Prawie dziesięć lat temu niemieckie Federalne Ministerstwo Edukacji i Badań stworzyło termin opisujący transformację, która obecnie rozprzestrzenia się w przemyśle wytwórczym - Industrie 4.0 - obecnie częściej tłumaczone na angielski odpowiednik Industry 4.0. Zwrot ten, nazywany czasem czwartą rewolucją przemysłową, opisuje kolejny krok w kierunku zmian w technologii automatyzacji produkcji.
Podobnie jak trzecia rewolucja przemysłowa, Przemysł 4.0 obraca się wokół wykorzystania robotyki i sprzętu komputerowego. Wyróżnia się jednak zwiększonym skupieniem się na łączenie systemów ze sobą i pełne wykorzystanie danych gromadzonych przez każdy zautomatyzowany podsystem. Nacisk na komunikację jest powodem, dla którego Przemysł 4.0 jest ściśle powiązany z koncepcją przemysłowego Internetu rzeczy (IoT). Dzięki możliwości analizy danych, komunikacji i kontroli w czasie rzeczywistym roboty i narzędzia maszynowe stają się „systemami cyberfizycznymi”, które mogą znacznie inteligentniej reagować na zmiany warunków.
Skupienie się na aspektach technologii informacyjnej (IT) sterowania przemysłowego nie oznacza, że Przemysł 4.0 opiera się na całkowitej automatyzacji. Wiele operacji produkcyjnych wymaga interakcji człowieka. W przeciwieństwie do przeszłości, kiedy roboty były instalowane w klatkach bezpieczeństwa, z dala od pracowników hali produkcyjnej, trend zmierza w kierunku wykorzystania „cobotów”: robotów i narzędzi współpracujących bezpośrednio z ludźmi. Ma to na celu ułatwienie przejścia do znacznie bardziej elastycznej operacji, w której komórki produkcyjne mogą szybko i wydajnie zmieniać operacje. Ta możliwość ponownego kierowania pozwala komórkom reagować na nagłe zmiany zapotrzebowania, aby w razie potrzeby obsługiwać różne produkty i warianty. To z kolei napędza potrzebę, że komórki muszą reagować na znacznie bogatszy zestaw strumieni danych i odpowiednio planować.
Do tej pory obrabiarki i roboty były w dużej mierze projektowane tak, aby reagowały na własne okoliczności, wykorzystując wbudowane czujniki do wykrywania naruszenia tolerancji lub w niektórych przypadkach do monitorowania ich własnego stanu za pomocą analizy, na przykład wibracji. Oczekuje się, że zdolność samokontroli zostanie w nadchodzących latach szerzej wykorzystywana, aby zapobiegać nieprzewidzianym awariom i usprawniać czynności konserwacyjne.
W scenariuszu Industry 4.0 narzędzia mogą reagować na dane generowane przez sąsiednie jednostki lub zewnętrzne dane wejściowe, co pozwoli im szybko radzić sobie ze zmieniającymi się warunkami. Procesy mogą dostosowywać czasy ogrzewania i suszenia do zmieniającej się zawartości wilgoci w materiałach lub wilgotności otoczenia. Zmniejszenie wahań spowodowanych zmieniającymi się warunkami oznacza, że jakość produkcji poprawi się, a także zapewni możliwość oszczędzania energii w sprzyjających warunkach.
Produkty niektórych dostawców zapewniają nowatorskie możliwości dla określonych typów maszyn. Na przykład Motion Terminal VTEM od Festo jest pierwszym zaworem, który ma możliwość uruchamiania aplikacji dostosowujących działanie do różnych sytuacji. Kontrola jakości jest kluczowym elementem programowalnych narzędzi sprzęgających HS-Technik od Panasonic. Wbudowane czujniki rejestrują i oceniają wartości momentu dokręcania i kąta, które mają kluczowe znaczenie dla kontroli jakości w sytuacjach o wysokiej przepustowości.
