Roboty na tytułowych stanowiskach programuje się do wykonywania określonej sekwencji ruchów z założoną precyzją oraz powtarzalnością. Są często wyposażone w czujniki, które pozwalają im wykrywać położenie i orientację obiektów, którymi manipulują. Ich szybkość i wydajność zależą od konstrukcji mechanicznej (lekkie materiały wykonania, szybkie napędy) i algorytmów sterowania. Zrobotyzowane stanowiska pick and place projektuje się też tak, aby minimalizować odległość, na jaką należy przenosić obiekty.
Roboty na stanowiskach pick and place
Kluczowym zadaniem podczas projektowania stanowiska pick and place jest wybór robota. W tym zastosowaniu wykorzystuje się maszyny różnych typów.
Przykładem są roboty kartezjańskie, które mają trzy ortogonalne osie ruchu skoordynowane przez pojedynczy kontroler. Osie stanowią siłowniki liniowe, z chwytakiem zamocowanym na karetce na najbardziej zewnętrznej z nich. Są projektowane do poruszania się w osiach X– Y, X– Z albo X– Y–Z. Ich obszar roboczy stanowi płaszczyzna dwuwymiarowa albo trójwymiarowe pudełko, zaś liczba stopni swobody wynosi trzy plus ewentualnie oś obrotu chwytaka.
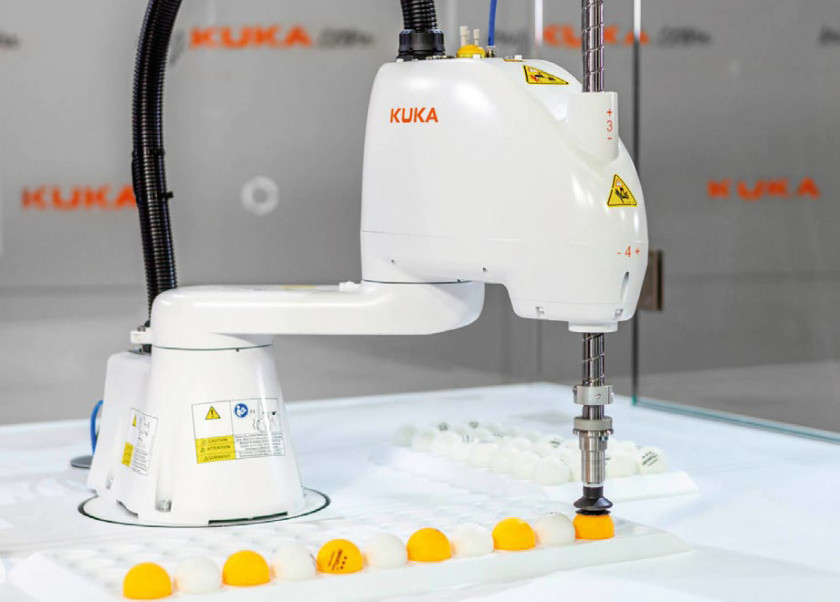
Ich zalety to: konfigurowalność, skalowalna przestrzeń robocza, łatwe sterowanie, duża dokładność, duży udźwig i kompaktowość w pionie. Z drugiej strony zajmują dużo miejsca w poziomie, mają ograniczoną liczbę stopni swobody, są typowo wolniejsze niż inne typy robotów. W zadaniach pick and place głównie sprawdzają się, jeżeli trzy (cztery) stopnie swobody wystarczą, jeśli wymagana jest duża przestrzeń robocza, kiedy wystarczy ograniczony ruch w pionie i przy dużej liczbie obiektów, które trzeba przenosić.
Roboty SCARA zbudowane są z zamocowanego na sztywnej podstawie dwuczłonowego ramienia ze złączami obrotowymi z poziomą osią obrotu i głowicy wyposażonej w przegub pryzmatyczny, pozwalający na ruch w płaszczyźnie pionowej. Mogą obracać nadgarstkiem (bez pochylania). Są to roboty czteroosiowe z ruchem w osiach X, Y, Z oraz obrotowym wokół osi Z (mają cztery stopnie swobody). Ich zalety to: duża szybkość i precyzja, kompaktowość, atrakcyjność cenowa, a wady: ograniczony zasięg i mała liczba stopni swobody.
Roboty przegubowe i delta
Roboty przegubowe nazwę zawdzięczają złączom między segmentami, z których zbudowane są ich ramiona. Przeguby te mogą się zginać i obracać. Przypominają pod tym względem stawy. Dzięki temu ramię robota porusza się jak ramię ludzkie. Roboty przegubowe mają sześć stopni swobody, czyli sześć osi ruchu, trzy liniowe oraz trzy obrotowe.
Ich zalety to: duża liczba stopni swobody i możliwość montażu nad stanowiskiem, a wady: złożona konfiguracja i programowanie, większy koszt. Na stanowiskach pick and place sprawdzają się: gdy wymaganych jest sześć stopni swobody, w realizacji skomplikowanych zadań montażowych i w ciasnych przestrzeniach.
