CZĘŚĆ III: KAMERY W SYSTEMACH WIZYJNYCH
Wybór kamery to niewątpliwie jeden z najważniejszych etapów tworzenia systemu wizyjnego. Zawiera ona przetwornik, na którym obiektyw odwzorowuje obraz obserwowanego obiektu, a jej zadaniem jest rejestracja tej informacji i transmisja do dalszej części systemu – zazwyczaj urządzeń analizujących jego zawartość.
Przez ostatnie kilkadziesiąt lat w tej dziedzinie zachodził ciągły postęp, do czego przyczyniały się zmiany w technologii przetworników obrazu – m.in. rozwój elementów CCD (Charge-Coupled Device) oraz przetworników CMOS (Complementary Metal Oxide Semiconductor).
PRZETWORNIKI OBRAZU
CCD i CMOS reprezentują dwie różne technologie, przy czym każda ma zarówno zalety, jak i wady. Wybór jednej z nich zależy głównie od specyfiki aplikacji, w której wykorzystana ma być dana kamera. Obydwa przetworniki działają na podobnej zasadzie fizycznej, przy czym różnice dotyczą procesu przetwarzania rejestrowanego obrazu. Światło padające na matrycę przetwornika powoduje zmianę ładunku elektrycznego w strukturze materiału światłoczułego.
W elementach CCD ładunki poszczególnych pikseli są przy użyciu dodatkowych układów przenoszone na wspólne wyjście przetwornika, gdzie następuje pomiar napięcia odpowiadającego natężeniu światła padającego na daną komórkę matrycy. W przetwornikach CMOS zmiana ładunku zostaje wykorzystana natomiast do sterowania tranzystorami, co pozwala na bezpośrednie określenie wymienionej wartości natężenia.
Obie technologie wynalezione zostały w latach 60.-70. zeszłego wieku, przy czym na początku dominowały na rynku przetworniki CCD. Było to związane z ówczesnym stopniem zaawansowania procesów technologicznych w zakresie produkcji półprzewodników. Na tym etapie układy CCD zapewniały po prostu znacznie lepszą jakość obrazu, jednak, wraz z rozwojem technik wytwarzania struktur półprzewodnikowych, w latach 90. wzrosło zainteresowanie produkcją przetworników CMOS. Nadzieje wiązano szczególnie z takimi cechami tych przetworników, jak niższy pobór mocy i większa skala integracji.
KAMERY KOLOROWE I MONOCHROMATYCZNE
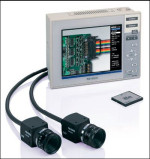
Oprócz rozróżnienia w zależności od typu przetwornika obrazu, kamery podzielić można także na monochromatyczne i kolorowe. Z pozoru może wydawać się, że decyzja o wyborze odpowiedniego ich typu nie jest trudna, jednak ma ona kluczowe znacznie dla kompletacji odpowiedniego systemu wizyjnego.
Wybierając kamerę do aplikacji przemysłowej, wiele osób odruchowo zdecydowałoby się na kamerę kolorową, ponieważ panuje przekonanie, że obraz monochromatyczny jest „gorszy”. Nie jest to jednak prawdą.
Przetworniki obrazu działają w oparciu o efekt fotoelektryczny, stąd rozpoznawanie kolorów wymaga implementacji dodatkowych rozwiązań. W większości kolorowych kamer CCD wykorzystywany jest pojedynczy przetwornik obrazu, na który zostaje naniesiona mozaika kolorowych filtrów.
Dzięki temu sąsiadujące piksele rejestrują natężenie światła o innej barwie. Jednak takie podejście w znaczący sposób zmniejsza rozdzielczość obrazu. Porównanie typowego układu kolorowej kamery z pojedynczym przetwornikiem i kamery monochromatycznej wypada zdecydowanie na korzyść drugiego rozwiązania. W kamerach monochromatycznych pojedynczy piksel niesie informacje jedynie o natężeniu padającego światła.
Brak filtrów koloru zwiększa rozdzielczość takiego układu, w związku z tym zazwyczaj kamery monochromatyczne mają o 10% większą rozdzielczość niż kamery kolorowe. Inne parametry, w tym współczynnik SNR, czułość i kontrast są także korzystniejsze w przypadku kamer jednobarwnych. Dodatkowo przetwarzanie obrazu monochromatycznego jest mniej skomplikowane, co przyspiesza proces ich analizy.
Można ocenić, że w dużej części przemysłowych systemów wizyjnych lepiej sprawdzają się kamery monochromatyczne. Dotyczy to zwłaszcza aplikacji pomiarowych, w których kluczowa jest duża rozdzielczość. Jeżeli jednak pojawi się konieczność połączenia dużej rozdzielczości i rejestracji obrazu kolorowego, należy sięgnąć po tzw. kolorową kamerę z trzema przetwornikami CCD. Rozwiązanie to oparte jest na wykorzystaniu pryzmatu oraz trzech przetworników obrazu i zapewnia dużą rozdzielczość, ale jednocześnie charakteryzuje się mniejszą czułością i wyższą ceną.
