Promieniowanie rentgenowskie to promieniowanie elektromagnetyczne o ekstremalnie krótkiej długości fali, wynoszącej od kilku pikometrów do 10 nm, czyli mieszczącej się poza zakresem światła widzialnego, pomiędzy promieniowaniem gamma a ultrafioletowym. Odpowiada jej częstotliwość od 10 tys. THz do 100 mln THz. Z wprost proporcjonalnej zależności między częstotliwością, a energią fotonu wynika, że promieniowanie rentgenowskie to strumień wysokoenergetycznych cząstek. Powstaje ono w wyniku przyspieszania albo zwalniania naładowanych cząstek, przykładowo wiązki elektronów uderzającej w metalową płytę w lampie rentgenowskiej albo krążącej w synchrotronie (akceleratorze cząstek). Emitują je również silnie wzbudzone atomy.
Jak odkryto promienie rentgenowskie?
Promieniowanie rentgenowskie zostało odkryte w 1895 roku przez niemieckiego fizyka Wilhelma Konrada Röntgena podczas badania wpływu wiązek elektronów, zwanych wtedy promieniami katodowymi, na wyładowania elektryczne w gazach o niskim ciśnieniu. Zauważył on wówczas zaskakujący efekt uboczny – okazało się, że ekran pokryty materiałem fluorescencyjnym, który znajdował się na zewnątrz rury wyładowczej, zaczął świecić, choć był osłonięty przed światłem.
Na tej podstawie naukowiec wydedukował, że nieznane wcześniej niewidzialne promieniowanie przeniknęło ścianę rury wyładowczej, powodując świecenie ekranu. Co więcej, nieprzezroczyste obiekty, które znajdowały się na drodze między rurą a ekranem, dla promieni tych okazały się przenikalne. By udowodnić ich istnienie, wykorzystując fakt, że promieniowanie oddziałuje na emulsję fotograficzną, Röntgen wykonał na kliszy zdjęcie kości ręki. Było to pierwsze prześwietlenie rentgenowskie.
Jak wykryć zanieczyszczenia na obrazie rentgenowskim?
Naświetlanie promieniowaniem rentgenowskim znalazło tak szerokie zastosowanie jako metoda inspekcji dzięki jego dwóm właściwościom. Pierwszą jest przenikalność przez materiały, które są nieprzezroczyste dla światła widzialnego, a drugą różnice w jego absorpcji przez różne materiały. Ilość energii promieniowania rentgenowskiego pochłaniana przy przejściu przez nie jego wiązki zależy od ich liczby atomowej, gęstości i grubości. Przykładowo produkty spożywcze składają się z pierwiastków o małej masie atomowej, poniżej 16, głównie wodoru, węgla i tlenu i mają małą gęstość, podczas gdy zanieczyszczenia zazwyczaj zawierają pierwiastki o dużej masie atomowej i dużej gęstości. W efekcie pierwsze słabiej, a drugie silniej absorbują promienie rentgenowskie. To oznacza, że prześwietlone na zdjęciu rentgenowskim te pierwsze będą zaznaczone jaśniejszym, zaś drugie ciemniejszym odcieniem szarości. To pozwala na ich rozróżnienie, czyli w praktyce wykrycie zanieczyszczeń w produkcie. Podobnie grubsze fragmenty będą ciemniejsze, co z kolei pozwala na detekcję poza ciałami obcymi, także defektów. Dla uproszczenia, porównując stopień pochłaniania promieni rentgenowskich przez różne materiały, używa się ich gęstości. Na przykład produkty spożywcze zwykle charakteryzują się dużą zawartością wody, więc ich gęstość jest zbliżona do jej gęstości (1 g/cm3). Wartość ta jest w inspekcji rentgenowskiej żywności wartością odniesienia – im większa jest różnica pomiędzy nią i gęstością zanieczyszczeń, tym łatwiej je wykryć. Dlatego przykładowo metale żelazne, większość metali nieżelaznych i stal nierdzewna o gęstościach od 7 do 8 g/cm³ są łatwo rozpoznawalne na zdjęciu rentgenowskim. Wykryć na nim można także cząstki z aluminium, szkła, kamienie i kości, których gęstość mieści się w przedziale 2‒3 g/cm³. Z kolei przykładowo drewno, mimo że jest twarde, ma małą gęstość i dlatego zwykle nie jest wykrywalne. Podobnie trudna, a nawet niemożliwa jest detekcja tworzyw sztucznych, jak polipropylen (0,9 g/cm³), owadów, pestek, włosów (0,3 g/cm³).
