Chociaż silniki przemysłowe są relatywnie wysoce niezawodne, są one stosowane w bardzo wielu procesach, co sprawia, że każdy z nich jest potencjalnym pojedynczym punktem awarii. Za każdym razem, gdy psuje się silnik lub jeden z kluczowych systemu, może być to katastrofalne w skutkach i powodować przestój całej instalacji. Oczywiście firmy mają zazwyczaj na stanie części zamienne, jednak nie można wyeliminować czasu potrzebnego do naprawy systemu i przywrócenia produkcji, a także usunięcia ekonomicznych strat z tym związanych.
Dzisiaj przedsiębiorstwa z różnych branż mają dostęp do nowych rozwiązań w zakresie monitorowania stanu maszyn (Condition-based Monitoring, CbM). Zapewniają one wiele korzyści, umożliwiając ciągłe monitorowanie silników, pomp, przekładni i innych systemów mechatronicznych, co skutkuje zmniejszaniem przestojów, zwiększoną produktywnością i oszczędnością w zakresie kosztów. Ponadto metodologia predykcyjnego utrzymania ruchu (Predictive Maintenance, PdM) pozwala prognozować przyszłe zmiany w zakresie aktywów, możliwe awarie oraz wyznaczać czynności serwisowe, które należy wykonać, aby zapobiegać występowaniu przestojów. Coraz więcej przedsiębiorstw zaczyna postrzegać tego typu rozwiązania jako niezbędne dla ich efektywnej działalności.
ZMIANA STRATEGII UTRZYMANIA PARKU MASZYNOWEGO
Wdrażanie praktyk inteligentnego utrzymania ruchu jest kluczowym czynnikiem umożliwiającym rozwój Przemysłu 4.0 i koncepcji inteligentnych fabryk. Monitorowanie stanu maszyn oznacza ciągłą kontrolę warunków ich pracy oraz stanu zasobów, co pozwala na wczesne wykrywanie potencjalnie występujących awarii. Tego typu strategia umożliwia precyzyjne określanie momentu, gdy monitorowany parametr osiąga niezadowalający poziom. Dodatkowo, wykorzystując odpowiednie wzory i modele, możliwe jest wdrożenie strategii predykcyjnego utrzymania ruchu. Prace serwisowe prowadzone są na podstawie analizy monitorowanych parametrów – zwiększona temperatura, wysoki poziom hałasu i nadmierne wibracje są predykcyjnymi wskaźnikami nieprawidłowego działania maszyn. Ostatecznym celem jest wczesne wykrywanie i ostrzeganie o awariach.
Czas to naprawdę pieniądz, szczególnie jeśli chodzi o wykrywanie degradujących się maszyn i innych urządzeń Na rysunku 1 przedstawiono, jak rosną koszty produkcji zależnie od czasu wykrywania problemów z urządzeniami. System monitorowania, który pozwala na ujawnienie zawczasu anomalii, może zwrócić się zdecydowanie szybko! Podejmując proaktywne działania oparte na zaawansowanej analizie danych, można przewidywać i unikać awarii, zamiast wykonywać serwis jedynie jako czynność reaktywną, następującą po awarii maszyny. Kombinacja różnych metod wykrywania, dzięki wykorzystaniu tzw. sensor fusion, pozwala na wczesne i skuteczne wykrywanie oraz rozpoznawanie przyczyn awarii.
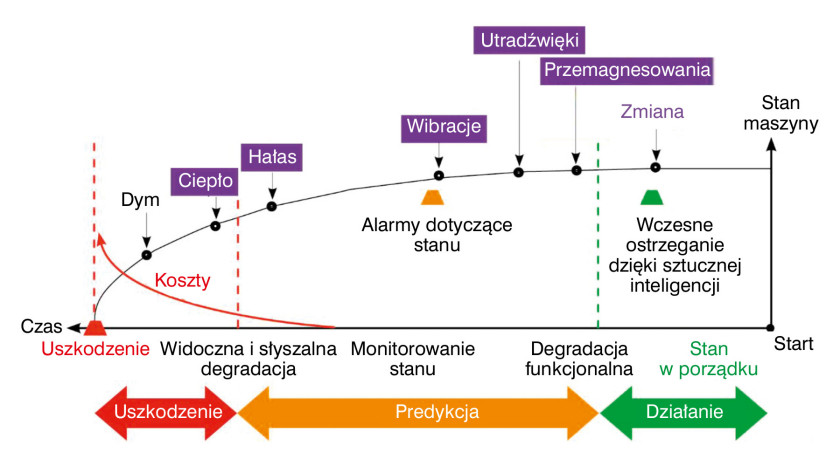
Do niedawna jedynie duże, wysokiej klasy instalacje – np. w elektrowniach atomowych – mogły być wyposażane w tego typu kompleksowe systemy monitorowania. Dzisiaj, dzięki postępowi technologicznemu, rozwiązania CbM, a wraz z nimi metodologie predykcyjne, mogą pojawiać się w coraz większej liczbie sektorów przemysłowych, zapewniając znacznie głębszy wgląd w stan wykorzystywanych maszyn.
