Czynników nieprzyjaznych jest wiele. Mają też różny charakter. Niektóre z nich mają charakter "zwykłych wielkości fizycznych", aczkolwiek aby oddziaływać destrukcyjnie, muszą mieć ekstremalną wartość – przykładem są: skrajnie wysokie albo ekstremalnie niskie temperatury i ciśnienie. Inne to substancje, jak woda, woda morska, chemikalia i pyły, niektóre zaś wynikają z formy złożonych procesów – taki jest korozja. Jest to proces postępującego niszczenia materiałów, zwłaszcza metali, w następstwie ich reakcji z otoczeniem. Rozwija się w obecności cieczy albo gazów, w dowolnej temperaturze, choć na ogół szybciej w wyższej. Jej postępowi sprzyja również obecność zanieczyszczeń.
Woda, korozja i zapylenie
Jakie są typy korozji? Gdzie stanowi problem?
Wyróżnia się kilka rodzajów korozji. Pojawia się na powierzchni równomiernie albo miejscowo (korozja wżerowa, korozja szczelinowa). Galwaniczna występuje, jeżeli dwa albo więcej metali styka się ze sobą w obecności elektrolitu. Mikrokrystaliczna rozwija się na granicach ziaren metalu w wyniku niewłaściwej obróbki cieplnej, na przykład spawania, a wysokotemperaturowa na skutek reakcji z otoczeniem w podwyższonej temperaturze – przykładem jest pogorszenie się właściwości mechanicznych metali, które wystawiono na działanie m.in. amoniaku, azotu, fluoru, tlenku węgla, metanu, chloru. Najpowszechniej występuje korozja atmosferyczna – przykład to rdza na żelazie. Może mieć charakter chemiczny albo elektrochemiczny.
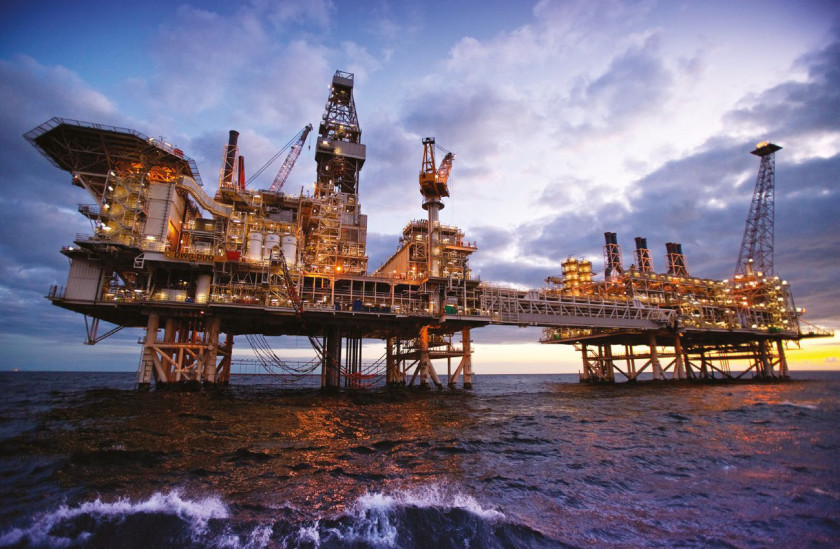
Korozja to problem w branży morskiej, w jednostkach pływających i elektrowniach wiatrowych. Elementy ich konstrukcji i wyposażenia mają kontakt z wilgotnym i silnie zasolonym powietrzem, na które narażona jest część statku niezanurzona w morzu i jego wnętrze (maszynownia, ładownia, kabiny), a w przypadku elektrowni – turbina, i ze słoną wodą morską, z którą stykają się podwodna część kadłuba statków i wieże wiatraków. Korodują również części maszyn budowlanych, do prac leśnych, sprzętu górniczego. Choć korozji nie można całkiem wyeliminować, można ją ograniczyć. Jeżeli mimo wszystko rozwija się, oznacza to, że zastosowane środki nie są wystarczające lub dany sprzęt nie nadaje się do użytku w tych konkretnych warunkach.
Jak zapobiegać korozji?
