Programowalne sterowniki logiczne, wykorzystywane do sterowania urządzeniami i maszynami, są kluczowymi komponentami systemów automatyki w przemyśle i poza nim. Zbudowane są z wejść i wyjść, analogowych i cyfrowych, modułów komunikacyjnych, pamięci i jednostki obliczeniowej. Ta ostatnia analizuje dane z wejść, by stosownie do nich zmienić stan wyjść sterujących. Sterowniki PLC programuje się do wykonywania określonych zadań. Ich programy składają się z sekwencji cyklicznie wykonywanych poleceń, które implementują algorytmy sterowania. Uniwersalność, kompaktowość, modułowość i łatwość przeprogramowania zapewniły sterownikom tego typu dużą popularność.
PLC w wersji safety to natomiast specjalizowane sterowniki, które są przeznaczone do zastosowań o krytycznym znaczeniu dla bezpieczeństwa. W porównaniu ze standardowymi wprowadza się w nich rozwiązania, sprzętowe i programowe, dzięki którym wykrywają usterki, błędy i zagrożenia w systemie oraz odpowiednio na nie reagują. Dzięki redundancji i funkcjom diagnostycznym są niezawodne. Sterowniki bezpieczeństwa są też certyfikowane na zgodność z normami dotyczącymi bezpieczeństwa funkcjonalnego (PN-EN 2061, ISO 13849-1, PN-EN 61508).
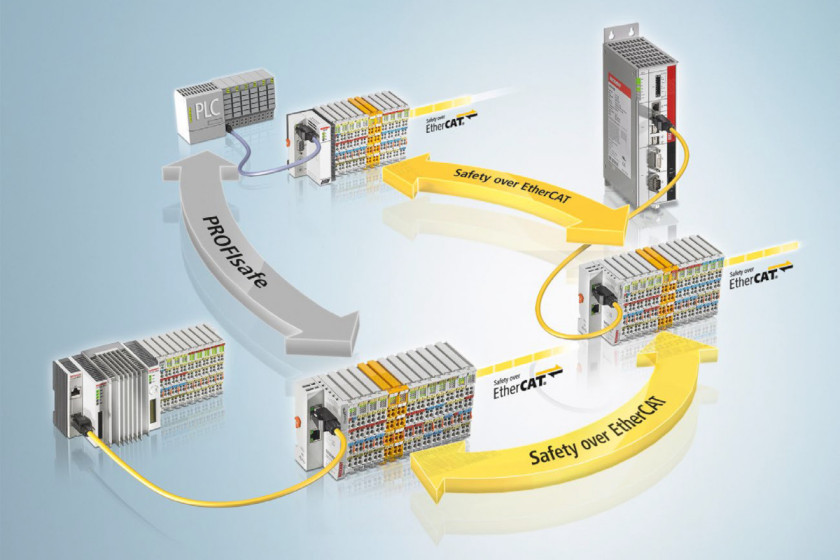
PLC a safety PLC
Wskazać można trzy główne różnice pomiędzy sterownikami bezpieczeństwa a standardowymi sterownikami PLC. Dotyczą one architektury oraz realizacji wejść i wyjść.
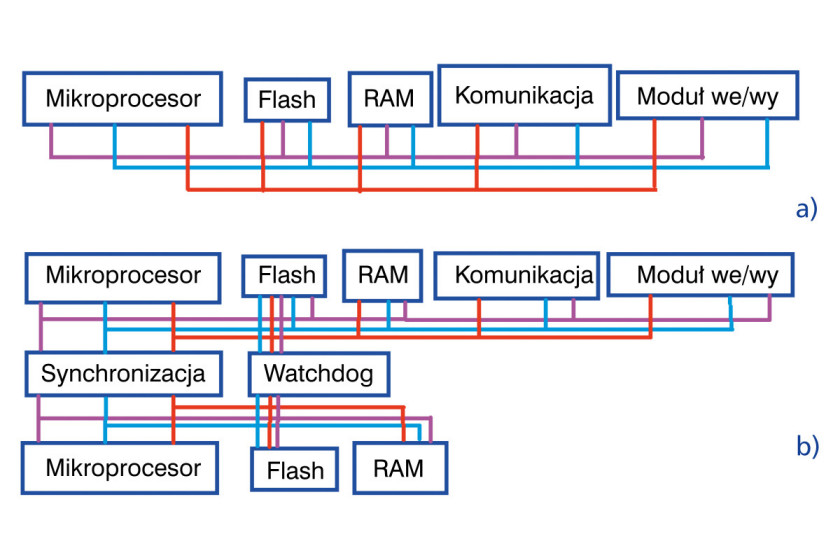
Jeżeli chodzi o pierwszą, na rysunku 1 przedstawiono schematy blokowe obu typów PLC. W przypadku standardowych sterowników programowalnych wyróżniamy: jeden mikroprocesor, który wykonuje program, pamięć Flash, w której przechowywany jest kod programu, pamięć RAM, w której zapisywane są wyniki obliczeń, porty komunikacyjne oraz wejścia i wyjścia do wykrywania stanów obiektu sterowania oraz ich zmiany. Na schemacie blokowym sterownika w wersji safety z kolei przedstawiono: redundantne mikroprocesory, pamięć Flash oraz pamięć RAM, które są stale monitorowane przez układy watchdoga i synchronizacji.
