Paletyzacja polega na umieszczeniu produktów na palecie, zazwyczaj w celu przekazania ich do wysyłki albo zmagazynowania. Układa się je w stos w taki sposób, by jak największa ich liczba zajmowała jak najmniej miejsca, równocześnie dbając o stabilność ładunku, by nie dopuścić do jego przesuwania się na palecie, jej przewrócenia się ani zniszczenia poszczególnych paczek.
Konieczność usprawnienia załadunku palet pojawiła się wraz z uruchomieniem pierwszych linii pakowania. Początkowo przepustowość paletyzacji starano się zwiększyć przez oddelegowanie do tego zadania większej liczby pracowników. Efektywność tego sposobu jednak, zwłaszcza w przypadku ciężkich towarów, była mała. Nawet bowiem często zmieniani pracownicy szybko się męczyli, a to niestety powodowało spadek wydajności, wypadki, uszkodzenie ładunków. Doprowadziło to do rozpoczęcia prac nad systemami mechanicznymi, które mogłyby być używane zamiast lub we współpracy z pracownikami na stanowisku paletyzacji. Efektem był półautomatyczny system paletyzacji, który po raz pierwszy został wprowadzony do użytku na początku lat 50. zeszłego stulecia. Wciąż jest to popularne rozwiązanie, stale udoskonalane.
Półautomaty paletyzujące
Przykładowo w półautomacie paletyzacja przebiega następująco: najpierw paczki są przenoszone taśmociągiem na stanowisko, gdzie po dotarciu do ogranicznika układane są jedna przy drugiej, tworząc rząd, na przykład czterech sztuk. Następnie paczki ustawione w linii operator przesuwa na podnośnik. Na nim, rząd po rzędzie, układana jest warstwa. Gdy jest już gotowa, paczki zostają ze wszystkich stron wyrównane przez prowadnice. W kolejnym kroku płyta podnośnika przesuwa się nad paletę, gdzie zostaje wycentrowana nad poprzednią warstwą paczek. Następnie stopniowo wysuwa się spod nich, a te rząd po rzędzie układają się na ich poprzedniej warstwie. Kiedy paleta jest pełna, paczki są ponownie wyrównywane i zabiera ją wózek widłowy.
Aby zwiększyć przepustowość, w różny sposób usprawnia się tworzenie rzędów i warstw paczek, wykorzystując złożone systemy przenośników w pełni automatyzujące paletyzację. W zależności od konfiguracji systemu palety są obniżane z każdą uformowaną warstwą (układanie w dół) albo pozostają nieruchome, gdy podnoszone są warstwy paczek na podnośniku (układanie w górę). Półautomatyczne i automatyczne stanowiska paletyzacji dodatkowo wyposaża się w automatyczne foliarki. Owijają one w folię rzędy albo warstwy pakunków, co chroni je przed uszkodzeniem i stabilizuje ładunek palety.
W paletyzacji wykorzystywane są również roboty. Wyróżnia je większa elastyczność w zakresie zmiany typu obsługiwanych palet i wzorca układania paczek oraz szybkość.
Robotyzacja paletyzacji
W paletyzacji wykorzystuje się głównie roboty trzech typów: kartezjańskie, SCARA, przegubowe. Pierwsze mają trzy ortogonalne osie ruchu koordynowane przez jeden kontroler i poruszają się w osiach XY, XZ lub XYZ. Przeważnie nie sprawdzają się w paletyzacji z dużą przepustowością – maksymalnie typowo wynosi około 10 paczek na minutę, co wynika z ograniczonej przestrzeni operacyjnej i elastyczności robotów kartezjańskich w porównaniu do wymagań tego zadania. W wersji bramowej (gantry), czyli w konfiguracji 2XY lub 2XYZ (z dwiema równoległymi osiami bazowymi X), o dłuższym skoku oraz większym udźwigu niż w wersji podstawowej paletyzatory kartezjańskie sprawdzają się w załadunku większej liczby dużych paczek. Uzyskuje się to jednak kosztem zajęcia większej powierzchni magazynowej.
