Komponentami, na które należy zwrócić uwagę, są łożyska. Oznakami problemów z tymi elementami są nadmierne: ciepło, hałas i drgania. Pierwsze może być konsekwencją niewystarczającej ilości smaru, jego nadmiaru (powoduje jego ubijanie) lub nieodpowiedniego rodzaju (o niewłaściwej lepkości, konsystencji, dodatkach) oraz nieprawidłowego systemu smarowania. Kolejne przyczyny to: zbyt ciasne lub brudne uszczelki, wielokrotne uszczelnienia chroniące przed brudem, ale zwiększające tarcie, niewspółosiowość wału, za duża prędkość robocza i uszczelki niedostatecznie nasmarowane albo nieprawidłowo założone (w sposób uniemożliwiający wymywanie smaru).
Dlaczego łożyska się grzeją?
Przyczyną przegrzewania się jest także niewystarczający luz będący skutkiem: niewłaściwego luzu wewnętrznego łożysk (źle dobranych albo zużytych), niedopasowania współczynników rozszerzalności cieplnej materiału wału i stali łożyskowej, dużej różnicy temperatur między wałem a obudową, która powoduje nagrzewanie się (rozszerzanie się materiału) pierścienia wewnętrznego oraz chłodzenie (kurczenie) pierścienia zewnętrznego, odkształcenia oprawy łożyska, za ciasnego dopasowania pierścienia wewnętrznego łożyska do gniazda na wale lub między pierścieniem zewnętrznym łożyska a gniazdem w oprawie (powoduje rozszerzenie się pierścienia, odpowiednio wewnętrznego lub zewnętrznego, i w rezultacie zmniejszenie luzu wewnętrznego łożyska). Kolejny powód to obciążenie łożyska, niedostateczne, które wywołuje poślizg albo nadmierne (na skutek zmian w konfiguracji napędu, niewspółosiowości silnika i obciążenia, odwrotnego montażu łożyska jednokierunkowego, montażu (obciążenia) łożyska promieniowego osiowo lub osiowego promieniowo).
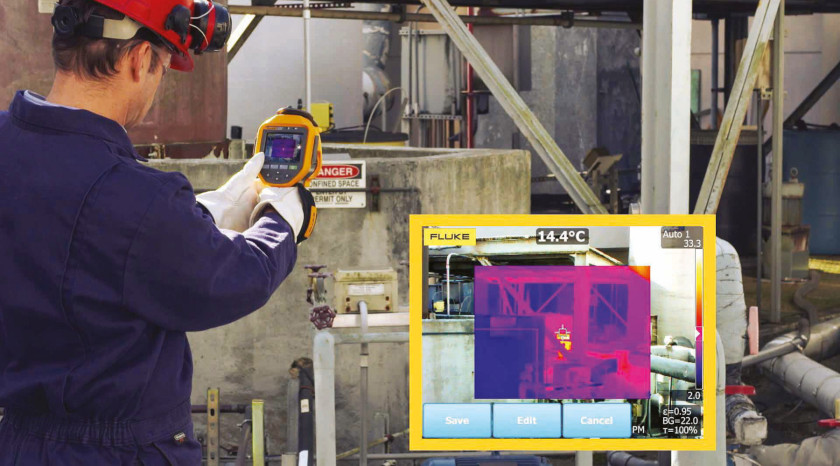
Co wywołuje hałas i drgania łożysk?
Źródłem alarmujących dźwięków jest występowanie kontaktu metal–metal, na skutek zbyt małej ilości smaru lub poślizgu. Kolejne przyczyny to: wgniatające powierzchnie toczne drobne cząstki wnikające z zewnątrz, pozostawione w oprawie w produkcji albo pochodzące ze zużytych łożysk, nieusunięte przez niedokładne czyszczenie lub pochodzące z zanieczyszczonego smaru. Problem stanowią też zanieczyszczenia płynne, zmniejszające lepkość środka smarnego. Hałas jest ponadto powodowany za luźnym dopasowaniem, jeżeli: pierścień wewnętrzny obraca się na gnieździe wału, które jest za małe lub zużyte, lub pierścień zewnętrzny obraca się w za dużym lub zużytym gnieździe obudowy, albo na skutek niewyważenia wału. Jego źródłem są także: za słaby docisk łożysk do współpracujących elementów i nadmierny luz wewnętrzny, promieniowy i osiowy. Generalnie też wszelkie uszkodzenia powierzchni bieżni i elementów tocznych skutkują emisją dźwięków, przykładowo spowodowane: zużyciem ściernym, obciążeniem udarowym, drganiami statycznymi (fałszywe ślady Brinella), przepływem prądu łożyskowego. Uciążliwym dźwiękom z powyższych przyczyn towarzyszą zwykle wibracje.
