Pierwszy komponent typowej instalacji produkcji i dystrybucji sprężonego powietrza to kompresor. W procesie sprężania zostaje w nim zmagazynowana energia, uwalniana później podczas rozprężania w odbiorniku. Kolejne elementy to zbiornik na sprężone powietrze, niezbędny do kompensacji wahań zapotrzebowania na to medium, oraz osuszacz. Zbiornik znajduje się przed albo za nim. Następnie sprężone powietrze trafia do zespołu jego przygotowania, skąd jest rozprowadzane do odbiorników (rys. 1).
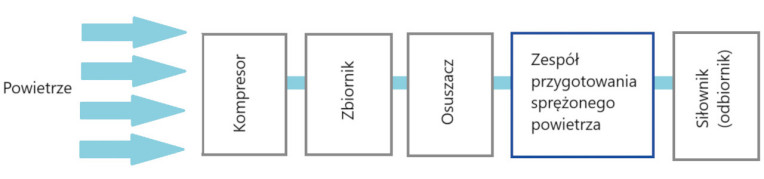
Temat artykułu stanowi jednostka przygotowania tytułowego medium. Zasadniczo pełni ona trzy funkcje.
Główne funkcje
Pierwszą jest usunięcie zanieczyszczeń. Idealnie sprężone powietrze powinno być ich pozbawione. W praktyce tak jednak nie jest i trzeba się liczyć z obecnością cząstek stałych, wody i olejów. Wynika to z ich nieuniknionego występowania w powietrzu atmosferycznym – w jego jednym metrze sześciennym unosić się mogą nawet setki milionów cząstek stałych o rozmiarach od ułamka do kilkuset mikrometrów. Przykłady to cząstki dymu tytoniowego, włosy, para wodna i krople olejów. Źródłem zanieczyszczeń może być również sam kompresor.
Podczas sprężania powietrza stężenie cząstek obcych w jednostce objętości czynnika roboczego też wzrasta. Następnie wraz z nim są one przenoszone do instalacji jego dystrybucji i do odbiorników. Ma to liczne negatywne konsekwencje.
Nagromadzenie cząstek stałych, które osadzają się na elementach ruchomych, staje się przyczyną zwiększonego tarcia, m.in. między ścianą cylindra a uszczelnieniem na tłoku siłownika. Obecność wilgoci może doprowadzić do korozji, której produkty zanieczyszczą czynnik roboczy. Drobiny rdzy również są w stanie uszkadzać powierzchnie na skutek tarcia i blokować elementy ruchome. Oleje natomiast potrafią zlepiać inne zanieczyszczenia i powodować pęcznienie materiałów uszczelnień. W dłuższej perspektywie obecność cząstek obcych w sprężonym powietrzu może skrócić żywotność urządzeń pneumatycznych, spowodować spadek ich precyzji, awarię, zwiększyć koszt konserwacji, a gdy doprowadzi to do nieszczelności – skutkować stratami energii.
Częścią zespołu przygotowania sprężonego powietrza są też układy regulacji ciśnienia i przepływu tego czynnika roboczego odpowiednio do potrzeb odbiorników, np. wymaganej prędkości i siły posuwu tłoka siłownika. Konieczne może być również wprowadzenie do sprężonego powietrza czynnika smarnego w postaci mgiełki, o ile jego odbiorniki tego wymagają.