Kluczowe znaczenie ma dobór odpowiednich materiałów. Odporna na korozję jest m.in. stal nierdzewna. Zawdzięcza ona tę właściwość zawartości chromu (minimum 10%), który tworzy na powierzchni samonaprawiającą się warstwę tlenku. Występuje w różnych odmianach. Przykładem jest stal nierdzewna 316, wyróżniająca się wyjątkową odpornością na korozję ze względu na większą zawartość niklu oraz dodatek molibdenu. Jest to dzięki temu popularny materiał wykonania obudów urządzeń elektrycznych wykorzystywanych w środowisku morskim. Ten typ stali sprawdza się szczególnie w ich korpusach, natomiast nie jest polecany jako materiał wykonania elementów takich jak nakrętki, śruby, złącza. W zamian lepiej jest wykorzystać stal nierdzewną 304, ze względu na jej wyższą wytrzymałość i odporność na zużycie, częściowo z powodu nieco wyższej zawartości chromu, i niższy koszt.
Kolejne materiały to stopy miedzi. Wyróżnia je dobre przewodnictwo cieplne i elektryczne, dobre właściwości mechaniczne, łatwość obróbki. Chociaż reagują z pewnymi kwasami, generalnie w powietrzu, wodzie, słonej wodzie, w obecności wielu organicznych i nieorganicznych chemikaliów charakteryzuje je duża odporność na korozję. Nikiel oraz jego stopy są z kolei odporne na roztwory żrące. Inny przykład to aluminium oraz jego stopy, m.in. 5052, który poza odpornością na korozję wyróżnia wytrzymałość zmęczeniowa i łatwość spawania.
Kolejną ważną kwestią jest kompatybilność metali – powinno się unikać tych ich zestawień, w których może wystąpić korozja galwaniczna. Przykład to połączenie miedzi i stali nierdzewnej. Metale zabezpiecza się również, pokrywając je powłokami ochronnymi. Wytwarza się je m.in. w procesie cynkowania i miedziowania. Przed korozją zabezpiecza też malowanie proszkowe oraz powłoki ceramiczne.
Złącza hermetyczneNewralgicznym elementem obudów są złącza. Jeżeli będą użytkowane w warunkach, w których czynniki środowiskowe mogą przez nie przenikać do wnętrza urządzenia, żeby do tego nie dopuścić, trzeba korzystać z modeli z uszczelnieniem. W tym zakresie można wybrać jedno z dwóch rozwiązań, w zależności od wymagań. Są to złącza: wodoodporne i pyłoszczelne lub złącza hermetyczne. Wodoodporność oraz pyłoszczelność zapewniają uszczelnienia z tworzyw sztucznych. W złączach hermetycznych z kolei izolację kontaktów wykonuje się ze szkła, ceramiki lub żywicy. Są one zaprojektowane tak, by wytrzymywały wysokie ciśnienie. Gazoszczelność wymagana jest zwykle w zastosowaniach specjalnych, na przykład w wojsku, lotnictwie i zadaniach realizowanych na dużych głębokościach, na przykład w eksploracji dna morskiego. Dużą popularnością cieszy się zwłaszcza pierwszy z wymienionych materiałów. Wśród zalet złączy hermetycznych z uszczelnieniem ze szkła wymienić należy: trwałość, wytrzymałość mechaniczną oraz wysoką temperaturę pracy. Proces uzyskiwania gazoszczelności polega na topieniu szkła w piecu do czasu, aż wypełni ono przestrzeń między kontaktami i obudową wkładki, a pomiędzy szkłem i metalem wytworzą się trwałe wiązania. Wówczas temperatura jest obniżana, aż do schłodzenia wkładów. Aby zapewnić szeroki zakres temperatur pracy, szkło i metal powinny charakteryzować się zbliżonymi współczynnikami rozszerzalności termicznej. Zapobiega to powstawaniu niekontrolowanych naprężeń i przesunięć komponentów wkładki przy zmianach temperatury. |
Zalanie i zapylenie
Niekorzystny jest nie tylko kontakt zewnętrznych powierzchni obudów urządzeń z czynnikami korozyjnymi, ale również ich przenikanie do wnętrza – przykładowo woda morska i zwykła powodują zwarcia. Podobnie negatywnie wpływają zjawiska atmosferyczne, jak deszcz oraz śnieg, chemikalia (smary, rozpuszczalniki, sól drogowa), środki myjące. Na kontakt z nimi narażone jest: wyposażenie statków, morskich elektrowni wiatrowych, jak i m.in. panele operatorskie w sprzęcie pracującym w terenie, na przykład w maszynach górniczych, maszynach budowlanych (koparki), pojazdach komunalnych (śmieciarki, odśnieżarki), pojazdach ratowniczych (wozy strażackie). Szafy elektryczne i obudowy z kolei często pracują w pomieszczeniach o dużym zapyleniu, na przykład w produkcji żywności i kopalniach. Drobiny pyłu, które przenikną do ich wnętrza, również są źródłem wielu problemów (zwarcia, zatykanie wentylacji powodujące przegrzewanie).
