Wybierając obudowę, trzeba przeanalizować szereg jej cech. Taką jest rozmiar. Dobierając go, trzeba się upewnić, że zmieszczą się w niej wszystkie komponenty urządzenia, jak również, że miejsca będzie wystarczająco dużo by poprowadzić okablowanie. Jeżeli chodzi o to ostatnie, należy pamiętać, że może być wymagana dodatkowa przestrzeń, aby zachować odpowiedni odstęp między kablami mogącymi się zakłócać. Obudowa musi się też zmieścić w miejscu montażu. W przypadku szaf z drzwiami powinno się uwzględnić przestrzeń potrzebną do ich otwierania. Na rozmiary obudowy ma też wpływ wymagana wydajność odprowadzania ciepła przez układ wentylacji. Zwykle dobrym pomysłem jest pewna nadmiarowość – dzięki luzom w obudowie przepływ powietrza będzie swobodniejszy, a montaż oraz konserwacja łatwiejsze. Generalnie jednak jej rozmiar jest zawsze kompromisem między powyższymi wymogami a ceną.
Obudowa z metalu czy tworzywa?
Kolejną kwestią jest materiał wykonania. Pierwszym wyborem jest z reguły metal, gdyż generalnie obudowy tego typu są solidne i trwałe. Warto się jednak zastanowić, czy cechy te są wymagane w konkretnym przypadku, na przykład jeżeli dane urządzenie jest częścią innego i przed wpływem czynników zewnętrznych jest już chronione przez jego obudowę. W takim razie często ważniejsze są inne cechy osłony – przede wszystkim jej waga i kompaktowość. Są one istotne m.in. w sprzęcie medycznym, rolniczym, wyposażeniu statków. Ponadto obudowy z metalu wymagają uszczelnienia, by zapobiec wnikaniu wilgoci i w konsekwencji rozwijaniu się korozji. Ta ostatnia jest ich ważnym ograniczeniem – większość metali rdzewieje, a postęp tego procesu zależy od typu materiału oraz warunków środowiskowych. Te szczególnie niekorzystne to na przykład częste mycie detergentami i płukanie wodą, wymagane w przypadku wyposażenia linii produkcyjnych w branży spożywczej. W takich zastosowaniach, jeżeli wybierane są obudowy metalowe, są one zazwyczaj wykonywane z aluminium albo stali nierdzewnej, które cechuje większa odporność na korozję.
Popularyzacji obudów z plastiku sprzyja postęp w technologii tworzyw sztucznych. Przykładem są dodatki, które poprawiają odporność tych materiałów na wpływ długotrwałego nasłonecznienia czy wytrzymałość na rozciąganie. Osłony z tworzyw sztucznych są oprócz tego lżejsze niż metalowe, zapewniają izolację elektryczną, są tańsze i łatwiej formowalne, co ułatwia wykonywanie obudów o niestandardowych kształtach i nie korodują.
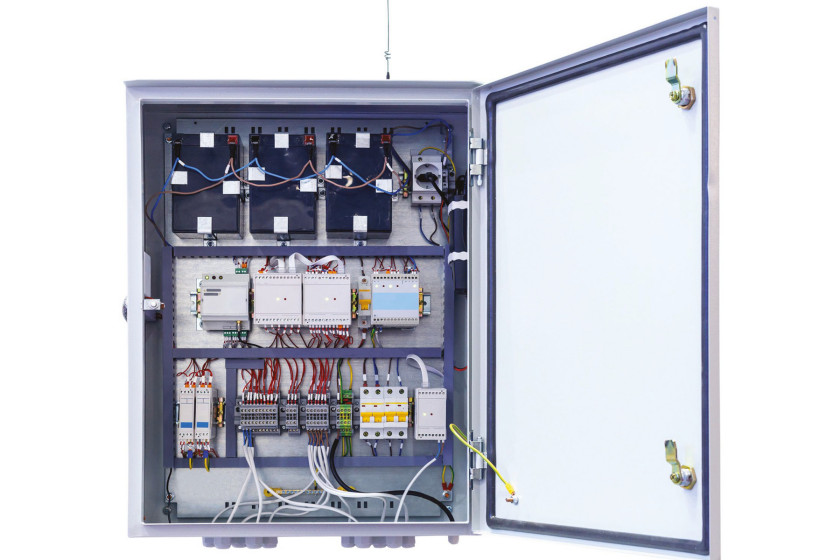
Na co jeszcze zwrócić uwagę?