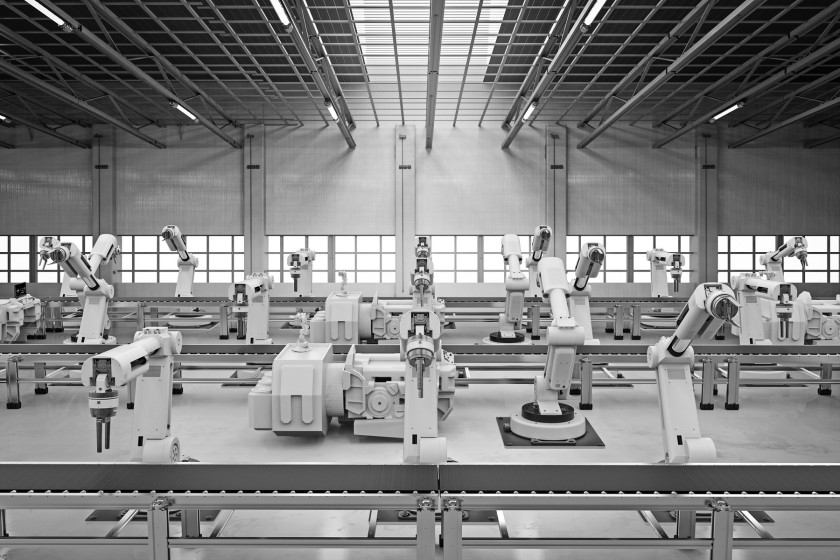
Trend # 1 - symulacja i cyfrowe bliźniaki
Nacisk na wykorzystanie narzędzi i robotów do produkcji oprzyrządowania dostarcza obszernych danych do operacji produkcyjnych, które można wykorzystać do informowania o wyborach projektowych i pomocy w zarządzaniu całym cyklem życia produktu. Analitycy z GlobalData widzą, że koncepcja cyfrowego bliźniaka zyskuje na popularności. Dzięki obsłudze cyfrowej reprezentacji każdego fizycznego produktu, który jest wysyłany, który przechowuje większość danych z czujnika uzyskanych podczas produkcji i przez cały okres użytkowania, cyfrowy bliźniak znacznie ułatwia ocenę skuteczności fizycznego produktu. Kluczem do koncepcji cyfrowego bliźniaka jest technologia symulacji. Zamiast polegać wyłącznie na wzorcach danych z czujników, symulacja cyfrowego bliźniaka z wykorzystaniem zarejestrowanych informacji może pokazać potencjalne, wcześniej ukryte problemy, które nie tylko pomagają w utrzymaniu istniejących części, ale także informują o projektowaniu następczych produktów.
Adrian Lloyd z Interact Analysis zauważa, że symulacja cyfrowego bliźniaka pomaga nie tylko w produktach, ale także w liniach używanych do ich wytwarzania Przykładem był start-up motoryzacyjny VinFast. We współpracy z Siemensem producent samochodów wykorzystał symulację układów hali produkcyjnej, aby poprawić przepustowość i produktywność przed zainstalowaniem narzędzi, zapewniając ogromne oszczędności w porównaniu z tradycyjnymi metodami stosowanymi przy uruchamianiu takich linii produkcyjnych.
Schneider Electric odnosi się do idei wykorzystania symulacji do rozwoju linii produkcyjnych, jako „inżynierii zerowej”, rozszerzając koncepcję na programowanie poszczególnych elementów wyposażenia sterującego. Zamiast ograniczać możliwości produkcyjne na potrzeby programowania i testowania, można teraz eksperymentować i konfigurować sterowniki Modicon i AVEVA w domenie wirtualnej. Techniki cyfrowego bliźniaka łączą modele wirtualne z systemami fizycznymi. Kiedy zmiana jest potrzebna, programowanie po prostu przenosi się z jednego do drugiego.
Według ABB podejście do wirtualnego uruchamiania skraca ogólny czas projektowania o 20 procent, zmniejsza nakłady kapitałowe o 25 procent i skraca czas szkolenia o połowę. Aby wesprzeć to podejście, ABB dostarcza rozwiązanie do wirtualnego uruchamiania, Ability, które nie tylko obsługuje konfigurację w domenie cyfrowej, ale oferuje interfejsy rzeczywistości wirtualnej, aby wspierać efektywne i terminowe szkolenie operatorów.