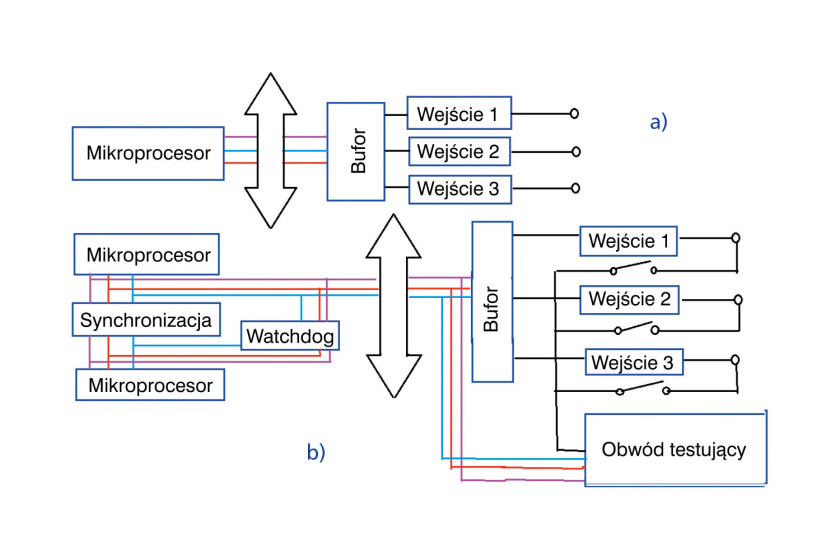
Na rysunku 2 można porównać sposób realizacji wejść w obu typach sterowników. W standardowych PLC nie ma możliwości wewnętrznego testowania funkcjonalności obwodów wejściowych, inaczej niż w przypadku sterowników bezpieczeństwa. W tych każdemu wejściu przypisany jest obwód testowy zrealizowany wewnętrznie. W celu zweryfikowania sprawności wejść okresowo podawane są na nie sygnały kontrolne.
Wejścia i wyjścia
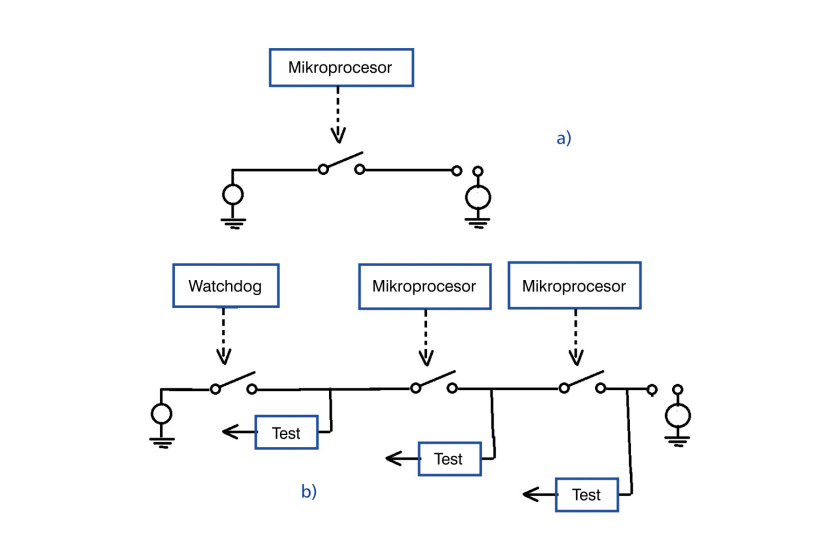
Na rysunku 3 zestawiono schematy blokowe wyjść cyfrowych sterownika PLC i sterownika w wersji safety. Ten pierwszy obejmuje pojedynczy obwód przełączający. W drugim przypadku obydwa wyłączniki bezpieczeństwa są sterowane przez oddzielny mikroprocesor. Każdemu z nich jest przyporządkowany obwód testujący, podobnie jak głównemu sterownikowi wyjścia. Dzięki temu PLC wykrywa zarówno awarię tego ostatniego, jak i problemy w którymkolwiek z wyłączników bezpieczeństwa, z powodu awarii przełącznika lub mikroprocesora.
