Najczęstszym problemem w systemach sprężonego powietrza są spadki ciśnienia w instalacji jego dystrybucji, z powodu których występuje różnica w ciśnieniu tego medium na wyjściu sprężarki w stosunku do ciśnienia na wejściu zasilanego nim odbiornika. Objawami tego są na przykład awarie maszyn, zbyt mała siła wytwarzana w cylindrach pneumatycznych w stosunku do tej wymaganej w danej aplikacji albo niewystarczający moment obrotowy narzędzi pneumatycznych.
Chociaż pewien spadek wartości tej wielkości jest nieunikniony, w prawidłowo funkcjonującym systemie nie powinien on przekraczać 10%. Inaczej próba skompensowania większej straty przez zwiększanie ciśnienia na wyjściu sprężarki spowoduje wzrost kosztów operacyjnych, a poza tym z czasem wpłynie też na skrócenie jej żywotności na skutek jej ciągłego przeciążania wywoływanego przez sztucznie generowane zapotrzebowanie.
Dlatego zamiast doraźnego, niwelującego tylko objawy, takie jak przestoje maszyn, a przez to w dłuższej perspektywie wysoce nieefektywnego rozwiązania, lepiej jest od razu zidentyfikować przyczynę. To pozwoli na wyeliminowanie stratnych punktów w obrębie sieci przesyłu tego medium.
Co jest przyczyną spadku ciśnienia w instalacji?
Jedną z trzech głównych przyczyn spadku ciśnienia w systemie dystrybucji sprężonego powietrza jest duża odległość między kompresorem a odbiornikami. W takim przypadku nawet gdy wszystkie części instalacji pośredniczące w transporcie tego medium są dobrze zwymiarowane i są w dobrym stanie, wielostopniowe połączenia wnoszą pewne straty. Dlatego zawsze warto jest ograniczać ich liczbę, skracając dystans kompresor–odbiorniki do niezbędnego minimum.
Drugą przyczyną strat ciśnienia w systemach sprężonego powietrza są jego wycieki. Dochodzi do nich w różnych miejscach instalacji. Te najbardziej newralgiczne to: złącza, które się poluzowały i przewody, którymi powietrze jest prowadzone. Do wycieków dochodzi wzdłuż węży i rurociągów, jak też w miejscach ich połączeń, a są one tym bardziej prawdopodobne, im większa jest odległość między sprężarką a odbiornikiem. Potencjalnymi stratnymi punktami są także takie komponenty systemu dystrybucji powietrza, jak rozdzielacze (trójniki), kolanka i elementy instalacji, które spełniają dodatkowe funkcje, jak filtry, regulatory, zawory czy dysze.
Wycieki
Szacuje się, że przeciętnie nawet 30% sprężonego powietrza może wyciekać. Poza tym, że spowodowane tym spadki ciśnienia zmniejszają wydajność sprzętu zasilanego tym medium, znacząco pogarszają również sprawność energetyczną instalacji jego produkcji. Dlatego nie powinno się ich ignorować, mimo że są trudne do wykrycia, a w związku z tym, że sprzęt się nieuchronnie starzeje, nawet w razie wyeliminowania ich w jednym miejscu, można się wkrótce spodziewać pojawienia się ich w innym. Chociaż zatem wycieków nie da się całkiem wykluczyć, warto je przynajmniej ograniczać.
W zakresie ich detekcji wyróżnia się kilka metod, nowszych, jak i tych o dłuższej historii. Do tych drugich można zaliczyć lokalizowanie wycieków dzięki temu, że można je usłyszeć. Z reguły jednak oznacza to, że ubytek sprężonego medium musi już być znaczny. W przeciwnym razie na co dzień w zakładach przemysłowych, gdzie poziom hałasu jest wysoki, a od pracowników wymaga się noszenia ochronników słuchu, nie są one słyszalne, o ile inspekcja nie jest przeprowadzana w czasie przestoju.
