Sortowanie to typowa czynność manipulacyjna w zarządzaniu stanem magazynowym i kompletacji zamówień w centrach dystrybucji. Polega na podziale strumienia produktów według określonych kryteriów i następnie ich przekierowaniu na różne drogi transportowe. W nowoczesnych obiektach logistycznych zadanie to jest zautomatyzowane, częściowo albo w pełni. Zwykle sortery zasilane są za pośrednictwem automatycznych systemów podających. Towary mogą być również wprowadzane ręcznie przez pracowników. Przepływ ładunków jest śledzony w czasie rzeczywistym, a w miejscu docelowym zostają one automatycznie rozładowane.
Automatyczne sortery
Zautomatyzowany system sortowania składa się zazwyczaj z kilku komponentów. Główny element konstrukcyjny to tor, który zapewnia ścieżkę ruchu dla ciągłej cyrkulacji ładunków. Jest zazwyczaj wykonany ze stali polakierowanej proszkowo, w celu zabezpieczenia przed zużyciem i korozją, lub z wytłaczanych profili aluminiowych. Układ toru jest przeważnie konfigurowalny i może mieć kształt linii prostej, prostokątny, owalny, typu Z, U albo C. Dostępne są także konstrukcje dwupoziomowe, zapewniające większą przepustowość sortowania.
Na torach montuje się elementy, na których ładunki są układane, wraz z którymi się przemieszczają i z których są rozładowywane. Ich konstrukcja jest specyficzna dla różnych typów sorterów, opisywanych dalej. Generalnie jednak w ich projektach kładzie się nacisk na kilka cech wspólnych. Są to: równomierny rozkład obciążenia, małe tarcie, lekkość, trwałość. Dzięki nim uzyskuje się szybki, płynny i stabilny ruch ładunku, bez względu na kształt toru, na odcinkach prostych, zakrętach, jak i pochyłościach. Ważne jest też ograniczenie hałasu. Projekty transporterów ładunków są oprócz tego optymalizowane pod kątem łatwości montażu, demontażu, konserwacji oraz skalowalności. Cechy te osiąga się dzięki konstrukcjom modułowym.
Niezbędne segmenty systemu sortowania stanowią też: stanowiska podawania i odbioru towarów, systemy ich śledzenia oraz sterowania zrzutem. Jeśli chodzi o te pierwsze, ręczne podawanie sprawdza się w przypadku ładunków o nieregularnych kształtach, rozmiarach i delikatnej strukturze. Zapewnia ono też elastyczność w przypadku dużej zmienności typów towarów. Zautomatyzowane stanowisko stanowi typowo przenośnik, którego przesuw jest zsynchronizowany z sorterem. Przepływ ładunków śledzą zwykle skanery kodów kreskowych. Identyfikują one towary i na podstawie informacji z centrali – np. z systemu zarządzania magazynem – wysyłają komunikat aktywujący zrzut ładunku. W zakresie zsuwni również dostępnych jest wiele opcji, w tym m.in. konstrukcje proste, spiralne czy rolkowe.
Wykorzystywane są różne typy sorterów. Dalej przedstawiamy te najpopularniejsze.
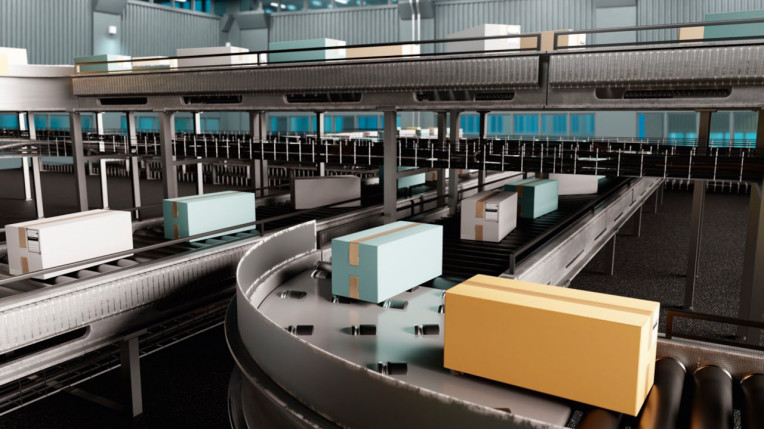
Sortery suwakowe
Przykładem są te suwakowe typu shoe. Chodzi o przenośniki z powierzchnią nośną w postaci listew (profili), zwykle wykonanych z anodowanego aluminium, zamontowanych prostopadle do kierunku przepływu ładunków. Do każdego profilu przymocowany jest suwak (ślizgacz), zazwyczaj wykonany z tworzywa sztucznego. Są to elementy ruchome, przesuwające się wzdłuż listew. Suwaki służą do kierowania produktu. Gdy znajdzie się on w miejscu przekierowania, ślizgacze zostają aktywowane. Przesuwają się wówczas po profilach w skoordynowany sposób, by przemieścić (zepchnąć) ładunek na docelowy tor boczny. Pasy odbioru są zazwyczaj umieszczone pod kątem 30° albo 22° względem pasa głównego. Sortery typu suwakowego mogą przekierowywać towary w jednym albo w obu kierunkach (lewo, prawo) względem głównej osi ich przepływu.
