Strategia zwiększania efektywności energetycznej w obszarze sprężonego powietrza musi bazować równocześnie na wielu zależnych od siebie działaniach, związanych z modernizacją sieci, doborem maszyn i komponentów, optymalizacją połączeń, monitoringiem statycznych i dynamicznych procesów produkcyjnych oraz wypracowaniem i wdrożeniem właściwych schematów zachowań ludzkich. Narzędziami ułatwiającymi realizację każdego z tych zadań są usługi serwisowe Festo, prowadzone według normy ISO/DIN 11011 wyznaczającej standardy audytów efektywności energetycznej sprężonego powietrza.
Wdrożenie projektu zwiększenia efektywności energetycznej może być realizowane według modelu "Bottom To Top". Polega on na przeprowadzaniu nieagresywnych inwestycyjnie cykli oraz stopniowym zwiększaniu ich zasięgu, z implementacją bardziej zaawansowanych technologii, finansowanych już z zysków (oszczędności) wypracowanych w cyklach poprzednich. W przypadku takiego schematu wdrażania środków utrzymania ruchu korzyści wynikające z pierwszych, małych audytów zapewnią w krótkim czasie, praktycznie bez kosztów początkowych, pełną profilaktykę i monitoring efektywności o znaczących indeksach oszczędności.
Zwiększanie efektywności energetycznej w liczbach
Aby dostrzec rozmiar strat związanych z wyciekami sprężonego powietrza, warto analizować pomiary w skali dłuższego okresu. Akademickim wręcz przykładem (tabela 1) może być wyciek z jednej tylko nieszczelności o przykładowej średnicy, rozpatrywany w czasie roku (do obliczeń przyjęto średni, występujący w przemyśle koszt wytwarzania sprężonego powietrza).
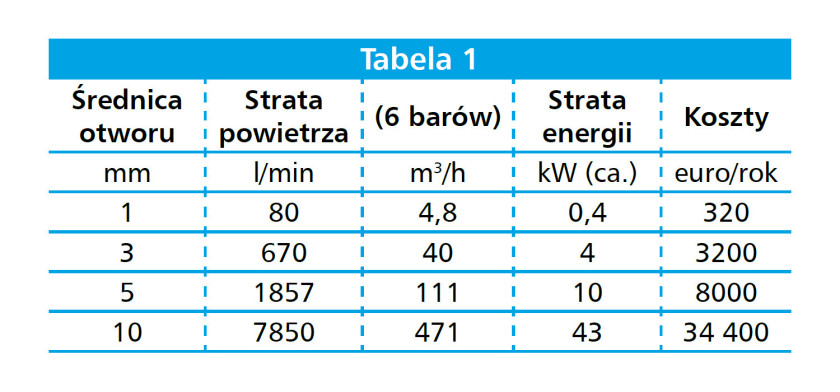
Straty wynikające z dużej liczby wycieków ilustruje kalkulacja wdrożenia programu zwiększenia efektywności energetycznej (tabela 2), polegającego na wykryciu i eliminacji wycieków na poziomie całej sieci pneumatycznej w jednym z zakładów należących do światowego producenta żywności.
