W pomiarach zmian tej wielkości wykorzystuje się zazwyczaj mostek Wheatstone’a (rys. 1). Jeżeli w takim układzie wartości rezystancji R1, R2, R3 oraz R4 spełniają warunek R1/R2 = R4/R3, a napięcie wejściowe zostanie przyłożone pomiędzy punktami A i C, wówczas między punktami B i D nie będzie różnicy potencjałów. Mostek jest wtedy zrównoważony.
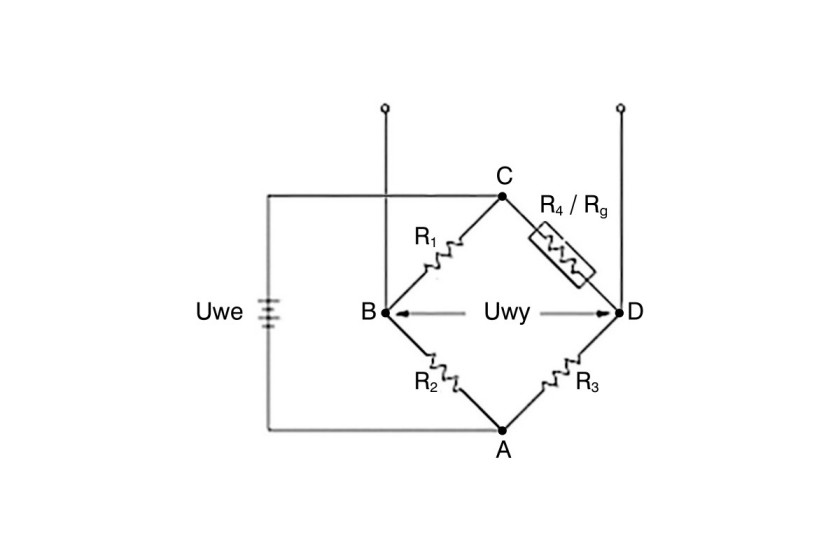
Jeżeli w gałęzi z rezystorem R4 zamiast niego włączony zostanie tensometr Rg, natomiast pozostałe oporniki będą miały stałą rezystancję, zmiana oporu Rg spowoduje stan niezrównoważenia mostka. W konsekwencji, proporcjonalnie do naprężenia tensometru, zmianie ulegnie napięcie wyjściowe mostka.
Przetworniki w konfiguracji mostka Wheatstone’a zwykle wykorzystują jednak cztery tensometry. To gwarantuje większą czułość oraz rozdzielczość pomiaru w porównaniu z układem pomiarowym tylko z pojedynczym tensometrem. Zapewniona jest także wówczas kompensacja temperaturowa, ponieważ zmiana rezystancji spowodowana zmianami temperatury będzie taka sama dla wszystkich ramion mostka pomiarowego.
Konfiguracje pomiarowe
Sposób rozmieszczenia tensometrów na mierzonym obiekcie warunkuje to, jaki rodzaj odkształcenia można zmierzyć (patrz rys. 2). W konfiguracji jak na rysunku 2a mierzone jest odkształcenie zginające ɛa. Jest ono równe ilorazowi naprężenia zginającego i modułu sprężystości Younga E. Naprężenie zginające jest z kolei równe momentowi zginającemu podzielonemu przez wskaźnik wytrzymałości na zginanie, który w przypadku prostokątnego przekroju poprzecznego wynosi bh²/6. Tensometry w tej konfiguracji wykorzystuje się do określenia obciążenia pionowego Fv:
Fv = E · ɛa · bh²/6 · l.
Na rysunku 2b został przedstawiony układ pomiarowy odkształcenia osiowego ɛb równego naprężeniu osiowemu podzielonemu przez moduł sprężystości Younga. Naprężenie osiowe z kolei odpowiada stosunkowi obciążenia osiowego do pola przekroju poprzecznego wynoszącego w tym przypadku bh. Tensometry w takiej konfiguracji wykorzystuje się do określania obciążeń osiowych Fa:
Fa = E · ɛb · bh.