Dlaczego sprzęgła ulegają awarii?
Jeżeli wybierając sprzęgło, uwzględni się warunki eksploatacji, charakteryzowane przez: moment i prędkość obrotową, niewspółosiowość, sztywność skrętną, bezwładność, tłumienie drgań, czynniki środowiskowe i ograniczenia przestrzenne, w całym przewidywanym okresie ich użytkowania nie powinny wystąpić problemy. Inaczej można się spodziewać przedwczesnej awarii, której oznaki to: hałas, wibracje, chybotanie, wycieki smaru z uszkodzonych uszczelek, uszkodzenie łożysk i większy niż zazwyczaj pobór prądu przez napęd.
Szczególnie ważna jest niewspółosiowość, kątowa, równoległa, osiowa albo stanowiąca ich kombinację, pod kątem której należy wybrać typ sprzęgła – na przykład Oldhama sprawdzą się nawet przy dużej niewspółosiowości równoległej, ale nie kątowej ani osiowej. Częstym powodem awarii jest też niedoszacowanie niewspółosiowości i w konsekwencji nadmierne obciążenie, które przekracza wytrzymałość sprzęgła. Podobnie trzeba uwzględnić nie tylko moment obrotowy w stanie ustalonym, ale też ten maksymalny chwilowy. Nieodpowiednia sztywność skrętna skutkuje przesunięciem kątowym, a luzy zmniejszają precyzję pozycjonowania. Jeżeli wymagana jest duża dokładność, zaleca się sprzęgła o małej bezwładności. Żywotność sprzęgła jest krótsza, jeżeli nie zapewnia odpowiedniego tłumienia drgań. Awarią skutkuje też wybór modelu o nieodpowiedniej maksymalnej bezpiecznej prędkości roboczej.
Problemy z przekładniami...
Kolejny newralgiczny komponent to systemy przenoszenia napędu, a w nich przekładnie i pasy. Pierwsze podczas eksploatacji ulegają nieuniknionemu zużyciu, które spowalnia konserwacja (smarowanie) i kontrola w celu wczesnego wykrycia potencjalnych uszkodzeń kontaktowych i zanieczyszczeń środka smarnego. Jeśli bowiem drobne uszkodzenia nie zostaną zauważone, będą się pogłębiać, aż w końcu na powierzchni przekładni powstaną wżery, których obecność zdradzają nadmierne drgania i hałas. Z kolei w przypadku zanieczyszczenia smaru dochodzi do zużycia ściernego w postaci promieniowych zadrapań i innych śladów na powierzchni, o czym świadczy hałas i pogorszenie się parametrów pracy przekładni. Takim uszkodzeniom zapobiega wymiana smaru oraz kontrola jego czystości. Jeżeli nastąpi rozkład smaru wraz z utratą jego właściwości smarnych, to może rozwinąć się korozja objawiająca się drobnymi, jednolitymi wgłębieniami na powierzchni przekładni. Uszkadza się ona też pod wpływem nadmiernego ciepła – pokrywają ją wówczas gęste mikrowgłębienia (frosting). Duże oraz głębokie wżery świadczą natomiast o przeciążeniu. Przy ekstremalnie dużym może dojść do złamania zębów przekładni.