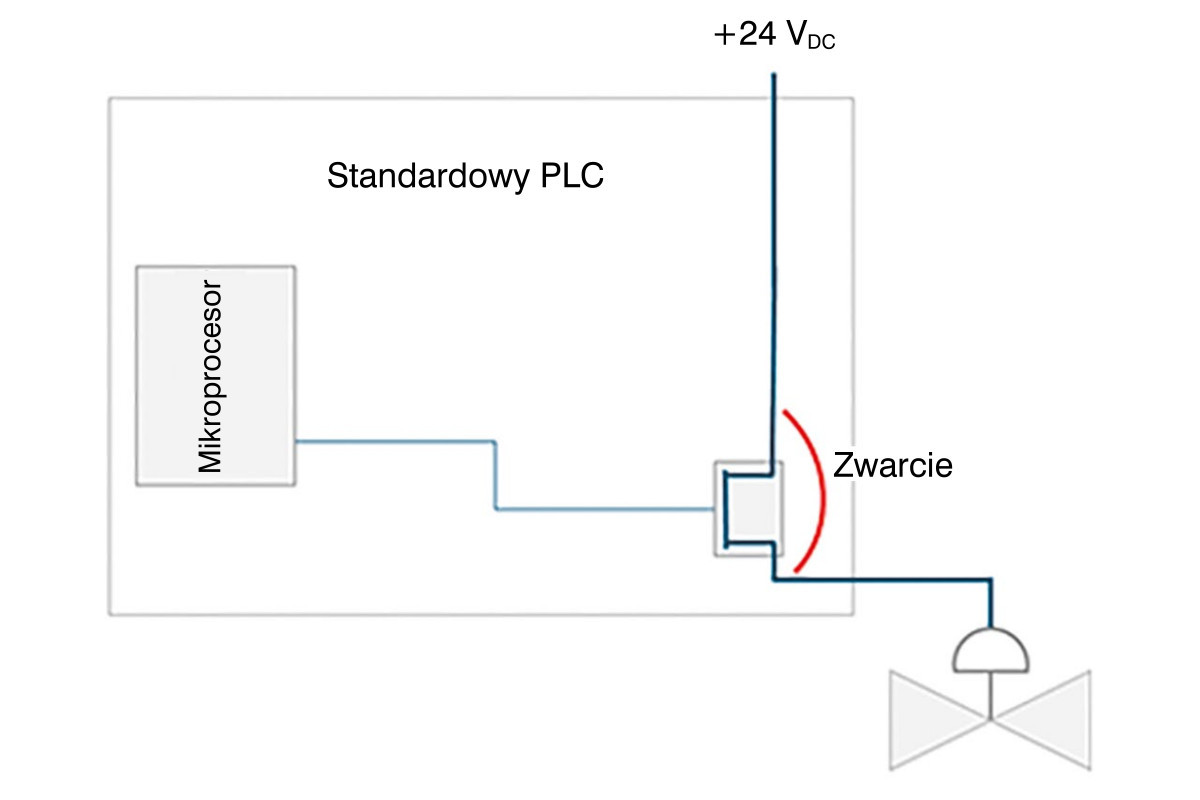
Na rysunku 4 przedstawiono uproszczony schemat wyjścia cyfrowego sterownika programowalnego ogólnego przeznaczenia. W razie gdy tranzystor wyjściowy zostanie zwarty, wystąpi niebezpieczna sytuacja, ponieważ zawór nie zamknie się zgodnie z poleceniem mikroprocesora.