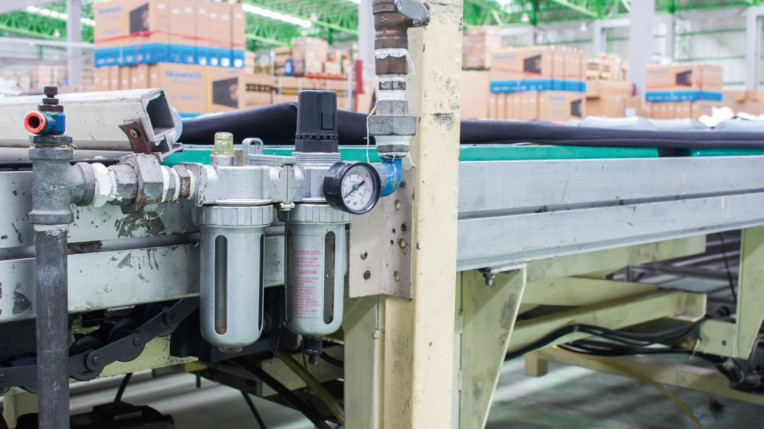
Czystość sprężonego powietrza
Wejściowym komponentem zespołów przygotowania sprężonego powietrza jest zwykle jednostka, która stanowi połączenie reduktora ciśnienia z układem odprowadzania wilgoci i filtrem. Sprężone powietrze, które wpływa do komory tego zespołu, uderza w specjalnie ukształtowaną przegrodę. To powoduje zaburzenie przepływu tego medium w taki sposób, że tworzy się wir. Ponieważ cząstki wilgoci są cięższe od powietrza, pod wpływem siły odśrodkowej są wyrzucane na boki i uderzają w ścianki komory, po których spływają na jej dno. Stąd są odprowadzane spustem będącym częścią regulatora, opróżnianym ręcznie albo automatycznie. Odwodnione powietrze przechodzi następnie przez filtr.
Klasy czystości sprężonego powietrza zostały zestandaryzowane w normie ISO 8573-1. Przypisuje się im określone zawartości cząstek stałych, wody i oleju. W normie podano maksymalną ilość zanieczyszczeń, jaka może znajdować się w sprężonym powietrzu danej jakości. W odniesieniu do cząstek stałych określona jest maksymalna liczba drobin danej wielkości w jednostce objętości i ich stężenie masowe. Jeżeli chodzi o wilgoć, unormowane są jej zawartość w jednostce objętości i punkt rosy, czyli temperatura, po schłodzeniu poniżej której sprężone powietrze ulega kondensacji, zaś w przypadku oleju – jego całkowita zawartość (w postaci cieczy, pary, aerozolu), która przypada na jednostkę objętości. Im wyższa klasa, tym niższy jest stopień czystości. Przykładowo, klasa 7, jeżeli chodzi o cząstki stałe oznacza ich stężenie masowe od 5 do 10 mg/m³, a klasa 4 w odniesieniu do wilgoci – punkt rosy ≤ +3°C, zaś w przypadku olejów – zawartość ≤ 5 mg/m³.
Wymagania w zakresie stopnia czystości sprężonego powietrza dla komponentów pneumatycznych, takich jak zawory i siłowniki, podaje ich producent. Podobnie różne zastosowania wymagają tego medium o określonej ilości zanieczyszczeń, zależnie od sposobów jego wykorzystania, które można generalnie podzielić na trzy grupy. Do pierwszej należy sprężone powietrze używane do sterowania zaworami, zasilania siłowników i chwytaków, niemające bezpośredniego kontaktu z produktami. Do kolejnej zalicza się to używane do czyszczenia maszyn oraz przedmiotów obrabianych. Ma ono bezpośredni kontakt z produktami, np. podczas obróbki skrawaniem. Powietrze procesowe to z kolei medium, które ma fizyczny kontakt lub reaguje chemicznie z produktami. Może być także używane do ich transportu.
Filtry
Częścią zespołów przygotowania sprężonego powietrza są zatem także filtry. Skuteczność usuwania przez nie zanieczyszczeń zależy od rozmiaru ich oczek. Większe cząstki – o wielkości przeważnie od kilku do kilkudziesięciu mikrometrów – są wychwytywane przez wkłady. Jeżeli wymagana jest wyższa klasa czystości medium, trzeba skorzystać z filtrów o mniejszych oczkach, które np. mogą usuwać cząstki o rozmiarze poniżej 1 μm. Największą skuteczność filtrowania, w tym pozostałości węglowodorów, substancji zapachowych i oparów oleju, zapewniają filtry węglowe.
