Co się kryje za "4.0"?
Pierwszy raz nazwa "Industry 4.0" w odniesieniu do przemysłu, została użyta w 2011 roku na targach w Hanowerze, w kontekście promowania cyfryzacji w fabrykach. Zabieg ten miał na celu pobudzenie wzrostu technologicznego w przemyśle, w którym dotychczas znaczącą rolę odgrywały firmy niemieckie.
Złośliwi mogą twierdzić, że chodziło głównie wzmocnienie niemieckiej gospodarki poprzez eksport technologii, ale faktem jest, że systemy komputerowe każdego roku deklasują rozwiązania stosowane kilka lat wstecz i wygląda na to, że rozwój w tej dziedzinie wcale nie zwalnia, a wręcz przeciwnie każdego roku nabiera coraz większego rozpędu.
Przykładem jest poniższy graf ze skalą logarytmiczną, przedstawiający zwiększanie możliwości obliczeniowych superkomputerów przez ostatnie lata – liczba operacji FLOPS (floating-point operations per second, liczba operacji zmiennoprzecinkowych na sekundę).
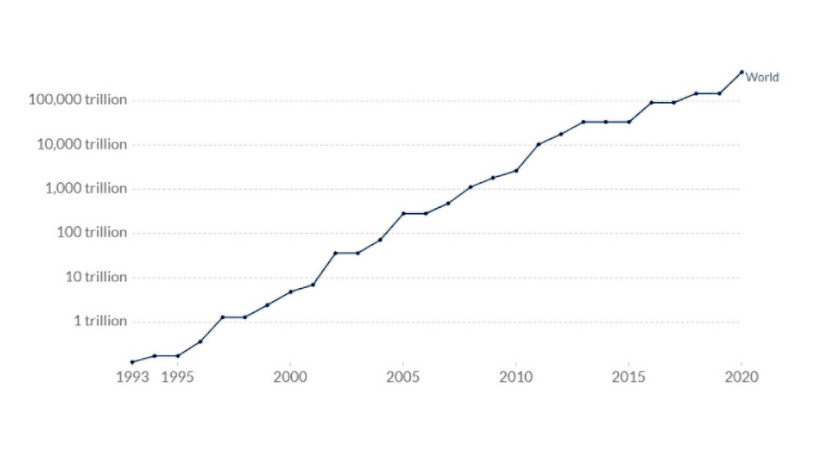
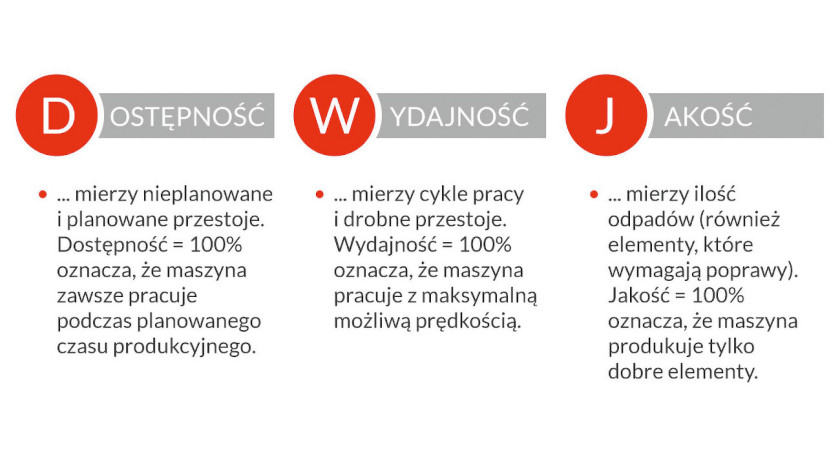
Polepszenie wskaźników jakości w przemyśle
W przemyśle chodzi o ciągłe doskonalenie. W wielu firmach oceną wydajnej pracy maszyn jest wskaźnik OEE (Overall Equipment Effectiveness, oacena efektywności wykorzystania maszyny), który określa, jak efektywnie korzysta się z maszyny i wyznaczany jest według poniższego wzoru:
Dostępność * wydajność * jakość = OEE
Np. dla dostępności = 92%, wydajności = 80% i jakości = 90%, OEE wynosi 66%
APA Group przez lata zdobywała doświadczenia w realizowaniu projektów w automatyce przemysłowej. Poprzez bliski kontakt z firmami produkcyjnymi zaobserwowaliśmy pojawiającą się potrzebę cyfryzacji na szeroką skalę.
Ktoś mógłby powiedzieć, że przecież przemysł jest zautomatyzowany i sterowniki PLC są na każdym kroku. Owszem, niemniej najczęściej ma się do czynienia z różnymi systemami, które albo wymieniają szczątkowe informacje między sobą, albo taka wymiana informacji nie istnieje.
Wszystkie firmy produkujące otwarcie przyznają, że dla nich ciągłe polepszanie wskaźnika OEE jest sprawą kluczową. Producenci są mocno ukierunkowani na ciągłe doskonalenie (np. korzystające ze wskaźnika OEE) i twierdzą, że coraz trudniej jest im ograniczać koszty funkcjonowania.
