Jedną z głównych zalet identyfikacji opartej na falach radiowych jest fakt, że nośniki danych (tzw. tagi) mogą zostać ponownie wykorzystane. Pozwalają one ponadto na gromadzenie i przetwarzanie dodatkowych danych, np. dotyczących ostatnio przeprowadzanych operacji.
Nośniki te towarzyszą obrabianemu elementowi na każdym etapie produkcji i kontroli jakości - istotne informacje zostają automatycznie zapisane na tagach i odczytane na końcu łańcucha produkcji.
"Jeżeli chcemy, aby proces produkcji był niezawodny i wysoce powtarzalny, musimy wdrożyć zautomatyzowany system identyfikacji RFID, który wymaga jedynie niewielkiego wkładu pracy operatora" - wyjaśnia Heinz Ehmann, manager firmy Alfred Thun z siedzibą w Ennepetal.
W trakcie 43 lat pracy dla tradycyjnych firm rodzinnych był świadkiem wielu prób wprowadzenia ręcznego systemu nadzoru produkcji. Ze względu na wysoki nakład pracy, jaki niosą za sobą takie rozwiązania, nigdy nie były one brane pod uwagę jako realne opcje.
Obecnie, wraz z rozwojem technologii RFID, dostajemy nowe możliwości realizacji zautomatyzowanych systemów kontroli i nadzoru produkcji materiałów. Dzięki takim rozwiązaniom rodzinna firma mogła zwiększyć wydajność i utrzymać wiodącą na rynku pozycję we wszystkich swoich segmentach produktów.
Firma Thun zaopatruje przemysł rowerowy na całym świecie w łożyska wewnętrzne do rowerów miejskich, dziecięcych i górskich. Ponadto dostarcza kompletne komponenty do rowerów elektrycznych systemu Pedelec, których popularność w ostatnim czasie stale rośnie.
Firma licząca 60 pracowników wytwarza każdego roku prawie milion sztuk łożysk, co daje jej 60% udziału i czyni jednym z liderów na rynku europejskim.
WYMAGANIA APLIKACJI
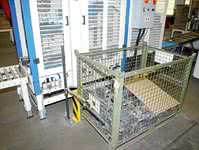
Fot. 1. Głowica zapisująco-odczytująca HF niezawodnie odczytuje nośniki danych RFID zamontowane na siatce kontenera, niezależnie od dużej ilości metalu znajdującej się wokół
W 2009 roku firma zdecydowała się zmodernizować swoją produkcję. Celem było wdrożenie pewnego systemu nadzoru partii materiału w całym łańcuchu produkcji przy użyciu systemu RFID. W trakcie wdrażania należało rozwiązać kilka technicznych kwestii, takich jak sposób montażu nośnika, proces przyjęcia towaru do identyfikacji, a także etap oczyszczania i powlekania łożysk.
Pierwszym rozwiązaniem, jakie wzięto pod uwagę, był system RFID pracujący na częstotliwości UHF. Zaletą tego zakresu częstotliwości jest niewątpliwie zasięg pracy urządzeń oraz elastyczność całego systemu. Zastosowanie jej w środowisku produkcyjnym firmy Thun nie było jednak takie oczywiste ze względu na metalową obudowę koszy transportowych, do których miały być przymocowane nośniki.
Postanowiono wykorzystać alternatywne rozwiązanie, które zostało zaproponowane przez integratora systemów, firmę Weingartner Automatisierung z Ober hausen. Rozwiązanie to wykorzystuje system BLident firmy Turck. BLident to bogaty pakiet produktów i rozwiązań identyfikacji RFID, które spełniły wszystkie wymagania projektu.
System firmy Turck pozwala na jednoczesne stosowanie komponentów HF i UHF. W pierwszym etapie projektu wykorzystano technologię HF, gdzie do komunikacji używana jest częstotliwość 13,56 MHz. W tym przypadku zmniejszony jest wpływ potencjalnych zaburzeń, co było szczególnie istotne w przypadku pracy w otoczeniu urządzeń generujących silne zakłócenia elektromagnetyczne.
Decyzja o wyborze tego rozwiązania zapadła po udanym teście zanurzenia nośników RFID w kąpieli galwanicznej. Wysoka temperatura i kwaśne środowisko galwaniczne nie zaszkodziło tagom, które cechują się stopniem ochrony IP67. Jednym z wyzwań było też dostrojenie komunikacji pomiędzy elementami sieci, które miały być dostosowane do systemu ERP Navision.
REJESTRACJA OTRZYMANYCH TOWARÓW
Proces identyfikacji rozpoczyna się w momencie, gdy towar jest odbierany. Jeżeli dokument dostawy jest wyposażony w kod Data Matrix, komponenty od dostawców są skanowane. Dane docierają do systemu ERP i są łączone z polem UID nośnika RFID przypisanego do odpowiedniego kosza transportowego.
