BEZKONTAKTOWY, RÓŻNICOWY POMIAR WIELKOŚCI GEOMETRYCZNYCH
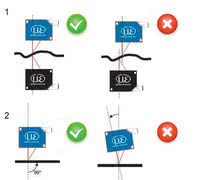
Rys. 1. Prawidłowa instalacja czujników laserowych
W omawianej metodzie wykorzystuje się dwa czujniki laserowe (lub ich wielokrotność) - liczba zależy od punktów, w których chcemy dokonywać kontroli danej wielkości. Sensory powinny być ustawione naprzeciw siebie, tak aby ich wiązki laserowe znajdowały się w jednej osi i były skierowane do środka pola pomiarowego. Rysunek 1 przedstawia prawidłową instalację czujników laserowych.
Do realizacji pomiarów, oprócz samych czujników laserowych, niezbędny jest odpowiedni kontroler. Umożliwi on wykonywanie prostych obliczeń arytmetycznych, które mają na celu wyznaczenie danej wielkości geometrycznej - np. szerokości, jak na rysunku 2. Algorytmy obliczeń kontrolera zostały zestawione w kolejnych wzorach.
X1 = Kanał_1 * Mnożnik_1 + SMR_1
X2 = Kanał_2 * Mnożnik_2 + SMR_2
X1 i X2 to odległość między czujnikiem (odpowiednio pierwszym i drugim) od badanego detalu (wielkość podawana w mm); Kanał_1 i Kanał_2 to wartości sygnałów analogowych czujników; Mnożnik_1 i Mnożnik_2 to stałe parametry wynikające z zakresów pomiarowych czujnika pierwszego i drugiego; SMR_1 i SMR_2 to strefy martwe czujników (parametr podawany jest zawsze przez producenta czujników w dokumentacji technicznej).
Do precyzyjnych pomiarów szerokości lub wysokości metodą różnicową niezbędna jest odpowiednia kalibracja systemu pomiarowego. Taką funkcję powinien posiadać kontroler wykorzystany w tym układzie pomiarowym. Kontroler ten umożliwia również wykonywanie wszystkich niezbędnych obliczeń arytmetycznych, mających na celu wyznaczenie dawnej wielkości.
METODY KALIBRACJI
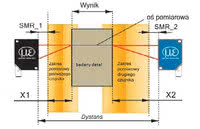
Rys. 2. Zasada różnicowego pomiaru szerokości detalu
Kalibrację systemu pomiarowego, który ma realizować pomiar różnicowy, można wykonać na dwa sposoby.
Sposób 1 - w kontrolerze systemu musimy ustawić stałą odległość między zainstalowanymi czujnikami laserowymi (odległość ta, na potrzeby kolejnych wzorów, została określona jako Dystans)
Sposób 2 - gdy nieznana jest odległość między czujnikami. W takim przypadku musimy dysponować detalem wzorcowym o znanych wymiarach (wymiar szerokości detalu został określony jako Wzorzec). Detal ten należy ustawić w polu pomiarowym systemu i zmierzyć odległość poszczególnych czujników od jego ścian (czyli określić parametry X1 oraz X2). Dzięki temu kontroler, korzystając z kolejnego wzoru, będzie mógł wyznaczyć odległość między czujnikami. Dystans = X1 + wzorzec + X2.
Po wykonaniu kalibracji układu pomiarowego kontroler będzie potrafił wyznaczyć daną wielkość geometryczną (określoną jako Wynik), korzystając ze wzoru: wynik = dystans - X1 - X2.
SYSTEM DO RÓŻNICOWEGO POMIARU WIELKOŚCI GEOMETRYCZNYCH
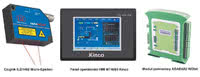
Rys. 3. Elementy systemu pomiarowego
Firma WObit posiada w swojej ofercie gotowe rozwiązanie do bezkontaktowego pomiaru szerokości lub wysokości. System ten składa się z dwóch czujników laserowych firmy Micro-Epsilon, z serii ILD1402, modułu pomiarowego produkcji WObit - ADAE42U oraz panelu HMI firmy Kinco. Produkty te zostały przedstawione na rysunku 3. ILD1402 to ekonomiczna seria czujników, wykorzystująca triangulację laserową.