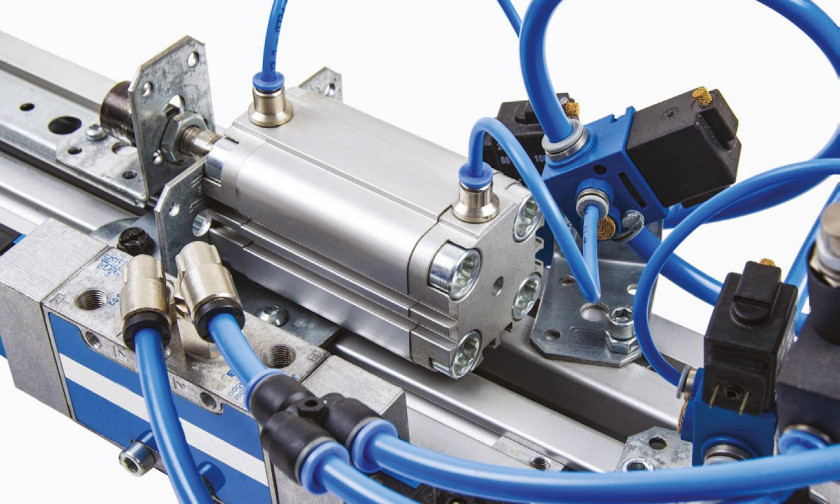
Jak wykryć wycieki?
Do kategorii metod praktykowanych coraz rzadziej należy również zaliczyć technikę, w której punkty podejrzewane o występowanie wycieków są spryskiwane wodą z mydłem. Jeśli do ubytku medium rzeczywiście tam dochodzi, pojawiają się bąbelki powietrza. Metoda ta jest pracochłonna i czasochłonna, niedokładna, a poza tym pogarsza bezpieczeństwo na stanowiskach pracy, ponieważ rozlewanie mydlin zwiększa poślizg posadzki.
Nowocześniejszą metodą jest wykorzystywanie mierników ultradźwiękowych. W tym przypadku wykorzystuje się fakt, że wyciekom sprężonego powietrza towarzyszy emisja ultradźwięków. Ich źródłem są zaburzenia w przepływie gazu, normalnie bowiem jest on laminarny, zaś jeśli w rurze występuje nieszczelność, wokół niej zmienia się on w przepływ turbulentny. Sygnał ten jest w detektorze ultradźwięków wykrywany i wzmacniany. Najnowsza generacja mierników ultradźwiękowych wykorzystywanych w detekcji wycieków sprężonego powietrza (i nie tylko) umożliwia też zobrazowanie rejestrowanych sygnałów na wyświetlaczu. Ich rozkład, po nałożeniu na obraz obszaru poddawanego inspekcji, ułatwia zlokalizowanie miejsca ubytku. Znacznie ułatwia i przyspiesza to wykrywanie wycieków.
Blokady przepływu
Trzecią z głównych przyczyn spadku ciśnienia w systemach dystrybucji sprężonego powietrza są wszelkie fizyczne przeszkody w kanałach transportowych. Ich obecność powoduje zablokowanie przepływu medium. Jeżeli wstrzymują go całkowicie, przeważnie na skutek spowodowanego tym nadmiernego wzrostu ciśnienia w instalacji, aktywują się zabezpieczenia, które wyłączają sprężarkę. Do spadku ciśnienia dochodzi natomiast zwykle przy częściowym zablokowaniu kanału, wówczas bowiem przed przeszkodą ciśnienie wzrasta, a za nią spada. Przyczyną tego mogą okazać się na przykład wszelkie elementy, które zmniejszają średnicę rurociągów, jak: mocowania, zawory, czujniki.
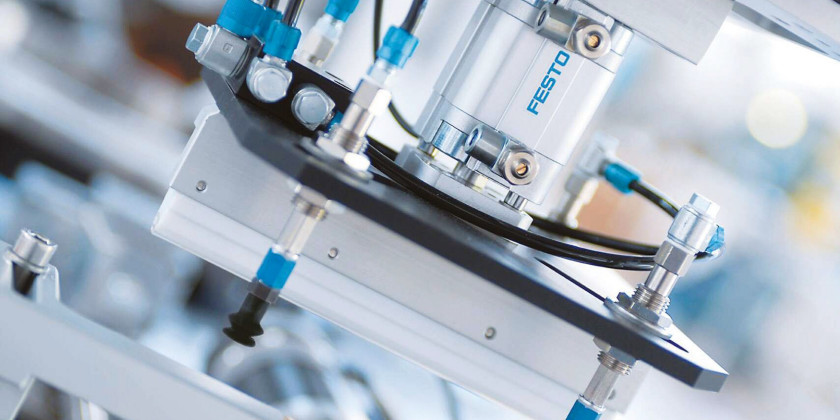
Spadki ciśnienia wynikające z obecności takich wbudowanych elementów są z reguły trudne do wyeliminowania, na szczęście jednak zazwyczaj nie stanowią głównego źródła nieefektywności. Poważniejszym problemem są zanieczyszczenia osadzające się na komponentach systemu – na przykład na filtrach powietrza wlotowego do sprężarki, wykorzystywanych w przypadku dużej koncentracji pyłów na wejściu kompresora. Gdy stają się zbyt brudne, zawory wlotowe zasysają coraz mniej powietrza, w konsekwencji obniżając wydajność produkcji medium.