Kamery na rynku – przykłady![]() Kamera z serii pilot z interfejsem GigE
Szeroki asortyment produktów do systemów wizyjnych proponuje niemiecka firma Basler. Jej oferta obejmuje m.in. kamery obrazowe serii pilot z interfejsem GigE Vision o rozdzielczości 1, 2 i 5 megapikseli oraz prędkości rejestracji od 12 do 120 klatek/s. Firma dostarcza także kamery z serii scout z interfejsem IEEE1394b oraz GigE Vision, które charakteryzują się rozdzielczościami 1,4 i 2 megapikseli przy liczbie klatek/s od 14 do 77. Oprócz kamer obrazowych Basler oferuje także kamery linijkowe, m.in. serię Runner z interfejsem GigE Vision i rodzinę Sprint z interfejsem Camera Link. W przypadku tej pierwszej producent oferuje modele o rozdzielczości 1024 pikseli, 2048 pikseli oraz model trzylinijkowy o rozdzielczości 2098 pikseli. Z kolei w serii Sprint dostępne są modele o rozdzielczości 2048, 4096 i 8192 pikseli. W serii Runner maksymalna możliwa częstotliwość skanowania to 56kHz, a w serii Sprint 140kHz. ![]() Kamera linijkowa firmy Basler z serii Runner
Firma oferuje także kamery inteligentne z serii eXcite. Są to kompletne urządzenia, które oprócz akwizycji obrazu zapewniają też jego wstępną obróbkę. Przetwarzanie obrazu realizowane jest z wykorzystaniem 64-bitowego procesora taktowanego zegarem 1GHz. Kamery serii eXcite zapewniają rozdzielczość w zakresie od VGA do 2 megapikseli i prędkość rejestracji do 180 klatek/s. Oddzielny mikrokontroler odpowiada za realizację wszelkich wewnętrznych funkcji, takich jak konfiguracja i akwizycja obrazu. Modele z tej serii mogą komunikować się ze światem zewnętrznym za pośrednictwem interfejsu Gigabit Ethernet, USB oraz RS232 i cyfrowych portów I/O. W Polsce dystrybucją kamer z oferty Basler zajmuje się firma CRI Jolanta oraz Avicon. |
KAMERY OBRAZOWE CZY LINIJKOWE?
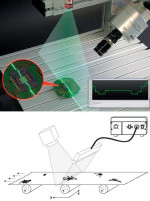
Na etapie projektowania systemu wizyjnego należy rozstrzygnąć również kwestię, czy w danej aplikacji stosowana będzie typowa kamera obrazowa (matrycowa, area-scan), czy kamera linijkowa (linescan). Do tych ostatnich projektanci systemów wizyjnych odnoszą się, często niesłusznie, z rezerwą. Właściwego wyboru pozwala dokonać analiza charakteru obiektu podlegającego inspekcji.
Systemy wizyjne wykorzystujące kamery linijkowe znaleźć mogą zastosowanie m.in. w pomiarach obiektów obracających się, a przede wszystkim w kontroli produkcji materiałów takich jak: papier, szkło, blachy stalowe czy materiały włókiennicze.
Obiekty tego typu na etapie produkcji mają często postać długich arkuszy. Innym przykładem wykorzystania kamer linijkowych jest przemysł spożywczy, gdzie systemy wizyjne używane są np. w procesach eliminacji ziaren o niewystarczająco dobrej jakości lub wszelkich ciał obcych zmieszanych z produktem podstawowym.
Ziarna, przesuwając się na taśmie lub spadając ze zsypu, tworzą również jednolitą powierzchnię. W takich przypadkach istotna staje się właściwość kamer linijkowych umożliwiająca uzyskanie obrazu ciągłego obiektów o dużej powierzchni.
Widzenie w 3D![]() System wizyjny wykorzystujący kamerę IVC-3D firmy Sick pozwala na kontrolę powierzchni takich produktów, jak elementy hamulców samochodowych
IVC-3D to inteligentna kamera przeznaczona do kontroli i pomiarów w przestrzeni 3-wymiarowej, gdzie trzeci wymiar uzyskiwany jest za pomocą metody triangulacyjnej. Urządzenie zawiera moduł akwizycji obrazu, oświetlacz oraz jednostkę analizującą dane. Oprócz wykonywania standardowych pomiarów jak w przypadku kamer 2D, IVC-3D pozwala na pomiary kształtu przedmiotu, w tym jego wysokości i objętości. Jeśli aplikacja wymaga pomiaru lub kontroli niepłaskiego obiektu, kamera pozwala na uwydatnienie różnic w jego wysokości. Urządzenie pozwala na akwizycję do 5 tys. profili 3D na sekundę, a do oświetlenia wykorzystuje wbudowany laser. W kamerze wykorzystano przetwornik CMOS o rozdzielczości 1536×512 pikseli, obrazy 3D uzyskiwane są niezależne od kontrastu (pozwala to np. na wykrywanie białych obiektów na białym tle). Do przetwarzania danych używany jest wbudowany komputer z procesorem taktowanym z częstotliwością 800MHz. Do komunikacji służą interfejsy: szeregowy i Ethernet, kamera ma też wbudowane serwery FTP, OPC oraz WWW. Urządzenie cechuje się stopniem ochrony IP65. Producent dostarcza do niego także bezpłatne środowisko programowania IVC-Studio, które zawiera ponad 100 gotowych procedur i narzędzi. |
KAMERY LINIJKOWE
W opisanych powyższych zastosowaniach kamery linijkowe sprawdzają się zazwyczaj lepiej niż obrazowe, czego przyczyną jest inna zasada ich działania. Kamery obrazowe rejestrują sekwencję obrazów odwzorowujących poruszający się obiekt. W praktyce ciągła rejestracja w obiektach o nieograniczonej powierzchni uzyskiwania jest poprzez zapis częściowo pokrywających się obrazów. W dalszej kolejności specjalne oprogramowanie przetwarza pozyskane obrazy, usuwając zdublowane fragmenty i eliminując zniekształcenia.