Trend #2 – Inteligentne czujniki są wszędzie
Zastosowanie czujników będzie szeroko rozpowszechnione w fabryce i poza nią. Dostawcy tacy jak Omega i Omron zapewniają szeroki wachlarz modalności czujników, które wykorzystują między innymi techniki indukcyjne, światłowodowe, magnetyczne, ciśnieniowe i techniki triangulacji laserowej wśród wielu innych. Dzięki zapotrzebowaniu na dokładne pomiary, grupa analityków Mordor Intelligence przewiduje, że globalny rynek czujników Internetu rzeczy (IoT) będzie rósł w złożonym rocznym tempie nieco ponad 24 procent od 2020 do 2025 roku. Według badania firmy Ericsson, z 28 miliardów wszystkich urządzeń podłączonych do Internetu do 2021 roku, prawie 16 miliardów stanowić będą urządzenia IoT, a produkcja będzie stanowić znaczną część całości.
W dzisiejszym środowisku typowym modelem wykorzystania danych z czujników jest przesyłanie większości z nich do chmury. W miarę rozprzestrzeniania się czujników staje się to coraz trudniejsze do wsparcia. Przetwarzanie lokalne będzie potrzebne do analizowania danych i uzyskiwania wglądu w dowolne miejsce przed przesłaniem skondensowanego formularza zawierającego tylko istotne zmiany stanu na serwery w chmurze w celu dalszej dogłębnej analizy. Wysokowydajny, niedrogi sprzęt do obliczeń brzegowych ma kluczowe znaczenie dla osiągnięcia tego celu i jest dostępny od wiodących dostawców w różnych formach.
Omron wprowadził funkcjonalność sztucznej inteligencji AI do swojej platformy sterowania Symaec, podczas gdy Opto22 zapewnia wysokowydajne obliczenia do sterowania w czasie rzeczywistym blisko hali produkcyjnej dzięki rodzinie modułów Groov.
Trend # 3 - Bezpieczeństwo, nawet w heterogenicznym środowisku
Wraz ze wzrostem możliwości przetwarzania brzegowego i podłączonych modułów czujników, bezpieczeństwo staje się kluczową kwestią dla wdrażających. Wszechobecna łączność wynikająca z IIoT zapewnia hakerom wiele celów ataku. Obecność wielu standardów komunikacyjnych na hali produkcyjnej zwiększa ogólną złożoność zapewniania ochrony.
Aby zwalczyć ryzyko włamania, wdrażający muszą zwrócić szczególną uwagę na ryzyko i mechanizmy przeciwdziałania atakom. Częścią rozwiązania jest wykorzystanie doświadczeń ze świata IT w operacyjnym środowisku technologicznym. W przestrzeni IT powszechne jest obecnie szyfrowanie danych nie tylko podczas transmisji, ale także w spoczynku, a także zapewnienie, że cały kod uruchamiany w sieci jest podpisany przez zatwierdzonego dostawcę. Ponadto producenci muszą upewnić się, że mogą aktualizować oprogramowanie i oprogramowanie układowe w przypadku znalezienia luk w zabezpieczeniach. Dostawcy tacy jak Schneider Electric opracowali strategie pomagające producentom w zapewnieniu bezpieczeństwa i zapewniające klientom architekturę, która radzi sobie z problemami. Jednak inni dostawcy wdrażają mechanizmy ochrony w swoich produktach, aby zapewnić producentom możliwość tworzenia własnych bezpiecznych architektur.
Łącząc to wszystko razem
Podsumowując, sterowanie i automatyzacja przemysłowa rozwijają się szybko na wielu frontach, ponieważ producenci zaczynają wykorzystywać elastyczność i możliwości, jakie niosą ze sobą technologie Przemysłu 4.0. Chociaż bezpieczeństwo i inne kwestie niosą ze sobą wyzwania, ulepszenia technologii sprawią, że produkcja będzie bardziej wydajna i skuteczniejsza w zaspokajaniu potrzeb klientów. Dokonując ostrożnych wyborów pod względem stosowanej przez nich technologii i wykorzystując skalowalne platformy, organizacje mogą ułatwić to przejście. Tego typu decyzje nie muszą być trudne, wystarczy zwrócić się do globalnych dystrybutorów, takich jak Farnell, którzy mogą zapewnić dostęp do wiodącego na rynku portfolio produktów, silnej sieci dostawców, niezawodnej usługi dystrybucji i wsparcia technicznego w celu wyposażenia firmy każdej wielkości i wykorzystania technologii automatyki przemysłowej.
Cliff Ortmeyer
Globalny Dyrektor ds. Marketingu Technicznego
Farnell
Źródło: Farnell