Technologia CbM ewoluuje z platformy wykrywania usterek w kierunku systemów, które mogą faktycznie prognozować problemy i sugerować najlepsze możliwe warianty działania. W nadchodzących latach rozwiązania sztucznej inteligencji (AI) i uczenia maszynowego (ML) zapewnią jeszcze większe umiejętności przewidywania usterek oraz sugerowania ich napraw, co pozwoli na wdrażanie "inteligentnych" systemów utrzymania ruchu i serwisowych.
ROZWIĄZYWANIE PROBLEMÓW ZWIĄZANYCH Z PRODUKCJĄ
Monitorowanie stanu maszyn wspomagane przez AI i ML to potężny zestaw narzędzi, który pozwala na rozwiązywanie złożonych problemów produkcyjnych wymagających wiedzy specjalistycznej. Tego typu zagadnienia niejednokrotnie wykraczają poza umiejętności operatorów w przemyśle czy firm będących partnerami zakładów w zakresie integracji systemów. Ciągłe monitorowanie stanu daje ogromne korzyści pod względem bezpieczeństwa, dostępności i wydajności wszystkich systemów technicznych oraz maszyn przemysłowych.
Elastyczna i łatwa do zaadaptowania technologia monitorowania zasobów pozwala organizacjom na wdrożenie jednego lub więcej omawianych systemów. Daje to możliwość jednoczesnego monitorowania różnych maszyn i instalacji przemysłowych, a także dobór najlepszych technologii do danych zastosowań. Niskie koszty początkowe związane z wdrożeniem i zgodność z procesami wewnętrznymi otwierają drogę do płynnego wdrożenia systemu po jego implementacji testowej (jako proof-of-concept).
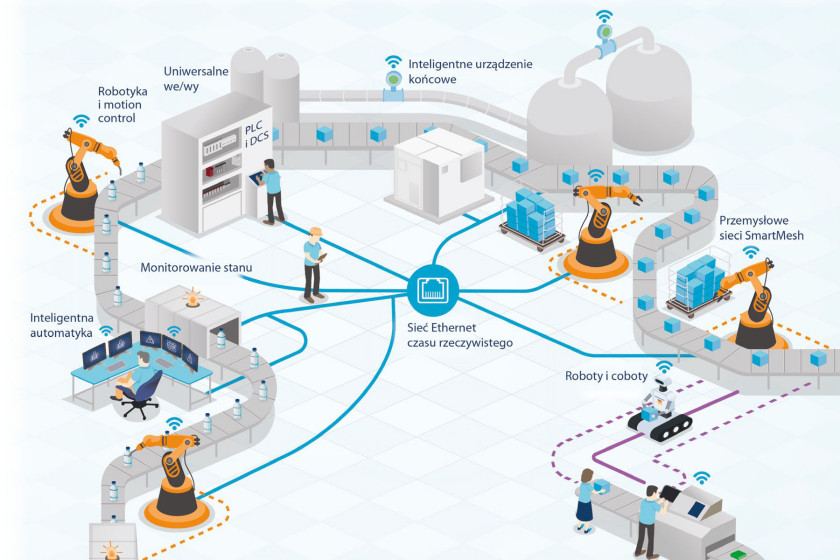
Coraz więcej maszyn i systemów może na bieżąco informować o swoich warunkach pracy, stąd też są one wymieniane dopiero wtedy, gdy są rzeczywiście zużyte – a nie wtedy, gdy przewiduje to stały plan konserwacji. Ich serwisowanie staje się coraz bardziej inteligentnym procesem, który jest wspierany przez oprogramowanie i sztuczną inteligencję. Swoją rolę do odegrania mają tutaj też dostawcy rozwiązań, którzy oferują całościowe platformy sprzętowo-programowe umożliwiające wdrażanie systemów monitorowania i strategii predykcyjnego utrzymania ruchu.
W drugiej części artykułu omówione zostaną szczegóły rozwiązania technicznego z platformą iCOMOX.
www.arrow.com
cbm.gc.pl@arrow.com