Historia manometrów mechanicznych sięga czasów rewolucji przemysłowej, gdy wraz z upowszechnianiem się maszyn parowych w przemyśle i transporcie zaczęło dochodzić do wypadków powodowanych przekroczeniem limitów ciśnienia pary – żeby chronić personel i użytkowników, wyposażano je w zawory bezpieczeństwa i właśnie ciśnieniomierze. Chociaż w międzyczasie rozwinął się segment manometrów cyfrowych, popularność tych analogowych nie słabnie, głównie dzięki postępowi w zakresie materiałów konstrukcyjnych i technologii produkcji, m.in. technik spawania, czy badania szczelności. W efekcie nowoczesne manometry mechaniczne nie ustępują pozostałym przyrządom do pomiaru ciśnienia pod względem trwałości, czytelności, dokładności w mniej wymagających aplikacjach ani ceny. Dzięki temu wskaźniki tego typu są częścią na przykład agregatów spawalniczych, sprężarek, agregatów hydraulicznych, głowic odwiertów. Montowane są oprócz tego m.in. w instalacjach ciepłowniczych i chłodniczych, systemach wentylacji i klimatyzacji i sprzęcie medycznym, rurociągach mediów ciekłych i gazowych. Manometry mechaniczne znajdują również zastosowanie w monitoringu pomp, filtrów oraz w laboratoriach. m.in. przy wzorcowaniu czy w próbach szczelności.
Jak jest zbudowany manometr mechaniczny?
Popularną grupą manometrów mechanicznych są te sprężynowe. W ich przypadku do wyznaczenia wartości wielkości mierzonej wykorzystuje się zależność stopnia sprężystego odkształcenia elementu pomiarowego od ciśnienia wywieranego na niego przez medium procesowe.
Ciśnieniomierze sprężynowe są standardowo zbudowane z tarczy z podziałką wyskalowaną w danej jednostce ciśnienia. Po niej przesuwa się igła, jednym końcem zamocowana w jej środku, a drugim zataczająca niepełny okrąg (typowo początek oraz koniec skali wypada mniej więcej na godzinach siódmej i piątej zegara, chociaż zależy to od zakresu i dokładności pomiaru i specyfiki wykonania). Ruchoma końcówka wskazówki ciśnieniomierza wskazuje na podziałce aktualną wartość ciśnienia, połączona jest bowiem z elementem pomiarowym, który jest ukryty za tarczą. Razem z nią sensor jest umieszczony w obudowie, zazwyczaj w postaci metalowego odlewu lub kształtki z tworzywa sztucznego. Osłona jest od frontu przeszklona. Z obudowy wyprowadzone są przyłącza procesowe. W niektórych modelach manometrów, ze zintegrowanymi elementami elektronicznymi, dostępny jest dodatkowo elektryczny sygnał wyjściowy. W przypadku problemów z jego transmisją albo wyłączenia zasilania wartość wielkości mierzonej może mimo to zawsze zostać odczytana na miejscu. Jest to główną zaletą ciśnieniomierzy mechanicznych, wskazujących ciśnienie bez konieczności podłączania do zasilania.
Czym jest rurka Bourdona?
Ciśnieniomierze klasyfikuje się ze względu na typ elementu pomiarowego. W zależności od tego wyróżnia się manometry: rurkowe, przeponowe oraz mieszkowe. Dużą popularnością cieszą się szczególnie pierwsze z wymienionych. Wyróżniają się one szerokim zakresem pomiarowym – manometry rurkowe znajdują zastosowanie w pomiarach ciśnień o wartościach niskich, przez średnie, aż po wysokie, do kilku tysięcy barów. Wykorzystuje się je w kontrolowaniu ciśnienia gazów i cieczy. Są tanie.