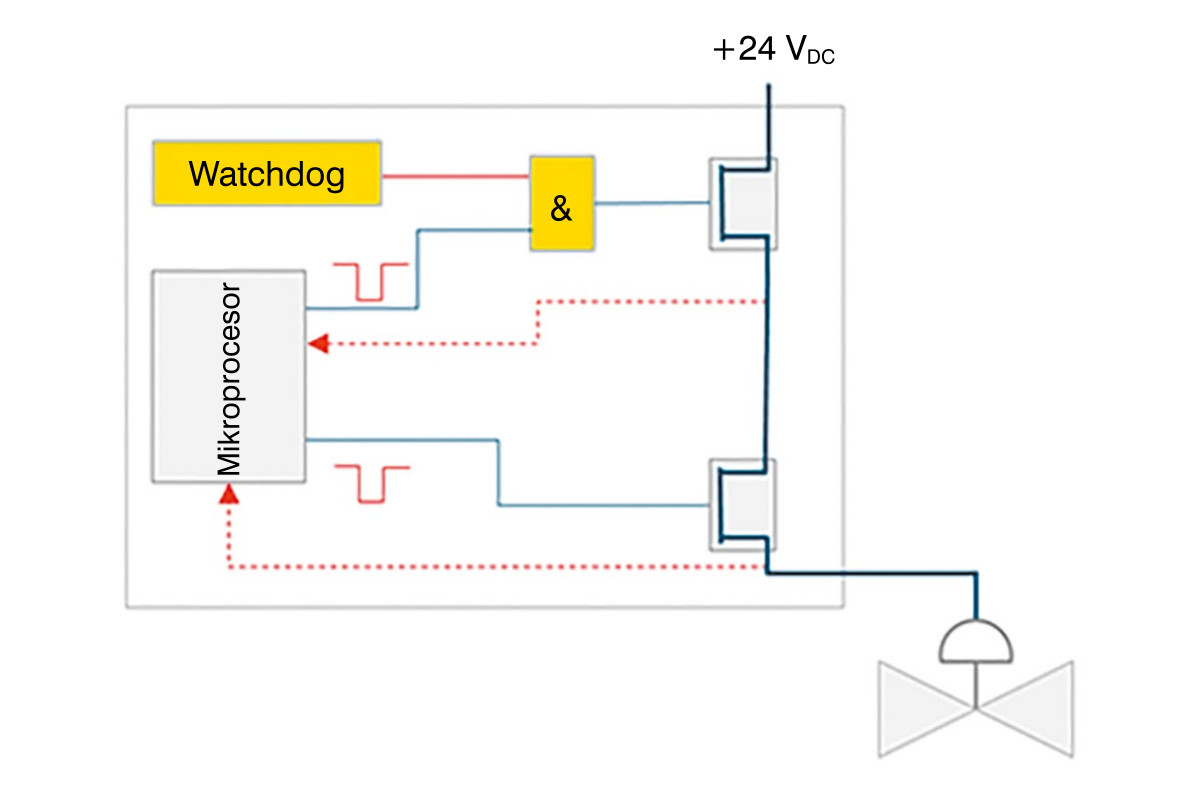
W sterowniku PLC w wersji safety (rys. 5) wykrywanie zwarć zapewnia procedura diagnostyczna z wykorzystaniem mikroimpulsów oraz obwodu monitorowania stanu wyjścia. W przypadku zwarcia aktywowany zostanie alarm. Uzupełnieniem jest drugi tranzystor włączony szeregowo oraz układ watchdoga, który porównuje stan obu tranzystorów. Układ z rysunku 5 w sterownikach bezpieczeństwa dubluje się by zapewnić redundancję (rys. 6).