Paletyzatory typu SCARA także poruszają się wzdłuż trzech osi, ale z dodatkową funkcjonalnością ramienia obrotowego, dzięki czemu ich przestrzeń robocza ma kształt pierścienia (toroidu). Roboty SCARA wyróżnia większa wydajność operacyjna w porównaniu z kartezjańskimi, ale z drugiej strony ich udźwig nie przekracza 20 kilogramów. Sprawdzają się za to w wielotorowych liniach pakowania.
Najelastyczniejsze rozwiązanie to roboty przegubowe. Ruch ich ramienia jest nieliniowy i ma aż sześć stopni swobody. Charakteryzuje je również duża szybkość i udźwig, dlatego są najczęściej używane w paletyzacji.
Typowy udźwig paletyzatorów przegubowych wynosi od kilkudziesięciu kilogramów do ponad tony. W ciągu godziny mogą wykonać nawet kilka tysięcy cykli załadunków przy obciążeniu kilkuset kilogramów. Akcesoria oraz elastyczne opcje programowania pozwalają na szybką modyfikację wzoru układania, w tym paletyzację pojedynczych paczek, ich rzędów, warstw i dostosowywanie się do zmian ładunku. Dzięki dużemu zasięgowi pionowemu i poziomemu sprawdzają się w załadunku wysokich palet i obsłudze paletyzacji wielotorowej.
Akcesoria robotów paletyzujących
Chociaż specyfika typu robota ma istotne znaczenie, jeszcze ważniejszy jest wybór jego oprzyrządowania, od którego zależą możliwości podnoszenia i manipulowania ładunkami. W tym zastosowaniu używane są chwytaki różnego typu. Na przykład szczęki pneumatyczne podnoszą ładunek, zamykając się na nim z zewnątrz lub otwierając wewnątrz niego. Sprawdzają się przede wszystkim w podnoszeniu pojedynczych opakowań, gdy wymagana jest ich rotacja i duża przepustowość. W przypadku ciężkich paczek, szczególnie tych o równoległych bokach, najlepsze są szczęki równoległe. Chwytaki widłowe z dwoma rzędami zazębiających się palców podnoszą ładunek, zabezpieczając go od spodu. Są popularne w paletyzacji worków i delikatnych paczek. Używane są też chwytaki (przyssawki) próżniowe (podciśnieniowe). Zasada ich działania jest następująca: po zetknięciu przyssawki z powierzchnią podnoszonego przedmiotu aktywowany jest generator podciśnienia usuwający powietrze z miejsca styku. Ponieważ ciśnienie w chwytaku jest niższe niż na zewnątrz, ciśnienie atmosferyczne dociska ładunek do przyssawki. Przyssawki sprawdzają się w paletyzacji z kilku powodów. Są uniwersalne – siłę ssania można regulować w zależności od rozmiaru, kształtu czy wagi ładunku i nadają się do podnoszenia przedmiotów o nietypowych kształtach, które trudno złapać szczękami. Są również najlepszym wyborem w przypadku delikatnych, na przykład kruchych, ładunków. Działają też szybciej niż szczęki. Zwiększa to przepustowość paletyzacji, podobnie jak możliwość wyposażenia chwytaka w wiele przyssawek, dzięki czemu może podnieść równocześnie kilka przedmiotów lub równomiernie rozłożyć siłę ssania w przypadku dużych, płaskich przedmiotów.
Ważnym uzupełnieniem robotów są systemy wizyjne. Dzięki nim mogą tworzyć warstwy na palecie składające się z różnych produktów, które na podstawie informacji wizyjnej obracają i ustawiają, by najefektywniej wykorzystać dostępne miejsce lub kompletować kilka palet z różnymi produktami jednocześnie.
Jak uniknąć wąskich gardeł?
Żeby uzyskać maksymalne korzyści z inwestycji w robota paletyzującego, należy wyeliminować wąskie gardła na linii produkcyjnej, które mogą wystąpić w ciągu technologicznym przed nim i za nim. Takimi są zwykle stanowiska podawania pustych palet i owijania tych załadowanych w folię, które w celu zwiększenia ich wydajności najlepiej zautomatyzować, korzystając z podajnika palet oraz owijarki folii. Wąskim gardłem może się także okazać konfiguracja, w której wyjścia linii pakowania są kierowane na stanowisko paletyzacji, najpierw jednak przechodząc przez pojedynczy przenośnik. Zamiast tego lepiej, bez łączenia strumieni ładunków, korzystać z wielu transporterów, spotykających się w punkcie paletyzacji. Znacznie poprawia to jej przepustowość.