Elementem pomiarowym jest w nich rurka Bourdona. Jest to wygięty w łuk kawałek elastycznego metalowego przewodu o owalnym (spłaszczonym) przekroju. Rurki Bourdona mogą mieć różny kształt. Zwykle spotykane są te w kształcie litery C, śrubowe, spiralne. Jeden koniec rurki jest zamocowany w przyłączu procesowym, a drugi, o zamkniętym wylocie, pozostaje swobodny. Pierwszym jest doprowadzane mierzone medium, zaś drugi jest połączony z mechanizmem przekładni, a za jej pośrednictwem ze wskazówką manometru. Przy zmianie ciśnienia płynu przekrój rurki Bourdona zmienia kształt z owalnego w okrągły, jeżeli ciśnienie wewnątrz niej jest wyższe niż ciśnienie zewnętrzne lub odwrotnie – rurka ulega spłaszczeniu, jeżeli ciśnienie wewnątrz jest niższe od zewnętrznego. Towarzyszące temu naprężenia powodują odchylanie się zgiętej rurki – odpowiednio rozwija się ona albo się zwija. To wywołuje przemieszczanie się jej swobodnej końcówki. Ruch ten, który jest proporcjonalny do mierzonego ciśnienia, znajduje odzwierciedlenie w położeniu igły na tarczy ciśnieniomierza.
Na możliwości pomiarowe manometru ma wpływ typ rurki, a zwłaszcza kąt jej zwinięcia. W przypadku rurek w kształcie litery C jego maksymalna wartość nie przekracza 360°, dlatego jeżeli wymagana jest większa czułość, stosowane są rury spiralne albo śrubowe. Poza tym zakres pomiarowy zależy od materiału wykonania oraz średnicy rurki.
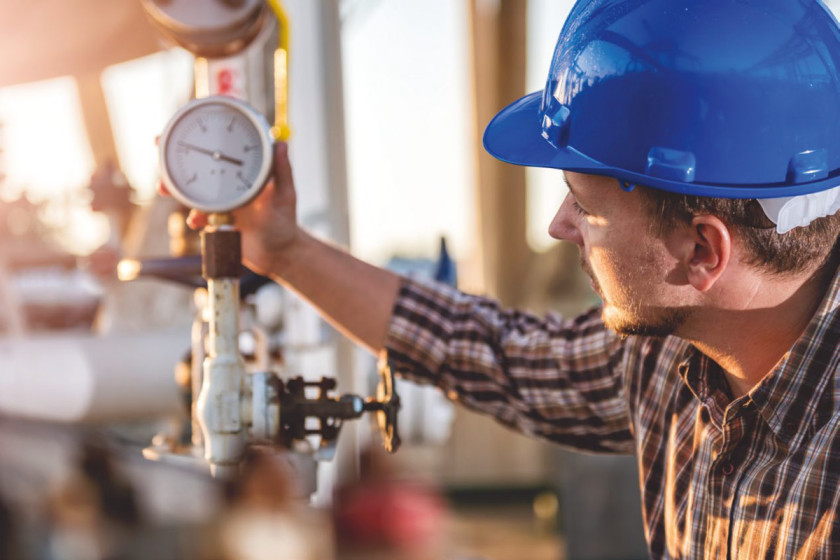
Co wyróżnia manometry przeponowe i mieszkowe?
Elementem pomiarowym w manometrach przeponowych, inaczej membranowych, jest – jak sama nazwa wskazuje – membrana, rozciągnięta i zamocowana w korpusie obudowy. Jej odkształcenie pod wpływem zmian ciśnienia jest przenoszone przez przekładnię na igłę przesuwającą się po tarczy. Zakres pomiarowy tego typu przyrządów wynosi typowo 0‒40 barów. Zdecydowanie najlepiej ciśnieniomierze przeponowe sprawdzają się w pomiarach ciśnień niskich, co wynika z dużej powierzchni membrany. Łatwo są także przez nie wykrywane niewielkie zmiany ciśnienia. Manometry tego typu wykorzystuje się ponadto w pomiarach podciśnień i ciśnień różnicowych. Z drugiej strony membrana jest podatna na pękanie w razie oddziaływania dużego ciśnienia, powyżej wartości znamionowej. Na stan taki wskazuje zwykle nieruchoma wskazówka, zatrzymana na dole skali. Ważną zaletą ciśnieniomierzy przeponowych jest natomiast odporność na wstrząsy. Ponadto łatwo jest je zabezpieczyć przed korozją czy ścieraniem w razie kontaktu z płynami agresywnymi chemicznie, pokrywając membranę stosowną powłoką ochronną. W porównaniu z manometrami z rurką Bourdona mniejsze jest też prawdopodobieństwo ich zatkania podczas pomiarów mediów z cząstkami stałymi. Niestety skoki temperatury powodują, że wskazania ciśnieniomierzy tego typu są mniej dokładne.
