W centrach dystrybucyjnych Avon wykorzystuje się automatyczne systemy sortowania, które pomagają w szybkim przemieszczaniu towarów z magazynów na linie wysyłkowe.
Technologie te:
- przyspieszają realizację zamówień i dostaw do klientów;
- zwiększają dokładność kompletacji zamówień, redukując liczbę błędów;
- umożliwiają obsługę większej liczby zamówień przy mniejszym zaangażowaniu pracowników.
Automatyzacja paletyzacji niesie wiele korzyści dla procesu przygotowania towaru na paletach. Jeśli dodamy do tego zaawansowaną technikę miksowania na określoną liczbę kierunków, otrzymamy optymalizację procesu w centrum dystrybucyjnym, która pozwala na bardziej elastyczną i efektywną niż dotąd obsługę zamówień. Dlatego Avon zdecydował się na dalsze inwestycje w tej dziedzinie, a firma ASTOR
dostarczyła system paletyzacji EtE®flow z miksowaniem na dwanaście kierunków.
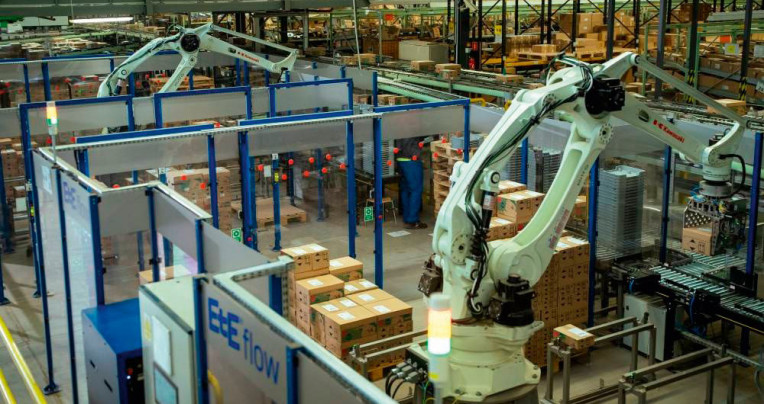
Jak działa system
Już na etapie koncepcji przygotowane zostały symulacje wydajnościowe oraz symulator algorytmu układania palety. Dzięki tym symulacjom przed przystąpieniem do projektu istniała pewność, że system spełni oczekiwania jakościowe klienta oraz zapewni zapas wydajności na rozwój produkcji oraz sprzedaży.
System, który ostatecznie stworzono, składa się z dwóch bliźniaczych stanowisk do paletyzacji kartonów na sześć kierunków każdy, składających się z:
- robota Kawasaki Robotics CP180L,
- specjalnie zaprojektowanego chwytaka klapowego,
- przenośników rolkowych do transportu kartonów i tacek,
- pozycjonerów palet,
- buforów odkładczych na kartony połówkowe,
- stakera tacek.
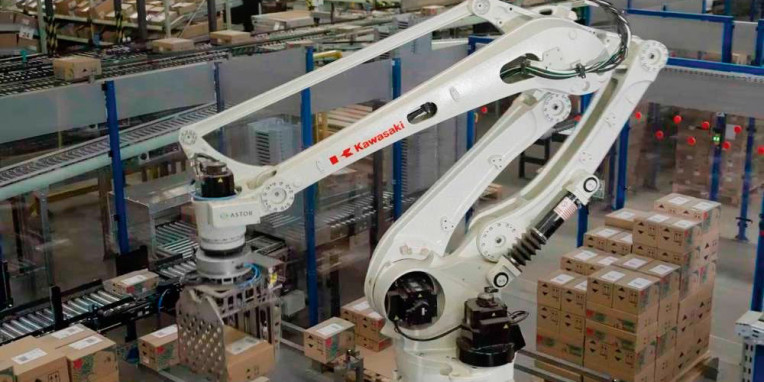
Do sterowania procesem wykorzystywane są dwa sterowniki PLC Astraada One Compact. Pierwszy z nich steruje pracą całego stanowiska: robotem oraz podajnikami i transporterami rolkowymi. Drugi jest przeznaczony do sterowania stakerem tacek.