W układzie jak na rysunku 2c, przez pomiar odkształcenia pod kątem 45º, mierzone jest odkształcenie ścinające równe naprężeniu ścinającemu podzielonemu przez moduł sprężystości poprzecznej. Naprężenie ścinające jest z kolei wprost proporcjonalne do momentu powierzchniowego wokół osi neutralnej oraz obciążenia pionowego, natomiast odwrotnie proporcjonalne do grubości i momentu bezwładności. Tensometry w takiej konfiguracji można zatem wykorzystać do określenia obciążeń pionowych Fv. W układzie jak na rysunku 2d z kolei wyznaczane są odkształcenia skrętne pozwalające na określenie momentów skręcających.
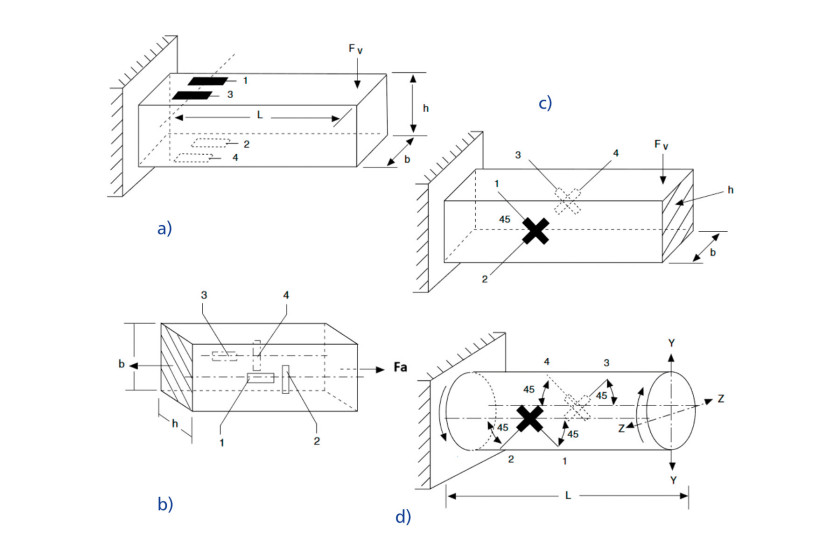
Materiały tensometrów
Przy wyborze tensometru należy wziąć pod uwagę właściwości materiału, z jakiego go wykonano. Najważniejsze parametry to: współczynnik czułości odkształceniowej, rezystancja, współczynnik temperaturowy współczynnika czułości odkształceniowej i współczynnik termiczny rezystancji.
Najpopularniejszymi materiałami wykonania tensometrów są stopy miedzi z niklem i stopy niklu z chromem. W czujnikach tego typu wykorzystuje się także piezorezystancyjne właściwości germanu i krzemu. Chociaż większa rezystancja jednostkowa i czułość tensometrów półprzewodnikowych są ich niezaprzeczalnymi zaletami, ich większa wrażliwość na zmiany temperatury oraz tendencja do dryftu są wadami w porównaniu z sensorami z folii metalicznej. Ważne ograniczenie tensometrów półprzewodnikowych to również nieliniowa zależność rezystancji od odkształcenia, co próbuje się kompensować programowo.
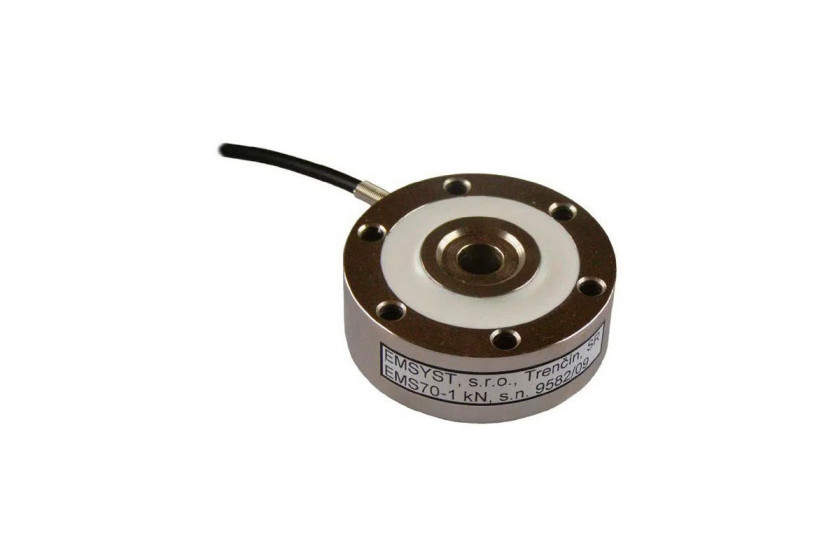
Konstrukcje tensometrów
Tensometry typowo mają postać siatki z bardzo cienkiego metalowego drutu, folii albo materiału półprzewodnikowego połączonego z naprężoną powierzchnią albo matrycą nośną cienką warstwą spoiwa, na przykład żywicy epoksydowej. Kiedy obiekt (a wraz z nim matryca nośna) ulega naprężeniu, odkształcenie jest przenoszone na materiał siatki przez klej. Siatkę wykonuje się w taki sposób, aby zmaksymalizować rezystancję, jednocześnie zapewniając kompaktowość przez minimalizację jej długości i szerokości.