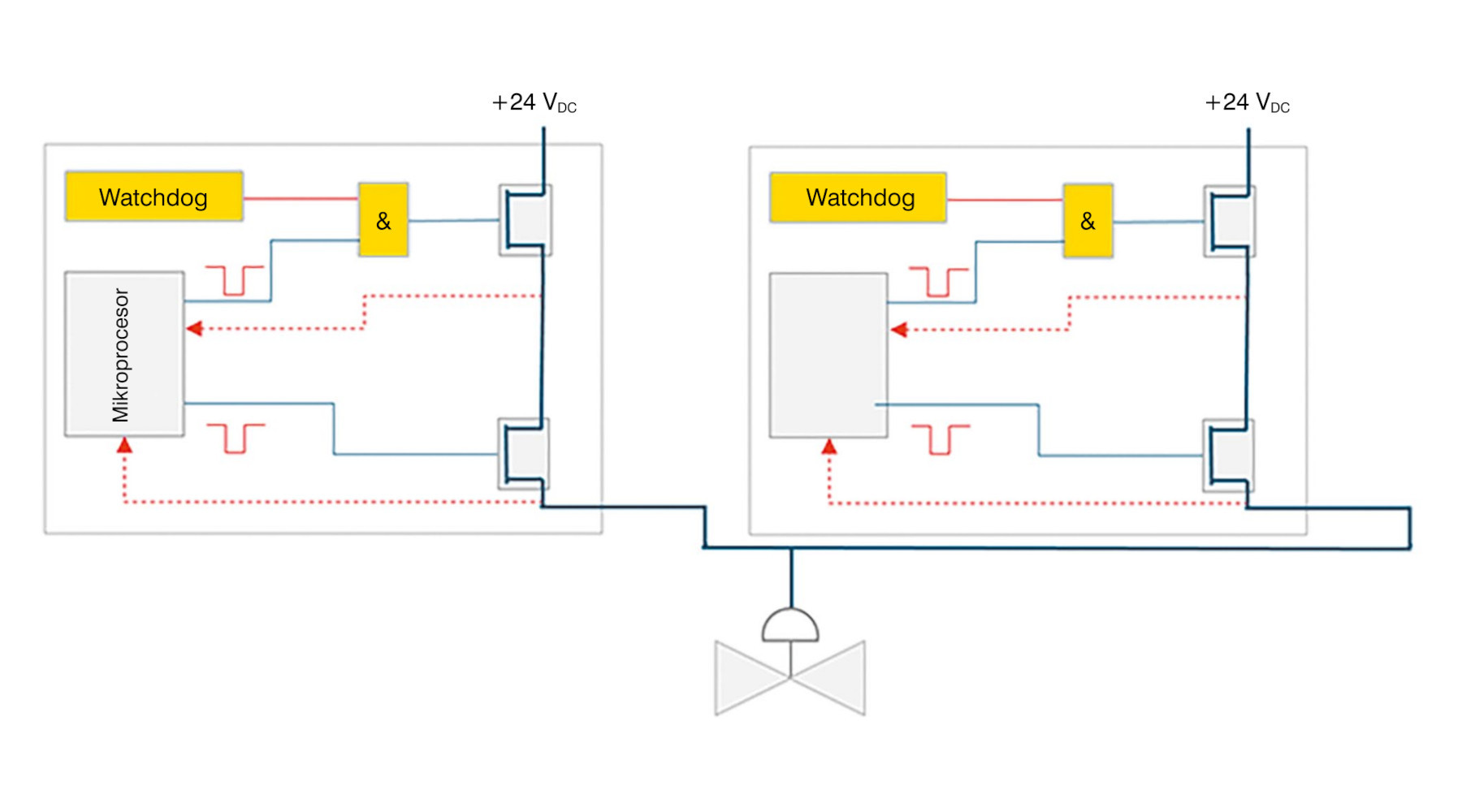
Rozwiązania programowe
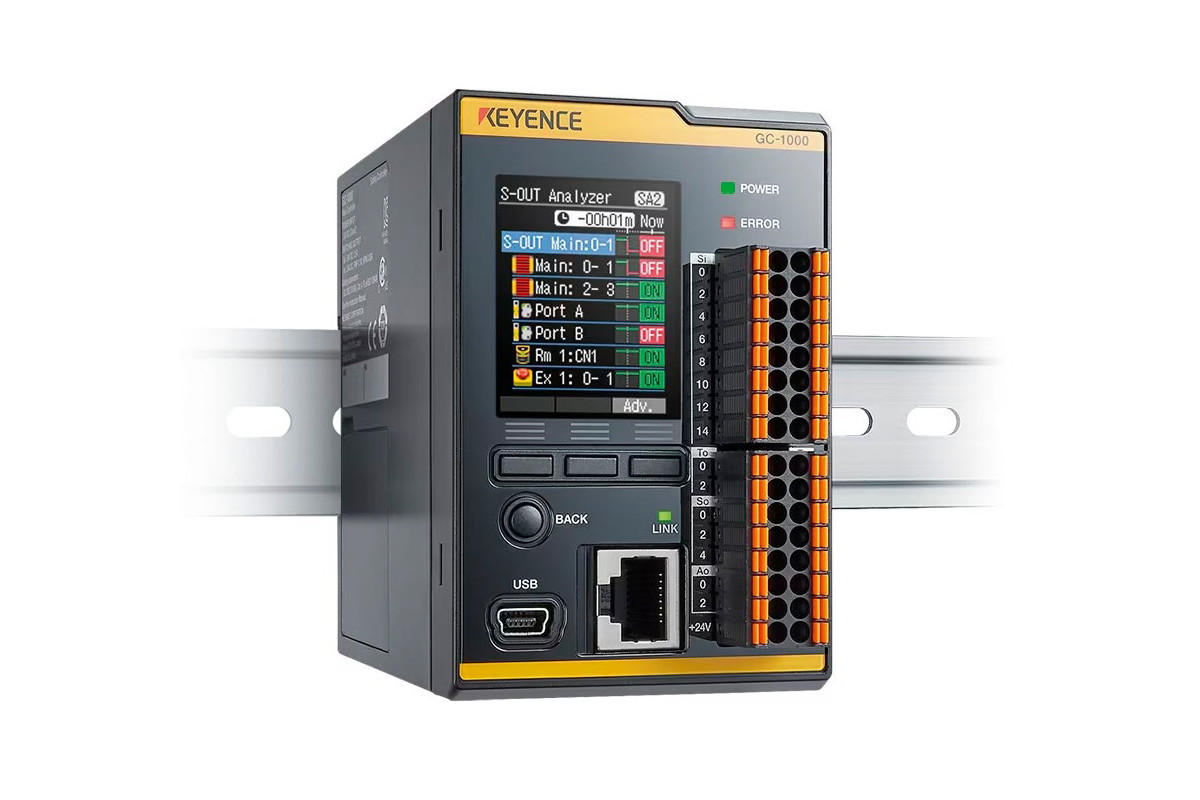
Jeżeli chodzi o stronę programową, w sterownikach bezpieczeństwa wykorzystuje się dwa oddzielne programy. Kod pierwszego implementuje algorytm sterowania procesem, natomiast drugi realizuje wyłącznie funkcje bezpieczeństwa. Oba są wykonywane równocześnie, przy czym ten drugi jest wykonywany wielokrotnie w jednym cyklu wykonania pierwszego kodu. Zobrazowano to