W ramach jednego stanowiska paletyzacji robot pobiera karton za pomocą chwytaka klapowego oraz kładzie go na palecie odpowiadającej danemu kierunkowi wysyłkowemu. Wyjątkiem są tzw. kartony połówkowe, które przed odłożeniem na paletę robot kompletuje w pary. Używa do tego tzw. bufora odkładczego, umieszczonego bezpośrednio przed każdym gniazdem paletyzacji.
W warstwie logicznej system sterowania stanowiska komunikuje się z bazą danych klienta, z której uzyskuje informację o kierunku wysyłkowym danego kartonu. Dodatkowo, system korzysta ze specjalnego algorytmu układania kartonów. Na jego podstawie robot podejmuje decyzję, na które pole w ramach danej palety ma odłożyć dany karton. Kartony pojawiają się w sposób losowy, a zatem robot buduje paletę w taki sposób, aby była możliwość odłożenia każdego możliwego rodzaju kartonu, zachowując przy tym stabilność palety. Ta zostaje ukończona po osiągnięciu wagowego lub wysokościowego warunku ukończenia palety.
Stanowiska wyposażone są dodatkowo w skanery kodów kreskowych oraz bramki pomiarowe, których zadaniem jest pomiar wysokości kartonów i odrzut tych niespełniających parametrów jakościowych.
Staker odpowiada za budowanie stosów plastikowych tacek, na których dostarczane są niektóre typy kartonów. Tacki są układane w stosy, które po ułożeniu transportuje się za pomocą przenośnika rolkowego na zewnątrz stanowiska. Za stakerem przewidziane są trzy miejsca buforowe do magazynowania stosów tacek. Kartony typu „error” (nieczytelny kod, pomiar wysokości poza tolerancją, nieprawidłowy kierunek) są odkładane przez robota na przenośnik, który transportuje je poza stanowisko.
Do komunikacji sterownika z kontrolerem robota Kawasaki oraz ze sterownikami transporterów rolkowych wykorzystywany jest protokół Ethernet/IP. Algorytm oraz program sterujący stanowi autorskie rozwiązanie opracowane przez producenta rozwiązania, firmę ASTOR.
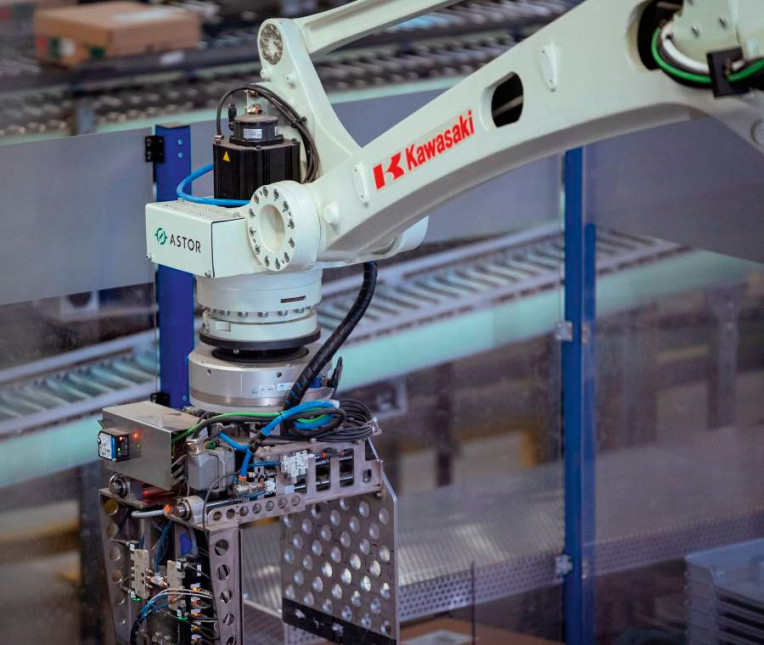
Uzupełnieniem całego systemu jest panel HMI Astraada PC Terminal, który wyświetla aplikację wizualizacyjną, uruchomioną bezpośrednio w sterowniku Astraada One. Dzięki temu operatorzy mają dostęp do interfejsu pozwalającego nadzorować i konfigurować cały system.
