CEL PROJEKTU
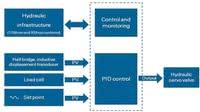
Rys. 1. Schemat blokowy systemu sterowania
Firma DOLSAT Consult, która założona została w 2005 roku, jest dystrybutorem sprzętu i oprogramowania National Instruments specjalizującym się w opracowywaniu rozwiązań pomiarowych i kontrolnych dla wielu branż przemysłowych.
Instytut Teoretycznych i Eksperymentalnych Analiz Struktur Aeronautycznych (STRAERO), z siedzibą w Bukareszcie, zlecił firmie wymianę swojego przestarzałego sterownika PID firmy Schenck (fot. 2), który steruje dwiema maszynami wytrzymałościowymi Schenck Hydroplus (fot. 1) oraz sześcioma serwozaworami hydraulicznymi. Instytut chciał mieć możliwość wykonywania bardziej złożonych i miarodajnych testów w sposób bardziej przyjazny użytkownikowi.
Jako dostawca usług badawczych i rozwojowych z zakresu lotnictwa, STRAERO oferuje specyficzne testy struktur mechanicznych - wytrzymałościowe oraz naprężeń granicznych, w tym testy granicznych naprężeń rozciągających i ściskających, zmęczeniowe, sprężystości, a także udarności przy obciążeniu do 60 ton.
![]() Fot. 1. System kontrolno-pomiarowy |
![]() Fot. 2. Urządzenie Schenck Hydroplus |
Hydrauliczny system kontroli położenia firmy Schenck przez ostatnie 20 lat swojej pracy był rozwiązaniem niezawodnym i został w tym czasie wzbogacony między innymi o generator przebiegów Rigol o wysokiej dokładności i stabilności oraz system akwizycji danych MGCplus firmy HBM. Jednak ograniczenia regulatora PID, w połączeniu ze złożonością integracji nowych ulepszeń sprzętowych z punktu widzenia oprogramowania, stały się kłopotliwe - nawet przy przeprowadzaniu prostych testów.
ROZWIĄZANIE
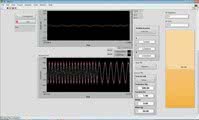
Rys. 2. Testowanie płaskiej metalowej sztaby z wykorzystaniem sinusoidalnego przebiegu siły o amplitudzie ±5 KN (na biało: wyniki pomiaru, na czerwono: zadany przebieg)
Potrzebny był nowy system automatyzacji (rys. 1) pozwalający na implementację ośmiu regulatorów PID do sterowania serwozaworami hydraulicznymi oraz siłownikami maszyny Hydroplus. Miał on także zastąpić stary, bazujący na przekaźnikach system kontrolno-pomiarowy infrastruktury hydraulicznej.
Rozważaliśmy rozwiązania firmy Moog i Parker Hannifin, ale ostatecznie zdecydowaliśmy się na użycie kompletnej platformy sprzętowej NI PXI (fot. 3) z powodu ścisłej integracji sprzętu z oprogramowaniem, jak również oferowanej elastyczności i skalowalności.
WYKONANY SYSTEM
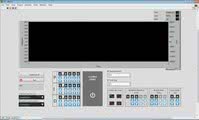
Rys. 3. Podstawowy interfejs użytkownika
W maszynach Hydroplus wykorzystywane są transformatorowe czujniki przemieszczeń nieliniowych firmy HBM z serii W. Aby zachować kompatybilność, użyliśmy modułu kondycjonowania sygnałów HBM Clip AE501 z wyjściem ±10 V. W celu obejścia ograniczeń nałożonych przez wykorzystanie przetworników analogowo-cyfrowych typu delta-sigma do jednopunktowej, próbkowanej sprzętowo akwizycji danych, zastosowaliśmy wzmacniacz pomiarowy HBM-AE101, również z wyjściem ±10 V. Do zebrania sygnałów ze wspomnianych wyżej modułów HBM użyliśmy ośmiu różnicowych wejść analogowych wielofunkcyjnej karty NI PXI-6220 serii M, która okazała się bardziej niż odpowiednia do tego zadania.
Do sterowania serwozaworem użyliśmy wzmacniacza Pees Components AN405 ze standardowym wejściem ±10 V, które ma możliwość dostarczenia prądu o natężeniu ±100 mA. Mimo że system operuje w warunkach zakłóceń elektrycznych, dzięki użyciu izolowanego modułu wyjść analogowych NI PXIe-4322 mogliśmy sterować opisanym wyżej wzmacniaczem bez typowych problemów napięć wspólnych.
Miało to kluczowe znaczenie przy projektowaniu niezawodnej i deterministycznej aplikacji sterującej. Do zbierania 24-woltowych sygnałów logicznych pochodzących z jednostki firmy Schenk monitorującej hydraulikę, takich jak informacja o przekroczeniu dopuszczalnej wartości temperatury oleju, spadku jego ciśnienia, czy działaniu ogrzewania, użyliśmy izolowanego modułu wejść cyfrowych NI PXI-6511. Do sterowania pompami spustowymi i sygnałami bezpieczeństwa użyliśmy przekaźników statycznych ABB z interfejsem typu R600, kontrolowanych przez izolowany moduł wyjść cyfrowych NI PXI-6513.
OPROGRAMOWANIE
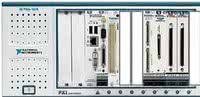
Fot. 3. Wybrany system PXI
Zdecydowaliśmy się na użycie kompletnej platformy sprzętowej NI PXI wykorzystującej system czasu rzeczywistego LabVIEW Real-Time z powodu ścisłej integracji sprzętu z oprogramowaniem, jak również oferowanej elastyczności i skalowalności. Praca nad oprogramowaniem systemu już od samego początku była prostym zadaniem. Przykładowe projekty zawarte w module NI LabVIEW Real-Time oraz rozbudowana dokumentacja pomogły nam szybko stworzyć prototyp w pełni funkcjonalnej aplikacji (rys. 2).
Część pracująca pod kontrolą systemu czasu rzeczywistego składa się z czterech równoległych pętli. Jednej odpowiedzialnej za próbkowaną sprzętowo akwizycję danych i kolejnych, zajmujących się komunikacją z komputerem PC, logowaniem danych oraz monitorowaniem stanu całego systemu. Komunikacja pomiędzy aplikacją czasu rzeczywistego i komputerem PC (rys. 3) została zaimplementowana z wykorzystaniem strumieni sieciowych - zarówno do przesyłania danych pomiarowych, jak i pojedynczych wiadomości.
WNIOSKI
Używając platformy sprzętowej i programowej NI oraz dzięki wsparciu zespołu National Instruments stworzyliśmy skalowalne i niezawodne rozwiązanie modernizujące 20-letni, sprawdzony w przemyśle system Schenck Hydroplus.
Tom Savu, Daniel Cazacu
DOLSAT Consult
dolsat.com