Czujniki tej serii dostępne są z zakresami 5, 10, 20, 50, 100, 200, 250 lub 600mm (zależy od modelu). Charakteryzują się bardzo dobrymi parametrami pomiarów - liniowość: maks. 9μm, rozdzielczość: maks. 0,6μm, prędkość pomiaru: 1,5kHz (konfigurowalne). Informacje o zmierzonej odległości otrzymujemy w postaci sygnału analogowego (4…20mA lub 1…5V) oraz cyfrowego (RS-422). Drugi element układu to moduł pomiarowy ADAE42-U firmy WObit, z czterokanałowym wejściem analogowym (0..10V, 0..20mA lub 4..20mA) oraz dwoma wejściami cyfrowymi dla enkoderów inkrementalnych.
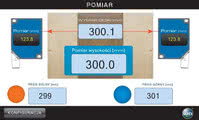
Rys. 4. Okno panelu HMI systemu pomiarowego
Moduł posiada funkcję uśredniania wyników pomiarów oraz niezbędne w wielu aplikacjach funkcje matematyczne, które umożliwiają działanie na wartościach mierzonych z kanałów analogowych i cyfrowych. Z urządzeniem tym można komunikować się przy wykorzystaniu interfejsu USB oraz RS-485 (MODBUS RTU). Dodatkowo razem z modułem dostarczane jest darmowe oprogramowanie na komputer PC, które umożliwia konfigurację systemu oraz rejestrację pomiarów do pliku.
Ostatnim elementem systemu pomiarowego jest panel operatorski HMI serii MT4404T firmy Kinco, wyposażony w wyświetlacz TFT 7" o rozdzielczości 800×480. Panel posiada interfejsy USB (do programowania z poziomu komputera PC przy wykorzystaniu darmowego oprogramowania), RS-232 oraz RS-485.
PRZYKŁADOWA APLIKACJA Z SYSTEMEM WOBIT
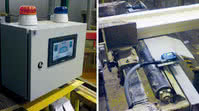
Rys. 5. Pomiar wysokości belki dwuteownika
Omawiany system pomiarowy znalazł już zastosowanie w branży drzewnej, przy pomiarze wysokości belki dwuteownika. Tego typu problem aplikacyjny pojawił się w jednej z wiodących firm z przemysłu drzewnego w Polsce. Rozwiązano go dzięki wykorzystaniu czujników z serii ILD1402 o zakresie pomiarowym 200mm połączonych z modułem pomiarowym ADAE42-U oraz z panelem HMI. Moduł ADAE42, pełniąc funkcję kontrolera, umożliwia ciągły pomiar oraz kontrolę wysokości produkowanej belki.
Wyniki pomiarów są na bieżąco wyświetlane na panelu HMI, który obsługuje operator maszyny. Dodatkowo kontroler sygnalizuje przekroczenie progów tolerancji wysokości belki. Jest możliwe dzięki wbudowanym, programowalnym wyjściom cyfrowym, do których podłączono indykatory. Niezbędna konfiguracja systemu odbywa się również przy wykorzystaniu panelu HMI, na którym udostępniono odpowiednie funkcje.
Na rysunku 4 zostało przedstawione główne okno panelu, gdzie wyświetlane są wyniki pomiarów, informacje o zmierzonych przez czujniki odległościach oraz zaprogramowanych progach tolerancji. Rysunek 5 przedstawia natomiast zdjęcia wykonane na obiekcie, gdzie widać zainstalowane czujniki laserowe oraz skrzynkę instalacyjną z wbudowanym panelem operatorskim.