Stanowiska paletyzacji są wyposażone są w system bezpieczeństwa. Jego pierwszym elementem jest CUBIC-S, czyli dodatkowy kontroler safety Kawasaki Robotics, nadzorujący w czasie rzeczywistym ruchy robota. CUBIC-S nie daje robotowi możliwości osiągnięcia pozycji, która znajduje się poza wygrodzeniami stanowiska. Tym samym gwarantuje bezpieczeństwo obsługi systemu przez operatorów.
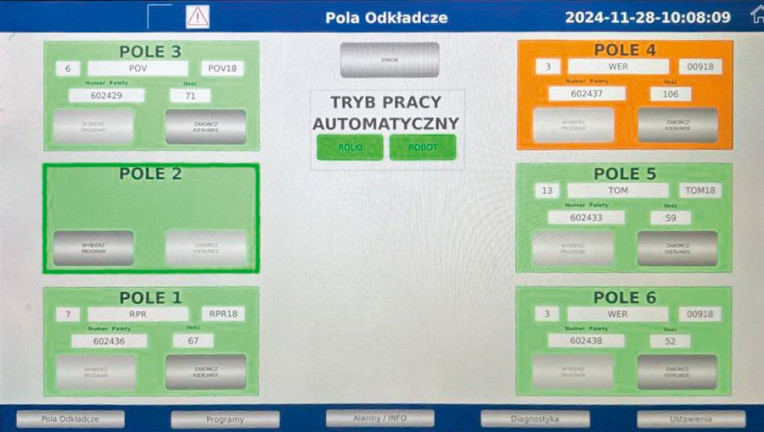
Stanowiska są wyposażone dodatkowo w elektromagnetyczne rygle bezpieczeństwa zamontowane przy wejściach oraz przyciski bezpieczeństwa umieszczone wewnątrz oraz na zewnątrz stanowiska. Naciśnięcie przycisku bezpieczeństwa lub wtargniecie do stanowiska skutkuje natychmiastowym zatrzymaniem awaryjnym robota. Procesy wymiany palety oraz rozpoczęcia pracy są opisane sekwencją startową (zresetowanie stanowiska wewnątrz oraz na zewnątrz), która dodatkowo podwyższa bezpieczeństwo układu.
Każde ze stanowisk wyposażono w osobny system sterowania i bezpieczeństwa oraz oprogramowanie pozwalające na ergonomiczną obsługę funkcjonalności. Tym samym oba stworzone stanowiska są całkowicie niezależne, dzięki czemu przestój jednego z nich, spowodowany wymianą palety lub serwisem, nie wpływa na pracę drugiego.
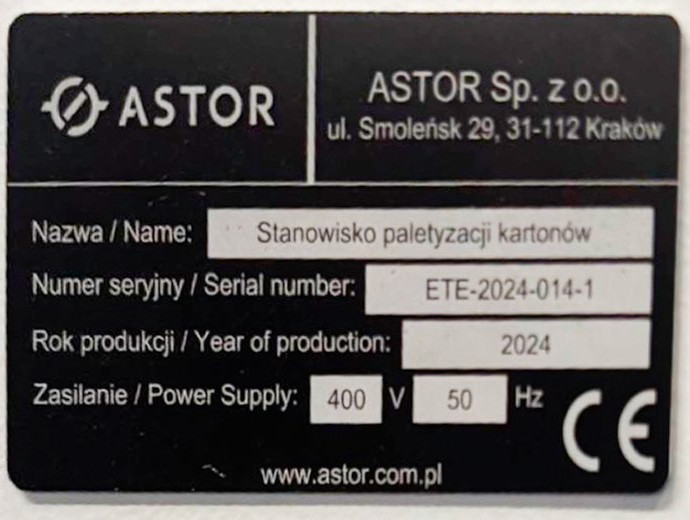
Kinga Tarsa, Mateusz
Pijanowski (współautor)
ASTOR
www.astor.com.pl