Roboty w pakowaniu
Na stanowiskach pakowania roboty zazwyczaj realizują zadania typu pick and place. Obejmują one następującą sekwencję czynności: podniesienie obiektu, jego przeniesienie, a potem odłożenie go w miejscu docelowym, często z zachowaniem konkretnej orientacji. Takiego podejścia wymagają produkty, które należy, ze względu na ich specyfikę, podnosić i odkładać pojedynczo. Przykładami są drobne artykuły spożywcze o delikatnej strukturze, jak ciastka czy czekoladki, które przez roboty na stanowiskach pakowania są przekładane z taśmociągu linii produkcyjnej do pudełek. Wspólnymi cechami typowych aplikacji pick and place są: bardzo duża szybkość operowania przekładanymi obiektami i stosunkowo krótkie odległości, na jakie są one przenoszone.
Wprawdzie zadanie pick and place w teorii wydaje się nieskomplikowane, w praktyce jednak zorganizowanie takiego stanowiska pakowania z robotem przemysłowym może się okazać wyzwaniem. Przede wszystkim, żeby móc w pełni wykorzystać szybkości osiągalne przez roboty przemysłowe, należy zsynchronizować stanowisko pick and place z innymi liniami, stanowiskami i systemami, z którymi współpracuje. Przykładem są przenośniki taśmowe – skoordynowanie robota z taśmociągiem pozwala na pobieranie i odkładanie produktów bez konieczności zatrzymywania przenośnika. To znaczenie przyspiesza pakowanie.
Oprócz tego roboty zwykle są sterowane wizyjnie. W ten sposób nakierowuje się je na obiekt i informuje, czy – i jeśli tak, to jak – powinny zmienić jego orientację. Ponadto, opierając się na sygnale z kamery, można połączyć pakowanie z kontrolą jakości. Dzięki temu robot będzie podnosił tylko produkty spełniające zadane kryteria, pozostawiając na taśmociągu te wybrakowane, albo z sortowaniem produktów, jeżeli na taśmie wspólnie są transportowane wyroby różnego typu, np. różniące się kolorem, które należy zapakować oddzielnie.
Case study – Paletyzacja na linii pakowania farb
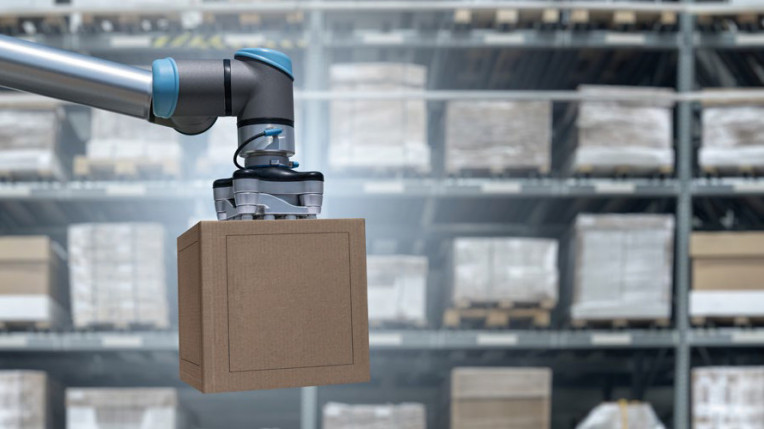
Pewne przedsiębiorstwo z branży farbiarskiej zainwestowało w zmodernizowanie przestarzałej linii pakowania i paletyzacji pojemników z farbami, na której występowały problemy z konserwacją. To powodowało częste przestoje. Celem było też zwiększenie wydajności. Integrator, który podjął się realizacji tego zadania, zorganizował stanowisko scentralizowanej paletyzacji. Obsługuje ono równocześnie trzy linie produkcyjne i pakowania: puszek farby o pojemności 1 litra, wiader o pojemności 3,5 litra i wiader mieszczących 5 litrów farby.
Stanowisko
Na opisywanym stanowisku pracują dwa roboty przegubowe, skonfigurowane tak, aby paletyzowały skrzynie lub tace puszek i wiadra w jednym cyklu. Jedna maszyna jest przeznaczona do obsługi tych pierwszych, zaś druga paletyzuje wiadra 3,5- i 5-litrowe. Ich chwytaki dobrano w taki sposób, żeby mogły manipulować pojemnikami o różnych pojemnościach i pobierać palety bezpośrednio z dozownika. Ten ostatni jest ważnym komponentem stanowiska. Zaprojektowano go tak, by zapewnić zgodność z paletami w różnych rozmiarach. Ma kompaktową budowę. Można go też rozbudować w celu dostosowania do nowych wymagań, bez uszczerbku dla ogólnego układu stanowiska.
