Środowisko Industry 4.0 jest w takim przypadku doskonałym rozwiązaniem, które maksymalizuje efektywność i znacznie upraszcza zarządzanie obiektem. Obecnie dysponujemy technologią, która jest dostępna nie tylko dla międzynarodowych gigantów, ale także dla firm z sektora MŚP. Systemy mierników, wspólne protokoły komunikacyjne, urządzenia produkcyjne z dostępem do sieci, SCADA i szereg platform informatycznych – wszystko to umożliwia stworzenie kompletnego środowiska do kontroli i rozwoju strefy produkcyjnej przy jednoczesnym zachowaniu kosztów, które są akceptowalnym wyborem w relacji do osiąganych korzyści.
Jakie są potencjalne korzyści?
Przyjrzyjmy się pokrótce co możemy osiągnąć wybierając jako przykład zakłady produkcyjne ze strefami cleanroom, gdzie kontrola i stabilność parametrów jest szczególnie ważna.
Krótkie przypomnienie: upraszczając cleanroom to strefa w której zapewniamy kontrolę i stabilność parametrów, jak liczbę cząstek, wilgotność, temperaturę i inne parametry – związane np. z antystatyką. Ocena stabilności parametrów odbywa się na podstawie zgodności z wartościami wyznaczonymi w normach i standardach, przede wszystkim ISO 14644 i GMP, ale także VDI, ECSS i szeregu innych. Wszystkie działania w cleanroom służą do prowadzenia wymagającej jakości produkcji lub zawansowanych procesów badawczych, np. w farmacji, elektronice, motoryzacji czy branży spożywczej.
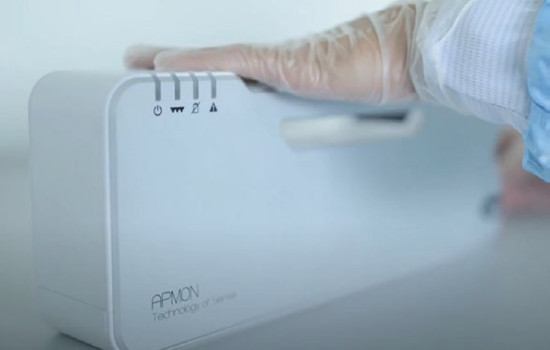
Przykładowo w branży farmaceutycznej lub elektronice wielokrotnie możemy mieć do czynienia z obiektem produkcyjnym, w którym konieczne jest utrzymanie zadanych parametrów z dokładnością ±0,01°C, wilgotnością powietrza ±0,5% i czystością powietrza z kontrolą cząstek o wielkości 0,1 μm. Ponieważ parametry te są wymagane do skutecznego prowadzania produkcji, a wpływ na nie ma funkcjonowanie instalacji budynkowej, jakość prowadzenia procesu, linie produkcyjne, praca a nawet poruszanie się pracowników, to służby utrzymania ruchu i kierownicy produkcji są nieustannie zajęci kontrolą instalacji HVAC, pomiarami czystości powietrza, analizą wpływu poszczególnych czynników na jakość procesów i ciągłymi nastawami parametrów. Oczywiście istotna jest także kontrola kosztów i ich optymalizacja.
Zintegrowane zarządzanie procesem produkcji
W strefie produkcyjnej z cleanroom panować należy nad wieloma parametrami, przy czym są to co najmniej:
- Parametry środowiska przede wszystkim
a) Ilość cząstek w powietrzu
b) Ilość cząstek opadłych na powierzchnie płaskie
c) Zanieczyszczenia mikrobiologiczne
d) Wilgotność
e) Temperatura
f) Ciśnienie - Efektywność urządzeń produkcyjnych i ich wpływ na parametry środowiskowe
- Praca ludzi i wpływ na parametry strefy
Budując zintegrowany system skupimy kontrolowane parametry w jednolitym interfejsie, do którego podłączone są sensory i mierniki, tak aby dostarczyć analiz użytkownikowi, zaś automatyce pozwolić na konieczne reakcje.
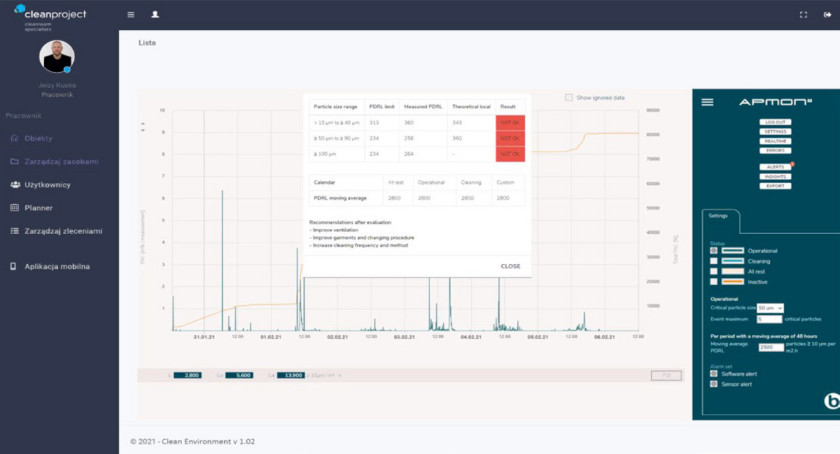
Co zyskuje użytkownik?
