Jeżeli chodzi o przykładowe maszyny specjalistyczne, które odpowiadają za jednostkowe operacje, dalej opisujemy problemy często występujące w przypadku urządzeń wykorzystywanych do pakowania produktów w postaci płynnej oraz pozostałych (zwartej, sypkiej), odpowiednio: nalewarek przelewowych i pionowych maszyn pakujących (Vertical Form Fill Seal, VFFS).
Pierwsze z wymienionych urządzeń wyposażone są w dyszę, którą płyn wpływa do opakowania. Gdy jego ilość przekroczy zadany poziom, jego nadmiar jest zwracany do zbiornika. Ten rodzaj nalewarek jest zaliczany do kategorii maszyn napełniających wszystkie butelki do jednakowego poziomu, dzięki czemu są one popularne wśród producentów wyrobów, które są sprzedawane w przezroczystych opakowaniach. Przeważnie użytkownicy nalewarek przelewowych borykają się z następującymi problemami negatywnie wpływającymi na przebieg procesu pakowania: wyciekami płynu, unieruchomieniem dyszy, pienieniem się i niejednakowym poziomem napełnienia sąsiednich pojemników.
Jak zapobiec wyciekom?
Jeżeli chodzi o wycieki produktu, mogą one mieć kilka przyczyn. Przykładem jest nieszczelna gumowa uszczelka w dyszy – element ten naturalnie z biegiem czasu się zużywa, w związku z czym powinno się go poddawać regularnej inspekcji pod tym kątem, zaś w razie wykrycia, że jest powodem przecieku, natychmiast trzeba go wymienić. Do wycieku dochodzi zwykle również, jeśli w ramach danej linii nalewania zostaje zmieniony typ rozlewanego produktu i okazuje się, że jest on niekompatybilny z materiałem uszczelki dyszy. Wówczas ulega ona zużyciu w jeszcze krótszym czasie.
Jeżeli jednak sprawdzenie uszczelki nie ujawni jej jako powodu wycieku płynu, należy się upewnić, że parametry pracy głowicy zostały właściwie dobrane do specyfiki produktu i opakowania. Może się na przykład okazać, że w danym przypadku ze względu na ciśnienie wywierane przez płyn w butelce dyszę powinno się wyjmować z niej po jego napełnieniu po krótszym albo po dłuższym czasie. Jeżeli w ramach danej linii rozlewu używanych jest wiele rozmiarów opakowań, to jest właśnie częstą przyczyną wyciekania produktu.
Jak odblokować dyszę?
W razie wykrycia wycieku płynu powinno się również sprawdzić, czy głowica nalewarki nie uległa uszkodzeniu. Chociaż jest to raczej rzadki przypadek, może do tego dojść, jeśli na przykład dysza uderzyła w zakapslowaną butelkę, co spowodowało, że jej korpus się uszkodził albo po prostu uległ skrzywieniu. To również może skutkować jej rozszczelnieniem.
Kolejny problem to nieruchoma dysza. Jeżeli głowica nie podnosi się ani nie obniża, nalewarkę należy przeważnie jak najszybciej sprawdzić pod kątem najczęstszej przyczyny takiego stanu rzeczy – problemu w instalacji sprężonego powietrza.
Ponieważ dysze w tego typu maszynach specjalistycznych są zwykle zasilane pneumatycznie, w pierwszej kolejności powinno się poddać inspekcji przewody, którymi przesyłane jest sprężone powietrze. Trzeba sprawdzić, czy nie występują w nich nieszczelności, które powodują przeciek tego medium, poluzowania na przyłączach, blokady przepływu sprężonego powietrza ani czy nie nastąpiło odłączenie danej linii od źródła tego medium zasilającego. Należy również sprawdzić sprężarkę powietrza, żeby upewnić się, że jest włączona i pracuje poprawnie z wymaganą wydajnością.
Jak usunąć pianę?
Nalewarki przelewowe są zalecane do rozlewania płynów, które mają tendencję do pienienia się – zasada ich działania umożliwia usuwanie piany, przy jednoczesnym zapewnieniu jednakowego poziomu napełnienia poszczególnych butelek. Czasem jednak zdarza się, że piana pozostaje w opakowaniu już po jego napełnieniu. Rozwiązaniem jest w takim przypadku wydłużenie czasu napełniania, aby umożliwić wylanie się piany z butelek. Jeśli to nie pomoże, należy spróbować wyregulować głębokość zanurzenia dyszy w opakowaniu.
