CZYM JEST WYTWARZANIE PRZYROSTOWE?
Stapianie laserowe jest jednym z określeń techniki wytwarzania przyrostowego (nazywanej również: drukiem 3D, laserowym wytwarzaniem warstwowym, szybkim prototypowaniem oraz laserowym przetapianiem/spiekaniem), w której do konsolidacji proszków metalicznych do postaci półwyrobów lub gotowych części o wysokiej gęstości (na poziomie 99,7%) stosuje się wiązkę laserową. Proces wytwarzania przyrostowego - warstwa po warstwie - umożliwia produkcję trójwymiarowych produktów z wykorzystaniem dwuwymiarowych przekrojów modelu komputerowego (CAD).
ETAPY PROCESU WYTWARZANIA PRZYROSTOWEGO
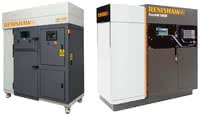
Fot. 1. System stapiania laserowego proszków metalicznych firmy Renishaw: RenAM 500M i AM 400
Do etapów procesu wytwarzania przyrostowego należy zaliczyć:
- zaprojektowanie trójwymiarowego modelu wytwarzanej części za pomocą oprogramowania CAD,
- przygotowanie pliku sterującego procesem wytwarzania z wykorzystaniem modelu 3D CAD.
- przekazanie pliku procesowego do jednostki sterującej urządzeniem w celu wytworzenia części.
Opracowanie pliku sterującego obejmuje: ustalenie pozycji modelu części w przestrzeni roboczej (tzw. ustalenie strategii pozycjonowania), wygenerowanie struktur wspierających, podział modelu wraz ze strukturami wspierającymi na warstwy o zdefiniowanej grubości, a następnie zdefiniowanie parametrów pracy urządzenia (dla wybranego typu metalicznego materiału proszkowego).
Sam proces konsolidacji materiału proszkowego do zadanego kształtu części polega na równomiernym rozprowadzeniu warstwy materiału proszkowego na powierzchni platformy bazowej urządzenia, a następnie na konsolidacji tego materiału z wykorzystaniem laserowego układu wykonawczego. Ten proces jest powtarzany dla każdej zaprogramowanej warstwy modelu 3D i pozwala na budowanie elementów o złożonej geometrii.
ZALETY TECHNOLOGII WYTWARZANIA PRZYROSTOWEGO
W porównaniu z tradycyjnymi technologiami stapianie laserowe pozwala na: znaczące zmniejszenie strat materiałowych (ubytków), skrócenie czasu trwania procesu produkcyjnego oraz wyeliminowanie konieczności stosowania dodatkowych narzędzi. Możliwość szybkiego prototypowania lub wytwarzania elementów o skomplikowanych kształtach, których wyprodukowanie klasycznymi metodami ubytkowymi i odlewniczymi jest niemożliwe bądź zbyt kosztowne, to kolejna zaleta systemów laserowego wytwarzania przyrostowego.
Nie bez znaczenia jest również fakt, że stapianie laserowe nadaje się do produkcji wyrobów o strukturze kratownicowej i posiadających kanały wewnętrzne. Konstruktorzy zindywidualizowanych wyrobów wytwarzanych tą techniką stosują oprogramowanie komputerowe do projektowania oraz wspierania samego procesu stapiania laserowego.
ZASTOSOWANIE SYSTEMÓW DRUKU 3D
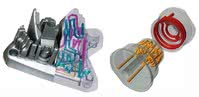
Fot. 2. Przykładowe wizualizacje 3D formy wtryskowej oraz wkładek z układami kanałów konformalnych
Technologia stapiania laserowego proszków metalicznych ma swoje miejsce w różnych gałęziach przemysłu, a zwłaszcza w wytwarzaniu części na potrzeby branży narzędziowej (formy wtryskowe oraz wkładki z konformalnymi układami chłodzącymi), motoryzacyjnej i lotniczej, a także w produkcji dóbr konsumpcyjnych, wyrobów artystycznych i medycznych (protezy szkieletowe, mosty protetyczne, implanty stomatologiczne i ortopedyczne).
Systemy stapiania laserowego Renishaw są przykładem wykorzystania technologii wytwarzania przyrostowego do produkcji części do różnych zastosowań. Części są budowane z metalowych proszków, które stapia się laserowo w kontrolowanej, obojętnej atmosferze argonu podczas nakładania kolejnych warstw o grubości od 20 do 100 μm. Systemy Renishaw są wyposażone we włóknowe lasery iterbowe o mocy w zakresie od 200 do 500 W oraz w komorę próżniową; zużywają niewielkie ilości gazu obojętnego (do 50 l/h).
Zostały zaprojektowane w sposób zapewniający łatwość obsługi - zastosowano w nich m.in. dotykowy panel i przejrzyste menu operatora. W przypadku systemów Renishaw AM250 i AM400 przestrzeń robocza ma wymiary 250 × 250 × 300 mm (dla systemu RenAM 500M Z = 350 mm), prędkość skanowania wynosi 2000 mm/s, natomiast wielkość plamki lasera - 70 μm/75 μm (RenAM 500M).
Technologia stapiania laserowego umożliwia użycie wielu typów proszków metalicznych, takich jak: stal nierdzewna 316L, stop aluminium AlSi10Mg, stop tytanu Ti-6Al-4V, stop kobaltowo-chromowy CoCr, stop niklu Inconel 625/718 oraz stal narzędziowa typu maraging.
WYTWARZANIE WKŁADEK Z UKŁADEM WEWNĘTRZNYCH KANAŁÓW CHŁODZĄCYCH
Laserowe wytwarzanie części z proszków metalicznych staje się coraz bardziej pożądaną technologią wspierającą optymalizację procesu wtrysku materiałów polimerowych przez zastosowanie specjalnie zaprojektowanych wkładek do form wtryskowych. Wspomniane wkładki, wyposażone w indywidualnie zaprojektowane układy kanałów konformalnych, pozwalają na redukcję czasu cyklu wtrysku nawet o 70% dzięki zwiększeniu efektywności chłodzenia i w efekcie - na zmniejszenie kosztów produkcji.
Wykorzystanie technologii wytwarzania przyrostowego umożliwia produkcję wkładek o bardzo skomplikowanych kształtach z uwzględnieniem przebiegu kanałów konformalnych w bliskiej odległości od miejsc chłodzonych. Klasycznie stosowane ubytkowe metody wytwarzania wkładek do form wtryskowych mają poważne ograniczenia ze względu na lokalizację kanałów chłodzących oraz zmianę ich kierunku i przekroju. Wytwarzanie przyrostowe stało się alternatywą znoszącą ograniczenia klasycznych metod produkcji.
Oferuje szerokie możliwości optymalizacji konstrukcji wkładek oraz samych form wtryskowych. Należy podkreślić, że właściwości materiału wkładek wytwarzanych przyrostowo spełniają wymagania stawiane tego typu wyrobom. Twardość drukowanej wkładki osiąga wartość ponad 50 HRC (dla stali typu maraging po dodatkowej obróbce cieplnej). Jak już wspomniano, zaletami tej technologii są zmniejszone zużycie materiału oraz zminimalizowanie ilości odpadów poprodukcyjnych.
dr inż. Bogdan Dąbrowski
Renishaw Sp. z o.o.
www.renishaw.pl