Roboty delta zbudowane są z podstawy i ramion. Podstawa, mocowana na przykład do sufitu, ma zazwyczaj kształt trójkątny albo okrągły. Do niej przymocowane są cienkie ramiona zbudowane z segmentów z ruchomymi przegubami, zakończone chwytakiem. Ramiona poruszają się w sposób skoordynowany, przemieszczając chwytak. Mają cztery osie ruchu: trzy liniowe i jedną obrotową.
Ich zalety to: dużą szybkość i precyzja, lekka, kompaktowa konstrukcja, montaż nad stanowiskiem, zaś wady: ograniczony udźwig i przestrzeń robocza. W zadaniach pick and place sprawdzają się, gdy wymagana jest duża przepustowość i przy przenoszeniu lekkich obiektów.
Projektowanie stanowisk pick and place
Nie ma dwóch identycznych stanowisk pick and place. Każde ma wymagania i ograniczenia, które warunkują jego projekt i wybór wyposażenia. Poza tym jednak kilka kwestii pozostaje wspólnych dla wszystkich stanowisk pick and place, co trzeba uwzględnić przy ich kompletacji.
Taką jest wymagany obszar roboczy. Jeżeli jest dowolnie duży, lepszym rozwiązaniem może być robot kartezjański o dostosowanej rozmiarem obwiedni prostokątnej niż kilka współpracujących ze sobą robotów SCARA o ograniczonym zasięgu. Jeśli z kolei docelowe miejsca podnoszenia oraz odkładania detali znajdują się na różnych powierzchniach roboczych, wówczas korzystniejsze może być umieszczenie pomiędzy nimi kompaktowego robota SCARA, zamiast ich łączenia za pośrednictwem zajmującego dużo miejsca robota kartezjańskiego.
Kolejna kwestia to wymagana liczba stopni swobody. Jeżeli wszystkie docelowe lokalizacje mają tę samą orientację wzdłuż wspólnej płaszczyzny poziomej, wystarczy już robot kartezjański z trzema stopniami swobody, przy ograniczonym zasięgu pionowym (wzdłuż osi Z). Czasem jednak są one rozmieszczone wzdłuż wielu nierównoległych płaszczyzn. Ma to miejsce na przykład wówczas, gdy płaski element jest podnoszony z poziomego przenośnika, następnie jego orientacja ulega zmianie i ostatecznie zostaje ustawiony pionowo w celu dalszej obróbki. Takiemu zadaniu najlepiej sprosta ramię robota przegubowego z sześcioma stopniami swobody.
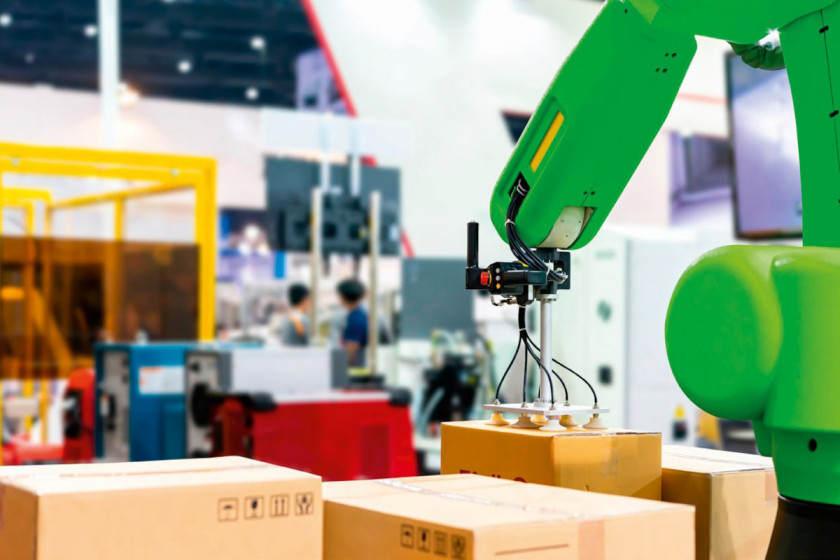
Udźwig, szybkość, precyzja
Udźwig robota musi być odpowiedni do masy obciążenia. Na tę składa się nie tylko masa ładunku, który będzie podnoszony i odkładany w inne miejsce, ale i masa chwytaka. Czasem w specyfikacji robotów podawany jest udźwig nominalny, poza tym maksymalnym. Jeśli masa ładunku tę pierwszą wartość przekroczy, należy uwzględnić to, że pozostałe podane parametry nominalne (prędkość, przyspieszenie, dokładność) ulegną obniżeniu.
Kolejną kwestią jest czas cyklu robota. Określając go, należy uwzględnić wymaganą całkowitą przepustowość systemu zautomatyzowanego, którego częścią będzie stanowisko pick and place. W przeciwnym razie może się ono stać wąskim gardłem danego procesu.