Przebieg procesu
Proces paletyzacji zaczyna się od tego, że puszki i wiadra z farbą poddawane są kontroli wagi. Te, które nie spełniają wymagań, zostają odrzucone. Następnie robot pakujący umieszcza puszki na tacach lub w skrzynkach, zgodnie z wytycznymi danego zamówienia. Te opakowania zbiorcze są przenośnikiem transportowane na stanowisko paletyzacji. Równocześnie z drugiej linii trafiają tam wiadra 3,5- i 5-litrowe. Roboty paletyzujące pobierają z dozownika palety i układają na nich tace, skrzynki i wiadra, zgodnie z określonym wzorem. Załadowane palety są transportowane na stanowisko, gdzie zostają owinięte folią, co ma przygotować je do bezpiecznej wysyłki.
Korzyści
Wdrożenie opisywanego stanowiska przyniosło przedsiębiorstwu wiele korzyści. Przede wszystkim poprawiono niezawodność i zwiększono wydajność o kilkanaście procent. Ponadto zrobotyzowane paletyzatory ograniczyły ręczną obsługę, zmniejszając ryzyko wypadków. Specjalnie zaprojektowane chwytaki umożliwiły bezproblemową paletyzację rozmaitych typów i rozmiarów opakowań oraz obsługę różnych wzorców pakowania oraz paletyzacji. Stanowisko zostało zorganizowane tak, żeby można je było skalować, dodając kolejne przenośniki i roboty – chcąc np. sprostać większej liczbie zamówień. Dodatkowo jego układ można łatwo odtworzyć w innej lokalizacji.
Pakowanie pick and place
Wychodząc naprzeciw potrzebom w zakresie koordynowania robotów na stanowiskach pick and place z pozostałym wyposażeniem, ich producenci oferują specjalne rozwiązania programowe, w których proces synchronizowania modułów odwzorowujących poszczególne funkcjonalności jest maksymalnie uproszczony. Tego typu programy zazwyczaj pozwalają także optymalizować zadanie pakowania pod różnymi kątami, np. jego maksymalnego przyspieszenia albo zastosowania profili ruchów ograniczających zużycie energii lub zużycie mechaniczne komponentów robota.
Kolejną istotną kwestią na etapie organizowania stanowiska pakowania z robotem realizującym zadanie pick and place jest dobór odpowiedniego chwytaka. Jest to element, który ma bezpośredni kontakt z transportowanym produktem. Dlatego od jego właściwego doboru zależy zarówno to, czy przenoszony obiekt nie zostanie w trakcie transportu uszkodzony, jak i to, czy robot będzie w stanie go utrzymać. Oferta dostawców chwytaków jest pod tym względem bardzo bogata. Przykładami są te przeznaczone do manipulowania obiektami o powierzchni o wysokim połysku w taki sposób, aby nie pozostawiać na niej śladów – co jest ważne, jeżeli nie ma możliwości ich przetarcia po zapakowaniu, oraz chwytaki przystosowane do przenoszenia produktów delikatnych, takich jak jajka czy owoce. Te ostatnie wykonuje się np. z miękkiego silikonu.
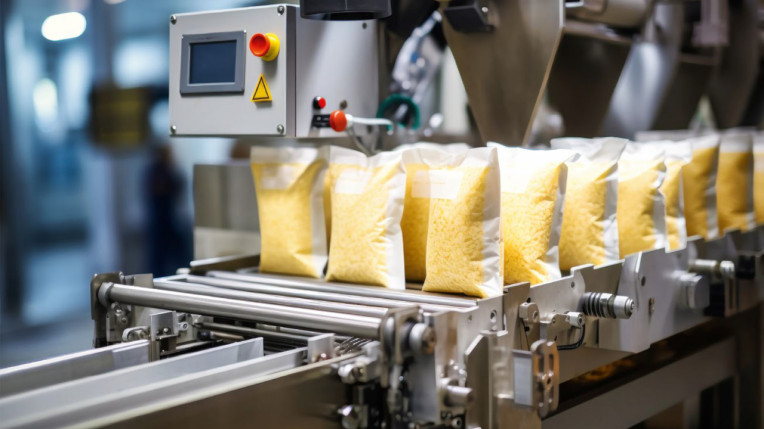