Wszystkie dane gromadzone w centralnej bazie danych SQL są odczytywane i zapisywane za pomocą systemu Middleware Visam. Thun zoptymalizował ten proces, pozwalając, aby dostawca mógł zachować minimalny poziom zapasów. Aktualnie dostępne i wymagane ilości mogą być pobierane z systemu ERP w dowolnym momencie za pomocą dostępu online.
System identyfikacji sprawdził się szczególnie na etapie oczyszczania i montażu łożysk. Czystość łożyska musi być zagwarantowana na każdym etapie procesu produkcyjnego. Dzięki tagom RFID w dowolnym momencie wiadomo, która partia produkcyjna jest przetwarzana. Światło lampki K50 sygnalizuje pracownikowi, czy procedura jest wykonywana prawidłowo, czy też nie.
![]() ![]() Fot. 2. Nośniki danych RFID są pewnie zamontowane na metalowym kontenerze przy użyciu elementu dystansującego |
Czerwone światło wskazuje błąd. W trakcie wdrażania systemu pojawił się też pewien problem, który został szybko rozwiązany. Wykorzystywana w procesie oczyszczania śrutownia miała ładowność jedynie 80 kg, podczas gdy kosze transportowe były dwukrotnie cięższe.
W przeszłości używanie wag wymuszało ręczne kalibrowanie, obecnie proces ten udało się zautomatyzować. Dzięki technologii RFID wszystkie wałki z jednego kosza transportowego mogą być łatwo przypisane do właściwej serii.
Podczas opróżniania kosza czujnik mierzy kąt nachylenia, co pozwala automatycznie na jego ponowne napełnienie. Wykorzystanie czujnika znacznie usprawniło pracę systemu, ponieważ w przeszłości zdarzały się przypadki opóźnień spowodowane powtórnym trafieniem do procesu pełnego kosza.
ZAPEWNIANIE JAKOŚCI
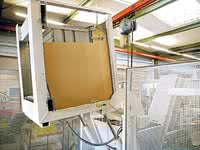
Fot. 3. Inklinometr na koszu informuje, kiedy kontener jest opróżniany
Kolejnym etapem była automatyzacja montażu specjalnych uchwytów. W przeszłości pracownik ręcznie wprowadzał specjalną konfigurację zawierającą typ uchwytu za pomocą panelu operatorskiego znajdującego się na maszynie montującej. Niestety przy stosowaniu wielu typów uchwytów taki sposób pracy prowadził do błędów.
Obecnie zamówienie jest wprowadzane centralnie za pomocą systemu ERP i przesyłane bezpośrednio do maszyny, gdzie pracownik jedynie je akceptuje i uruchamia proces. Maszyna odczytuje wszystkie potrzebne informacje zawierające ustawienia i komponenty z bazy danych, a następnie ustawia poprawną konfigurację.
Głowice RFID odczytują dane z umieszczonych na koszach nośników, zapewniając, że właściwe komponenty zostaną użyte w bieżącym zamówieniu. Czujnik nachylenia firmy Turck gwarantuje z kolei właściwe opróżnienie kosza.
Informacja z czujnika i odczytane z nośnika dane są zbierane razem by, za pomocą interfejsu systemu BL67 i środowiska CoDeSys, a następnie przesyłane z wykorzystaniem protokołu Modbus TCP do systemu Middleware Visam.
TO NIE WSZYSTKO
Udane wdrożenie w firmie Thun to tylko jeden z przykładów, gdzie system BLident mógł pokazać niektóre ze swoich możliwości. Rodzina produktów BLident opiera się na modułowych systemach BL67, BLcompact i BL20. W zależności od stopnia skomplikowania układu, jedna stacja umożliwia obsługę od 2 do 16 kanałów RFID.
Systemy mogą pracować jako interfejsy sieci Profibus-DP, DeviceNet, Modbus TCP, Ethernet/IP oraz Profinet. W zależność od potrzeb interfejs sieci (slave) może być programowany zgodnie ze standardem IEC 61131-3 w środowisku CoDeSys.
Sercem takiego układu jest 32-bitowy procesor RISC z pamięcią programu 512 kB przetwarzający do 1000 instrukcji AWL w czasie krótszym niż 1 ms. Interfejs programowalny dzięki swojej "inteligencji" odciąża pracę sterownika, gdyż całość procedur związanych z działaniem systemu RFID może być obsługiwana z jego poziomu.
Możliwości systemu identyfikacji BLident wykraczają poza zwykłą identyfikację elementu. Kontrola jakości (nośnik przechowuje dane kontrolne decydujące o tym, czy element przejdzie do następnego etapu produkcji), identyfikacja w transporcie i logistyce czy magazynach wysokiego składowania - to tylko niektóre z miejsc, gdzie BLident został z powodzeniem wdrożony.
Bartłomiej Besz
TURCK
www.turck.pl