Obraz na ekranie kamery termowizyjnej, na którym poszczególnym temperaturom odpowiadają różne kolory powstaje dzięki temu, że istnieje korelacja pomiędzy natężeniem promieniowania podczerwonego emitowanego przez każdy obiekt o temperaturze powyżej zera bezwzględnego (-273,15°C), a aktualną temperaturą powierzchni przedmiotu inspekcji. Przeliczenie pomiędzy tymi wielkościami wykonywane w kamerze uwzględnia właściwości obiektu pomiaru, jak też specyfikę otoczenia. Funkcja umożliwiająca automatyczne wyznaczenie współczynników te czynniki charakteryzujących jest obecnie w większości kamer termowizyjnych standardem. Mimo to, na wypadek gdyby konieczne było ich ręczne ustawienie lub korekcja, warto jest wiedzieć więcej na ten temat.
Emisyjność, a refleksyjność
Przede wszystkim trzeba pamiętać, że promieniowanie podczerwone rejestrowane w kamerze stanowi sumę tego emitowanego, odbijanego i przenikającego przez obiekty znajdujące się w jej polu widzenia. Miarą zdolności materiału do emisji promieniowania termicznego jest jego emisyjność (ε). Zależy ona od jego właściwości, wykończenia powierzchni oraz w przypadku niektórych materiałów też od jej temperatury. Duża emisyjność, na którą ich temperatura nie ma wpływu, cechuje na przykład tworzywa sztuczne i beton, z kolei metale mają niską emisyjność, zależną od ich temperatury. Zawsze jest ona jednak mniejsza, niż 1 ze względu na to, że obiekty rzeczywiste nie tylko emitują, lecz również odbijają i przepuszczają promieniowanie termiczne.
Zdolność materiału do jego odbijania charakteryzuje refleksyjność. Zależy ona od właściwości powierzchni, temperatury, typu materiału – generalnie gładkie i błyszczące powierzchnie mają większy współczynnik odbicia niż chropowate i matowe.
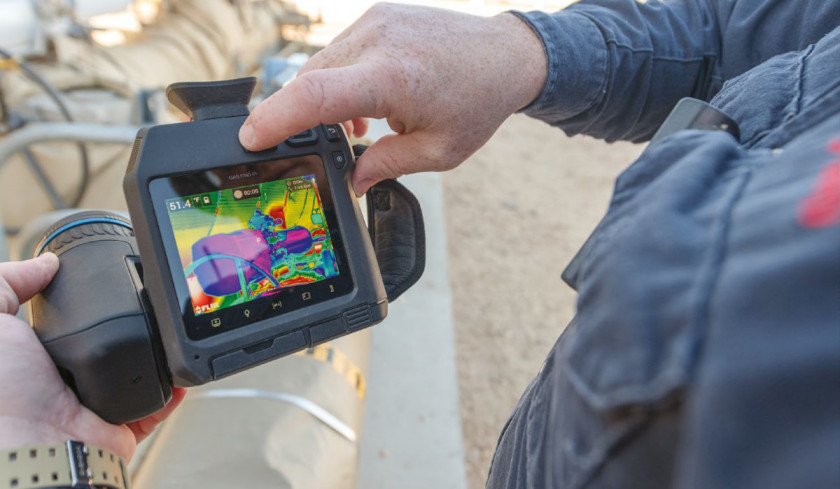
Skutki zaniżonej i zawyżonej emisyjności
Współczynniki emisyjności i RTC (Reflected Temperature Compensation) to właśnie te wspomniane wcześniej parametry wymagane do ustawienia w kamerze termowizyjnej. Transmisyjność natomiast, w związku z tym, że większość materiałów nie przepuszcza promieniowania podczerwonego, w rzeczywistości nie ma znaczenia.
