WYZWANIA I ZAŁOŻENIA PROJEKTOWE

Rys. 1. Ciasta przed znakowaniem
Specyfika projektu związana była z samym procesem produkcyjnym, w którym niemożliwy był kontakt fizyczny z ciastem w celu posortowania go i ułożenia na linii. Odpowiednie ułożenie produktu ułatwiłoby wykonanie prostego systemu do znakowania opartego na dyszach i czujnikach optycznych. Kolejnym wyzwaniem była wydajność linii, która wymuszała znakowanie ośmiu obiektów w ciągu jednej sekundy.
Założenia projektu skłoniły integratora do zastosowania nowoczesnego systemu wizyjnego wraz z matrycą ultraszybkich dysz dozujących. Po przeprowadzeniu szeregu testów z różnego typu dyszami wybrano wprawdzie system spełniający wymagania techniczne, ale okazał się on za drogi w stosunku do wymagań klienta. Należało poszukać innego, bardziej ekonomicznego rozwiązania.
Z tych powodów zdecydowano się na zastosowanie systemu z jedną dyszą, która jest odpowiednio przemieszczana. Rozwiązanie to ograniczało koszty, jednakże wymagało zastosowania precyzyjnego, ultraszybkiego napędu do pozycjonowania. Z pomocą przyszli doradcy techniczni firmy Omron, którzy zaproponowali użycie nowoczesnego napędu liniowego, który w łatwy sposób można było zintegrować z systemem wizyjnym. Za wyborem takiego rozwiązania przemawiał również fakt, że wszystkie moduły sterowania były dostępne z magazynu w ciągu kilku dni.
SYSTEM WIZYJNY
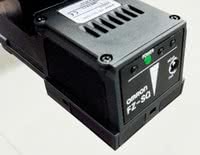
Rys. 2. Głowica systemu wizyjnego
Wybrany system wizyjny bazuje na dwóch inteligentnych kompaktowych kamerach typu FZ-SQ100N oraz kontrolerze FZ5-L355. Układ pozwala na sterowanie zewnętrzne poprzez port I/O w czasie poniżej 1 ms, co umożliwia precyzyjne sterowanie wyzwalaniem wykonania zdjęcia oraz otrzymanie potwierdzenia przetworzenia obrazu.
Kontroler wizyjny tworzy obraz punktów na podstawie wykonanego zdjęcia i pozwala na odczyt danych poprzez port EtherCAT. Algorytm pracy systemu wizyjnego polega na znalezieniu krawędzi, dopasowaniu ich do kształtów i znalezieniu punktów na obiekcie w odpowiedniej odległości od środka.
WYBÓR NAPĘDU
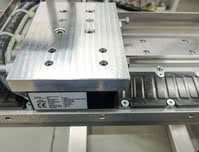
Rys. 3. Zastosowany napęd liniowy
Biorąc pod uwagę ciężar głowicy i wózka liniowego oraz przyśpieszenia i prędkości, z jakimi musi się poruszać układ dozujący, wybrano docelowy napęd liniowy. Składa się on z:
- dwóch magnetycznych ścieżek 384 mm (serii R88L-EC-FM),
- liniowej cewki (serii R 88L-EC-FW),
- serwonapędu (R88D-KN02H-ECT-L).
Całość zmontowano na profilu ze stali nierdzewnej wraz z szyną i wózkiem HIWIN. Do pozycjonowania zastosowano krańcówkę z amortyzatorem i czujnikiem elektromagnetycznym. Konfiguracja osi układu znakowania opiera się na głowicy pomiarowej LIA20 z okresem podziału 20 µm oraz enkoderze obrotowym E6C2-C 2000 impulsów. Liniowy układ pomiarowy odpowiedzialny jest za określanie pozycji głowicy znakującej, zaś obrotowy - pozycji taśmy linii produkcyjnej.
UKŁAD STEROWANIA ORAZ ZASTOSOWANY ALGORYTM
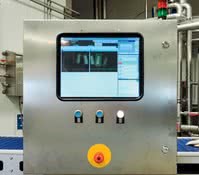
Rys. 4. Panel sterujący podczas pracy systemu
Do kontroli systemu użyto sterownika NJ301-1100 wraz z wyspą I/O NX-ECC201 składającą się z:
- 16 wejść cyfrowych NX-ID5442,
- 16 wyjść cyfrowych NX-OD5256,
- 3 wejść enkodera NX-EC0142.
Nad bezpieczeństwem pracy czuwa przekaźnik bezpieczeństwa G9SA zintegrowany z systemem bezpieczeństwa sterownika napędu liniowego oraz wyłącznikiem bezpieczeństwa.
Algorytm pracy systemu znakowania zawiera dwa główne programy wymieniające ze sobą dane poprzez tablicę punktów w osi x i y. Pierwszy program jest odpowiedzialny za wyzwolenie wykonania zdjęcia, monitorowanie pozycji linii oraz odczyt listy punktów z systemu wizyjnego, zaś drugi steruje pozycją głowicy dozującej i momentem uruchomienia głowicy znakującej. Algorytm w tym programie odpowiada również za sortowanie punktów i optymalizację trajektorii ruchu głowicy.
PODSUMOWANIE
Pierwsze testy u klienta wypadły pomyślnie. Dzięki wsparciu specjalistów z firmy Omron konfiguracja systemu wizyjnego oraz nauczenie go wykrywania obiektów na linii trwała niecałą godzinę. Implementacja algorytmu oraz konfiguracja parametrów napędu liniowego w środowisku Sysmac Studio nie sprawiła większych trudności. Układ działa poprawnie.
iNEO-tech z Wrocławia, firma będąca integratorem omawianego systemu, zajmuje się automatyzacją i wizualizacją procesów produkcyjnych. Na jej portfolio składają się między innymi: układ utrzymania lepkości cieczy online, układ sygnalizacji stopnia napełnienia systemu odciągów, system rozproszonych paneli UI. Wprowadziła ona również na rynek autorski system MES (Manufacturing Execution System), który pozwala na optymalizację procesów produkcyjnych.
iNEO-tech
Omron Electronics
www.industrial.omron.pl