Korzystając ze zintegrowanych rozwiązań w ramach Industry 4.0 zarządzanie obiektem produkcyjnym staje się przewidywalnym i skalowalnym procesem. Użytkownik, korzystając z niemal dowolnego urządzenia (komputer, tablet, smartfon) i aplikacji w chmurze ma pełen dostęp do:
- Synoptyki i w praktyce dowolnie skonfigurowanych parametrów, które chce kontrolować
- Historii, trendów, raportów
- Powiadomień i alarmów
- Nastaw systemów
- Harmonogramów serwisowych
- Raportów do przygotowania kwalifikacji, rekwalifikacji, walidacji
- Ewidencji stanu i ilości wyposażenia eksploatacyjnego
Oczywiście dane wykorzystywane są przez systemy automatyki do autoregulacji instalacji na potrzeby zapewnienia jak najbardziej autonomicznego środowiska. Dla przykładu automatyka wykryje uszkodzenie i otwarcie bramy szybkobieżnej, zmieni nastawy w instalacji HVAC, uruchomi tryb alarmu, wyśle powiadomienia do operatorów i służb utrzymania ruchu z koniecznością podjęcia działań serwisowych. Inny przykład: system wykryje ponadnormatywne opadanie cząstek w punkcie montażu aplikacji (np. soczewka kamery), wyświetli alarm dla operatora i kierownika strefy lub nawet zatrzyma proces i zasugeruje działania naprawcze.
Maciej Malinowski
Cleanproject
Zdecydowanie tak. Jako kierownik serwisu doskonale rozumiem służby utrzymania ruchu i kierowników produkcji. Wszyscy chcemy, aby nasza praca przebiegała bez zbędnych utrudnień, przestojów i strat w produkcji. Po zbudowaniu obiektu to właśnie służby techniczne są przede wszystkim odpowiedzialne za jego funkcjonowanie. Nikt nie lubi wieczornych alarmów z systemu HVAC, przekraczania zadanych parametrów, itd. Jeśli cleanroom ma działać bezproblemowo, to automatyka w nim znajdująca się musi być zaprojektowana, wdrożona i obsługiwana bardzo przemyślanie. Dlatego my sami poświęcamy temu dużo uwagi.
Tu również muszę się zgodzić. Przede wszystkim trzeba bardzo dobrze zrozumieć potrzeby klienta i jego procesy. Ponadto nasze systemy najczęściej funkcjonują jako system naczyń połączonych i wymagają zrozumienia całościowego, co oznacza, że nasi inżynierowie naprawdę muszą poznać każdy centymetr kwadratowy zakładu, każdy sterownik, czujnik, a także zasady, na jakich elementy te wpływają na siebie. Oprócz tego komponenty automatyki funkcjonują przecież w specyficznym środowisku – są to urządzenia, które nie mogą pylić, traktowane są agresywną chemią, a dostęp do nich bywa utrudniony. Najczęściej są to też systemy, które muszą reagować bardzo szybko na zmiany i pracują w nietypowych zakresach pomiarowych.
Pandemia jeszcze bardziej przyspieszyła i tak widoczny trend do zdalnego zarządzania budynkami. Choć oczywiście nadal wysyłamy do klientów zespoły serwisowe, szacuję, że obecnie z naszego centrum serwisowego nawet 90% zadań realizujemy zdalnie. Pamiętam zdarzenie, gdy podczas imprezy firmowej z telefonu komórkowego obsłużyłem alarm u jednego z naszych klientów i wraz z kolegami z zespołu w kilkanaście minut zapanowaliśmy nad awarią w obiekcie z rozbudowanym system wentylacyjnym! Świetne jest także to, że automatyzacja pokrywa kolejne obszary związane z działalnością obiektów. Coraz więcej systemów działa niezależnie od użytkowników i jest to coraz bardziej skuteczne funkcjonowanie. Oczywiście to ludzie projektują takie systemy, jednak jako osobę odpowiedzialną za funkcjonowanie wielu obiektów bardzo mnie cieszy to, że rozwój odbywa się w ramach Industry 4.0. |
Możliwości, jakie daje system, wyznaczają głównie potrzeby użytkownika, a nie ograniczenia technologiczne. Użytkownicy najczęściej korzystają z poniższych:
- Operatorzy otrzymują stały monitoring parametrów jak ilości cząstek w powietrzu i na powierzchniach płaskich, wilgotności, temperatury oraz szeregu innych działań związanych z prowadzeniem produkcji.