...i pasami
Oznaką przedwczesnego zużycia i nadchodzącej awarii pasa transmisyjnego jest jego uszkodzenie. W skrajnym przypadku zostaje zerwany na skutek obciążenia, do którego nie został przystosowany lub błędów montażu, jeżeli na tym etapie taśma zostanie naderwana albo zwinięta. Może też pękać w kontakcie z ostrymi krawędziami ładunku, jeśli nie jest odpowiednio wzmocniony. Uszkodzenia na brzegach pasa są skutkiem niewspółosiowości kół pasowych powodującej jego nierównomierne prowadzenie, a niekiedy jego skręcanie podczas pracy, podobnie jak ześlizgiwanie się taśmy i jej skręcanie. Ostatnie mogą być także spowodowane nagromadzeniem się brudu na krążkach, zbyt słabym napięciem pasa, silnymi wibracjami, obciążeniem udarowym. Taśma uginająca się pod ciężarem ładunku, który powinna unieść, też została za słabo napięta albo koła pasowe są już zużyte. Jeśli krawędzie i wierzch pasa twardnieją, może to wskazywać, że się ześlizguje, co zwiększa tarcie i ciepło albo że był narażony na nadmierne ciepło z otoczenia lub ładunku. Zanieczyszczenia olejem i chemikaliami z kolei powodują, że pasek pęcznieje, łuszczy się albo lepi.
Przyczyny awarii silników
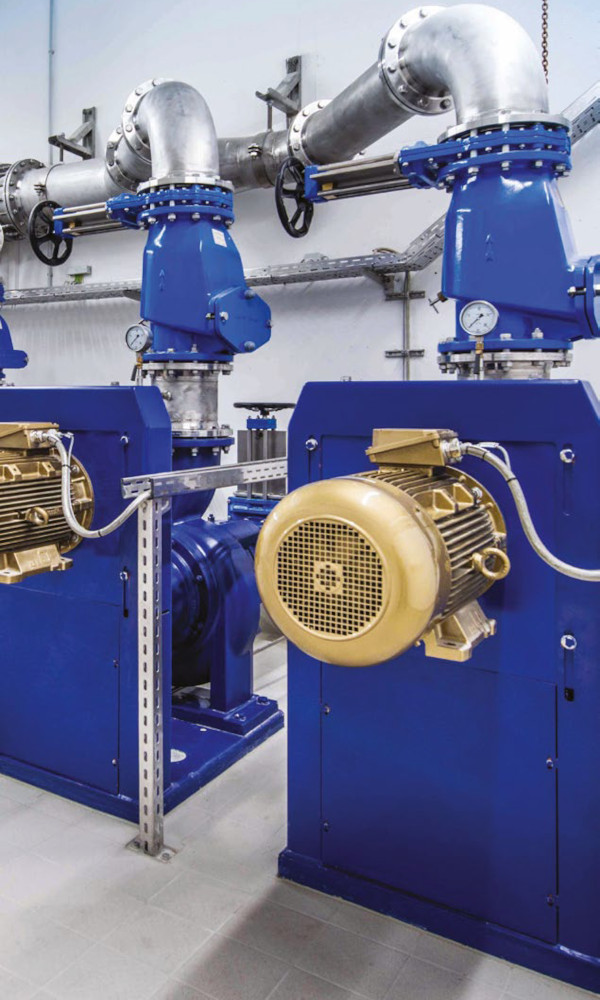
Problemy z silnikami zwykle objawiają się ich drganiami, wzrostem temperatury i większym niż zwykle poborem prądu. Wibracje mogą być skutkiem: niewspółosiowości, luzów, niewyważenia, wygięcia wału, problemów z łożyskami, uszkodzenia uzwojeń i zbyt lekkiego obciążenia. Jeśli z kolei silnik się przegrzewa oznacza to, że wzrosła ilość ciepła w nim wydzielanego albo ciepło w ilościach typowych w warunkach znamionowych nie jest skutecznie rozpraszane przez obudowę ani odprowadzane na zewnątrz przez wentylator, który wymusza wymianę powietrza w osłonie.
