprogramowanie poinformuje operatorów, że drgania przekroczą dopuszczalny poziom na przykład już prawdopodobnie za tydzień.
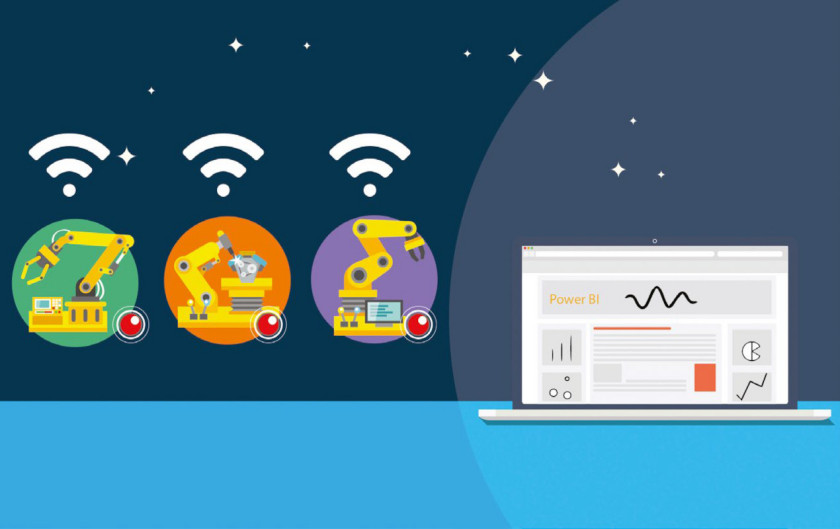
Monika Jaworowska