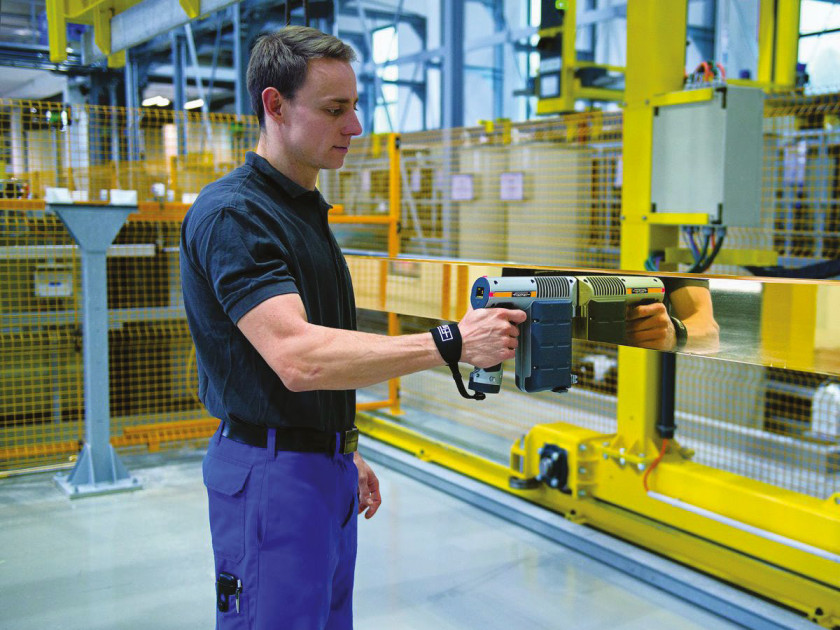
Automaty do inspekcji rentgenowskiej
Systemy inspekcji rentgenowskiej składają się z części sprzętowej i programowej. Główne elementy pierwszej to źródło oraz detektor promieniowania. Promienie rentgenowskie są wytwarzane w generatorze w postaci szklanej rury z katodą z żarnikiem, anodą i tarczą wolframową. Żarnik katody rozgrzany do wysokiej temperatury przez przepływ prądu elektrycznego jest źródłem elektronów. Wysokie napięcie przyłożone między anodą a katodą przyspiesza je, a te uderzając w tarczę, emitują promieniowanie rentgenowskie. Generator dla bezpieczeństwa jest ekranowany miedzią i umieszczony w od wewnątrz również pokrytej miedzią obudowie wypełnionej olejem. Pełni on funkcję chłodziwa i izolatora elektrycznego. Promienie rentgenowskie opuszczają generator okienkiem w obudowie, przechodząc przez wbudowany w nie kolimator, i padają na detektor. Na drodze pomiędzy ich źródłem a odbiornikiem umieszcza się obiekt inspekcji, który część ich absorbuje a część przepuszcza. Zwykle w obrębie automatu do inspekcji jest on transportowany na przenośniku. Tradycyjnie detektorem była klisza, która wymagała wywołania. Obecnie jednak coraz popularniejsza staje się radiografia cyfrowa, w której wynik prześwietlenia jest dostępny od razu w postaci obrazu na komputerze. Detektorami są w tym przypadku płytki czułe na promienie rentgenowskie, generujące proporcjonalne do niego sygnały elektryczne, przekształcane potem w obraz. Wyróżnia się dwa ich typy: do konwersji pośredniej i bezpośredniej. Pierwsze pokrywa materiał, który przekształca promieniowanie rentgenowskie w światło widzialne przetwarzane w sygnał elektryczny przez matrycę światłoczułych diod (fotodiod). Z kolei detektory z bezpośrednią konwersją pokrywa fotoprzewodnik, jak amorficzny selen lub tellurek kadmu. Sygnał przez niego generowany zasila mikroelektrody. Dzięki temu, że nie występuje przetwarzanie pośrednie, straty sygnału są mniejsze, a obraz jest ostrzejszy i ma większą rozdzielczość. W przemyśle upowszechnia się poza tym tomografia komputerowa, popularna metoda w diagnostyce medycznej. Dzięki temu, że jej wynikiem jest obraz 3D, pozwala nie tylko stwierdzić defekt albo obecność zanieczyszczeń, ale również je oszacować, na przykład ilościowo.
W uproszczeniu przemysłowy tomograf komputerowy składa się z trzech elementów: źródła promieniowania, detektora i bardzo precyzyjnego stołu obrotowego. Rejestruje on zbiór dwuwymiarowych obrazów powstających przy prześwietlaniu obiektu inspekcji obracanego wokół własnej osi za każdym razem o określony kąt. W zależności od tego, z jakim krokiem jest to wykonywane liczba prześwietleń może sięgać setek i więcej. Obrazy te są następnie przetwarzane w oprogramowaniu implementującym algorytmy rekonstrukcji, generującym trójwymiarowy rozkład współczynnika absorpcji w obiekcie. Specjalne oprogramowanie służy też do wizualizacji i analizy trójwymiarowych modeli i przekrojów. W zależności od celu inspekcji te ostatnie bazują na różnych algorytmach. Na przykład w detekcji zanieczyszczeń popularne jest progowanie polegające na ustaleniu wartości progowej, poniżej którego piksele obrazu klasyfikowane są jako fragmenty obiektu inspekcji, a pozostałe uznawane są za ciała obce.