Straty ciśnienia w sprężarce
Warto zatem pamiętać, że nie tylko po stronie przesyłu i odbioru sprężonego powietrza może dochodzić do strat ciśnienia, występują one też bowiem w części produkcyjnej. Dlatego w razie odnotowania na wejściu odbiornika ciśnienia niższego, niż oczekiwane, należy sprawdzić pod tym kątem również sprężarkę.
Kilka komponentów kompresora może potencjalnie spowodować spadek jego wydajności. Jednym z nich są separatory olej–powietrze w sprężarkach śrubowych. Ich zadaniem jest oddzielenie cząstek oleju od powietrza. Olej jest wtryskiwany jako czynnik chłodniczy. Uszczelnia także powierzchnię roboczą śruby oraz smaruje wszystkie ruchome części. Zużyty separator oleju powoduje zmniejszenie sprawności kompresora. Newralgiczne komponenty kompresorów to również: chłodnica końcowa, czyli wymiennik ciepła, który chłodzi gorące sprężone powietrze, doprowadzając do kondensacji wody, która inaczej skropliłaby się w instalacji przesyłu sprężonego powietrza, separatory wilgoci, osuszacze oraz filtry. Ich nieprawidłowe działanie i zanieczyszczenia również pogarszają wydajność sprężarki. Generalnie powinny być także dobrane tak, aby zapewnić możliwie najmniejszy spadek ciśnienia w określonych warunkach pracy. Oprócz tego, jeżeli zmiana ustawienia ciśnienia na wyjściu sprężarki nie zadziała, może to oznaczać problem z uszkodzonymi zaworami.
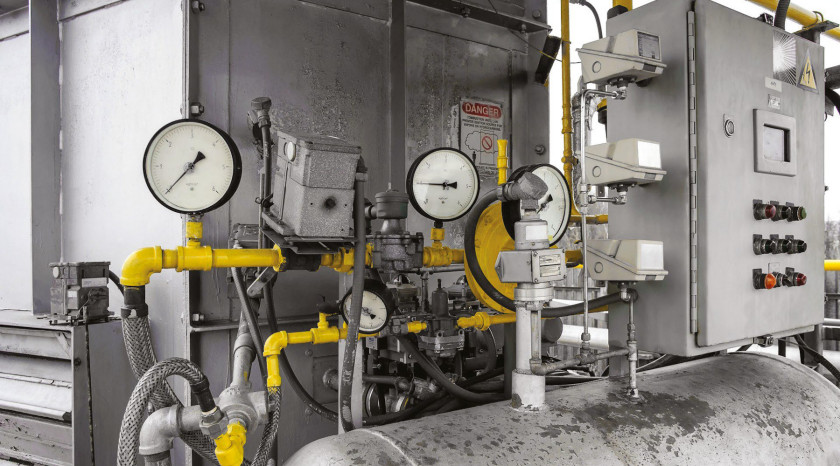
Słaba jakość powietrza
W tym miejscu warto dodać, że w niektórych zastosowaniach, na przykład jeżeli wymagana jest sterylność, zapewnić trzeba wysoką jakość powietrza. Jej pogorszenie się może nastąpić z kilku przyczyn, na przykład jeżeli serwisowe zawory obejściowe w wyniku niedopatrzenia personelu zostaną pozostawione otwarte po zakończeniu konserwacji i ponownym uruchomieniu systemu.
Kolejnym powodem mogą być niedziałające zawory spustowe i/albo zablokowane przewody spustowe. Często fakt ten może pozostać niezauważonym jeżeli prawidłowo działa osuszacz ziębniczy, którego zadaniem jest schłodzenie powietrza, co powoduje skroplenie wody, po odprowadzeniu której powietrze można ponownie podgrzać do temperatury pokojowej. To zapobiega kondensacji w przewodach dystrybuujących sprężone powietrze. Jeżeli jednak z powodu awarii spustu/zatkania jego przewodów woda nie zostanie odprowadzona, wilgoć z powrotem może przeniknąć do sprężonego powietrza na wylocie kompresora.