Sortery suwakowe to popularne urządzenia, używane już od lat 80. XX wieku. Sortują z szybkością od kilkudziesięciu do kilkuset produktów na minutę, co jest średnią prędkością w porównaniu z innymi rodzajami sorterów. Są dokładne i wszechstronne – sprawdzają się w sortowaniu towarów w szerokim zakresie rozmiarów oraz kształtów, w tym pudełek nierównomiernie wypełnionych. Poza kartonami rozdzielają m.in. skrzynki, torby i koperty. Ze względu na specyfikę działania lekkich, plastikowych ślizgaczy przesuwających produkty po metalowych profilach o małym tarciu, sortery suwakowe nadają się do transportu delikatnych ładunków. Pod względem kosztów z kolei plasują się między sorterami najtańszymi i tymi najdroższymi jako rozwiązanie średniej klasy. Ich ślizgacze można łatwo zdemontować, co ułatwia konserwację i skraca przestoje. Wymagają jednak solidnej konstrukcji wsporczej, z powodu sporej bezwładności podczas ich uruchamiania i zatrzymywania. Można je montować na podłodze albo na odpowiednio wytrzymałej antresoli.
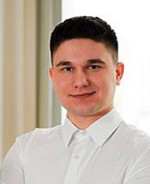
Norbert Szponar
Elmark Automatyka
Czy obserwują Państwo wzrost zainteresowania automatyzacją ze względu na problemy z dostępnością siły roboczej lub inne czynniki ekonomiczne?
Niedobory kadrowe oraz uwarunkowania ekonomiczne wyraźnie przyspieszają tempo robotyzacji. W obecnych czasach coraz trudniej o stałych pracowników – zarówno wykwalifikowanych, jak i tych wykonujących proste, powtarzalne czynności. Firmy szukają alternatyw zapewniających ciągłość produkcji, niezbędną do utrzymania się na rynku. Automatyzacja umożliwia przejęcie przez roboty powtarzalnych, monotonnych i często niebezpiecznych zadań o wysokim ryzyku urazów, zmniejszając zależność zakładu od brakujących rąk do pracy.
Poza tym rosnące koszty pracy, presja na podnoszenie wydajności oraz wysokie wymagania jakości sprawiają, że inwestycje w roboty mają mocne uzasadnienie biznesowe. Doświadczenia ostatnich lat, takie jak pandemia czy zakłócenia łańcuchów dostaw, pokazały, że zrobotyzowane fabryki łatwiej utrzymują ciągłość produkcji w kryzysowych warunkach. W efekcie robotyzacja staje się receptą na problemy kadrowe i sposobem na zwiększenie odporności biznesu w niepewnych czasach.
Dodatkowo, firmy traktują automatyzację jako inwestycję w rozwój. Dzięki wyższej wydajności mogą przyjmować większe zamówienia mimo braku personelu, a poprawa powtarzalności i jakości ułatwia spełnienie rygorystycznych norm oraz wejście na wymagające rynki. Poza tym unowocześnienie parku maszynowego podnosi atrakcyjność firmy jako pracodawcy – zaawansowane technologie przyciągają młodych, wykwalifikowanych pracowników, o których na rynku jest bardzo trudno.
Wszystkie te czynniki sprawiają, że zainteresowanie takimi elastycznymi rozwiązaniami stale rośnie. Robotyzacja przestaje być postrzegana jako luksus, a staje się standardem nawet w średniej i małej wielkości zakładach. To właśnie tu widzimy największy wpływ, jaki wywierają roboty – szczególnie te współpracujące, ze względu na swoją prostotę programowania i elastyczność. Coboty oferują bardzo niski próg wejścia przez to, że są po prostu przyjazne operatorowi. Nawet jeden taki robot potrafi zmienić oblicze przedsiębiorstwa i stać się motorem napędowym jego dalszych sukcesów.