- Alarmy i powiadomienia informujące o zbliżaniu się do wyznaczonych granic lub ich przekroczeniu. Daje to ogromną przewagę w walce z kontaminacją, gdy przed zanieczyszczeniem produktu użytkownik otrzyma z systemu informację przesłaną poprzez e-mail, SMS oraz sygnalizację w obiekcie o zbliżaniu się do określonej ilości cząstek w wyznaczonych punktach zarówno w powietrzu, jak i na powierzchni. Dzięki temu można zatrzymać proces, skorygować go i uruchomić produkcję bez strat.
- Automatyczne generowanie raportów i dokumentacji do partii wyrobów czy poszczególnych produktów co jest niezwykle przydane w łańcuchach dostaw, kwalifikacji i walidacji, postępowaniach gwarancyjnych czy ogólnie w rozwoju produktu.
- Kontrola urządzeń, nadzorowanie czasu trwania cyklu produkcyjnego, korekty norm ilościowych, wpływ urządzenia na środowisko. Przy czym obecnie możliwy jest także monitoring urządzeń, nie wyposażonych w protokoły komunikacyjne a z wykorzystaniem np. sensorów mierzących ruch i wibrację.
- Wyprzedające działania serwisowe i planowe wymiany elementów eksploatacyjnych, ocena ryzyka awarii przed jego wystąpieniem.
- Pomiary, analiza i optymalizacja zużycia mediów.
- Praca osób w strefie kontrolowana jest od etapu przygotowania się do wejścia do pracy aż po zakończenie pracy – tj. opaski kontrolują ruch między strefami, czujniki w dyspenserach uniemożliwią ominięcie dezynfekcji, monitoring odzieży podaje informacje o właściwościach ESD i ilościach prań, przydzielane są zasoby jak pobrane wyposażenie, analizowane są normy jakościowe i ilościowe, itp.
- System wizualny nie tylko wyświetla parametry systemu i alarmy ale także komunikaty, instrukcje stanowiskowe czy filmy instruktażowe.
Dlaczego jest tak mało wdrożeń?
Przed kilkunastoma czy jeszcze kilkoma laty powszechne stosowanie tych technologii było utrudnione przede wszystkim z uwagi na wysokie koszty wdrożenia, ale również z powodu braku standardów komunikacyjnych umożliwiających współpracę urządzeń. Dziś koszty wdrożeń znacznie spadły, a standardy komunikacyjne są na tyle upowszechnione, że do BMS można podłączyć niemal każde urządzenia z ekspresem do kawy włącznie.
Dlaczego więc szczególnie w sektorze MŚP kompleksowych wdrożeń jest nadal niewiele? Przyczyny znajdujemy przede wszystkim w dwóch ograniczeniach:
- W nowych inwestycjach utrudnieniem jest specyfika procesu budowlanego, w którym uczestniczy kilka podmiotów inwestor-użytkownik-deweloper-podwykonawcy. Interesy tych grup nie zawsze są zbieżne, a zakres zadań przy projektowaniu, wykonaniu i oddaniu obiektu do użytkowania tak szeroki, że finalnie bardzo często wybierane są rozwiązania klasyczne, znane od dziesięcioleci.
- Drugi powód jest jeszcze bardziej prozaiczny – bardzo niewielka ilość firm, które są w stanie doradzić inwestorowi i użytkownikowi, rozumieć procesy produkcyjne, prowadzić dialog z użytkownikiem, następnie opracować projekt instalacji, mieć dostęp do systemów i wiedzę o nich, wdrożyć rozwiązanie, prowadzić serwis, opracowywać raporty i rozwijać system.
Podsumowanie
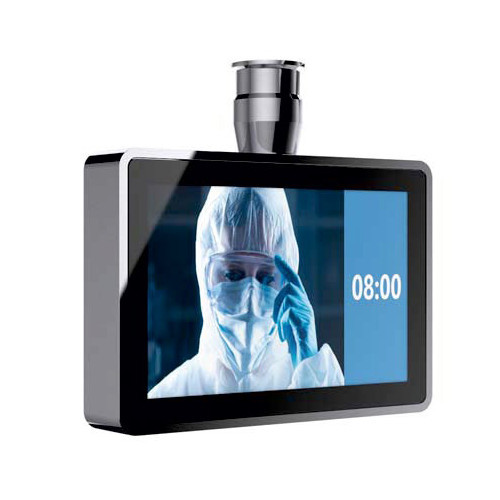
Niewielka liczba wdrożeń jest wynikiem braku czasu, wiedzy i chęci do skorzystania z nowoczesnych technologii. Wypada jednak zachęcać do zapoznawania się z powyżej zarysowanymi rozwiązaniami. Zapewne w najbliższych latach staną się one coraz bardziej widoczne również w małych oraz średnich firmach, przyczyniając się do ich rozwoju. Nie warto pozostawać w tyle wyścigu – tym bardziej, że na rynku są już dostępne rozsądnie skonfigurowane rozwiązania dla dużych podmiotów, ale także właśnie małych i średniej wielkości przedsiębiorstw. Przykładem na takie rozwiązania może być "Clean Environment" firmy Cleanproject.
Jerzy Kustra
www.cleanproject.pl
Więcej na www.cleanproject.pl