W manometrach mieszkowych, inaczej puszkowych, elementem pomiarowym jest z kolei metalowa, pofalowana po bokach puszka (mieszek), z wlotem otwartym dla mierzonego płynu. Pod wpływem przykładanego ciśnienia mieszek się rozszerza. Jego przemieszczenie znajduje odzwierciedlenie w ruchu wskazówki na tarczy manometru, z którą jest on sprzężony. Przyrządy tego typu sprawdzają się szczególnie w pomiarach niskich ciśnień.
Wybieramy manometr – na co zwrócić uwagę?
Jeżeli już zdecydujemy się na manometr mechaniczny (gdy wiadomo, że nie jest wymagany wysoki poziom dokładności ciśnieniomierzy cyfrowych ani dodatkowa funkcjonalność, na przykład kompensacja temperatury, czy bezprzewodowa transmisja pomiarów, które są standardowymi opcjami w manometrach tego rodzaju), wybierając konkretny model, powinniśmy wziąć pod uwagę kilka czynników zależnych od specyfiki zastosowania.
Na wstępie zdecydować trzeba, który z typów ciśnieniomierzy najlepiej sprawdzi się w danej aplikacji, uwzględniając ich mocne strony i ograniczenia, o których pisaliśmy wyżej. I tak na przykład, jeśli zastanawiamy się nad zakupem manometru z rurką Bourdona, powinniśmy się wcześniej upewnić, że nie będzie wykorzystywany do pomiaru ciśnienia mediów z cząstkami stałymi ani korozyjnych albo że zostanie przed tym dodatkowo specjalnie zabezpieczony, na przykład dzięki zastosowaniu separatora membranowego, oddzielającego wrażliwy element pomiarowy od płynu procesowego. Jest on zbudowany z elastycznej, wytrzymałej membrany, stykającej się z jednej strony z agresywnym medium, zaś z drugiej z bezpiecznym płynem, który wypełnia przestrzeń między nią a elementem pomiarowym manometru. Zespół membrana–płyn przekazuje temu ostatniemu ciśnienie wywierane przez mierzone medium. Jeśli natomiast rozważamy zakup ciśnieniomierza przeponowego trzeba sprawdzić, czy w instalacji nie są spodziewane bardzo duże skoki ciśnienia przekraczające maksymalne ciśnienie znamionowe przyrządu ani wahania temperatury, a jeśli tak, należy zabezpieczyć manometr na wypadek ich wystąpienia. Przed pierwszymi chronią na przykład regulowane ograniczniki ciśnienia, natomiast wyrównanie temperatury zapewniają m.in. akcesoria rozpraszające ciepło procesowe, na przykład rurki syfonowe chłodzące mierzony płyn.
Generalnie należy też pamiętać, że manometry, które charakteryzuje duża powtarzalność oraz precyzja pomiarów w zakresie wysokich ciśnień, przeważnie będą miały gorsze parametry w pomiarach ciśnień niskich. Poza specyfiką typu ciśnieniomierza ważne są także zastosowane rozwiązania konstrukcyjne, dzięki którym jest dostosowany do nietypowych warunków pracy oraz odporny na te nieprzyjazne. Przykładem są różne materiały części zwilżanych manometru, które powinny być kompatybilne z mierzonym płynem. I tak przykładowo elementy mosiężne są odpowiednie do wody, powietrza lub innych nieagresywnych cieczy i gazów. Z kolei w przypadku płynów silnie reaktywnych chemicznie wymagane są materiały odporne na korozję jak stal nierdzewna czy monel (stop niklowo-miedziowy).