Sortery cross belt
Popularnym rozwiązaniem są też sortery typu cross belt. Są one zbudowane z segmentów w postaci dwukierunkowych przenośników, ustawionych poprzecznie do kierunku głównej osi ruchu. W miarę jak człony sortera się przemieszczają, podawane są na nie produkty z ustawionego pod kątem zasilającego toru bocznego. Po osiągnięciu docelowego miejsca rozładunku przenośnik odpowiedniego segmentu sortera jest uruchamiany. To powoduje przeniesienie produktu na wylotowy tor boczny (zsyp, ześlizg), ustawiony przeważnie prostopadle do kierunku głównej osi ruchu. Rozładunek pod kątem 90° pozwala na uzyskanie dużej gęstości lokalizacji przekierowania.
W tego typu urządzeniach standardowe prędkości sortowania sięgają kilkuset produktów na minutę. Są one wykorzystywane w rozdziale ładunków o dużej rozpiętości rozmiarów, tzn. zarówno tych mieszczących się na jednym segmencie, jak i takich, które zajmują dwa człony i więcej.
W przykładowym wykonaniu segmenty sortera typu cross belt (pkt 1 na rys. 1) są montowane na ramie i wyposażane w mechaniczny zespół napędowy. Jego częścią jest przekładnia stożkowa z dwoma kołami ustawionymi względem siebie pod kątem 90° (4). Klapy z napędem pneumatycznym, zamontowane po jednej z każdej strony sortera w punktach przekierowania paczek (5), służą do wprawiania w ruch pierwszej rolki napędowej (2), na sztywno połączonej z przekładnią stożkową. Ta ostatnia natomiast przenosi ruch na drugą rolkę napędową (3), która znajduje się pod taśmą przenośnika. Wprawienie jej w ruch powoduje przemieszczenie ładunku na boczny tor.
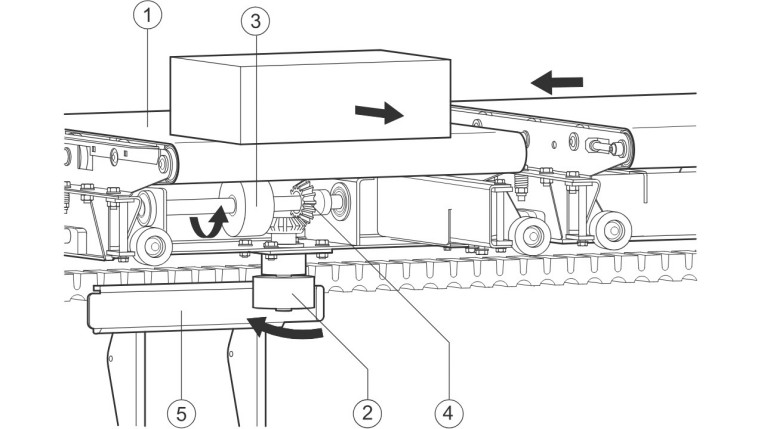
Sortery tilt tray
Kolejnym przykładem są sortery typu tilt tray, składające się z ciągu wózków z uchylnymi tackami. Po umieszczeniu ładunku na podstawce wózek przemieszcza się do punktu zrzutu. Tam się zatrzymuje. Wówczas tacka przechyla się w jedną lub drugą stronę, w zależności od położenia docelowego miejsca przekierowania produktu. Powoduje to jego zsunięcie się na boczny tor.
Kluczowym komponentem sorterów tego rodzaju są uchylne podstawki. Ich konstrukcję – materiał (przeważnie stal albo laminowane drewno), rozmiar oraz kształt – dostosowuje się do różnych typów ładunków. Przykładowo, w przypadku tych małych, transportowanych luzem, najlepiej sprawdzają się tacki wklęsłe, zaś dla większych, stabilnych towarów – powierzchnie płaskie. Funkcja przechyłu realizowana jest natomiast często z wykorzystaniem mechanizmu krzywki. Kontroluje on ruch podstawki, tak by zapewnić dokładny i bezuszkodzeniowy rozładunek, z prędkością odpowiednią do założonej przepustowości i pod kątem dobranym do specyfiki zsypu. Po opróżnieniu tacka jest automatycznie ustawiana poziomo i zostaje w takiej pozycji zablokowana.
Dzięki temu produkty układane na niej w kolejnym cyklu nie powodują jej przechyłu i nie spadają.