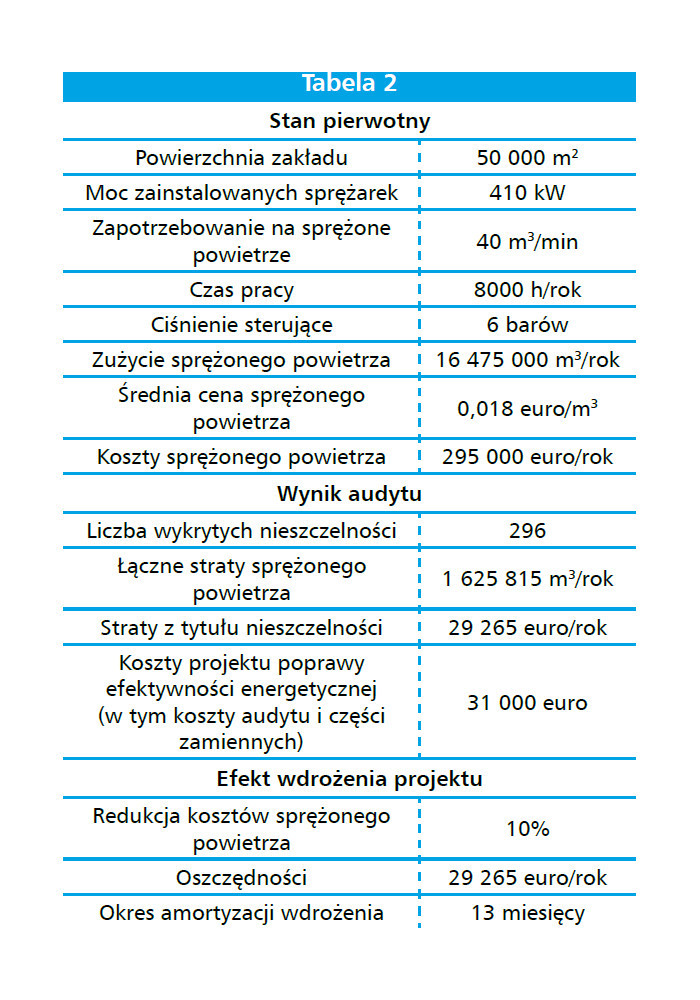
Spektakularnym przykładem wdrożenia przez Festo programu zwiększenia efektywności energetycznej mogą być również działania podjęte przez holenderską firmę Tate & Lyle, będącą światowym producentem składników i rozwiązań dla przemysłu spożywczego. W przedsiębiorstwie działającym pod presją ogromnej konkurencji postanowiono przebadać szczelność wszystkich pracujących w zakładzie systemów sprężonego powietrza. "Specjaliści z firmy Festo dokonali przeglądu naszych systemów i znaleźli mnóstwo przecieków – wyjaśnia kierownik utrzymania ruchu, Remo Dubbeld. – Ogółem traciliśmy 6 tysięcy litrów powietrza na minutę, co generowało ok. 8% kosztów sprężonego powietrza. Przy założeniu, że nasza średnia cena metra sześciennego sprężonego powietrza wynosi 0,025 euro, roczne oszczędności osiągają poziom 75 tys. euro".
Komu powierzyć wykonanie pomiarów?
Zakład przemysłowy ma dwie możliwości monitorowania i optymalizacji efektywności energetycznej: w oparciu na własnych zasobach działu utrzymania ruchu lub za pomocą zewnętrznej, wyspecjalizowanej firmy. Kluczem do dokonania właściwego wyboru jest udzielenie odpowiedzi na następujące pytania:
- Ile czasu i pieniędzy potrzeba do samodzielnego wykrycia i wyeliminowania nieszczelności w całym zakładzie?
- Ile czasu i pieniędzy może wymagać samodzielna analiza wytwarzania, jakości i zużycia sprężonego powietrza w przypadku wszystkich posiadanych systemów i sprężarek?
- Czy zakład dysponuje odpowiednimi przyrządami pomiarowymi, a jego pracownicy mają praktyczne umiejętności wykonywania i oceny pomiarów oraz interpretacji wyników?
- Jakim kosztem dla przedsiębiorstwa byłoby przygotowanie listy wszystkich wymaganych części zamiennych i ich zamówienie?
- Ile potrzeba czasu, aby znaleźć odpowiednie zamienniki starszych, niedostępnych już wyrobów?
Aby implikacje decyzji o wyborze wykonawcy audytu były od początku istotnymi elementami długofalowego procesu oszczędzania, o wiele bezpieczniejsze i opłacalne od własnych działań jest skorzystanie z kompetencji firmy zewnętrznej, której eksperci mają do zaoferowania bogate doświadczenie w dziedzinie zwiększania efektywności energetycznej. Biorąc pod uwagę współpracę z firmą Festo, uzyskuje się pewność, że umiejętności audytorów i inżynierów wynikają z praktyki wstępnych badań i analiz, planowania i wdrażania środków służących do optymalizacji działania oraz dbania o utrzymanie satysfakcjonującego poziomu oszczędności w długim okresie. Fachowa ocena i interpretacja wyników pomiarów przez firmowych specjalistów stanowią bezcenną podstawę do przygotowania planów postępowania dostosowanych do indywidualnych wymagań klienta.