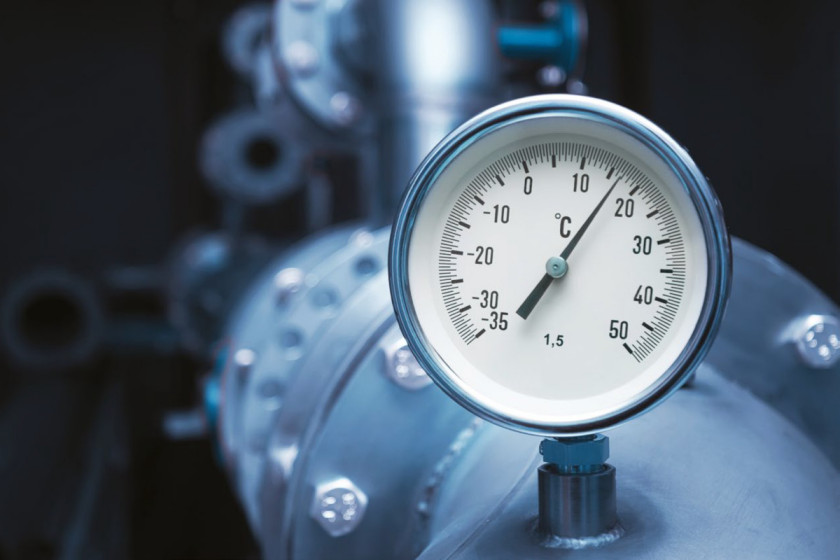
Rozmiar tarczy, a jej czytelność
Istotną kwestią jest odpowiedni rozmiar manometru. Ta jego cecha wpływa bowiem nie tylko na możliwość jego zamontowania w danym miejscu, ale także warunkuje precyzję i zakres pomiaru oraz czytelność wskazań przyrządu. Im większy ciśnieniomierz, tym jest bowiem większa tarcza, a im większą ma ona powierzchnię, tym może być gęściejsza podziałka skali, a nawet jest miejsce na podwójną lub wielozakresową skalę. Duża tarcza, z wyraźną skalą, będzie także lepiej widoczna z większej odległości. Z drugiej jednak strony, gdy występują ograniczenia przestrzenne, manometr z za dużą tarczą może się nie zmieścić. Trzeba także zwrócić uwagę na to, czy miejsce, w którym zostanie zamontowany, jest dobrze oświetlone. W przeciwnym razie odczyt wyników pomiarów, nawet gdy tarcza będzie sporych rozmiarów, może być utrudniony. Wtedy warto rozważyć zakup modelu z tarczą odblaskową albo wykonaną z materiału o właściwościach fotoluminescencyjnych.
Jaka jest rola cieczy wypełniającej?
Manometry mechaniczne można podzielić na dwie grupy: suche i zalane specjalnie dobraną cieczą. Obudowę przyrządu wypełnia się nią z kilku powodów. Przede wszystkim zapewnia ona tłumienie wibracji przenoszących się na ciśnieniomierz z otoczenia, których źródłem mogą być przykładowo pompy zasilające daną instalację albo inne maszyny z nią sąsiadujące. Jeżeli są szczególnie silne jest to konieczne, gdyż narażenie na ciągłe drgania jest jedną z częstszych przyczyn awarii manometrów. Wynika to stąd, że zewnętrzne wibracje wzbudzają do drgań ruchome komponenty ciśnieniomierza, jak rurka Bourdona czy przekładnia, powodując ich przedwczesne zużywanie się albo uszkodzenie. Poza tym, że ciecz w obudowie amortyzuje ruchome części przyrządu, zapobiega również trudnościom z odczytem wyniku pomiarów z powodu drgań wskazówki. Zapewnia także smarowanie mechanizmu przekładni manometru.
Zazwyczaj obudowa ciśnieniomierza jest wypełniona cieczą tłumiącą drgania najwyżej w 90% jej objętości. Zapas miejsca jest wymagany, aby zapobiec wyciekom płynu w razie jego rozszerzania się przy zmianach temperatury i wilgotności otoczenia. Ciecz wypełniająca to zwykle gliceryna z dodatkiem wody lub olej silikonowy. Pierwszą napełniane są manometry przeznaczone do użytku w temperaturach z przedziału –20°C.. +60°C. Poza tym zakresem, w temperaturach skrajnie niskich i wysokich, powinno się korzystać z przyrządów wypełnionych olejem silikonowym.
Manometry w niskich i wysokich temperaturach
W ekstremalne niskich temperaturach obecność cieczy wypełniającej w obudowie ma dodatkowe znaczenie – dzięki niej wewnątrz nie skrapla ani nie gromadzi się wilgoć. Ta jest niepożądana, ponieważ zamarzając w takich warunkach unieruchamia ruchome elementy manometru oraz powoduje oszronienie lub zamarzanie szybki, uniemożliwiając pomiar i odczyt wskazań.