Ponieważ nalewarki przepływowe powinny z zasady działania gwarantować napełnienie wszystkich opakowań do jednakowego poziomu, w przypadku kiedy tak się nie dzieje, jest to oczywistym skutkiem problemu w pracy takiej maszyny. Wówczas w pierwszej kolejności powinno się sprawdzić, czy nalewarka jest wypoziomowana względem podłogi. Powodem może być też niewyregulowanie ustawień maszyny przy jej przestrajaniu z jednego typu opakowań na inne – przykładowo przy przejściu na większe butelki należy stosownie skorygować czas napełniania. Zalecana jest również inspekcja stanu poszczególnych dysz i przewodów, którymi płynie produkt, żeby upewnić się, że nie występują w nich zatory ani wycieki, które wpływałyby na jego przepływ.
Problemy w maszynach VFFS
Główne komponenty pakowarek pionowych to: rolka z nawiniętym materiałem opakowania, układ prowadnic, którymi jest on rozwijany oraz prowadzony do kołnierza formującego torebkę, wsyp, którym podawany jest opakowywany produkt i zgrzewarka. Ostatnia łączy brzegi opakowania. Torebki wytworzone w pionowych maszynach pakujących typowo mają trzy szwy: biegnący wzdłuż, który powstał przez złączenie, zazwyczaj na zakładkę, brzegów folii, dolny, który zamyka spód torby oraz górny, uszczelniający ją od góry.
Najczęstszym źródłem problemów w formowaniu opakowań w maszynach typu VFFS jest etap rozwijania folii z rolki. Przykładowym alarmem, jaki może wtedy zgłosić pakowarka, jest błąd podawania folii. Może on oznaczać, że materiału tego nie ma w zasobniku, który w związku z tym powinno się uzupełnić albo folia została zerwana czy też się skleiła, co również wymaga interwencji operatora.
Maszyna może też zaalarmować o problemie z odwijaniem folii, który w razie braku reakcji może skutkować jej przerwaniem. Wówczas wśród potencjalnych przyczyn rozważyć należy: zbyt wysoki współczynnik tarcia materiału opakowania, brak folii albo jej zbyt mała ilość, jej nierównomierne nawinięcie na rolkę, zbyt silny docisk folii do rolki. Możliwe także, że jest rozdarta.
Dlaczego folia się nie centruje?
Kolejny problem, którego w takich maszynach można się spodziewać, to niewycentrowanie folii. Przyczyną tego bywa: niewyrównanie tego materiału na rolce, jego nieprawidłowe na niej nawinięcie, nierównoległe ustawienie względem siebie powierzchni rolek i elementów, które dociskają do niej folię, materiał z jednej strony rozwijany za luźno, a z drugiej za ciasno, niedziałający system automatycznego śledzenia folii. Powodem może być też uszkodzony lub nieprawidłowo zamontowany kołnierz formujący torebkę albo to, że rolki nie obracają się swobodnie.
Problemy występują również na etapie cięcia folii na poszczególne opakowania – koniec każdego odcinka, z którego zostanie uformowana torebka, wyznacza specjalny znacznik na rozwijanym z rolki materiale, który jest rozpoznawany przez czujnik pakowarki. W przypadku, gdy zostanie zgłoszony błąd w zakresie jego detekcji, przyczyny mogą być następujące: nieprawidłowe ustawienie sensora albo zabrudzenie jego detektora, niewystarczający kontrast pomiędzy kolorem znacznika a tłem (folią opakowania), materiał opakowania o zbyt odblaskowej powierzchni.
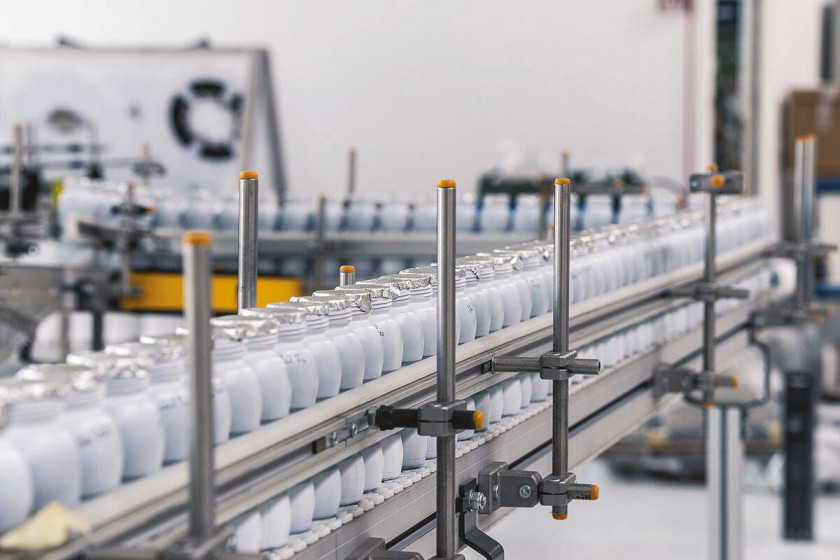
Dlaczego zgrzewy nie są szczelne?