Działania w ramach modelu "bottom to top"
Analiza zużycia energii przy wytwarzaniu sprężonego powietrza
System sprężania musi być w stanie przygotować i wytworzyć sprężone powietrze do zasilania wielu różnych odbiorników, zapewniając odpowiednią ilość i jakość powietrza w opłacalny i wydajny sposób.
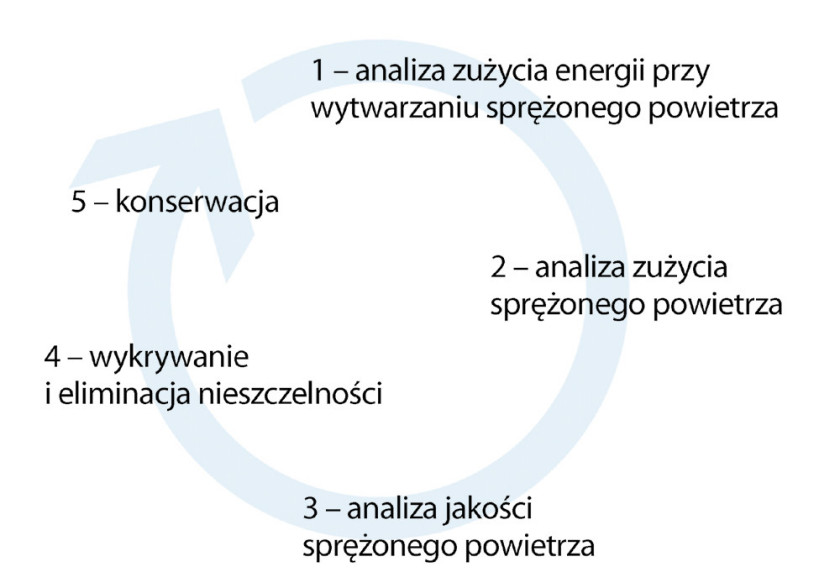
Cel serwisu:
- stworzenie profilu zużycia energii w odniesieniu do zapotrzebowania na sprężone powietrze w różnych okresach działania (obciążenie bazowe i szczytowe), z uwzględnieniem i rejestracją chwilowych wahań;
- wyznaczenie sposobów uzyskania potencjalnych oszczędności.
Zakres usługi:
- monitorowanie zużycia sprężonego powietrza w okresie kilku dni, włącznie z przestojami i dniami wolnymi od pracy;
- pomiar parametrów procesu – czas pracy sprężarek, pomiar bieżącego i łącznego zużycia sprężonego powietrza, pomiar wartości i zakresu zmian ciśnienia;
- określenie sprawności sprężania poprzez porównanie zużycia energii elektrycznej z ilością dostarczonego powietrza;
- analiza danych i kosztów w celu określenia środków służących do poprawy wyników.
Korzyści dla klientów:
- pomiar układu sprężania niezależny od producenta;
- prowadzenie pomiarów podczas pracy systemu;
- uzyskanie jednoznacznych danych o zużyciu energii w całej instalacji;
- uwidocznienie kosztów zużycia sprężonego powietrza;
- pomiar i wykazanie rezerwy systemu.
Analiza zużycia sprężonego powietrza
Znajomość poziomu zużycia sprężonego powietrza przez poszczególne maszyny ma istotne znaczenie dla optymalnej konfiguracji jego podaży i dystrybucji.
Cel serwisu:
- wyznaczenie zużycia sprężonego powietrza i strat powodowanych przez nieszczelności;
- wyznaczenie charakterystycznych wartości ciśnienia i przepływu.
Zakres usługi:
- dokładny pomiar zużycia sprężonego powietrza przez poszczególne maszyny w stanie statycznym (przestój) i dynamicznym (praca);
- rejestracja parametrów – zużycie powietrza przypadające na cykl pracy maszyny, średnie zużycie minutowe, maksymalne i minimalne ciśnienie w cyklu, maksymalne i minimalne natężenie przepływu;
- dokumentacja i analiza wyników pomiarów.