Obraz w kamerze linijkowej (rys. 1) tworzony jest krokowo. Przetwornik w postaci pojedynczej linijki pikseli rejestruje kolejne linie obrazu – w tym celu przesuwa się on nad obiektem lub obiekt porusza się pod kamerą. Technika ta jest od wielu lat stosowana m.in. w skanerach – różnica dotyczy jednak rozmiarów przetwornika, który w skanerach odpowiada zazwyczaj szerokości skanowanej powierzchni. Tymczasem kamery linijkowe wykorzystują miniaturowe przetworniki obrazu, które typowo stanowią linijkę złożoną z 512–8192 pikseli.
Sposób, w jaki w kamerach linijkowych rejestrowany jest obraz obiektu, wymaga dużego stopnia precyzji. Aby możliwe było uzyskanie dokładnego obrazu, rejestracja musi być zsynchronizowana w czasie z ruchem obiektu, a skanowanie powinno być równomierne. W praktyce prędkość ruchu obiektu może zmieniać się w sposób nieprzewidywalny, w związku z czym jest ona często dodatkowo monitorowana w punktach rozmieszczonych w równych odstępach, a ruch samego obiektu odpowiednio synchronizowany.
Z tych powodów aplikacja z kamerami linijkowymi może być bardziej skomplikowana niż w przypadku kamer obrazowych. Niemniej jednak te pierwsze pozwalają często uzyskać obraz o lepszej jakości, ponieważ w tym przypadku nie występuje efekt rozmazania obiektów będących w ruchu. Dodatkowo dane obrazowe przetwarzać można linijka po linijce, co sprawia, że proces obróbki jest wydajniejszy.
Przykładowe kompletacje![]() Karta akwizycji obrazu DominoMelody firmy Euresys
Firmy branżowe oferują nie tylko pojedyncze produkty, ale też kompletacje systemów obejmujące zestaw „kamera plus frame-grabber plus akcesoria”. Rozwiązania takie ma m.in. firma Adlink Technology – ich przykłady omówione zostały poniżej. Kamera analogowa ze skanowaniem progresywnym![]() Kamera CS8560D firmy Toshiba Teli
Rozwiązanie to przeznaczone jest przede wszystkim do systemów wizyjnych stosowanych w inspekcji elementów z otworami, detali takich jak śruby czy przy odczycie kodów. W skład zestawu wchodzi karta akwizycji obrazu Domino Melody firmy Euresys, kamera CS8560D Toshiba Teli oraz 5-metrowy przewód. Zasadniczym elementem zestawu jest analogowa kamera CS8560D ze skanowaniem progresywnym, która zawiera przetwornik obrazu CCD 1/3". Kamera umożliwia rejestrację 60 klatek/s przy rozdzielczości 640×480 pikseli. Oferowana w tym zestawie karta akwizycji obrazu przeznaczona jest do współpracy z monochromatycznymi kamerami analogowymi single-tap. Karta zawiera 10-bitowy przetwornik A/C o szybkości przetwarzania 40MHz oraz pamięć 16MB. Kamera analogowa z przeplotem![]() Frame-grabber firmy Euresys
Zestaw przeznaczony jest do systemów wizyjnych w inspekcji obiektów nieruchomych oraz w aplikacjach realizujących zadania optycznego rozpoznawania znaków (OCR). W jego skład wchodzi karta akwizycji danych z serii Picolo firmy Euresys oraz analogowa kamera firmy Toshiba Teli o symbolu CS8620i z przetwornikiem 1,2" CCD, która rejestruje 30 klatek/s. Zestaw z cyfrową kamerą linijkową![]() Kamera linijkowa Sentech STL-5150UCL
Zestaw ten znaleźć może zastosowanie w aplikacjach takich jak kontrola jakości obwodów drukowanych, detekcja defektów krawędzi i systemy inspekcji wyświetlaczy. VP-Val51 obejmuje kamerę linijkową typu STL-5150UCL (5150 pikseli) amerykańskiej firmy Sentech oraz kartę akwizycji obraz Grablink Value firmy Euresys. Jest to karta przeznaczona do akwizycji obrazu z kamer z interfejsem Camera Link. W skład zestawu wchodzi również 5-metrowy przewód. |
KAMERY INTELIGENTNE
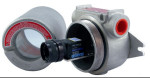
Oprócz wymienionych rozwiązań, na rynku coraz popularniejsze są tzw. kamery inteligentne. Ich podstawowymi elementami są przetwornik obrazu, obiektyw, układ mikroprocesorowy i komunikacyjny, ew. oświetlacze i układy sterowania oświetleniem.
Integrują one więc większość przedstawionych dotychczas komponentów typowych systemów wizyjnych, co pozwala na realizację bezpośredniej analizy obrazu w obrębie jednego układu. Kamery inteligentne bardzo często zapewniają też kompleksową analizę obrazu.
Ponadto, ze względu na wbudowanie interfejsu komunikacyjnego – np. Ethernet, rozwiązania tego typu mają możliwość łatwej komunikacji z innymi urządzeniami w sieci. Pozwala to również na bezpośrednią integrację ze sterownikami PLC, PAC oraz interfejsami HMI, a także sterowanie elementami wykonawczymi niektórych systemów przemysłowych.
Duży stopień integracji kamer inteligentnych sugeruje, że zaprogramowanie takiego urządzenia jest skomplikowane. Pod tym względem kamery inteligentne różnią się jednak od typowych systemów wizyjnych. Są one często prostsze w konfiguracji i obsłudze, a także pozwalają na realizację większości popularnych algorytmów przetwarzania obrazu.