O problemach świadczy również pogorszenie jakości opakowań. Jeżeli przykładowo zauważymy, że folia jest pofałdowana może to oznaczać, że kołnierz formujący kolejne torby jest już zużyty, zabrudzony albo został nieprawidłowo zamontowany. Powodować to mogą oprócz tego zabrudzone rolki.
Zaniepokoić powinny także niekompletne zgrzewy, przez które produkt się wysypuje, nierówne szwy, zgrzewy, które są mocniejsze z jednej strony niż z drugiej, pęcherze w szwach albo ich odbarwienia czy pofałdowania na zgrzewach opakowań. Może to być skutkiem: skończenia się folii, niewłaściwej temperatury zgrzewania, przesunięcia się zgrzewarki, zabrudzenia na szczękach zgrzewarki, uszkodzenia tego jej elementu, niewystarczającego docisku w czasie zgrzewania.
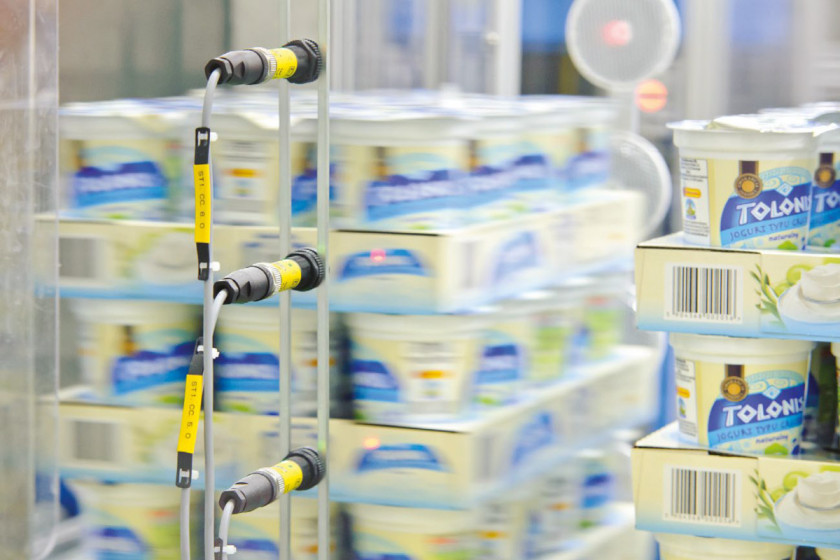
Problemy z przenośnikami
Potencjału zautomatyzowanych linii pakowania nie można wykorzystać w pełni, o ile nie zostanie zorganizowany sprawny mechanizm transportowania opakowań i wyrobów pomiędzy kolejnymi stanowiskami. W związku z tym należy, jak najszybciej, reagować też na problemy w działaniu taśmociągów, takie jak ich zablokowanie opakowaniem lub innym komponentem. Przykładami są butelka, nakrętka lub inny przedmiot, który zahaczy i utknie w szynach do prowadzenia oraz stabilizacji pojemników w miarę ich przemieszczania się na przenośniku, instalowanych m.in. w obrębie linii zautomatyzowanego butelkowania.
Kolejny problem to nadmierne poluzowanie pasów lub łańcucha taśmociągu – nietrudno o to, gdyż systemy przenośników na liniach pakowania często pracują bez przerw przez długi czas podczas kolejnych serii produkcyjnych, często przy nierównomiernym obciążeniu. Naciągnięcie pasa / zwiększenie naprężenia łańcucha mogą w takich przypadkach zapobiec ich ześlizgiwaniu się, a dzięki temu nierównomiernej pracy systemu transportowego.
Przenośniki, tak jak maszyny pakujące, mają części zużywające się, które z czasem wymagają wymiany (pasy, przekładnie). W razie problemów z przepływem opakowań/produktów między stanowiskami linii pakowania trzeba je również poddać inspekcji pod tym kątem. Warto dodać, że prawidłowa konserwacja i czyszczenie newralgicznych komponentów może prawdopodobieństwo problemów tym spowodowanych znacznie zmniejszyć.