W skrajnie niski temperaturach newralgicznym elementem ciśnieniomierzy są również uszczelki, których zadaniem jest zapobieganie wnikaniu wilgoci do obudowy oraz wyciekaniu z niej cieczy wypełniającej. Standardowo są wykonywane z elastomerów, które niestety w takich warunkach twardnieją i stają się kruche, nie gwarantując szczelności. Dlatego w manometrach do użytku w niskich temperaturach ten materiały zastępuje się innymi, odpornymi na ten czynnik środowiskowy.
Jeżeli natomiast chodzi o pracę w wysokich temperaturach, zarówno otoczenia, jak i mierzonego medium, należy unikać korzystania z manometrów z połączeniami lutowanymi, oddzielać gorący płyn od elementu pomiarowego na przykład za pomocą separatora membranowego z dodatkowymi elementami rozpraszającymi ciepło albo uzupełnić ciśnieniomierz w specjalny element chłodzący. Przykładem są komponenty do wkręcania w manometr / rurociąg, które wypromieniowują ciepło, obniżając dzięki temu temperaturę medium. W razie gdy ta ostatnia jest niższa niż temperatura otoczenia, z kolei zapewniają jego ogrzewanie.
Manometry w wykonaniu specjalnym
Dostępne są również manometry w wykonaniach specjalnych o konstrukcjach przystosowanych do konkretnych zastosowań. Przykładem są ciśnieniomierze dopuszczone do kontaktu z wodą pitną, które muszą być wykonane z materiałów bezołowiowych, hermetyczne, o wysokim stopniu ochrony obudowy i do zastosowań higienicznych, zabezpieczone przed kontaktem płynu procesowego z elementami manometru, które przykładowo są wyposażane w podwójne membranowe separatory oddzielone od siebie komorą próżniową. Ciśnienie w ostatniej monitoruje czujnik, dzięki czemu przebicie membrany zewnętrznej jest natychmiastowo wykrywane. Równocześnie, dzięki membranie wewnętrznej, pomiar jest kontynuowany. Kolejnymi przykładami są: manometry do tlenu i acetylenu, wykorzystywane w narzędziach i urządzeniach do spawania i do cięcia, w wykonaniu na przykład z szybką z poliwęglanu i przyłączami z mosiądzu, ciśnieniomierze ze stali nierdzewnej oraz modele bezpieczne. Ostatnie zawierają rozwiązania konstrukcyjne (m.in. przegrodę między tarczą a elementem pomiarowym, szybkę ze szkła laminowanego, specjalną oprawę), dzięki którym szybka nie pęka na kawałki w przypadku rozbicia, zaś w razie rozszczelnienia i wzrostu ciśnienia w obudowie medium i elementy manometru są wypychane tyłem przyrządu. Zapewnia to bezpieczeństwo personelowi znajdującemu się w pobliżu.
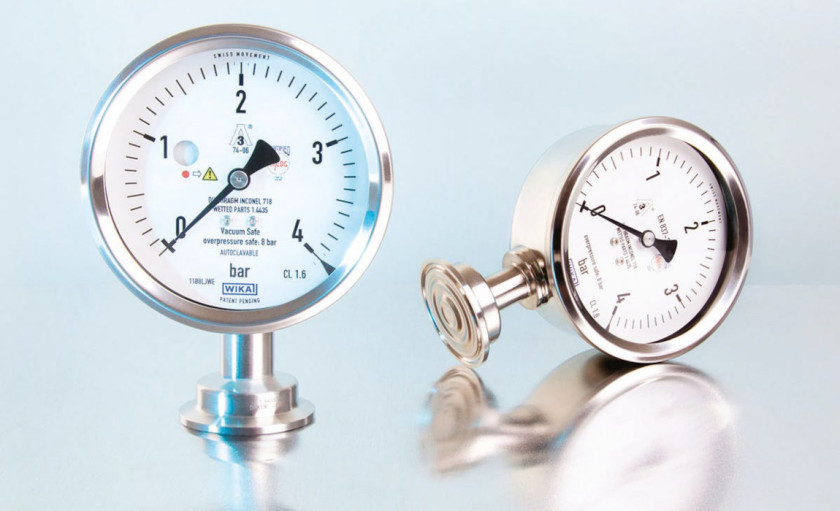
Monika Jaworowska