Popularne interfejsy kamer cyfrowychFireWire (IEEE 1394) ![]() IEEE 1394 to popularny standard magistrali szeregowej zaprojektowany przede wszystkim z myślą o realizacji komunikacji z urządzeniami multimedialnymi. Interfejs FireWire jest dziś implementowany w większości komputerów dostępnych na rynku. Nie wymaga instalacji frame-grabbera. Zaletą transmisji przy użyciu tego interfejsu jest też to, że w niewielkim stopniu obciąża procesor. Jest to ważne zwłaszcza w systemach wizyjnych, w których algorytmy przetwarzania obrazu mogą obliczeniowo obciążać jednostkę centralną. USB 2.0 ![]() Pierwotnym przeznaczeniem tego standardu była komunikacja z urządzeniami takimi jak klawiatury, myszki, drukarki. Jednak wraz z wprowadzeniem wersji 2.0, która zapewniła prędkość transmisji z szybkością 480 Mb/s przy maksymalnej długości połączenia 5m, zakres wykorzystania interfejsu USB wzrósł, obejmując też kamery cyfrowe. Wadą jest brak standardu przemysłowego tego interfejsu. Jest to przyczyną problemów z obsługą kamer z interfejsem USB pochodzących od różnych producentów. Wadą jest też duże obciążenie procesora. Dlatego nie jest zalecane wykorzystanie urządzeń z interfejsem USB w systemach wizyjnych, mimo że jest to stosunkowo tanie rozwiązanie. CameraLink ![]() Z większymi kosztami łączy się wykorzystanie kamer z interfejsem CameraLink. W zamian standard ten zapewnia dużą szybkość transmisji (do 4,8 Gb/s) oraz deterministyczną transmisję, która umożliwia implementację szeregu funkcji użytecznych w systemach wizyjnych. Interfejs CameraLink został zaprojektowany specjalnie w celu transmisji danych z kamer cyfrowych do komputera. Wymaga jednak instalacji frame-grabbera. Wadą jest też to, że komunikacja z dwoma kamerami wymaga dwóch oddzielnych framerabberów. Gigabit Ethernet (GigE) ![]() Deterministyczna transmisja jest natomiast problemem w przypadku komunikacji za pośrednictwem interfejsu GigE. Możliwość opóźnień transmisji lub utraty części danych w przypadku dużego obciążenia sieci jest jednak rekompensowana przez szereg zalet tego interfejsu, w tym wysoką przepływność 1Gb/s, długość kabla sieciowego 100m i nieograniczoną liczbę urządzeń. |
TABELA 1. Najpopularniejsze interfejsy kamer cyfrowych |
|||||
FireWire 1394.a |
FireWire 134.b |
USB 2.0 |
GigE |
Camera Link | |
Prędkość transmisji (Mb/s) |
400 | 800 | 480 | 1000 | 4800 |
Maksymalna długość segmentu sieci (m) |
4,5 | 100 | 5 | 100 | 10 |
Maksymalna liczba urządzeń |
63 | 63 | 63 | 127 | nieograniczona 1 |
Złącze | 6-pinowe | 9-pinowe | USB | RJ-45 kat6 | 26-pinowe |
Karta akwizycji obrazu | opcjonalnie | opcjonalni | opcjonalni | niewymagan | wymagane |
Zasilanie |
opcjonalnie |
opcjonalni | opcjonalnie | PoE (Power over Ethernet) |
PoCL (Power over Camera Link) |
![]() Adam Rosz Avicon
Sektor ten jest w istocie dwojaki, gdyż obejmuje rynki komponentów oraz integracji. W przypadku komponentów obserwujemy niesamowitą wręcz dynamikę rozwoju. Jeszcze rok, dwa lata temu mogliśmy na palcach jednej ręki wyliczyć poważnych dostawców komponentów wizyjnych – dzisiaj w Polsce swoje przedstawicielstwa mają wszystkie najważniejsze marki. Mocną stroną polskiego rynku jest też znaczna liczba firm świadczących usługi integracyjne i projektujących systemy pod klucz.
Elastyczność technologii wizyjnych w dopasowaniu do dowolnego procesu produkcyjnego jest ogromna i teoretycznie nie można wyróżnić uprzywilejowanych branż. Z naszego doświadczenia wynika, że największe zainteresowanie wykazuje segment FMCG, motoryzacyjny, farmaceutyczny oraz logistyczny. Bardzo dużym odbiorcą systemów wizyjnych są odbiorcy związani z nauką – uniwersytety, politechniki, instytuty naukowo-badawcze.
W segmencie kamer przemysłowych obserwujemy rozwój nowych interfejsów przesyłu danych. Oczekujemy, że detronizacja najszybszego obecnie komercyjnie dostępnego interfejsu Camera Link z transferem maksymalnym 5,4 Gb/s to kwestia kilku lat. Nowe, konkurencyjne technologie to bardziej ekonomiczny FireWire IEEE 1394-2008 z transferem 3,2 Gb/s oraz oparty na komunikacji światłowodowej i kompatybilny w dół 10 Giga Ethernet z transferem 10 Gb/s. Wzrost prędkości akwizycji będzie głównym motorem rozwoju innych części składowych kamer, w szczególności matryc obrazowych. |
ZA I PRZECIW
Kompletny system wizyjny w jednej obudowie, który zrealizowany jest z wykorzystaniem kamery inteligentnej, to w wielu aplikacjach lepsze rozwiązanie niż użycie kamery połączonej z oddzielnym komputerem. Pozwala zaoszczędzić miejsce montażowe, co w wielu przypadkach jest bardzo istotne.
Innym przykładem mogą być aplikacje wymagające zachowania sterylności, w których zintegrowane rozwiązania sprawdzają się znacznie lepiej niż systemy złożone z wielu elementów. Powyższe argumenty nie oznaczają, że klasyczne systemy wizyjne tracą znacząco na popularności.
