- Jesteśmy w dziale pakowania JBB – z jakich maszyn korzysta firma?
Mamy tu zintegrowanych 17 linii, na których odbywa się pakowanie automatyczne i półautomatyczne z wykorzystaniem robotów firmy FANUC. Linie pakowania są zintegrowane z zamykarką automatyczną, która wykorzystując sygnały cyfrowe od razu wie z jakim produktem ma do czynienia. Dzięki elektronicznej wymianie danych przezbraja się do konkretnego formatu.
- Ile kartonów obsługują te linie?
Obsługujemy około 1500–1700 opakowań kartonowych różnego kalibru w ciągu każdej godziny. Dzięki takiej wydajności w ciągu doby jesteśmy w stanie zapakować powyżej 300 ton gotowego wyrobu.
- Jaka rolę w tym procesie pełnią roboty?
Komórka paletyzacyjna jest wyposażona w cztery roboty FANUC R-2000iB/185L. Trzy z nich dysponują chwytakiem podciśnieniowym, umożliwiającym swobodne przemieszczanie ładunku o masie nawet 180 kg. Roboty są odpowiedzialne za paletyzowanie kartonów zawierających gotowy produkt, zamykanych na wcześniejszych etapach procesu. Są bardzo elastyczne i bez trudu radzą sobie z obsługą czterech różnych kompozycji kartonów na palecie. Dodatkowo żeby wiązać kolumnowe ustawienie mozaik i kartonów stosujemy przekładki, które robot układa na wybranych warstwach, co jest określone w jego programie, by zapewnić stabilność opakowań na palecie.
- Jaki jest klucz schematów paletyzacji?
W ramach naszej produkcji realizujemy oczywiście zamówienia dla sieci, ale przeważnie jest to szarża konkretnego asortymentu produktu. Poza tym mamy pewną sezonowość produkcji. W naszym asortymencie jest ponad trzysta produktów, których udział w globalnej produkcji waha się w zależności od sezonu.
Roboty perfekcyjnie pakują kartony na palety niezależnie od ich zawartości. Każda z palet otrzymuje indywidualny numer. Dzięki temu w magazynie od razu identyfikujemy poszczególne produkty i płynnie kierujemy je do odpowiednich odbiorców.
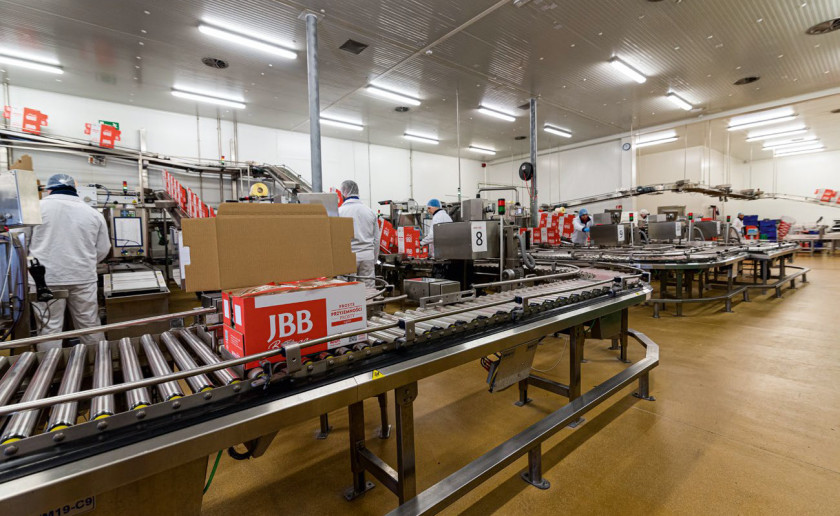
- Czy nowoczesne roboty wymagają zastosowania specjalnych palet?
Dziś na rynku liczy się indywidualne podejście do klienta. Odbiorcy naszych produktów mają bardzo zróżnicowane oczekiwania w obszarze transportu i logistyki. Większość klientów wciąż preferuje tradycyjne palety drewniane, ale są również tacy, którzy wolą plastikowe. W komórce paletyzacyjnej JBB mamy możliwość obsługi obu rodzajów palet.