Tensometry klejone mają liczne zalety. Są tanie i bardzo czułe, mogą osiągnąć dokładność rzędu +/–0,10%, jedynie w umiarkowanym stopniu ulegają wpływowi temperatury, mają małe wymiary i są lekkie. Tensometry oporowe ze spoiwem są wykorzystywane w pomiarach odkształceń statycznych i dynamicznych. Sprawdzają się w różnorodnych warunkach środowiskowych – mogą mierzyć odkształcenia w turbinach silników odrzutowych, pracując w ekstremalnie wysokich temperaturach, jak i w zastosowaniach z płynami kriogenicznymi, w temperaturach tak niskich jak –300°C.
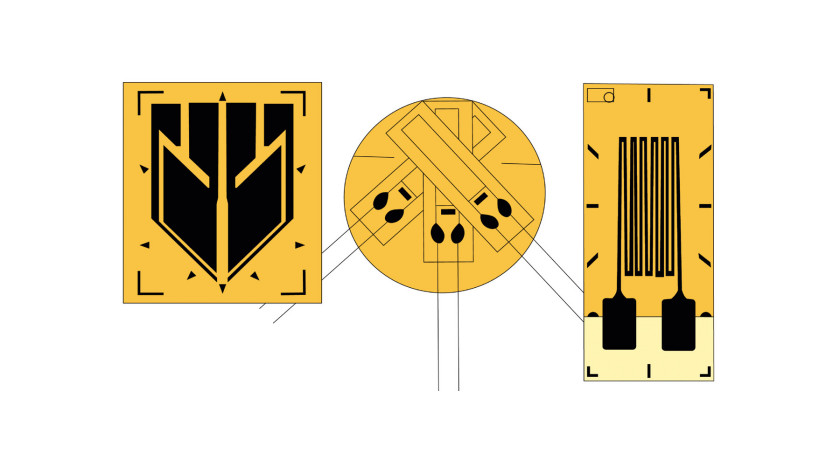
Klejenie i przygotowanie powierzchni
Pomiary z wykorzystaniem tensometrów są wiarygodne tylko wówczas, gdy mierzone odkształcenie zostanie bezstratnie przeniesione na element rezystancyjny. Spełnienie powyższego warunku zależy od ciągłości oraz elastyczności połączenia pomiędzy nim a odkształcanym podłożem. Na to z kolei wpływa typ kleju i metoda jego aplikacji. Przykładowo dostępne są spoiwa o konsystencji, dzięki której sprawdzają się w przyklejaniu tensometrów na powierzchniach porowatych, wykonanych z chłonnych materiałach. Kleje szybkoschnące wymagają z kolei szybkiej aplikacji i dobrej dostępności do miejsca ich nakładania. Ważna jest także temperatura aplikacji spoiwa i dopuszczalna temperatura użytkowa.
Przed naniesieniem kleju zwykle powierzchnia, na którą będzie aplikowany, wymaga obróbki. Od jej wykonania zależy przyczepność oraz trwałość połączenia. Rodzaj oraz zakres działań w ramach przygotowania powierzchni zależy od materiału wykonania obiektu pomiaru i jego stanu, tj. stopnia zużycia lub zabrudzenia jego powierzchni.
Na przykład w przypadku metali celem jest uzyskanie powierzchni pozbawionej porów, nierówności i pozostałości tlenków, niezbyt chropowatej i łatwo zwilżalnej. W tym celu, w zależności od potrzeb, przeciera się je, szlifuje, odtłuszcza, myje, suszy.