Korzyści dla klientów:
- wykazanie rzeczywistego zużycia sprężonego powietrza przez poszczególne maszyny;
- eliminacja niepożądanego spadku ciśnienia lub zbędnego zużycia energii na skutek niedostatecznej podaży powietrza;
- określenie wielkości i kosztów zużycia sprężonego powietrza związanego z nieszczelnościami;
- możliwość optymalnej konfiguracji dostaw sprężonego powietrza do maszyn;
- znajomość potencjalnych źródeł oszczędności.
Analiza jakości sprężonego powietrza
Obecność oleju, wody lub cząstek stałych w sprężonym powietrzu ma negatywny wpływ na trwałość komponentów i zespołów pneumatycznych. Substancje te przyczyniają się do usuwania smaru technologicznego oraz powodują zużycie i uszkodzenia uszczelnień lub innych współpracujących elementów. W efekcie rosną koszty nie tylko operacyjne, ale przede wszystkim te wynikające z nieplanowanych przestojów.
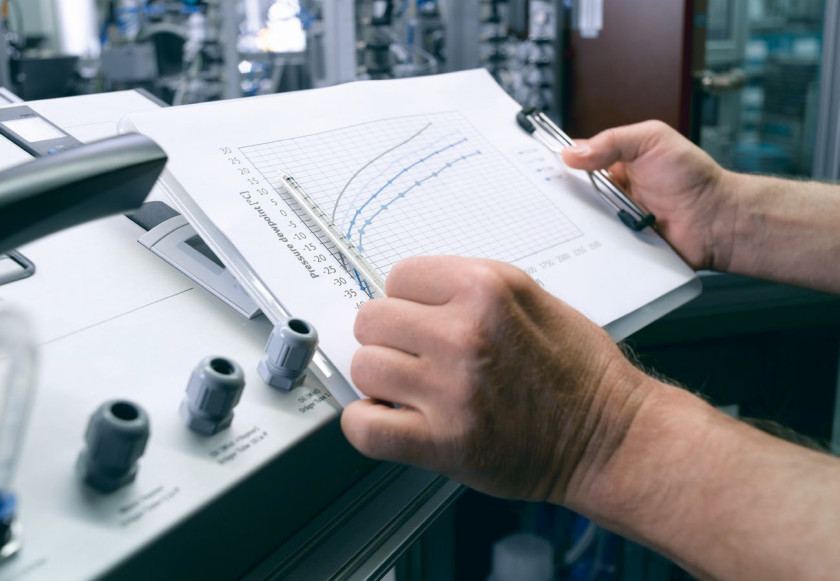
Cel serwisu:
- zwiększenie sprawności maszyn i niezawodności procesów;
- zmniejszenie kosztów utrzymania ruchu.
Zakres usługi:
- centralny lub rozproszony pomiar jakości sprężonego powietrza – kontrola zespołów przygotowania powietrza, pomiar zawartości wody i oleju;
- wyznaczenie ciśnieniowego punktu rosy;
- pomiar temperatury i ciśnienia powietrza;
- dokumentacja i analiza wyników.
Korzyści dla klientów:
- zapewnienie optymalnej jakości sprężonego powietrza;
- zwiększenie trwałości elementów pneumatycznych;
- ograniczenie do minimum występowania nieoczekiwanych usterek maszyn;
- możliwość modyfikacji sposobu przygotowania sprężonego powietrza na podstawie uzyskanych danych.
Wykrywanie nieszczelności
Systematyczne wykrywanie nieszczelności w instalacjach sprężonego powietrza i ich sprawne usuwanie znacząco zmniejszają koszty sprężonego powietrza. Według autorów studium "Compressed Air Systems in the European Union", opublikowanego przez Instytut Fraunhofera ISI, eliminacja samych tylko nieszczelności może przynieść zwrot w postaci 42% łącznych potencjalnych oszczędności.