Sortery wyposaża się także w systemy komunikacji w podczerwieni. W przykładowym wykonaniu nadajniki i odbiorniki IR montowane są wzdłuż trasy sortera typu tilt tray. Wysyłają one polecenia sterujące dla poszczególnych wózków. Komendy są dostosowane do specyfiki ładunków – zależą np. od typu powierzchni, kształtu i wagi produktu. Wózki także wyposaża się w nadajniki i odbiorniki podczerwieni oraz mikroprocesor. Ten ostatni przetwarza odbierane polecenia i tak steruje silnikiem mechanizmu regulującego prędkość pochylania tacki oraz szybkość jej obniżania, aby uniknąć np. efektu katapulty. Wózki ponadto nadają informacje diagnostyczne analizowane w jednostkach kontrolnych rozmieszczonych na trasie sortera.
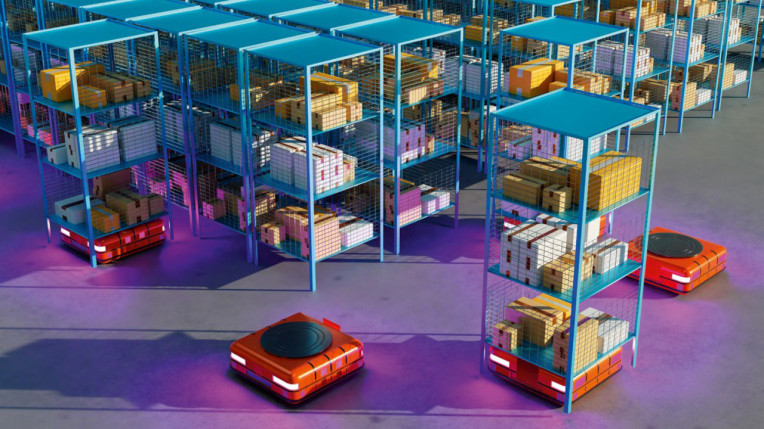
Sortery w kontroli jakości
przemyśle automatyczne systemy sortowania są zwykle częścią linii kontroli jakości. W ramach tego typu stanowisk sortery współpracują głównie z systemami wizyjnymi i oprogramowaniem do zautomatyzowanej klasyfikacji. Przykład to kontrola jakości żywności.
Dzięki niej zapobiega się dalszej obróbce albo wprowadzeniu na rynek zepsutych, uszkodzonych i niedojrzałych owoców, warzyw, zbóż czy zepsutego mięsa. W przemyśle spożywczym zapewnienie najwyższej jakości oraz bezpieczeństwa produktów ma olbrzymie znaczenie, konsumenci bowiem oczekują żywności świeżej, wolnej od wad i obcych materiałów. Osiągnięcie tego, szczególnie w produkcji na masową skalę, stanowi wyzwanie. Im jednak lepsza jakość, tym mniejsze ryzyko wycofania produktów z rynku (i poniesienia związanych z tym kosztów), a w efekcie – tym większe zaufanie konsumentów do danej marki.
Sortery w kontroli jakości wykorzystują zaawansowane, zazwyczaj zastrzeżone systemy, stanowiące kombinację oświetlenia, sensorów oraz algorytmów przetwarzania danych, które analizują wyniki pomiarów pod kątem koloru, kształtu i rozmiaru obiektów inspekcji. Na tej podstawie oceniane są ich cechy jakościowe, np. świeżość i dojrzałość owoców i warzyw oraz ich uszkodzenia, takie jak stłuczenia, w przypadku owoców (patrz ramka: Wykrywanie obitych jabłek).
W przykładowej realizacji sortera produkty są transportowane na przenośniku wibracyjnym, który zapewnia ich równomierny rozkład. To pozwala na ich dokładniejszą analizę, zmniejszając ryzyko fałszywych odrzuceń, jak i przeoczeń defektów. Sorter wyposażony jest w multispektralny system laserowy. Składa się on z kilkunastu laserów o różnych długościach fal.
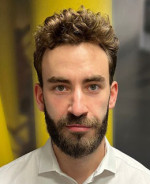
Aleksander Szepietowski
igus
Jak powinna wyglądać współpraca między producentem maszyn a klientem, by obaj osiągnęli sukces we wdrożeniu konkretnego rozwiązania z obszaru automatyzacji i robotyzacji?