- Proces przebiega automatycznie, bez potrzeby jakiejkolwiek ingerencji pracowników?
Komórka paletyzacyjna jest wygrodzona i solidnie zabezpieczona, co uniemożliwia dostęp osobom niepożądanym. Roboty pracują samodzielnie na zasadzie sygnałów wejść/wyjść, a to gwarantuje zarówno bezpieczeństwo produktu, jak i ludzi przebywających w hali produkcyjnej. By uzyskać najwyższy możliwy poziom bezpieczeństwa mamy także dodatkowe zabezpieczenia. Dzięki temu człowiek, który przekroczy obszar komórki, zawsze jest w pełni bezpieczny.
- Poruszamy temat bezpieczeństwa ludzi – jak wyglądało ono przed automatyzacją?
Dzięki 17 liniom obszaru zautomatyzowanego wielu pracowników, przeszło do innych zadań, gdzie ich wsparcie jest bardzo potrzebne. Choć nie jestem w stanie podać dokładnych danych to na pewno warto zaznaczyć, że po wprowadzeniu automatyzacji wzrosła wydajność, znacząco poprawiła się ergonomia, sprawność i bezpieczeństwo całego procesu. Ludzie, którzy dziś obsługują te maszyny, bardzo cenią sobie komfort pracy. Nie są zmęczeni czy znużeni realizowaniem tych samych czynności.

- Czy łatwo było wdrożyć pracowników do innego charakteru pracy?
Na samym początku wprowadzania zmian trzeba było wypracować nowe nawyki. Pewnie nie wszystkim było łatwo się przestawić, ale później wszystko przebiegało już bardzo płynnie. W procesie transformacji bardzo wsparł nas Zarząd Firmy. Wysłano nas na szkolenia, które pomogły w rozwoju świadomości i zdobyciu nowych umiejętności. Dziś potrafimy radzić sobie z tymi maszynami i działamy jeszcze bezpieczniej.
- Na czym polega praca operatorów w obszarze paletyzacji?
Operatorzy mają za zadanie wybrać odpowiedni program i nadzorować proces. W razie nieprzewidzianych problemów oczywiście także odpowiednio reagować. Nie jest to trudne bo w razie awarii na jednym panelu operatorskim jesteśmy w stanie szybko przejść na drugi screen i wykonać niezbędną operację w innym miejscu, a osoby odpowiedzialne za serwis w międzyczasie mogą naprawić ewentualną usterkę.
- Jak dawno wprowadzili Państwo roboty?
Pierwsza część komórki paletyzującej – z jednym robotem – została zbudowana w 2013 roku. Już rok później pojawiły się dwa kolejne roboty, a w 2017 roku czwarty robot. Inwestycja została podzielona na etapy, by można było pogodzić proces wdrożeniowy z prowadzeniem produkcji. Paletyzacja to jeden z ostatnich etapów naszej produkcji dlatego nie mogliśmy zatrzymać linii nawet na chwilę.
- Jak poradzili sobie Państwo z budową tego systemu?
Nasze linie były budowane przy wsparciu hiszpańskiego integratora. Działaliśmy w stałym porozumieniu stron, bo specyfikacja była bardzo rozbudowana. Z drugiej strony nasze potrzeby były bardzo jasne i czytelne więc nie było żadnych problemów komunikacyjnych, a efekty działania bardzo skuteczne.
