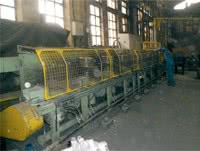
Fot. 1. Linia do przewijania drutu
Zadaniem linii do przeciągania drutu jest zmniejszenie średnicy drutu do średnicy zadanej w wyniku przeciągnięcia go przez serię rolek. Średnica jest zmniejszana stopniowo, po każdym zmniejszeniu drut nawijany jest na bęben. W skład maszyny wchodzi osiem bębnów. Pierwszy bęben obraca się z najmniejszą prędkością. Każdy kolejny bęben obraca się z prędkością odpowiednio większą. Każdy bęben wyposażony jest w sterowanie lokalne zawierające przyciski Zwolnij, Przyspiesz oraz pedały nożne: prędkość JOG i zwolnienie hamulca bębna.
Modernizacja była konieczna, ponieważ istniejący układ sterowania nie zapewniał oczekiwanych przez klienta wymagań produkcyjnych oraz stwarzał zagrożenie dla obsługi. W ramach modernizacji wymieniono całkowicie układ sterowania linii, silniki napędzające bębny do nawijania drutu, dodano układ bezpieczeństwa. Niezmieniona pozostała mechanika linii.
WYBÓR ELEMENTÓW I METODY STEROWANIA
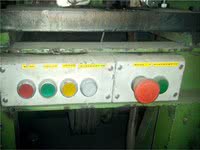
Fot. 2. Pojedynczy bęben
Nowe sterowanie linii miało zapewniać dwa tryby sterowania: zaciąganie, czyli pierwsze nawijanie drutu na bębny, oraz pracę normalną z drutem już nawiniętym na bębny. Do sterowania prędkością obrotową każdego bębna wykorzystano falowniki SV150iG5A-4 - 8 sztuk wraz z filtrami FFG5A-T051-3 (footprint) - 8 sztuk, po jednym na każdy bęben. Automatyczne sterowanie linii realizowane jest przez sterownik XBC-DR64H wraz z dodatkowymi kartami wejść, wyjść cyfrowych oraz kart wyjść analogowych. Interfejs użytkownika zrealizowany jest przez panel dotykowy XP-10BKB.
W ramach modernizacji konieczne było dodanie wyłącznika MCR126.IT odpowiedzialnego za realizację układu bezpieczeństwa linii. Dodatkowo dodano układ przepięciowy firmy Weidmüller. Wymieniono szafę sterowniczą na nową wraz z wszystkimi aparatami. Rozprowadzenie zasilania wykonano na moście szynowym. Dodano nowe elementy takie jak CKF, przekaźniki do załączania hamulców bębnów Aniro MPI-001-U240-116, chłodzenie obce MMS-32H 1,6A ze stycznikiem GMD-6M 24VDC 1,2W E - osiem sztuk zamontowanych na moście szynowym. Przeprowadzenie testów funkcjonalnych linii do przeciągania drutu potwierdziło poprawność wybranych elementów.
REALIZACJA APLIKACJI
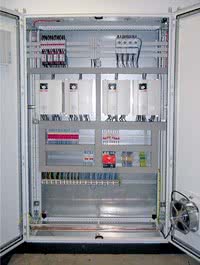
Fot. 3. Jedna sekcja szafy sterowniczej zawierająca falownik dla 4 bębnów
Poprawna praca linii wymagała wykorzystania obu trybów sterowania, każdorazowo po zainstalowaniu nowego bębna z drutem. W pierwszej kolejności wykonywano zaciąganie, czyli pierwsze nawijanie drutu na bębny. Nawijanie dokonywane jest przez panel nożny zainstalowany przy każdym bębnie. W trakcie zaciągania obraca się tylko jeden bęben naraz. Operator naciskając pedał nożny JOG obraca bęben z małą prędkością.
Po nawinięciu drutu na jeden bęben operację powtarza się dla kolejnych bębnów. Po nawinięciu wszystkich bębnów możliwe jest uruchomienie normalnej pracy linii. Po wciśnięciu przycisku Start rusza pierwszy bęben, z opóźnieniem rusza każdy kolejny. Po wciśnięciu przycisku Stop następuje zatrzymanie pracy - wszystkie bębny hamują jednocześnie. Każdy bęben wyposażony jest w hamulec zapobiegający samoczynnemu odwijaniu się drutu w trakcie postoju linii.