Kluczowe jest zrozumienie wymagań aplikacji i wybranie urządzeń odpowiednich do ich zadań. Rozwiązania szyte na miarę, dostosowanie robota do warunków i wymagań na linii produkcyjnej – to codzienność w firmie igus. Nasze roboty są konfigurowalne i zawsze jesteśmy otwarci na wypracowanie opcji niestandardowych, na życzenie klienta. Dotyczy to szczególnie modeli kartezjańskich, ale nie tylko. Dodatkowa oś obrotowa? Dwie? Mamy na to rozwiązanie! Potrzebna jest certyfikacja FDA do pracy z żywnością? Oferujemy wersje ze stali nierdzewnej i certyfikowanych polimerów! Słuchamy klientów i stale poszerzamy naszą standardową ofertę, opierając się na ich potrzebach.
Oprócz oczywistych korzyści wynikających z prawidłowego działania procesu, wyselekcjonowanie właściwego rozwiązania optymalizuje koszty. Klient nie przepłaca za przewymiarowane urządzenie, co wpisuje się w naszą ideę ekonomicznej automatyzacji. Odpowiednio dobrany robot może być nawet dziesięciokrotnie tańszy od standardowego rozwiązania. Zwrot kosztów inwestycji nie musi więc trwać lata!
Firma igus stawia szczególny nacisk na zwiększenie przystępności automatyzacji. Nasze roboty pozwalają na śmiałe wejście w świat robotyki, nie wymagając lat specjalistycznego doświadczenia i dużych nakładów finansowych. Każdy może też pobrać za darmo środowisko programistyczne igus Robot Control i przekonać się, jak nasze roboty mogą mu pomóc, samodzielnie programując symulowanego cyfrowego bliźniaka robota.
Oferujemy darmowe konsultacje, materiały do nauki, webinary. Zapraszamy do naszego biura, gdzie w laboratorium low-cost automation można przetestować i poznać, jak działają nasze roboty kartezjańskie, delta, scara i coboty ReBeL. Wykonujemy darmowe testy praktyczne – możemy zbadać rzeczywisty czas cyklu ruchów wybranego robota z wybranym obciążeniem i trajektorią. Oferujemy też bardziej zaawansowane testy z detalami klienta czy systemem wizyjnym – są one płatne, jednak koszty zwracamy częściowo lub w całości po zakupie robota. Dzięki nim klient może mieć pewność, że inwestycja się sprawdzi.
Przykładowo, lasery fluorescencyjne mierzą zawartość chlorofilu i obecność szkodliwych substancji, takich jak aflatoksyna (związek wytwarzany przez pleśnie) w orzechach i suszonych owocach czy solanina w ziemniakach oraz innych warzywach bulwiastych. Lasery SWIR (Short Wave Infrared) z kolei rozróżniają produkty mokre od suchych, znajdując ciała obce między warzywami i owocami. Produkty niespełniające norm są usuwane z przenośnika przez zdmuchnięcie za pomocą sprężonego powietrza.
Oprogramowanie sortera wykorzystuje też sztuczną inteligencję, aby uczyć się rozpoznawać wybrakowane obiekty. W procesie sortowania algorytm AI autonomicznie decyduje, które z nich są usuwane. Jeżeli operatorzy wykryją błędy w selekcji, mogą skorygować algorytm, wskazując, które produkty zostały nieprawidłowo sklasyfikowane. AI uwzględni tę sugestię w procesie uczenia się.
Wykrywanie obitych jabłek
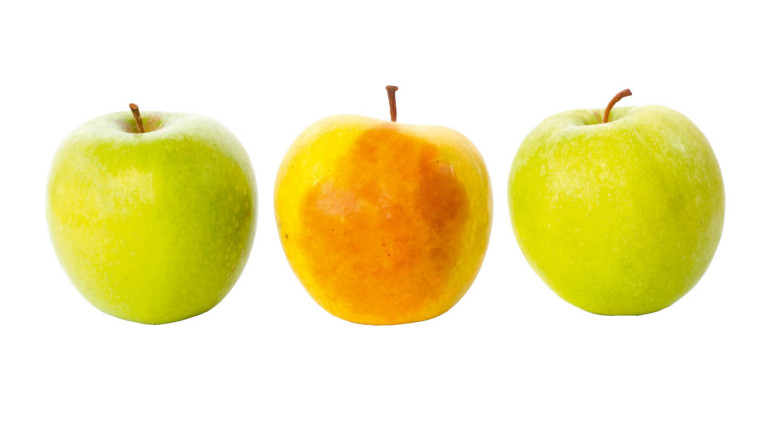
Obicia jabłek są jedną z częstszych wad, która znacząco obniża ich jakość. To przekłada się na cenę i ostatecznie możliwość zbytu. Uszkodzenia powstają podczas zbioru, transportu i magazynowania jabłek, na skutek ich upadku, przygniecenia w opakowaniu i uderzania owoców o siebie. Stłuczenia powodują nie tylko deformację kształtu jabłek, ale też zmiany biochemiczne w miąższu pod skórką, który mięknie, brązowieje i w końcu gnije. Nie tylko wpływa to na wygląd i smak jabłka, ale jeżeli rozwinie się pleśń, grozi zakażeniem innych owoców przewożonych lub przechowywanych razem z tymi uszkodzonymi.