Należy w związku z tym sprawdzić, czy wentylacja jest sprawna i drożna, a na obudowie nie zalega izolująca termicznie warstwa brudu. Trzeba także wykluczyć, że przegrzewanie jest skutkiem przeciążenia. Jeśli jednak pobór prądu jest większy niż ten, do pracy przy którym silnik zaprojektowano, może to oznaczać, że: napędzana maszyna się zablokowała, wystąpił problem z łożyskami albo silnik nie może wprawić w ruch zbyt ciężkiego ładunku. Ponadto przeciążenie może wskazywać na: problem z zasilaniem, nieprawidłowe podłączenie silnika, uszkodzenie uzwojeń. Do przegrzania dochodzi też, gdy wirnik ociera się o stojan, z powodu przerwy w uzwojeniach stojana, skoków napięcia, asymetrii napięć, jeżeli zewnętrzne źródło ciepła, jak piec lub inna, silnie nagrzewająca się maszyna, znajduje się zbyt blisko silnika.
Problemy w zaworach i rurociągach
Główny problem w przypadku zaworów to wycieki, wewnętrzne oraz zewnętrzne. Zdolność do odcięcia przepływu zależy od szczelności styku części otwierającej i zamykającej z gniazdem, która pogarsza się przeważnie na skutek zużycia pod wpływem erozyjnego wpływu medium. Zazwyczaj, ze względu na straty oraz zanieczyszczenie otoczenia, groźniejsze są wycieki na zewnątrz widoczne na obudowie. Ich przyczyny to: powodujące przeciekanie korpusu wady jakościowe (pęknięcia, otwory), które powstały w procesie odlewania albo na skutek erozji pod wpływem niszczących czynników zewnętrznych, nieodpowiedni materiał uszczelnień, ich nieprawidłowy montaż, słaba jakość (chropowatość) styku powierzchni uszczelnianych. Zawory mogą również przeciekać, gdy są zatkane brudem.
Co więcej, same mogą być źródłem problemów, jeżeli w wyniku ich szybkiego otwierania zmienia się ciśnienie w rurociągach, w efekcie czego rozchodzi się w nich fala medium. Towarzyszą temu hałas, wibracje i może dojść do uszkodzeniem rur. Żeby zminimalizować wpływ uderzenia płynu m.in.: zawory zamyka się tylko częściowo, stosuje się zawory przewymiarowane, wprowadza się zawory szybko zamykające się, które blokują falę ciśnieniową i stosuje się ograniczniki uderzeń medium, które absorbują skoki jego ciśnienia.
Dlaczego zawodzą uszczelnienia?
Uszczelki są ważnym elementami, poza zaworami, wielu podzespołów i maszyn, na przykład hydraulicznych. Częstą przyczyną usterek z nimi związanych jest ich nieprawidłowa instalacja, podczas której łatwo je uszkodzić (używając niewłaściwych narzędzi albo umieszczając w rowku z ostrymi krawędziami i narożnikami) albo zamontować je odwrotnie. Ponadto brudne uszczelki zużywają się szybciej. Jeżeli część uszczelnienia oderwała się i wpadła do szczelin między elementami, które chroni, oznacza to zbyt wysokie ciśnienie w systemie. Mogą temu zapobiegać: pierścienie ochronne, zmiana materiału uszczelnienia z elastomeru na tworzywo termoplastyczne i ograniczenie obszaru, w który może wejść uszczelka. Nieszczelność przy niskim ciśnieniu może oznaczać utratę elastyczności, a pęknięte uszczelki bywają wynikiem uwięzienia między nimi płynu, który, gdy jego ciśnienie wzrosło, je rozerwał. Ich materiał może się również okazać niekompatybilny z medium, na przykład płynem hydraulicznym, zwłaszcza ognioodpornym i biodegradowalnym w określonych temperaturach.
Dlaczego dochodzi do awarii pomp?
W pompach problemem jest kawitacja, zachodząca w wyniku za niskiego ciśnienia na końcu ssawnym pompy. Polega ona na gwałtownej przemianie cieczy w gaz przy spadku ciśnienia. Powstałe wówczas pęcherzyki powietrza implodują, kiedy ciecz przemieszcza się od strony ssącej wirnika do strony tłocznej, co wytwarza falę uderzeniową. Ta, oddziałując na pompę od wewnątrz wywołuje wibracje oraz uszkodzenia mechaniczne. Jeżeli powtarza się często, kawitacja powoduje wżery, pęknięcia wirnika i korpusu, wzrost oporu przepływu, a zatem mniejszą wydajność pompowania i skraca żywotność pompy.