Odporność na płyny i pyły uzyskuje się przez wybór odpowiedniego materiału obudowy, materiału i typu jej uszczelnień oraz konstrukcję złączy. Poziom ochrony zapewnionej w ten sposób opisuje się stopniem IP. Kod IP składa się z dwóch cyfr. Pierwsza, z przedziału od 0 do 6, opisuje poziom zabezpieczenia przed wnikaniem do wnętrza urządzenia ciał stałych, druga, w zakresie od 0 do 9, wody. Przykładowo obudowa o stopniu ochrony IP58 ma zagwarantowaną pyłoodporność oraz szczelność przy zanurzeniu ciągłym, IP56 pyłoodporność i szczelność przy zalaniu falą wody (zalecaną na przykład w przypadku obudów wyposażenia jednostek pływających), zaś IP67 pyłoszczelność i szczelność przy zanurzeniu czasowym.
Uszczelki chronią przed płynami i pyłem
Obudowy można zabezpieczyć przed wnikaniem ciał obcych m.in. uszczelkami: w postaci pasków, wyciętymi w kształcie obrysu złączanych elementów lub wylewanymi w formie pianki na podłoże zabezpieczone przed korozją, która następnie zastyga. Pierwsze są zazwyczaj tanie, ale niestety na złączach, w rogach, szybko niszczeją. Problem ten nie dotyczy uszczelek wylewanych – ich zaletą jest bowiem ciągłość na całym obwodzie oraz bardzo dobra przyczepność do podłoża. Są również tanie. Uszczelki wycinane są z kolei zwykle nieco droższe.
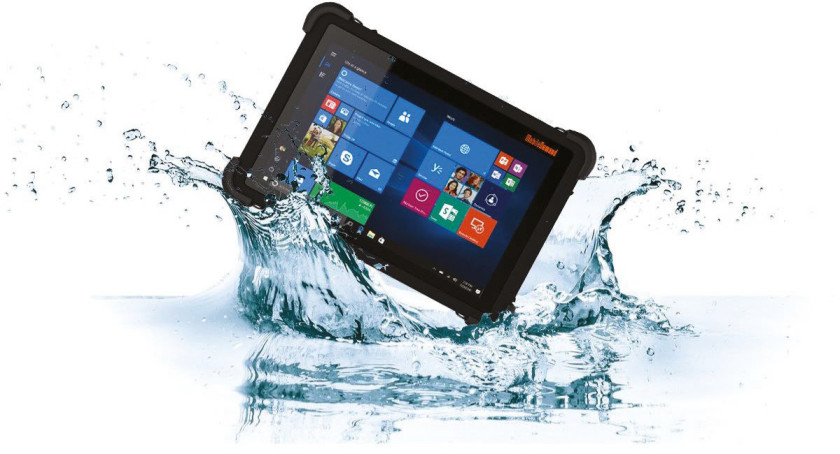
Materiał uszczelki powinien być odporny na te same czynniki zewnętrzne, co obudowa. Wykonuje się je najczęściej z TPE, czyli elastomerów (kauczuków) termoplastycznych, PUR (poliuretanu), EPDM (terpolimeru etylenowo-propylenowo-dienowego) o dużej wytrzymałości na rozciąganie, neoprenu oraz silikonu. Najczęściej używanym materiałem jest neopren. Zaletą poliuretanów jest natomiast łatwość wytwarzania uszczelek o nieregularnych kształtach. Za silikonem przemawia z kolei odporność na promienie słoneczne i szeroki zakres temperatur pracy (od –60°C do +170°C). Jest niestety droższy niż pozostałe materiały.