W uproszczeniu więc kamera termowizyjna mierzy tylko promieniowanie emitowane i odbite. W praktyce również im mniejsza jest emisyjność, tym większa refleksyjność. Przez to trudniej jest dokładnie zmierzyć temperaturę, a odpowiednio dobrany współczynnik RTC ma wtedy większe znaczenia dla precyzji pomiaru. Właściwe określenie emisyjności z kolei jest szczególnie ważne, jeżeli występują duże różnice temperatur między obiektem a otoczeniem. Jeśli bowiem pierwsza jest wyższa, ustawienie za dużej emisyjności skutkuje zaniżonym odczytem temperatury obiektu i odwrotnie – zbyt mała emisyjność zawyża odczyt. Analogiczny będzie wpływ błędnie określonej emisyjności w razie, gdy obiekt ma niższą temperaturę, niż otoczenie.
Emisyjność i refleksyjność w praktyce
W uzupełnieniu warto dodać, że nie tylko struktura powierzchni, ale również jej pokrycie, wpływa na precyzję pomiaru temperatury. Takim są różnego rodzaju powłoki, utworzone na przykład przez nagromadzenie wilgoci, szronu, śniegu, gdy obiekt inspekcji pracuje na zewnątrz budynku. W tym przypadku należy uwzględnić to, że takie pokrycia wpływają na temperaturę jego powierzchni. Na przykład kondensat ją ochłodzi, a śnieg zaizoluje. Z kolei w razie nagromadzenia się szronu, który nie tworzy szczelnej powłoki, trzeba uwzględnić emisyjność jego, jak i materiału pod nim. Generalnie jednak lepiej unikać pomiarów powierzchni mokrych, pokrytych szronem lub śniegiem.
Podobnie zafałszowany będzie pomiar przedmiotów zabrudzonych i zakurzonych, unikać trzeba zwłaszcza luźnych zanieczyszczeń ze względu na powietrze izolujące powierzchnię mierzoną. Z kolei jej kolor, od którego zależy stopień pochłaniania przez nią promieniowania podczerwonego (i tym samym szybkość nagrzewnia się), nie ma zauważalnego wpływu na jej emisyjność.
Na wyniki pomiarów kamerą termowizyjną mają również wpływ warunki otoczenia i inne źródła promieniowania termicznego w bezpośrednim sąsiedztwie przedmiotu inspekcji. Dlatego zaleca się unikania odczytów: w pobliżu gorących lub zimnych obiektów (ewentualnie ich zasłanianie), przy dużym bezpośrednim nasłonecznieniu (nawet na kilka godzin przed pomiarem), w czasie silnych opadów atmosferycznych, przy silnym wietrze (i wymuszonym przepływie powietrza w pomieszczeniach).