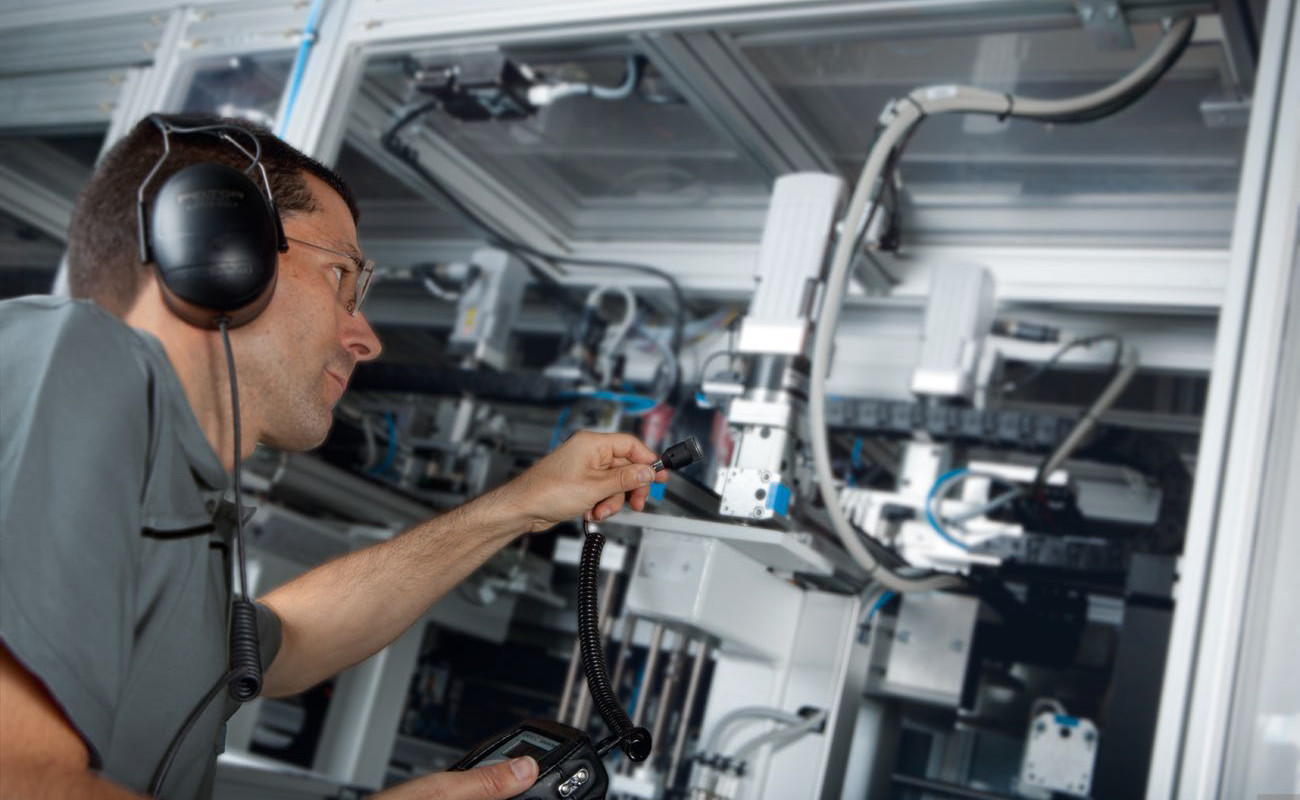
Cel serwisu:
- wykrywanie nieszczelności w poszczególnych maszynach, systemach lub w całej instalacji;
- oznakowanie, rejestrowanie i dokumentowanie wycieków;
- opracowanie indywidualnych planów działania w celu eliminacji nieszczelności.
Zakres usługi:
- badanie całego systemu sprężonego powietrza – od sprężarki po końcowe urządzenia wykonawcze;
- wykrywanie nieszczelności podczas pracy urządzeń przy użyciu detektorów ultradźwiękowych;
- oznaczenie wykrytych nieszczelności;
- klasyfikacja przecieków według wielkości, na potrzeby obliczania strat powietrza;
- rejestracja wszystkich informacji niezbędnych do napraw i usprawnień.