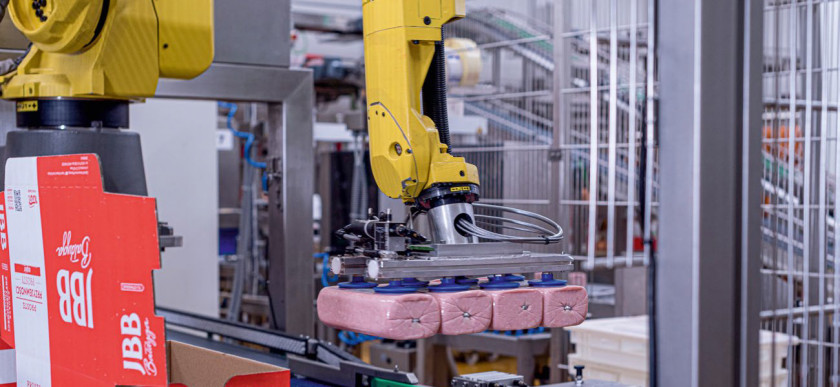
- Czy robotom w komórce paletyzacyjnej towarzyszą inne rozwiązania techniczne?
Cała komórka paletyzacyjna jest usiana skanerami ponieważ musimy w każdej chwili wiedzieć, gdzie jest każdy z wytworzonych produktów, w jakim kartonie, na jakim etapie produkcji czy pakowania.
Obszar pakowania to jeden z najbardziej wymagających odcinków naszej produkcji. Tu innowacji mamy sporo i wciąż pracujemy nad nowymi, które pozwolą nam jeszcze lepiej dostosować się do potrzeb i oczekiwań rynku.
Kolejne niestandardowe podejście do opakowań w naszym zakładzie to brak folii stretch. W efekcie oszczędzamy środowisko, przestrzeń i czas.
- Przejdźmy do linii półautomatycznych – jaka jest ich wydajność i jakie zadania wykonują roboty?
Roboty FANUC serii M-20iA są tu wykorzystywane do układania produktów w opakowaniach zbiorczych. Dzięki nim bardzo sprawnie zapełniamy kartony produktem jeszcze zanim trafią do komórki paletyzacyjnej. Linie do pakowania zapewniają wydajność obsługi produktu na poziomie 7 ton ma godzinę. Wszystko dzieje się tu bardzo sprawnie.
- Czy wprowadzenie innowacji na tym stanowisku również poprawiło komfort pracy pracowników?
Zdecydowanie tak. To stanowisko jest najlepszym przykładem tego jak nowe technologie sprawiły, że niegdyś jedno z najcięższych stanowisk dla pracowników przekształciło się w jedno z najlżejszych i najbardziej lubianych. Monotonne prace wykonują dziś roboty, a pracownicy korzystają z praktycznych rozwiązań wykorzystujących podciśnienie, co niweluje masę produktu i znacznie poprawia komfort pracy.
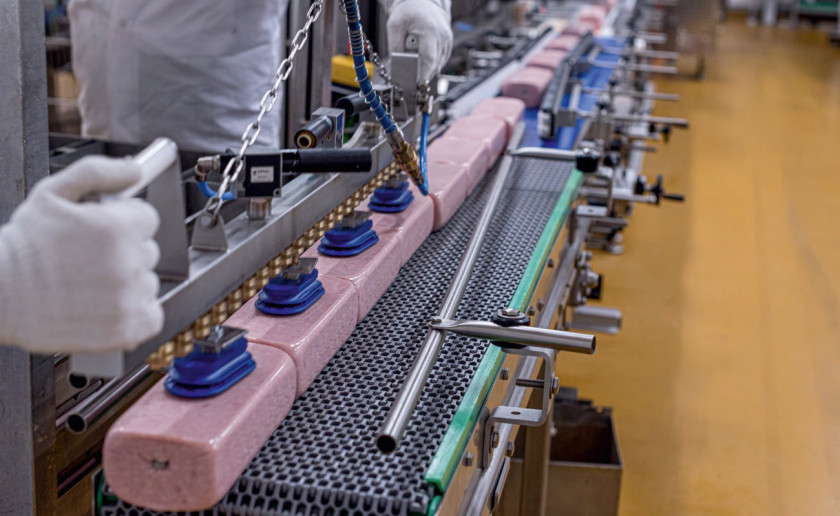
- Czy planują Państwo dalszą rozbudowę linii?
Tak, oczywiście. Intensywnie myślimy o możliwościach wykorzystania kolejnych robotów marki FANUC.
- Dziękuję za rozmowę.
FANUC Polska
www.fanuc.pl