Filtracja powinna być przeprowadzona etapowo. Jeśli np. dopuszczalne jest występowanie cząstek wyłącznie mniejszych niż 1 μm, najpierw należy wychwycić te większe, filtrując sprężone powietrze na wkładach o większych rozmiarach oczek, np. od kilku do kilkudziesięciu mikrometrów. W przeciwnym razie na filtrze docelowym zatrzymają się również zanieczyszczenia znacznie większe niż 1 μm, co bardzo szybko doprowadzi do jego nasycenia (przytkania). To skutkować będzie wzrostem spadku ciśnienia na wkładzie.
Podczas korzystania z filtrów istotne jest utrzymanie określonego zakresu przepływu medium. Jeśli w wyniku wzrostu zapotrzebowania na sprężone powietrze jego natężenie przepływu przekroczy maksymalną dopuszczalną wartość albo spadnie poniżej tej minimalnej, filtr może nie być w stanie zapewnić deklarowanej skuteczności filtracji. By z kolei ograniczyć nieunikniony spadek ciśnienia, warto jest wybrać filtr o większej powierzchni.
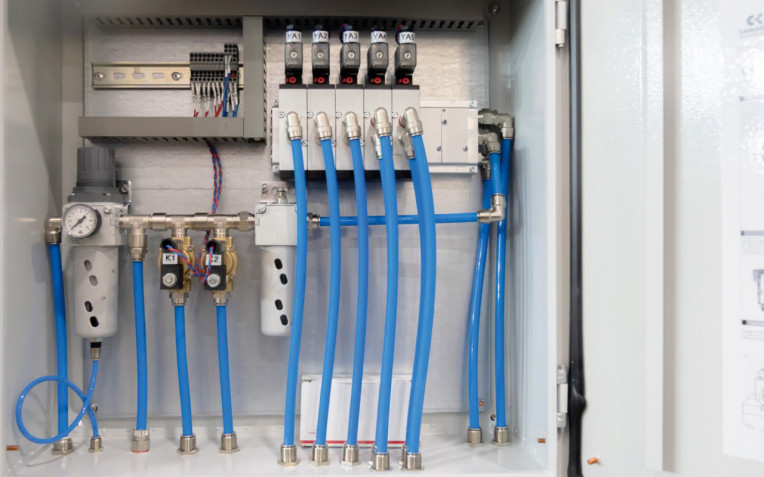
Osuszacze i smarownice
Oczyszczone sprężone powietrze przepływa do zaworu, gdzie następuje redukcja jego ciśnienia do ciśnienia roboczego. Jeżeli filtr nie jest w stanie wystarczająco obniżyć zawartości wilgoci, a tym samym punktu rosy do wymaganej wartości temperatury, potrzebne są dodatkowe osuszacze.
Wykorzystuje się różne ich konstrukcje. Przykładem są osuszacze membranowe. Wytwarzają one różnicę ciśnień między dwoma komorami oddzielonymi membraną pochłaniającą wilgoć. To powoduje, że sprężone powietrze jest przetłaczane przez tę przegrodę, na której zatrzymuje się woda. W ten sposób punkt rosy tego medium można obniżyć o co najmniej kilkanaście stopni. Jeśli to nie spełnia wymagań zastosowania, wykorzystuje się osuszacze adsorpcyjne, w których cząstki wilgoci są wiązane przez specjalny czynnik suszący.
W przypadku osuszaczy membranowych i adsorpcyjnych im wyższe ciśnienie wlotowe, tym lepsza skuteczność osuszania. Mimo to przeważnie umieszcza się je za reduktorem ciśnienia, żeby uniknąć sytuacji, w której stanie się on źródłem zanieczyszczeń. Jeżeli jednak ciśnienie na jego wyjściu jest za niskie, aby osuszacz działał skutecznie, należy rozważyć umieszczenie reduktora za nim i zastosowanie dodatkowego filtra na wyjściu reduktora.
Jeśli z kolei chodzi o smarownice – o ile to możliwe, powinno się je umieszczać bezpośrednio przed odbiornikiem, aby olej niepotrzebnie nie krążył w instalacji dystrybucji sprężonego powietrza. Są one też często zintegrowane z jednostką reduktora ciśnienia i filtru.
Monika Jaworowska