Korzyści dla klientów:
- prowadzenie pomiarów bez konieczności wstrzymania produkcji;
- szybkie wykrycie i zaliczenie nieszczelności do określonych kategorii;
- uwidocznienie strat energii i kosztów wynikających z nieszczelności instalacji;
- uzyskanie szczegółowej listy wymaganych napraw ze wskazaniem części zamiennych;
- możliwość śledzenia oszczędności dzięki rejestracji danych bieżących i historycznych.
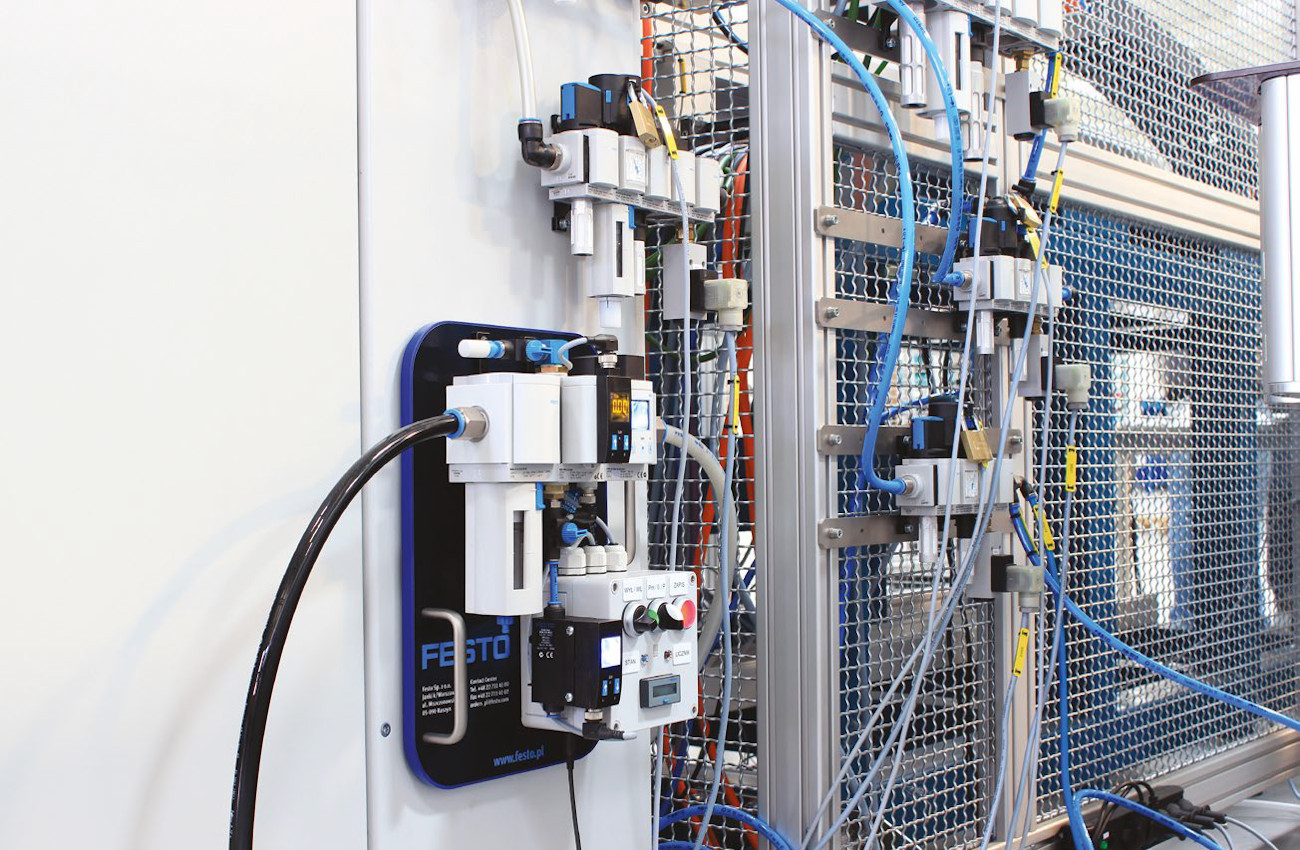
Jacek Paradowski
Festo sp. z o.o.
Janki k. Warszawy
ul. Mszczonowska 7, 05-090 Raszyn
tel. +48 22 711 41 00
festo_poland@festo.com
www.festo.pl