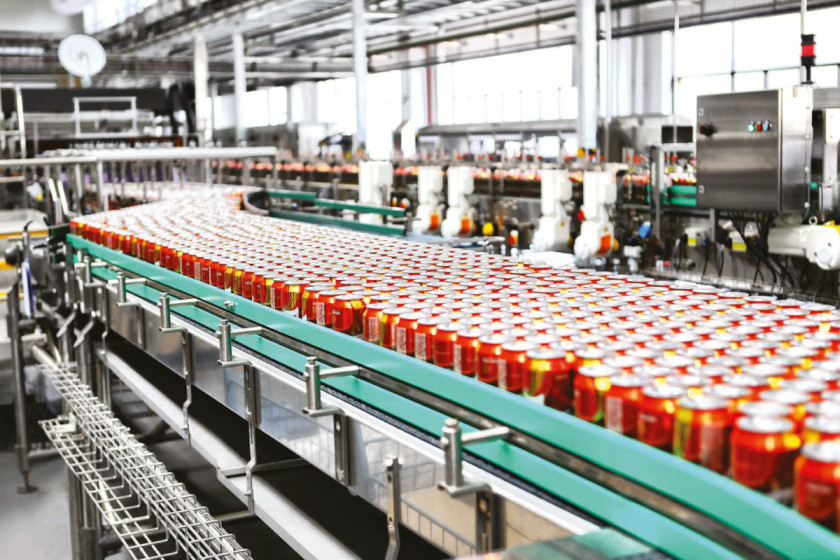
Zapobieganie przestojom
Problemem w przypadku linii pakowania są też tzw. wąskie gardła, czyli ograniczenia wydajności całego procesu przez stanowisko niedorównujące pod tym względem innym. Powodem spadku wydajności mogą być problemy takie, jak te przedstawione powyżej, które można rozwiązać doraźnie. Zdarza się jednak, że błąd, którego skutkiem jest wąskie gardło powtarzające się cyklicznie, został popełniony podczas projektowania linii pakowania. Zwykle polega on na niedopasowaniu kolejnych stanowisk pod względem wydajności. Aby tego uniknąć, na tym etapie powinno się stosować zasadę, zgodnie z którą wydajność jednej z maszyn jest uznana za wartość odniesienia przy wyborze pozostałych – im dalej od niej pracują (w obu kierunkach), tym powinny być od niej szybsze. Przykładowo taką maszyną może być nalewarka. Jeżeli płukarka butelek, która poprzedza ją w ciągu technologicznym, będzie pracować od niej szybciej, w nalewarce nigdy nie zabraknie opakowań do napełnienia. Podobnie, jeśli drukarka etykiet będzie pracować szybciej niż nalewarka, nigdy nie zaistnieje sytuacja, w której pełne opakowania będą oczekiwać na przenośniku na zamocowanie nalepki.
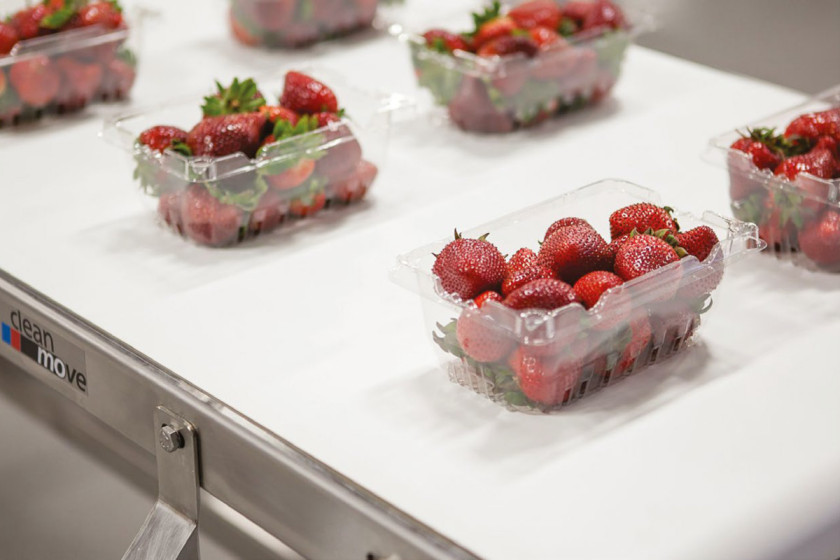
Monika Jaworowska