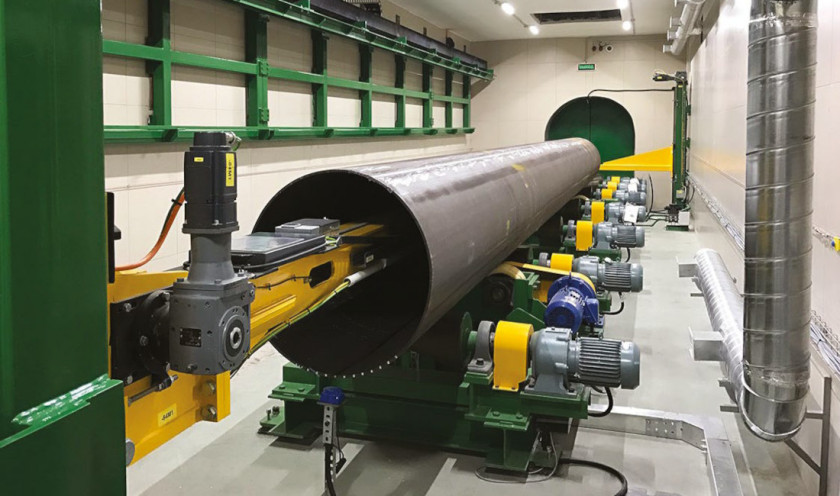
Aplikacje
Głównym zastosowaniem inspekcji rentgenowskiej jest wykrywanie zanieczyszczeń i defektów w produkcie. W przypadku na przykład przemysłu spożywczego oznacza to szeroki zakres aplikacji. Przykładami są sprawdzanie: czy w bombonierce zapakowano właściwą liczbę czekoladek, czy każdy pączek został wypełniony nadzieniem, czy ser jest gotowy do spożycia. W tym ostatnim wykorzystuje się fakt, że w trakcie dojrzewania niektóre rodzaje sera, takie jak Emmental czy Leerdammer wytwarzają dziury (oczka). Rozmiary i gęstość tych otworów są miarą jakości sera. Tradycyjnie sprawdzano to, pobierając próbki jego rdzenia, ale metoda ta jest destrukcyjna, a dodatkowo jeśli jest to ręczny proces, nieefektywna. Inspekcja rentgenowska jest szybsza i pozwala na analizę całego sera. Jeżeli dowiedzie, że gęstość dziur jest zbyt mała ser można przechowywać dłużej, pozwalając na jego dojrzenie. Radiografia w przemyśle spożywczym jest także wykorzystywana w kontroli uszczelnień opakowań. Przykładem funkcji automatów inspekcji rentgenowskiej użytecznej w tej branży jest też wyznaczanie masy. Jest ona obliczana w oparciu o pomiar różnicy jasności na radiografie między produktem referencyjnym a wyrobem mierzonym tego samego rodzaju. Najlepiej jest to wyjaśnić na przykładzie – mierząc w systemie inspekcji rentgenowskiej jasność produktów o grubości 50 mm i 45 mm, uzyskamy różnicę w ich jasności na obrazie rentgenowskim wynoszącą 10% (45 mm / 50 mm = 0,9). Jeśli przyjmiemy produkt pierwszy za odniesienie i dla następnej partii wyrobu zmierzymy jasność o 50% mniejszą, oznaczać to będzie również 50% różnicy w grubości mierzonej próbki (25 mm) względem tej referencyjnej. Znając gęstość produktu, można na tej podstawie obliczyć jego masę.
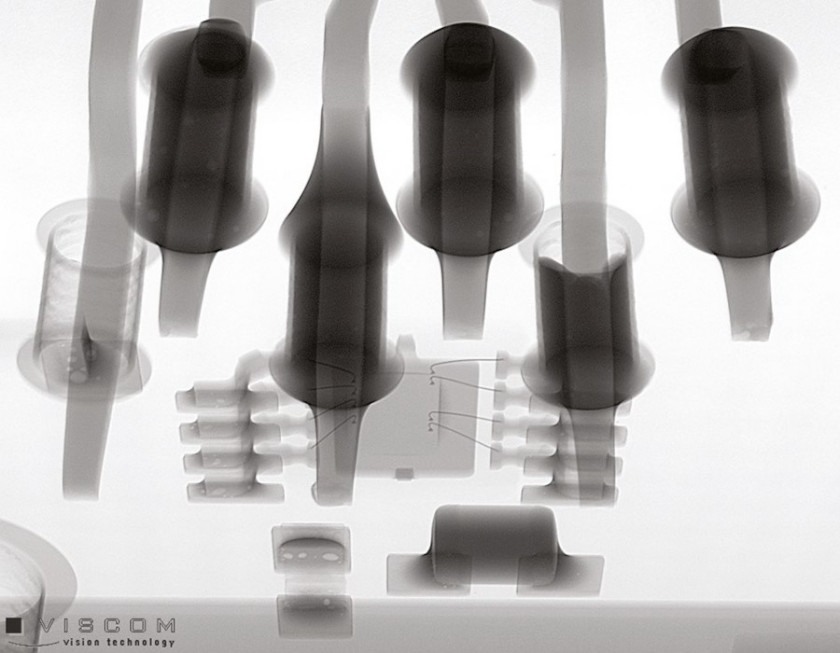
Monika Jaworowska