Rozwiązania typu „kamera plus komputer” wciąż zapewniają większą elastyczność tworzenia systemu. Dotyczy to w szczególności systemów z wieloma kamerami, które łączone są zbiorczo po kilka sztuk do jednego komputera analizującego obrazy. W takich rozwiązaniach często łatwiej jest również dobierać samo oprogramowanie, które w przypadku kamer inteligentnych pochodzi zazwyczaj z jednego źródła.
![]() Rys.2 Detekcja krawędzi - przykład
|
![]() Rys.3 Dopasowanie wzorca - przykład
|
Kamera inteligentna Matrox Iris GT z oprogramowaniem![]() Matrox Iris GT to najnowsza generacja kamer inteligentnych produkowanych przez firmę Matrox Imaging. Kamery tej serii bazują na jednostce centralnej z procesorem Intel Atom 1,6 GHz działającej pod kontrolą wbudowanego systemu operacyjnego czasu rzeczywistego Windows CE 6.0. Inne cechy kamery Matrox Iris GT to zintegrowany kontroler graficzny z wyjściem VGA, pamięć operacyjna DDR2 256MB oraz dysk Flash 1GB, porty komunikacyjne Gigabit Ethernet, USB 2.0 i szeregowy, a także optoizolowane wejście wyzwalające i wyjście strobujące. Dla bezpośredniej komunikacji ze sterownikami PLC i innymi urządzeniami automatyki Matrox Iris GT obsługuje także protokoły Ethernet/IP oraz Modbus over TCP/IP. Aplikacje wizyjne mogą być tworzone za pomocą interaktywnego środowiska rozwojowego Matrox Design Assistant (dostarczanego z każdą kamerą) lub opcjonalnej biblioteki oprogramowania Matrox Imaging Library. W tym pierwszym użytkownicy tworzą schemat blokowy aplikacji, który jest następnie tłumaczony na odpowiednią instrukcję dla kamery. Matrox Design Assistant oferuje narzędzia do przetwarzania i analizy obrazów niezbędne do stworzenia większości aplikacji widzenia maszynowego, a dodatkowo ma zintegrowany edytor HTML umożliwiający tworzenie podglądów operatorskich. Matrox Imaging Library (MIL) to z kolei zbiór narzędzi programistycznych do rozwijania przemysłowych aplikacji wizyjnych działających pod kontrolą Windows CE 6.0 i innych systemów operacyjnych. Zbiór narzędzi zawiera interaktywne oprogramowanie i funkcje programistyczne do pozyskiwania, przetwarzania, analizy, opisywania, wyświetlania i archiwizacji obrazów. W szczególności zawiera narzędzia do kalibracji, poprawiania i transformacji obrazu, lokalizacji obiektów, wydobywania i mierzenia cech, czytania łańcuchów znaków, dekodowania i weryfikacji oznaczeń identyfikacyjnych. |
CZĘŚĆ IV: SYSTEMY WIZYJNE
„KAMERA PLUS KOMPUTER” I NIE TYLKO
Postrzeganie standardowych systemów wizyjnych jako rozwiązań „kamera plus komputer” nie oddaje w pełni stopnia złożoności takich rozwiązań. Wymienione dwa elementy to wprawdzie podstawowe ich komponenty, ale nie są to jedyne wymagane składniki systemów wizyjnych. W przypadku kamer z interfejsem analogowym konieczne jest stosowanie kart lub modułów akwizycji obrazu, czyli tzw. frame-grabberów.
Kolejnym ważnym elementem jest oprogramowanie, które obejmuje zarówno sterowniki interfejsów kamery, jak i programy do przetwarzania obrazów. Ponieważ obecnie na rynku dostępny jest szeroki asortyment komponentów systemów wizyjnych, realizacja i konfiguracja instalacji zbudowanej z kilku niezależnych, współpracujących ze sobą podzespołów, wymaga umiejętności ich optymalnego doboru.
Systemy wizyjne![]() Kompletny system wizyjny Matrox4SigthX firmy Matrox Imaging
Dostępne na rynku kompleksowe platformy do systemów wizyjnych zazwyczaj integrują w sobie funkcjonalność komputera w formie dostosowanej do wykorzystania w trudnych warunkach przemysłowych. Przykładem jest platforma Matrox 4SightX firmy Matrox Imaging wyposażona w interfejsy GigE i IEEE 1394b. Wraz z opcjonalnym podsystemem akwizycji obrazu Matrox Nexis, frame-grabberami analogowymi lub Camera Link Matrox 4SightX zapewnia kompleksową realizację zadań systemu wizyjnego, umożliwiając przechwytywanie, przetwarzanie oraz wyświetlanie obrazu. Pozwala też na kompresję obrazu m.in. do JPEG2000 w czasie rzeczywistym. Wyświetlanie obrazu zapewnia analogowe wyjście główne oraz wyjścia dodatkowe: TV, analogowe VGA lub cyfrowe. Urządzenie ma też szereg portów komunikacyjnych, w tym USB, szeregowe i oddzielne interfejsy Ethernet oraz Gigabit Ethernet. Wraz z systemem producent dostarcza także kompleksowe oprogramowanie do przetwarzania obrazu w postaci bibliotek MIL (Matrox Imaging Library). Aby stworzyć kompletny system wizyjny, platformę Matrox 4SightX można połączyć np. z podsystemem akwizycji obrazu Matrox Nexis. System ten obejmuje jednostkę kontrolną kamer oraz kartę akwizycji obrazu i umożliwia sterowanie oraz jednoczesne przechwytywanie obrazu od dwóch do czterech kamer. |
FRAME-GRABBERY
Zadaniem frame-grabberów jest „przechwytywanie” obrazu z kamery i dalsze przesyłanie informacji obrazowych. Frame-grabbery występować mogą w postaci modułów lub kart o wejściach analogowych lub cyfrowych. Te pierwsze zawierają układ wstępnego przetwarzania sygnału oraz układ przetwornika A/C oraz bufor, który umożliwia przechowywanie kolejnych klatek przechwyconego obrazu. Urządzenia te mają często również pamięć przechowującą zarejestrowane obrazy.