Jakość medium może też ulec pogorszeniu w razie niedostatecznej konserwacji filtrów. Zwykle chcąc określić stopień ich zabrudzenia, personel opiera się na wskazaniach czujników różnicy ciśnień na wlocie oraz wylocie filtru. Może się jednak zdarzyć, że jeżeli jego wkład ulegnie uszkodzeniu, zanieczyszczając instalację, odczyt z sensorów zawsze będzie wskazywał zerową różnicę. Przez to pracownicy nigdy nie zostaną zaalarmowani o potrzebie wymiany wkładu.
Woda, olej, rdza w instalacji
Szczególne przypadki zanieczyszczeń mogą wskazywać na to, który konkretnie element instalacji sprężonego powietrza nie działa zgodnie z oczekiwaniami. Jeżeli medium jest nadmierne zawilgocone, zwłaszcza w punkcie docelowym, przyczyną mogą być uszkodzone pułapki kondensatu. Innym powodem może być też wadliwy albo nieprawidłowo dobrany (co zwykle oznacza nieuwzględnienie warunków pracy) osuszacz powietrza lub chłodnica końcowa. W obu przypadkach, mimo obecności tych komponentów w systemie, mogą być one całkiem bezużyteczne. Jeżeli w przewodach, którymi transportowane jest sprężone powietrze, dochodzi do kondensacji, a częścią instalacji nie jest ani chłodnica, ani osuszacz, zdecydowanie warto jest ją w nie doposażyć.
W razie stwierdzenie zanieczyszczenia medium cząstkami oleju warto bliżej przyjrzeć się wcześniej wspomnianemu separatorowi olej–powietrze. Należy wtedy sprawdzić jego stan, jak też porównać poziom oleju z zaleceniami producenta kompresora. Brud i rdza docierające do odbiornika wraz ze sprężonym powietrzem świadczą z kolei o starzeniu się rurociągów, które trzeba w takim przypadku wymienić lub zainstalować filtr bezpośrednio przed miejscem odbioru medium.
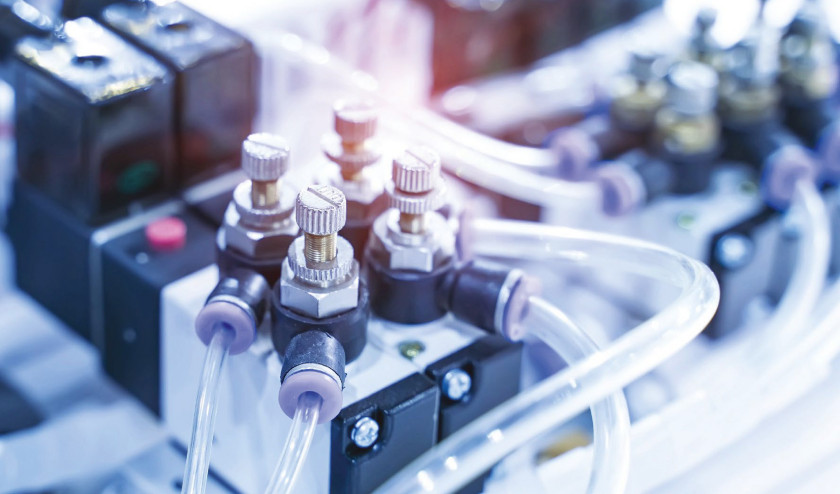
Podsumowanie
Generalnie zaniepokoić należy się też w przypadku, gdy sprężarka nadmiernie się nagrzewa. Prawdopodobnie jest to skutkiem słabej wentylacji lub zatkanych filtrów powietrza wlotowego.
Podsumowując, sprężone powietrze, jako medium produkowane na miejscu, w zakładzie, inaczej niż inne, od zewnętrznych dostawców, jak gaz czy energia elektryczna, wymaga większej uwagi, czyli w praktyce większego zaangażowania w ramach zarówno konserwacji prewencyjnej, jak i predykcyjnej. Jeżeli od dostępności sprężonego powietrza zależy ciągłość pracy maszyn oraz przebieg procesów kluczowych dla funkcjonowania zakładu, warto jest rozważyć zakup rezerwowego kompresora (albo wykorzystanie w tym celu wcześniej używanej sprężarki). Zapasowe kompresory należy utrzymywać w gotowości, nie tylko dzięki ich regularnemu konserwowaniu, ale również przez cykliczne czasowe uruchamianie.
Monika Jaworowska