na rysunku 7. Każdy żółty blok reprezentuje na nim jedno wykonanie programu bezpieczeństwa, zaś blok szary – jeden cykl programu podstawowego. Okresowo ten pierwszy przerywa program główny, weryfikuje funkcje bezpieczeństwa i informację zwrotną o ich stanie przekazuje do programu podstawowego. Jak wynika z rysunku 7 program bezpieczeństwa został wykonany pięć razy w ciągu pojedynczego obiegu programu głównego.
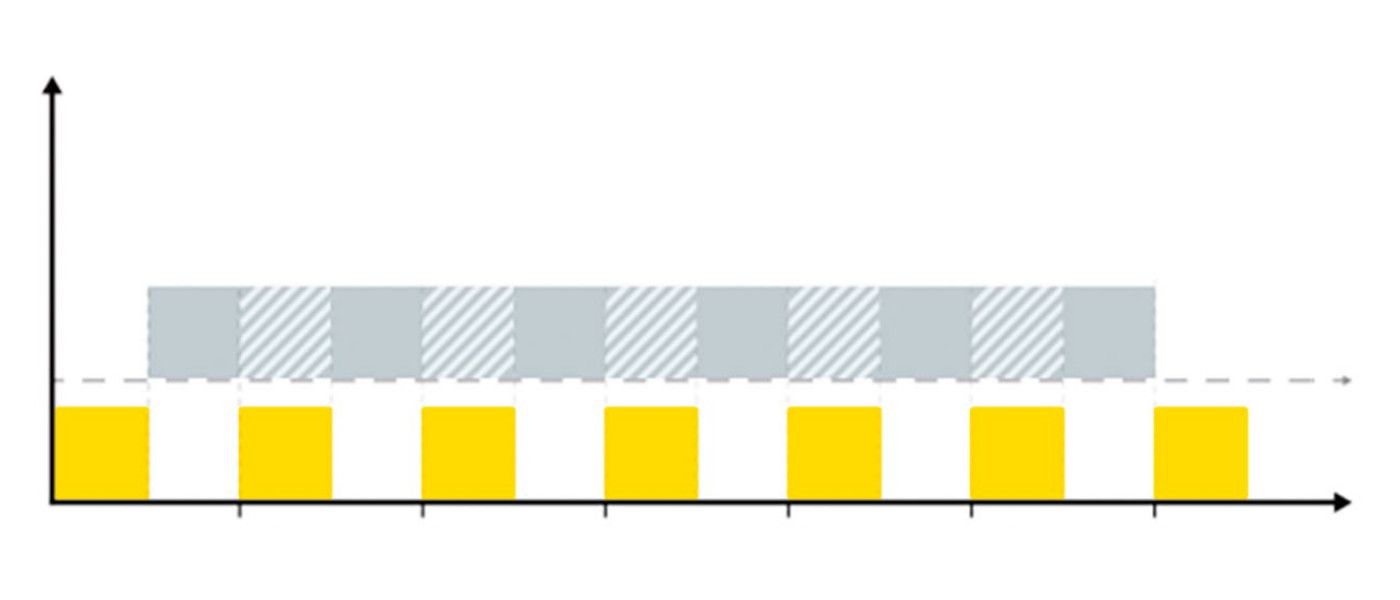
Zwykły PLC...