Metal ekranuje zaburzenia elektromagnetyczne. Kompatybilność elektromagnetyczną wykonanych z niego obudów można poprawić, stosując specjalne uszczelki. Obudowy z tworzyw sztucznych nie tłumią tego typu zaburzeń, ale można im nadać taką właściwość, powlekając je metaliczną powłoką.
Ważna kwestia to także waga podzespołów, które będą wypełniać obudowę. Musi być ona w stanie utrzymać ich obciążenie. Generalnie te metalowe są pod tym względem wytrzymalsze od tych z tworzyw sztucznych, lecz w przeciwieństwie do nich są podatniejsze na wgniecenia pod wpływem uderzeń.
Metalowe obudowy przewodzą i rozpraszają ciepło. Dzięki temu zapewniają jego odprowadzanie, jeżeli temperatura na zewnątrz osłony jest niższa niż wewnątrz. Obudowy z tworzyw sztucznych z kolei izolują termicznie swoją zawartość, dlatego transfer ciepła musi być wymuszony przez system wentylacji. Analogiczne są właściwości metali i tworzyw sztucznych, jeśli chodzi o przewodnictwo elektryczne, co warunkuje konieczność odpowiedniego ich uziemienia lub jego braku.
Przegląd materiałów
Obudowy do użytku w przemyśle wykonywane są z szerokiej gamy materiałów. Popularne są zwłaszcza: stal węglowa, stal nierdzewna typu 304 i typu 316, poliester wzmocniony włóknem szklanym i poliwęglan. Przy wyborze konkretnego z nich pomocna jest znajomość ich specyfiki.
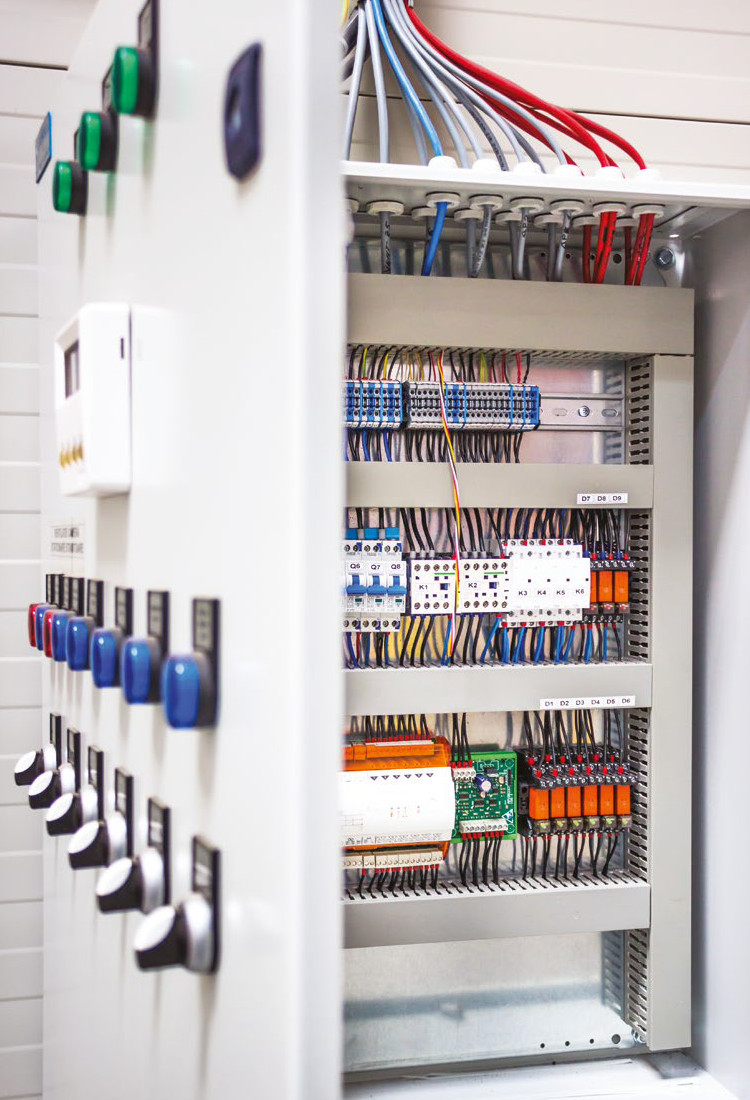
Stal węglowa to materiał tani, ale wymaga powlekania, by zapobiec korodowaniu. Trwałe, odporne na zarysowania pokrycie jest zwykle nanoszone techniką malowania proszkowego. W przypadku jego uszkodzenia metal bazowy rdzewieje. Oprócz tego nawet pomalowana stal węglowa ma ograniczoną odporność na rozpuszczalniki, zasady i kwasy. Wykonuje się z niej głównie obudowy do użytku wewnątrz pomieszczeń.