Optymalna odległość pomiaru
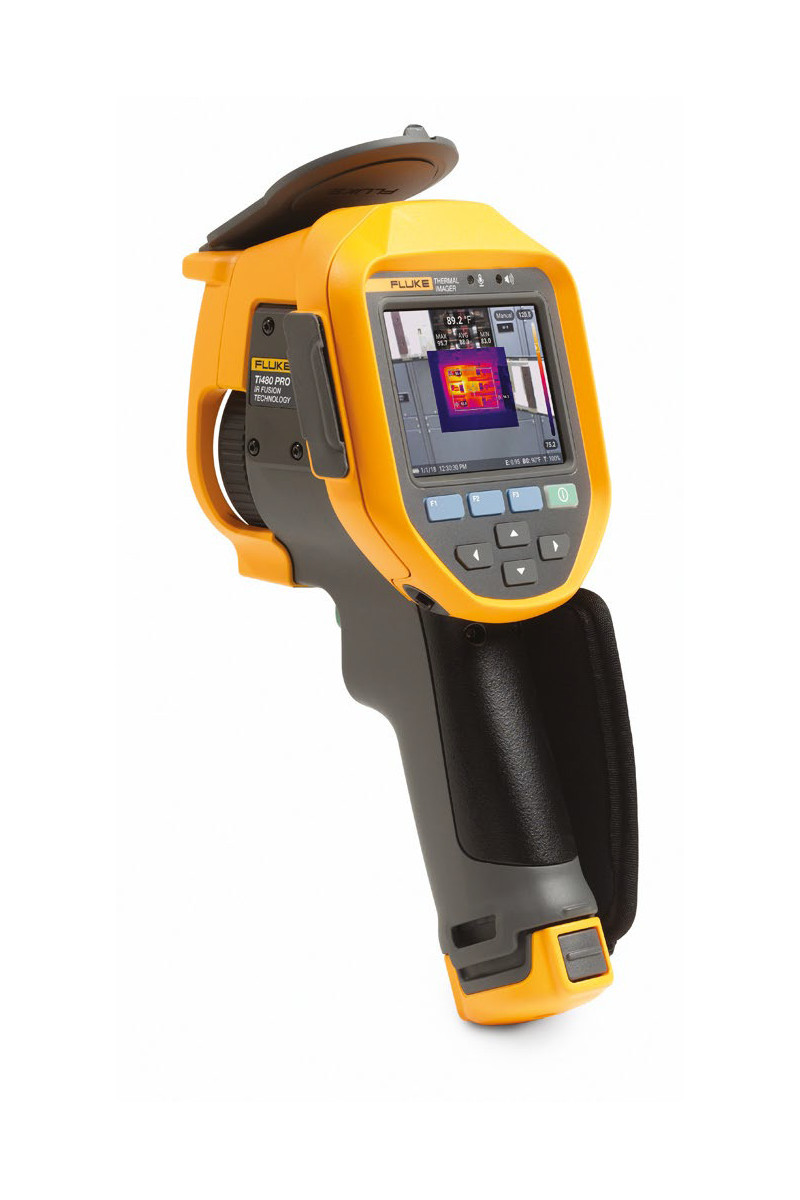
Poza nieprawidłowymi, nieadekwatnymi do rzeczywistych właściwości mierzonej powierzchni i otoczenia, ustawieniami emisyjności i RTC również z kilku innych powodów wyniki pomiarów kamerą termowizyjna mogą zostać zafałszowane. Jednym z nich jest nieodpowiedni dystans od obiektu inspekcji.
Aby ustalić ten optymalny trzeba wyznaczyć współczynnik SSR (Spot Size Ratio) kamery, pozwalający określić maksymalną odległość od przedmiotu o danym rozmiarze, przy której wciąż można uzyskać dokładny wynik pomiarów. W tym celu powinno się wyznaczyć parametr IFOV (Instantaneous Field of View), czyli w uproszczeniu pole widzenia pojedynczego piksela. Obszar, który każdy piksel może pokryć zależy od odległości do niego: im bliżej, tym jest on mniejszy. Parametr IFOV można obliczyć na podstawie wielkości pola widzenia kamery i jej rozdzielczości. W tym zakresie przeważnie producenci tych urządzeń zapewniają wsparcie, udostępniając kalkulatory online. Obliczoną w ten sposób wartość parametru IFOV w mrad należy przemnożyć przez odległość, na jaką planujemy dokonać pomiaru, wyrażając go w mm. Otrzymujemy w ten sposób rozmiar pojedynczego piksela (1 × 1), czyli rozmiar obszaru, którego temperaturę kamera jest w stanie zmierzyć przy określonym odstępie od obiektu inspekcji. Podstawiamy go we wzorze na SSR = d / IFOV, gdzie d to odległość pomiaru. Dla dokładniejszych wyników najlepiej jest jednak przyjąć, że rozmiar najmniejszego rozróżnialnego przez dany sprzęt pomiarowy obszaru powinien wynosić 3 × 3 piksele.
Inne źródła fałszywych odczytów
Poza zbyt krótkim albo za długim dystansem od obiektu inspekcji albo zbyt dużym minimalnym rozróżnialnym obszarem, powodem zafałszowań wyników mogą być zakłócenia występujące na drodze między kamerą, a przedmiotem pomiaru. Takimi są m.in. zanieczyszczenia powietrza – zawieszone w nim cząstki, jak kurz, sadza, dym, pochłaniają i rozpraszają promieniowanie podczerwone. Trzeba również pamiętać, że materiały przezroczyste dla światła widzialnego niekoniecznie muszą przepuszczać promieniowanie podczerwone.