W ramach modernizacji dodano układ bezpieczeństwa realizujący zatrzymanie pracy linii. W skład układu bezpieczeństwa wchodzi przekaźnik bezpieczeństwa, przyciski zatrzymania awaryjnego, osłony bębnów zamontowane na linii oraz czujniki zerwania drutu. Wszystkie bębny na linii zasłonięte są czterema osłonami.
Praca linii jest możliwa tylko w przypadku, gdy zamknięte są wszystkie osłony. Otworzenie którejkolwiek osłony powoduje natychmiastowe zatrzymanie pracy maszyny. Zerwanie przewijanego drutu detektowane jest przez specjalne czujniki wykrywające ten stan. W momencie uszkodzenia przewijanego drutu, zerwany drut dotyka specjalnej metalowej płytki. W wyniku dotyku wystawiany jest sygnał uszkodzenia drutu i praca maszyny zostaje natychmiastowo przerwana.
Na ostatnim bębnie zainstalowany został czujnik indukcyjny, który przy każdym obrocie bębna daje sygnał do sterownika. Zliczanie liczby obrotów ostatniego bębna umożliwia określenie długości przewiniętego drutu. Pozwala to na automatyczne zatrzymanie linii po przewinięciu określonej przez operatora długości drutu, w wyniku czego możliwe jest uzyskiwanie dowolnej, zadanej przez operatora ilości przewiniętego drutu, w szczególności uzyskiwanie tej samej powtarzalnej ilości drutu w produkcji seryjnej.
Sterownik PLC wraz z dodanymi kartami wejść/wyjść spełnia kilka zadań. Podstawowym jego zadaniem jest zapewnienie pracy automatycznej linii w obu wymaganych przez klienta trybach. Kolejnym zadaniem sterownika jest kontrola falowników sterujących bębnami. Sterownik wystawia sygnały sterujące do falowników: Start, Stop, prędkość nadrzędna JOG, przyspiesz/zwolnij prędkość obrotową bębna, sygnał resetu. Sterownik PLC analizuje również sygnały wyjściowe z falowników, takie jak sygnał awarii. Odpowiada on także za kontrolę zabezpieczeń i układu bezpieczeństwa. Sterownik analizuje sygnały od elementów bezpieczeństwa takich jak czujniki osłony bębnów oraz zerwania drutu, odpowiednio wysterowując linie.
Do zadań sterownika należy również analiza wszystkich sygnałów przychodzących z czujników, przycisków, pedałów, itp. i wymuszenie prawidłowego działania linii do przeciągania drutu. Zapewnia on też komunikację z panelem dotykowym HMI, który umożliwia operatorowi obsługę pracy linii i wybór jednego z dwóch trybów pracy.
Za pomocą panelu operator ma możliwość ustawienia długości przewiniętego drutu, po której nastąpi automatyczne zatrzymanie pracy. Wyłączenie tej funkcji powoduje ciągłą pracę linii, aż do naciśnięcia przycisku Stop. Dzięki HMI operator ma również możliwość sprawdzenia wszystkich parametrów pracy linii: sygnały o zadziałaniu hamulców, sygnały o awarii falowników, statusy sygnałów z pedałów nożnych.
Falowniki odpowiedzialne są za sterowanie prędkością obrotową bębnów. Pracują one w trybie sterowania U/f z forsowaniem momentu. Prędkość obrotowa zadawana jest przez sterownik PLC na dwa sposoby. W trybie pracy normalnej prędkość zadawana jest przez wejście analogowe 4...20 mA. W trybie zaciągania prędkość jest zadawana poprzez wejście cyfrowe JOG. Po wciśnięciu pedału nożnego następuje wywołanie prędkości przypisanej parametrem w falowniku do wejścia cyfrowego JOG.
TESTY OBIEKTOWE
Po zakończeniu modernizacji wykonano testy funkcjonowania linii do przewijania drutu, które wykazały poprawność aplikacji. Spełnione zostały założenia projektowe dotyczące wydajności oraz dokładności pracy linii.
PODSUMOWANIE
Opisana aplikacja została wykonana w oparciu o produkty koreańskiej firmy LSIS. Przeprowadzone testy obiektowe wykazały poprawność przyjętego układu sterowania. Na podstawie opisanego układu sterowania dokonano również modernizacji linii do przewijania drutu - układu 9-cio ciągu.
Obecnie linia do przewijania drutu działa bezawaryjnie od ponad roku. Klient jest zainteresowany modernizacją kolejnych maszyn w oparciu o system sterowania opisany w artykule.
Aniro Grupa Handlowa
www.aniro.pl