JESZCZE JEDEN PODZIAŁ KAMER
Kamery, które w celu nawiązania połączenia z systemem nadrzędnym wymagają stosowania kart akwizycji obrazu, podzielić można jeszcze na dwie grupy – kamery z analogowym oraz cyfrowym wyjściem sygnałowym. Te ostatnie wyposażone mogą być m.in. w takie interfejsy jak LVDS lub Camera Link. Obecnie na rynku coraz popularniejsze są kamery z możliwością bezpośredniego podłączenia do komputera za pośrednictwem istniejącego interfejsu, tj. bez udziału karty lub modułu akwizycji obrazu.
Powszechnie wykorzystywany jest tutaj IEEE 1392 (FireWire), USB oraz Ethernet. Rozpowszechnieniu się tego typu rozwiązań sprzyja głównie fakt, że wiele czynników, które w przeszłości wymuszały zastosowanie frame-grabberów, obecnie już nie ma znaczenia. Przede wszystkim o kilka rzędów wielkości zwiększeniu uległa szybkość przetwarzania danych obrazowych przez komputery. Ponadto duże znaczenie ma wprowadzenie kamer ze skanowaniem progresywnym oraz możliwość umieszczenia przetwornika A/C bezpośrednio w kamerze lub nawet w samym przetworniku obrazu.
NOWE STANDARDY
Na rozpowszechnienie kamer bezpośrednio przyłączanych do komputerów wpłynęło również wprowadzenie nowych standardów komunikacyjnych – przykładowo takich jak GigE Vision. Interfejs ten powstał w oparciu o protokół transmisji Gigabit Ethernet i umożliwia szybką transmisje danych obrazowych przy wykorzystaniu popularnych sieci komunikacyjnych.
Do zalet technologii GigE zaliczyć można również wysoką przepływność (1Gb/s), możliwość zastosowania dłuższego (do 100m) i tańszego okablowania oraz przede wszystkim redukcję kosztów związaną z faktem, że użycie kamery cyfrowej nie wymaga stosowania frame-grabberów. Ważna jest też możliwość zwiększenia przepływności w miarę rozwoju technologii Ethernetu w kierunku technologii 10GigE (10Gb/s).
CZY FRAME-GRABBERY SĄ JESZCZE POTRZEBNE?
Nowe standardy komunikacji nie zawsze spełniają wszystkie wymagania aplikacyjne. Wprowadzenie na rynek kamer bezpośrednio przyłączanych nie tyle wypiera z rynku frame-grabbery, co po prostu zmienia znaczenie kart akwizycji obrazu w systemie wizyjnym. Dotychczas urządzenia te były komponentami niezbędnymi, obecnie stają się elementami, których stosowanie jest w niektórych aplikacjach wymagane w celu uzyskania rezultatów nieosiągalnych w innych przypadkach.
Pozwalają one m.in. na przyspieszenie przetwarzania obrazu, zsynchronizowanie akwizycji obrazu z wielu kamer, wykorzystanie kamer analogowych i kamer specjalnego przeznaczenia. Zdaniem ekspertów tradycyjne frame-grabbery oraz kamery bezpośrednio przyłączane za pośrednictwem interfejsów GigE, FireWire, USB i podobnych będą cały czas współistniały na rynku. Wybór konkretnego rozwiązania zależy bowiem od wymagań aplikacji. Ważna jest tutaj w szczególności możliwość zapewnienia deterministycznej transmisji danych. W przypadku kamer z wymienionymi interfejsami z zalety tych rozwiązań wynika ich główne ograniczenie.
Wszystkie umożliwiają podłączenie kilku kamer do jednego interfejsu, lecz aby zapewnić taką możliwość, a jednocześnie uniknąć kolizji danych przesyłanych od różnych urządzeń, należy liczyć się z występowaniem opóźnień w transmisji. W wielu aplikacjach jest to do zaakceptowania, ale w niektórych całkowicie dyskwalifikuje takie rozwiązanie.
![]() Sławomir Trusiuk Sitaniec Technology
W ostatnim czasie widać duże zainteresowanie rozwiązaniami opartymi na systemach wizyjnych. Ich zaletą jest duża sprawność – mogą pracować 24 godziny na dobę przez 7 dni w tygodniu i dawać w 100% powtarzalny wynik inspekcji. W konsekwencji wzrasta wydajność produkcji i jakość wyrobów. Producenci elementów systemu wizyjnego poszli w kilku kierunkach. Jedni skoncentrowali się na bardzo wydajnych komputerach, do których dokładane są kamery z szybkimi przetwornikami. Inni proponują rozwiązania kompaktowe typu 2 w 1, czyli kamera + komputer. Generalnie wybór sprzętu i rozwiązania zależy od rodzaju aplikacji, w której ma pracować.