Ważna jest precyzja i powtarzalność ruchu. Na przykład w przypadku robotów kartezjańskich ten drugi parametr poszczególnych osi jest równy powtarzalności odpowiadającego im stopnia napędu. Przyjmuje się, że jest stała w całym obszarze roboczym. W rzeczywistości jednak osie nigdy nie są wzajemnie idealnie prostopadłe, co skutkuje większą odchyłką wraz z przesunięciem względem położenia wyjściowego. W przypadku robotów SCARA i przegubowych podobnie powtarzalność poszczególnych osi jest stała, ale ta wypadkowa będzie najmniejsza na granicy przestrzeni roboczej. Dlatego stanowisko pick and place należy projektować tak, by docelowe miejsca podnoszenia oraz odkładania detali były od jej skraju odpowiednio oddalone.
Michał Osiecki
Omron Electronics
Omron oferuje kompleksowe portfolio robotów stacjonarnych, mobilnych i współpracujących, które cieszą się dużym zainteresowaniem – szczególnie w przypadku 4-osiowych robotów SCARA oraz 6-osiowych robotów o udźwigu do 5 kg i zasięgu do 850 mm. Kluczowym czynnikiem popularności wersji SCARA jest nie tylko ich cena, ale przede wszystkim wszechstronność rozwiązań firmy Omron w zakresie automatycznego podawania detali, dzięki czemu roboty są idealne do aplikacji montażowych. Całościowe rozwiązanie obejmuje zarówno robota SCARA lub 6-osiowego, jak też wibracyjny podajnik iPF oraz zaawansowany system wizyjny. Dzięki jednemu oprogramowaniu ACE użytkownik ma możliwość programowania wszystkich aspektów aplikacji, w tym: obsługi wizji do rozpoznawania detali, ustalania współrzędnych dla robota, sterowania podajnikiem i zapewnienia ciągłości oraz rówomierności rozłożenia detali w polu pracy robota, a także koordynacji ruchów robota podczas pobierania i odkładania detali. To kompleksowe podejście umożliwia szybkie uruchomienie aplikacji, łatwe wprowadzanie nowych detali do procesu podawania oraz obsługę wszystkich urządzeń przez jednego specjalistę, również zdalnie. Dodatkowo podajnik pozwala na pracę z dwoma zasobnikami, a system wizyjny umożliwia wybór odpowiednich detali w przypadku ich zmieszania w podajniku. Dodatkowe kamery zapewniają kontrolę nad jakością pobieranych detali. Nasze rozwiązanie jest niezwykle uniwersalne i elastyczne, co pozwala na szybsze dostosowanie do zmieniających się potrzeb. Warto podkreślić, że sukces w automatyzacji nie polega jedynie na dostarczeniu robota, ale na zapewnieniu kompleksowego rozwiązania, które spełnia wszystkie wymagania użytkowników.
Coboty umożliwiły robotyzację w średnich i małych zakładach, oferując prostotę i elastyczność, a także nie wymagały dużych inwestycji w infrastrukturę. Zajmują niewiele miejsca i zastępują lub w bezpieczny sposób współpracują z ludźmi przy powtarzalnych, nużących operacjach, takich jak paletyzacja, przekładanie kartonów, wkładanie i wyjmowanie detali z maszyn, podawanie ich do stacji montażowych oraz odkładanie zmontowanych produktów. Pomimo początkowych obaw, pracownicy stosunkowo szybko akceptują obecność cobotów i doceniają takie wsparcie w swojej pracy. |
Dodatkowe wyposażenie
Dodatkowe elementy wyposażenia wymagane na stanowisku pick and place zależą m.in. od tego, czy detale, którymi ma manipulować chwytak robota, mają ustalone położenie i orientację. Jeżeli ich lokalizacja oraz ustawienie względem układu odniesienia robota są znane, wówczas można nim sterować w pętli otwartej. Oznacza to, że cyklicznie przemieszcza się on do określonego miejsca, skąd podnosi przedmiot, który następnie odkłada w innej lokalizacji. Jeśli detale pojawiają się w zasięgu ramienia robota w przypadkowych miejscach na taśmociągu i mogą mieć różną orientację, stanowisko należy uzupełnić o system ich detekcji.
Przykładowo można wykorzystać czujnik obecności wbudowany w przenośniku i system wizyjny z kamerą zainstalowaną nad taśmociągiem lub zamontowaną na ramieniu robota. W takim przypadku sekwencja zdarzeń może być następująca: sensor obecności wykrywa następny detal i sygnalizuje to sterownikowi systemu, który zatrzymuje przenośnik. Następnie na podstawie danych z systemu wizyjnego w kontrolerze wyznaczane jest położenie i orientacja obiektu. Informacja o tym jest przetwarzana na sygnał sterujący nakierowujący ramię robota. Po przeniesieniu detalu przenośnik jest uruchamiany ponownie.
Monika Jaworowska