Specyfika stłuczeń
Wykrywanie obić na jabłkach nie jest prostym zadaniem. Wpływ ma na to szereg czynników, takich jak rodzaj uszkodzenia, jego stopień, to, jak dawno do niego doszło i warunki, w jakich przebywały owoce przed i po zbiorze. Przykładowo, świeże obicia, które pojawiają się w ciągu kilku godzin po stłuczeniu, nie odznaczają się od otaczającej je skórki pokrywającej nieuszkodzony miąższ. Trudniej je więc wykryć niż te stare, dobrze widoczne. Zanim jabłka dotrą do klienta, te nowsze będą już też jednak wyraźne.
O ile zatem sortowanie owoców pod kątem ich rozmiaru i wagi łatwo zautomatyzować, o tyle obite jabłka wciąż częściej są rozpoznawane w ramach kontroli wizualnej przez pracowników. Niestety, oznaki stłuczeń (kolor, stan skórki, zapach) są przez nich interpretowane subiektywnie, więc skuteczność wykrywania zależy przez to od ich doświadczenia. W rezultacie wyniki ręcznej inspekcji mogą być niespójne. Dlatego na różne sposoby próbuje się jednak zautomatyzować to zadanie.
Ograniczenia technik detekcji
W tym celu wykorzystuje się systemy wizyjne. Te oparte na analizie obrazów rejestrowanych w świetle widzialnym są jednak niezbyt efektywne – trudność sprawia im głównie detekcja świeżych obić jabłek o różnych kolorach skórki. Pod kątem tego zastosowania pod uwagę brane są w związku z tym również inne metody, takie jak obrazowanie: SIRI (Structured-Illumination Reflectance Imaging), fluorescencyjne, termiczne, metodą rezonansu magnetycznego oraz rentgenowskie. Dostarczają one danych o strukturze wewnętrznej owoców, na podstawie których można wnioskować o uszkodzeniu miąższu. Choć w detekcji świeżych uszkodzeń techniki te sprawdzają się lepiej niż obrazowanie w świetle widzialnym, ich wdrożenie w praktyce jest trudne. Rezonans magnetyczny nie nadaje się do zastosowań w przemyśle z powodu wolnej akwizycji obrazów. Szybsze obrazowanie rentgenowskie ma małą rozdzielczość i kontrast, przez co skuteczność wykrywania stłuczeń jest niska. Ograniczona rozdzielczość dotyczy również techniki SIRI. Problemem w przypadku obrazowania termicznego są natomiast odbicia. Ponadto, ze względu na koszt i czas akwizycji, jego wykorzystanie w przemyśle w detekcji w czasie rzeczywistym staje się niepraktyczne.
Spektroskopia w podczerwieni
Alternatywą powyższych technik stała się spektroskopia w podczerwieni, wykorzystująca zależność między stężeniem danego składnika a ilością pochłanianego przez niego światła w tym przedziale długości fali. Pozwala ona wykryć stłuczenia pod skórką na podstawie nieregularności w rozkładzie zawartości wilgoci w miąższu (woda silnie absorbuje promieniowanie podczerwone w zakresach NIR (Near Infrared) i SWIR (Short-Wave Infrared)) – nawet gdy owoc wydaje się na powierzchni nieuszkodzony. Ponadto, postępy w dziedzinie czujników optycznych pozwoliły opracować metodę obrazowania hiperspektralnego dostarczającą na temat obiektu inspekcji informacji zarówno przestrzennych, jak i widmowych.
Uzupełnienie sensorów stanowi oprogramowanie do przetwarzania obrazów. Skuteczność detekcji świeżych obić jabłek rośnie w miarę rozwoju technik sztucznej inteligencji wykorzystywanych w obróbce danych z systemów obrazowania, opartych na spektroskopii bliskiej podczerwieni. W tym zastosowaniu najlepiej sprawdzają się algorytmy uczenia maszynowego nadzorowanego i splotowe sieci neuronowe.