System wizyjny znajdzie zastosowanie w każdej branży, gdzie towary produkowane są na masową skalę i gdzie wymagana jest kontrola jakości. Przy ich użyciu możemy sprawdzać wiele parametrów: rozpoznamy i skontrolujemy kształt, zmierzymy obiekt (wymiar, średnica, kąt, położenie), wykryjemy i skontrolujemy poprawność nadruku (data, wzór, treść, odczyt kodów), a także skontrolujmy obecność, wypełnienie i wady materiałowe. System wizyjny jest bardzo elastyczny. Dzięki temu zyskujemy możliwość sprawdzenia i eliminacji wadliwych produktów już na linii produkcyjnej. |
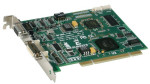
DODATEK: ALGORYTMY PRZETWARZANIA OBRAZU
Elementem dopełniającym systemy wizyjne jest oprogramowanie służące do przetwarzania i analizy obrazów. Integralną częścią pakietów dostarczanych przez producentów systemów wizyjnych jest zazwyczaj szereg algorytmów, które umożliwiają tworzenie różnych aplikacji kontrolno-pomiarowych. Do typowych z nich należą algorytmy dopasowywania wzorca, detekcji krawędzi oraz OCR.
DOPASOWANIE WZORCA (PATTERN MATCHING)
Jest to metoda identyfikacji polegająca na porównywaniu obrazu obiektu ze wzorcem. Pozwala odszukać w obrazie obiektu jego punkty charakterystyczne – np. otwory, które wykorzystywane będą w dalszych pomiarach. Proces testowania jest dwufazowy.
W pierwszym etapie, tzw. fazie uczenia się (learning phase), przetwarzany jest wzorzec (np. określane jego krawędzie), co ma na celu określenie jego cech, które wykorzystane zostaną podczas drugiego etapu, czyli porównywania z obrazami obiektów badanych.
Faza uczenia jest dosyć skomplikowana, a odpowiednie obliczenia zająć mogą kilka sekund przy dużych lub złożonych obiektach. Jest ona przeprowadzana jednorazowo dla każdego wzorca, a dane są zapisywane i wykorzystywane wielokrotnie. Tradycyjne metody analizy obrazów nie przewidują tego etapu – w większości przypadków wzorzec jest bezpośrednio porównywany z całym obrazem obiektu, fragment po fragmencie. Wybór odpowiedniego wzorca ma bardzo duży wpływ na prędkość oraz dokładność analizy i warto tutaj kierować się kilkoma zasadami.
Wzorzec powinien być wystarczająco asymetryczny, aby możliwe było zidentyfikowanie go w określonym położeniu. Przykładowo okrągły otwór nie będzie ze sobą niósł informacji o tym, czy obiekt nie został obrócony. Istotny jest również sam charakter wzorca. Jeżeli jako wzorzec zostanie wybrany skomplikowany element, jego odnalezienie w obrazie obiektu zajmie więcej czasu.
Jeżeli natomiast wzorzec będzie zbyt prosty – w efekcie może dojść do zafałszowania wyników porównywania. Jeżeli za wzorzec przyjęto prosty element, należy pamiętać, że powinien on mieć odpowiednio duży rozmiar. Jeżeli jest to np. zwykły otwór, to jako wzorzec warto wybrać fragment obrazu obejmujący wystarczająco duży fragment otoczenia otworu. Informacje o otoczeniu pozwolą odróżnić konkretny obiekt od podobnych elementów.
Miniaturowa inspekcja![]() DataMan 100 firmy Cognex to miniaturowy czujnik wizyjny pozwalający na odczyt kodów paskowych, nadruków, ale też inspekcję niewielkich powierzchni. Urządzenie jest w istocie inteligentną kamerą, która integruje przetwornik, oświetlenie, układ mikroprocesorowy przetwarzający dane oraz zapewniający komunikację. Pozwala ono na odczyt do około 50 kodów na sekundę. W Polsce dostępny jest m.in. w Firma Inżynierska Tadeusz Wędzony, HDF oraz SKK – Systemy Kodów Kreskowych. |
DETEKCJA KRAWĘDZI (EDGE DETECTION)
Termin ten odnosi się do procesu identyfikacji i lokalizacji konturów w obrazie obiektu. Krawędzie określić można na podstawie dużej wartości zmiany jasności pikseli. Klasyczne metody detekcji polegają na ustaleniu progu tej zmiany dla sąsiadujących ze sobą pikseli. Jeżeli próg jest za niski, wówczas nawet niewielka zmiana jasności w obrazie zostanie zidentyfikowana jako krawędź. Z kolei za wysoki próg będzie utrudniał detekcję niewielkich zmian jasności, które mogą odpowiadać np. niewielkim otworom.
W związku z tym istnieje ogromna liczba stosowanych wartości progowych wykorzystywanych filtrów, które odpowiadają rozmaitym typom krawędzi. Wybór algorytmu detekcji krawędzi zależy też w dużym stopniu od samej aplikacji. Można przykładowo zdefiniować go dla momentu pierwszego przekroczenia wartości progowej albo przy kolejnej zmianie jasności obrazu. Dotyczy to także sposobów detekcji orientacji krawędzi. Filtry optymalizowane są pod kątem wyszukiwania krawędzi w poziomie, pionie i po przekątnej.
![]() Wojciech Komosiński Vision
Rynek systemów wizyjnych w Polsce jest dużo mniejszy niż w krajach Europy Zachodniej, mimo to rejestrujemy stopniowy wzrost zainteresowania takimi metodami kontroli. Obserwacja rosnącej liczby zapytań ze strony naszych klientów pozwala zaryzykować stwierdzenie, że przyszłość kontroli produkcji należy właśnie do systemów wizyjnych. Widzimy dużą szansę na pojawienie się tej technologii w miejscach, do których dzisiaj jeszcze nie dociera. Dzięki swoim zaletom wynikającym z dużej wydajności i uniwersalności oraz malejącym cenom, systemy wizyjne w wielu zastosowaniach wyprą dotychczasowe – często zawodne lub zbyt rozbudowane – metody kontroli.