"Klasyczne metody poprawiania wskaźnika OEE przestają wystarczać, co więcej dalsze doskonalenie tradycyjnymi metodami staje się zbyt kosztowne" – mówi kierownik utrzymania ruchu w firmie z branży automotive.
Klęska urodzaju
Mnogość systemów oraz sterowników PLC, SCADA w jednej fabryce może przyprawić o ból głowy. Jeśli miał ktoś okazję przejść się po fabryce, to mógł zaobserwować setki mrugających lampek, wyświetlaczy, czujników wyświetlających parametry, czyli w skrócie – potężne ilości informacji, które coś oznaczają, mogą być istotne albo nie.
Ogarnąć ich nie sposób, nawet jeśli te wszystkie one są zapisane gdzieś na komputerze w bazie danych.
Często firmy informują, że po awarii, podczas analizy zapisanych danych w bazie lub urządzeniu, okazywało się, że rzeczywiście przed samą awarią napęd o oznaczeniu M34.1 (oznaczenie urządzenia przypadkowe) wykazywał symptomy właściwe dla maszyny, której żywotność się kończy.
Wyzwaniem w tym momencie jest określenie źródła problemu (czy usterka dotyczy układu chłodzenia, przekładni, wału, sprzęgła, a może jeszcze czegoś innego). Odpowiedzią na to pytanie może być stosowanie inteligentnych czujników, które mają w sobie już przetworzone informacje (np. diagnostyka drganiowa) lub korzystanie z uczenia maszynowego, które na podstawie danych pochodzących z tradycyjnych źródeł (temperatura, ciśnienie, prędkość itd.) jest w stanie określić obszar wymagający uwagi.
"Jeśli zredukujemy problem do danych, maszyna deklasuje człowieka" – wskazuje Jacek Kucharczyk, kierownik projektu, APA Group.
Niewidoczne zmiany w Przemyśle 4.0
Na podstawie rozmów z automatykami na temat Industry 4.0 można zauważyć, że przez te wszystkie lata niewiele się w przemyśle zmieniło.
W dalszym ciągu sterowniki PLC sterują, wizualizacje pokazują stan, tutaj coś świeci, a tam brzęczy, czasem podnosi się alarm i wtedy robi się bardziej gorąco, ale potem wszystko wraca do normy i dalej jest tak samo.
Przypuszczalnie w niedalekiej przyszłości dalej wszystko będzie wyglądać podobnie albo tak samo jak jest teraz natomiast najwięcej ciekawych rzeczy odbywać się będzie w ciszy, na dyskach komputerowych, a ingerencja człowieka ograniczy się tylko do utrzymywania procesu produkcji i dokonywania napraw na podstawie faktycznego stanu maszyn.
Transformacja w kierunku Przemysłu 4.0 - od czego zacząć?
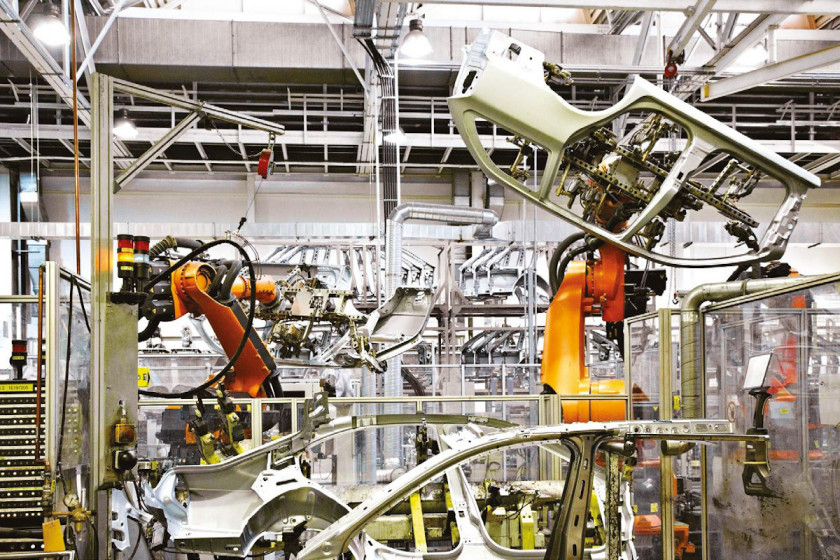
Firma APA Group uruchomiła program NAZCA 4.0, którego celem jest pomoc przedsiębiorstwom w transformacji w kierunku Przemysłu 4.0. Oparty jest on m.in. na przeprowadzaniu warsztatu celem określenia potrzeb danej firmy oraz ocenienie, w jakim punkcie dana firma się znajduje.
Dzięki takiemu podejściu możliwe jest zdefiniowanie następnych kroków: określenie, co można zastosować z już istniejącej infrastruktury, oraz co należy dołączyć i w jaki sposób. Kolejnym etapem będzie przeanalizowanie tego, w jaki sposób informacje z maszyn mają wpływać na procesy firmy. Są to raczej czynności, które należy wprowadzać stopniowo.
Marek Maciejewski, menadżer projektów Industry 4.0 w APA Group
www.apagroup.pl