Powinno się przy tym pamiętać, że osadzanie się kurzu, utlenianie, adsorpcja wilgoci, par, gazów następuje w sposób ciągły. To powoduje ponowne zanieczyszczenie przygotowanej powierzchni, zmniejszając zdolność wiązania aplikowanych klejów. Dlatego spoiwo powinno się nakładać jak najszybciej po oczyszczeniu powierzchni klejenia. Dotyczy to szczególnie metali, które się szybko utleniają i jeżeli spoiwo jest aplikowane w atmosferze przemysłowej.
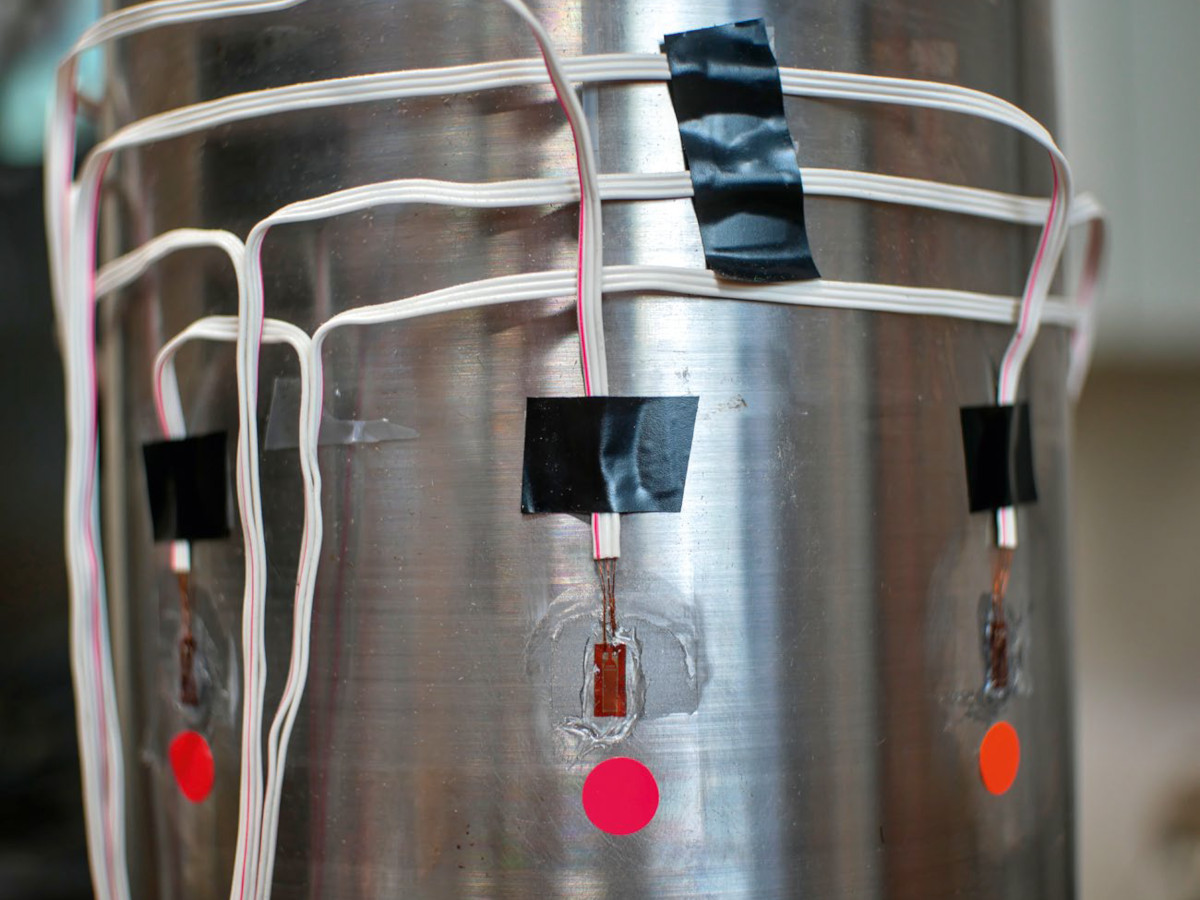
Monika Jaworowska