Standardowe sterowniki programowalne także bywają wykorzystywane w systemach związanych z bezpieczeństwem. W takim przypadku zazwyczaj konfiguruje się je parami. Nadmiarowy sterownik służy wtedy do zapewnienia bezpiecznego i uporządkowanego zatrzymania procesu w razie awarii tego głównego. Oprócz redundantnych sterowników wykorzystuje się wówczas dodatkowe wejścia do monitorowania sygnałów wyjściowych systemu bezpieczeństwa i więcej wyjść do generowania impulsów testowych dla modułów wejściowych systemu bezpieczeństwa. Ponadto wymagane jest niestandardowe oprogramowanie do jego monitorowania, sterowania i diagnozowania. Ostatecznie więc takie rozwiązanie charakteryzuje duży stopień skomplikowania pod względem sprzętowym i programowym. Jest to wyzwanie projektowe i wiąże się z większymi kosztami utrzymania.
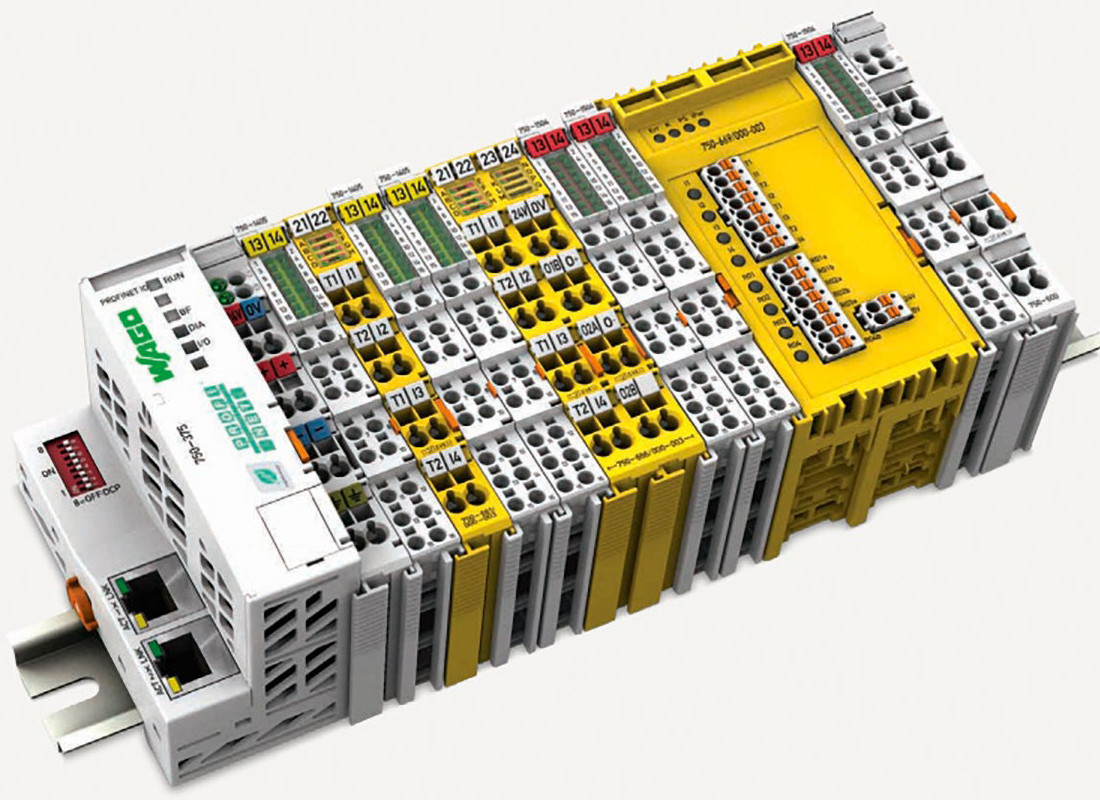
...czy w wersji safety?