Korzyści z robotyzacji paletyzacji
W porównaniu z półautomatami i automatami do paletyzowania przestrzeń zajmowana przez zrobotyzowane paletyzatory jest najczęściej mniejsza. Kolejną zaletą tych ostatnich jest łatwość adaptowania się do zmian w zakresie produktów, jak i dołączania dodatkowych linii pakowania. Ponadto zrobotyzowane paletyzatory w przeciwieństwie do tych zmechanizowanych nie wywierają nacisku na paletę ani ładunki w celu ich wyrównania w poziomie, ponieważ układają je zgodnie z określonym wzorcem, ostrożniej nimi manipulując. Jest to zaletą w przypadku lżejszych, łatwiej uszkadzalnych produktów. Oprócz tego ze względu na ograniczone możliwości w zakresie ich obracania zmechanizowane systemy paletyzowania nieefektywnie kompletują ładunki o nietypowych kształtach. Wraz z wprowadzeniem robotów współpracujących wybór między półautomatem / automatem do paletyzowania a robotem przemysłowym nie jest już jednak jedynym dylematem, przed którym stają projektanci stanowisk paletyzacji.
A może coboty?
Roboty zaprojektowane do współpracy z człowiekiem mają szereg zalet, ale i ograniczeń. Pierwsze to: krótki czas wdrożenia, łatwiejsza obsługa skracająca czas szkolenia pracowników, uproszczone programowanie, mniejsze wymiary. Nie są również potrzebne dodatkowe zabezpieczenia, które by izolowały od nich obsługę stanowiska, dzięki czemu nie trzeba wprowadzać znaczących zmian w organizacji linii produkcyjnej. "Zwykłe" roboty przemysłowe natomiast wymagają dostosowania stanowiska przez stosowanie zabezpieczeń chroniących osoby mogące znaleźć się w ich pobliżu. Przez to zajmują dużo miejsca, wymagają ingerencji w przestrzeń zakładu, a proces instalacji komplikuje się i wydłuża. Z drugiej strony roboty przemysłowe są maszynami o większych możliwościach, ze względu na udźwig i prędkość, niż roboty współpracujące. Dlatego w produkcji wielkoseryjnej, we współpracy z szybkimi przenośnikami, lepiej sprawdzą się te pierwsze, natomiast produkcja w tempie cobotów musi być odpowiednio wolniejsza. Te ostatnie jednak wymagają mniejszych nakładów, które zwykle szybciej się zwracają, niż w przypadku robotów przemysłowych.
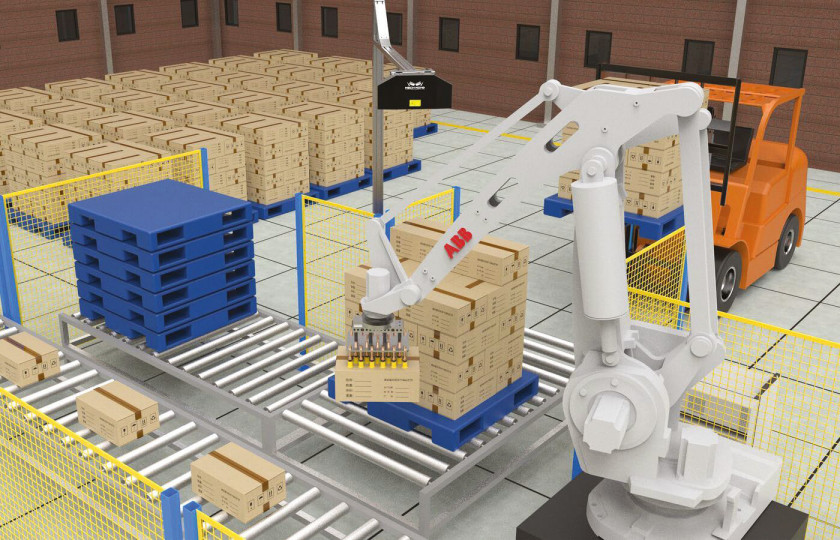
Monika Jaworowska