Rozwój sprzętu i oprogramowania w branży systemów wizyjnych wymuszany jest przez coraz wyższe wymagania odbiorców końcowych. Należy do nich duża dokładność (w przypadku aplikacji pomiarowych), prędkość przetwarzania obrazu (liczba klatek na sekundę) oraz możliwość swobodnej i szybkiej transmisji danych. Producenci, stawiając czoła tym wymaganiom, poszerzają wachlarz swoich produktów o kamery z przetwornikami o dużych rozdzielczościach, często wyposażonych we własne procesory i dowolny, szybki protokół komunikacyjny. W parze z rozwojem sprzętu idą zmiany w oprogramowaniu, które dzięki stosowaniu coraz nowszych algorytmów, pozwalają znacznie lepiej wykorzystać zasoby tkwiące w dostępnych urządzeniach.
Rynek systemów wizyjnych zdecydowanie napędzany jest przez przedsiębiorstwa produkcyjne z branży motoryzacyjnej. To tam nacisk na dokładność wykonania produktów jest największy, ponieważ przekłada się to na bezpieczeństwo końcowego użytkownika. Większość systemów, które wykonujemy dla naszych klientów z tego sektora, opiera się na aplikacjach dotyczących pomiaru, oceny kompletności montażu oraz wykrywanie defektów. Ważną cechą tych klientów jest większe zrozumienie specyfiki oraz możliwości systemów wizyjnych. |
OPTYCZNE ROZPOZNAWANIE ZNAKÓW (OPTICAL CHARACTER RECOGNITION)
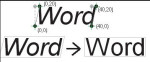
Algorytm OCR jest metodą rozpoznawania znaków powszechnie wykorzystywaną w przemyśle – służy np. do odczytywania numerów seryjnych produktów. Z OCR wiążą się dwa zagadnienia: rozróżniania i rozpoznawania znaków. Pierwszy termin odnosi się do lokalizacji pojedynczych znaków, określenia ich kolejności w odniesieniu do innych łańcuchów oraz identyfikacji pozycji danego znaku w łańcuchu.
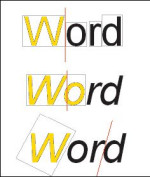
Drugim zagadnieniem i etapem procesu jest rozpoznawanie znaków. Tutaj algorytm oparty jest na klasyfikacji, przy czym niezbędny jest dostęp do znaków wzorcowych. Metody stosowane w tym zakresie zależą w dużej mierze od czcionki użytej w tekście.
Przykładem są znaki zapisane kursywą, które nie zostaną rozpoznane z wykorzystaniem standardowego zestawu znaków pisanych czcionką prostą. Kłopot sprawia lokalizacja poszczególnych znaków, ponieważ w tym przypadku sąsiednie litery zachodzą na siebie (patrz rysunek). Jednym ze sposobów na pokonanie tego problemu jest wyznaczanie granic poszczególnych znaków i ich oddzielna analiza. Jest to jednak metoda bardzo czasochłonna.
Innym sposobem jest przekształcenie tekstu zapisanego kursywą do standardowej postaci zapisu zwykłą czcionką. W tym celu należy na wstępie zdefiniować cztery punkty, po dwa w pierwszej i ostatniej literze słowa oraz punkty im odpowiadające w przypadku liter bez kursywy (również na rysunku). Na tej podstawie tekst zostaje przetworzony w odpowiedni sposób, tak by ułatwić rozpoznanie poszczególnych znaków.
Systemy wizyjne w kontroli nadruków na opakowaniach artykułów spożywczych![]() Systemy oparte o algorytmy optycznej weryfikacji znaków OCV (Optical Character Verification) stanowią istotny element linii produkcyjnych w przemyśle spożywczym. Kwestia poprawności i czytelności naniesionej daty ważności czy innych oznaczeń wyrobów jest dla ich producentów sprawą kluczową. Dotyczy to zwłaszcza towarów ulegających szybkiemu psuciu się. Obecnie metody nanoszenia oznakowania na towary są ciągle niedoskonałe. Rozmazany, niewyraźny nadruk jest częstym zjawiskiem i na jego powstanie wpływać może m.in. temperatura powierzchni, na którą nanoszona jest farba, konsystencja farby oraz warunki pakowania produktów, w tym wilgotność powietrza. W większości zakładów spożywczych w celu weryfikacji poprawności nadruków wykorzystuje się wielokrotną, ręczną kontrolę jakości przeprowadzaną okresowo na różnych etapach produkcji. Czynnik ludzki ma w tym przypadku decydujący i negatywny wpływ na wydajność oraz obiektywność takiej kontroli. Stąd coraz częściej w systemach weryfikacji tego rodzaju stosowane są automatyczne systemy wizyjne. Przykładem jest system zaprojektowany przez firmę A&RT, który realizuje weryfikację numerów seryjnych. System może zostać włączony bezpośrednio w istniejącą linię produkcyjną i kontrolować 600 nadruków na minutę. Zasadniczym jego elementem jest czujnik wizyjny Cognex Insight 5603, który ma możliwość realizacji algorytmu OCV. Inne elementy obejmują platformę Vision Server HMI firmy Control Vision i sterownik firmy CompactLogix. Projektanci systemu przewidzieli możliwość jego rozbudowania o dodatkowe czujniki wizyjne, których zadaniem może być np. weryfikacja etykiet czy kontrola szczelności opakowania produktów. |
Jaworowska, Piątek