Wybierając sterownik bezpieczeństwa, uzyskujemy oszczędności w zakresie liczby komponentów i okablowania. Dodatkową korzyścią jest także większa elastyczność – modyfikacje są łatwiejsze do wprowadzenia, gdyż wymagają jedynie zmian w programie sterującym, a nie modyfikacji sprzętu i okablowania. Krótszy jest też czas projektowania, instalacji i uruchomiania systemu z PLC w wersji safety. Z drugiej strony jednak choć sterowniki bezpieczeństwa zapewnią oszczędności w dłuższej perspektywie, przeważnie wybierając je, trzeba się liczyć z większymi kosztami początkowymi. Te bywają kwestią zaporową w prostych zastosowaniach, na przykład w systemach z pojedynczym elementem bezpieczeństwa, jak przycisk stop.
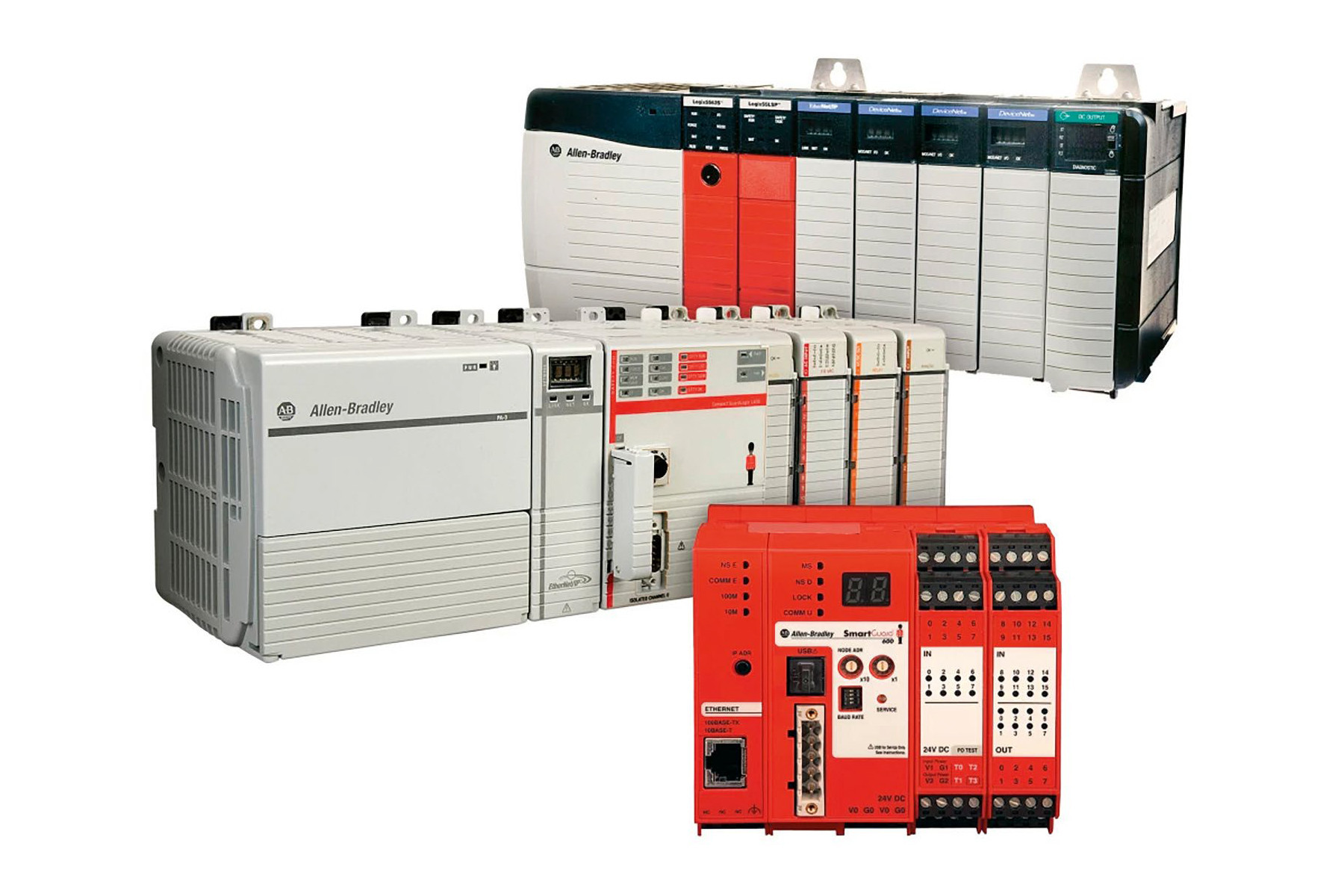
Monika Jaworowska