Kolejny problem to korozja w wyniku reakcji chemicznych lub elektrochemicznych między materiałami pompy a medium, która pogarsza wydajność oraz jest źródłem zanieczyszczeń, wymuszając częstsze konserwacje i dłuższe przestoje. Zapobiega jej dobranie materiału do specyfiki płynów. Na przykład żeliwo jest odporne na korozję przy kontakcie z tymi o pH neutralnym i wysokim, dzięki czemu sprawdza się w pompach ogólnego przeznaczenia, górniczych, nawadniających, ale nie nadaje się do pompowania tych o niskim pH.
Jeżeli z kolei spada wydajność, może to oznaczać, że cząstki stałe z medium przywarły i nagromadziły się we wnętrzu pompy, przez co musi ona pracować ciężej, by go przemieścić. Towarzyszą też temu nadmierne drgania.
Podsumowanie
Awaria to każde zdarzenie, w którym maszyna nie działa, całkowicie albo częściowo, albo przestaje pracować zgodnie ze swoim przeznaczeniem. Termin ten zatem może obejmować różne scenariusze i poziomy dotkliwości. Przykładem są awarie nagłe, w których nieoczekiwanie urządzenie działające do tej pory bez problemu przestaje pracować. W takim przypadku wcześniej nie występują żadne niepokojące oznaki, dlatego zdarzeniom takim trudno jest przeciwdziałać. Na szczęście jednak nie powtarzają się one często ze względu na charakter przyczyn, przed którymi chronią standardowo stosowane środki. Dochodzić może także do naprzemiennego wyłączania i ponownego załączania się maszyny po restarcie, kiedy wydaje się, że wszystko wróciło do normy, nim nastąpi kolejna przerwa w pracy. Takie zdarzenia poprzedzają zwykle całkowitą awarię maszyny. Zapobiegać im można przez regularną konserwację, podobnie jak stopniowemu pogarszaniu się parametrów pracy urządzenia (szybkości, dokładności). Takich problemów można więc stosunkowo łatwo uniknąć. W zależności od specyfiki maszyny i funkcji, jaką pełni w systemie, próg tolerancji dla jej awarii jest różny. To wpływa na wybór strategii w zakresie utrzymania ruchu. Bez względu jednak na stosowane podejście zawsze warto mieć na uwadze symptomy przedstawione w artykule i monitorować najbardziej awaryjne podzespoły w myśl zasady, że lepiej zapobiegać, niż leczyć.
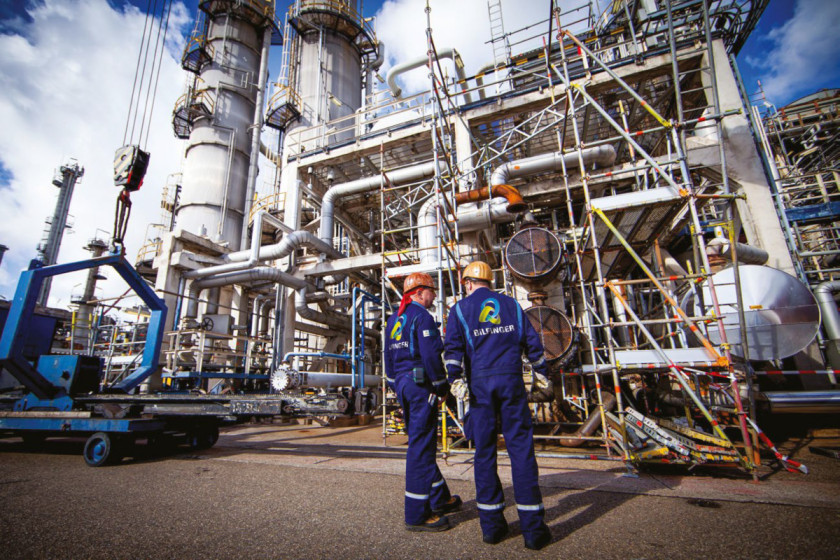
Monika Jaworowska