Takim przykładem jest szkło. Jeżeli zatem przedmiot pomiaru ukryty jest za osłoną wykonaną z takiego materiału kierując na nią celownik kamery termowizyjnej w rzeczywistości dokonujemy pomiaru temperatury powierzchni szklanej, a nie obiektu inspekcji. Z drugiej strony materiał ten przepuszcza promieniowanie słoneczne, o czym trzeba pamiętać, licząc się z tym, że może ono dodatkowo ogrzać przedmiot pomiaru. Szkło jest też źródłem zakłócających odczyt odblasków. Generalnie więc, o ile to możliwe (i bezpieczne) najlepiej na czas pomiaru szklaną osłonę zdjąć albo otworzyć.
Podsumowanie
Kamery termowizyjne to wszechstronne narzędzia w utrzymaniu ruchu, które pozwalają wykryć różnego typu anomalie objawiające się nadmiernym wzrostem albo spadkiem temperatury albo jej nierównomiernym rozkładem. Przykładami takich są: problemy w instalacjach elektrycznych (niezrównoważenie faz, przeciążenia, błędne połączenia, harmoniczne, okablowanie niedokładnie zamocowane, obluzowane, nadmiernie napięte, przerwane, ze skorodowanymi złączami, przepalone bezpieczniki, obluzowane zaciski) i układach mechanicznych. Drugie rozwijają się zazwyczaj w skutek nadmiernego tarcia, spowodowanego na przykład niedostatecznym smarowaniem albo niewspółosiowością. Kamery termowizyjne są także często jedynym sposobem, aby dokonać inspekcji – tak jest na przykład w instalacjach produkcji ciepła, jak kotły grzewcze i piece. Problemy, które pozwalają w nich wykryć to m.in.: uszkodzenia albo spadki wydajności wymienników ciepła, którym ulegają w wyniku nagromadzenia osadów na zewnątrz oraz wewnątrz rur, czy pęknięcia wewnętrznej ogniotrwałej osłony paleniska pieca.
Termodiagnostyka za pomocą tytułowych urządzeń pozwala też na przykład monitorować komponenty instalacji przesyłu pary wodnej. Takim newralgicznym w tym przypadku są odwadniacze, których usterki długo niezauważone mogą się stać przyczyną dużych strat ciepła. Prawidłowo wykorzystywane kamery termowizyjne mogą się zatem przysłużyć poprawie zarówno bezpieczeństwa, jak i wydajności zakładów przemysłowych.
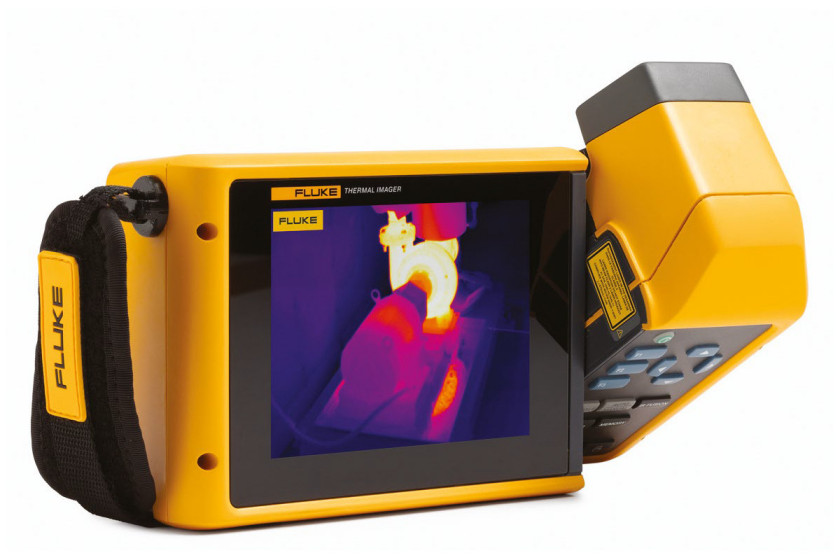
Monika Jaworowska