Stal nierdzewna typu 304 to stop na bazie żelaza zawierający od 18% do 20% chromu. Jest odporny na utlenianie (rdzewienie) i rozpuszczalniki, zasady i niektóre kwasy. Stal nierdzewna tego typu sprawdza się w przypadku obudów czyszczonych przez spłukiwanie i tych do użytku wewnątrz, jak i na zewnątrz.
Co wyróżnia poliwęglan?
Stal nierdzewna typu 316 zawiera molibden, dzięki czemu jest odporniejsza na korozję niż stal 304. Cechuje ją również lepsza odporność na siarczany, bromki, chlor, wodę morską (dzięki czemu sprawdza się w środowisku morskim), wysokie temperatury i niektóre kwasy. Obudowy ze stali nierdzewnej typu 316 stosowane są wewnątrz i na zewnątrz pomieszczeń.
Poliester wzmocniony włóknem szklanym wyróżnia odporność na korozję, wysoką temperaturę i uderzenia. Jest także lekki. Z drugiej strony z czasem blaknie, a długotrwała ekspozycja na światło słoneczne może powodować odbarwienia.
Poliwęglan jest wytrzymalszy na uderzenia i odporniejszy na światło słoneczne niż poliester wzmocniony włóknem szklanym. Jest to też materiał łatwiejszy w obróbce, dzięki czemu otwory w obudowie można staranniej wykończyć. Jest jednak droższy niż tworzywa ABS i PVC. Zakres zastosowań tych ostatnich ogranicza jednak mała wytrzymałość na uderzenia i wąski zakres temperatur pracy.
Ze względu na twardość wycinanie w obudowach ze stali nierdzewnej jest trudniejsze niż w tych ze stali węglowej. Cięcie tej ostatniej wymaga natomiast uzupełnienia uszkodzonej w wyniku tego działania powłoki ochronnej, w przeciwnym razie w miejscach odprysku farby rozwinie się korozja. Materiały na bazie włókna szklanego są łatwiejsze w obróbce, ale mogą pękać, a przy ich cięciu powstaje szkodliwy pył. Precyzyjniej można modyfikować obudowy z poliwęglanu. Również ich czyszczenie jest łatwiejsze i bezpieczniejsze.
Jeśli chodzi o koszt, to spośród wymienionych najdroższa byłaby obudowa ze stali nierdzewnej 316, a po niej ta ze stali nierdzewnej 304. Tańsze byłyby obudowy z poliestru wzmocnionego włóknem szklanym i poliwęglanu, a najtańsza ta z malowanej proszkowo stali węglowej.
Szczelność obudowy
Obudowy zabezpieczają też urządzenia przed zalaniem, zapyleniem, ciałami obcymi. By można je było pod tym kątem porównywać, stopień ochrony standaryzuje się i opisuje kodem IP. Składa się on z dwóch cyfr. Pierwsza z nich, od 0 do 6, oznacza stopień ochrony obudowy przed wnikaniem ciał stałych. Chodzi o cząstki pyłów, jak i większe ciała obce, z otoczenia albo wprowadzane do obudowy, celowo albo przypadkowo, przez użytkownika. I tak 1 oznacza ochronę przed obiektami większymi niż 50 mm (dłoń), 2 – większymi niż 12 mm (palec), 3 – większymi niż 2,5 mm (narzędzia i druty), a 4 – większymi niż 1 mm (drobne narzędzia i druty, gwoździe, śruby, większe owady). 5 gwarantuje pyłoodporność, a 6 pyłoszczelność.
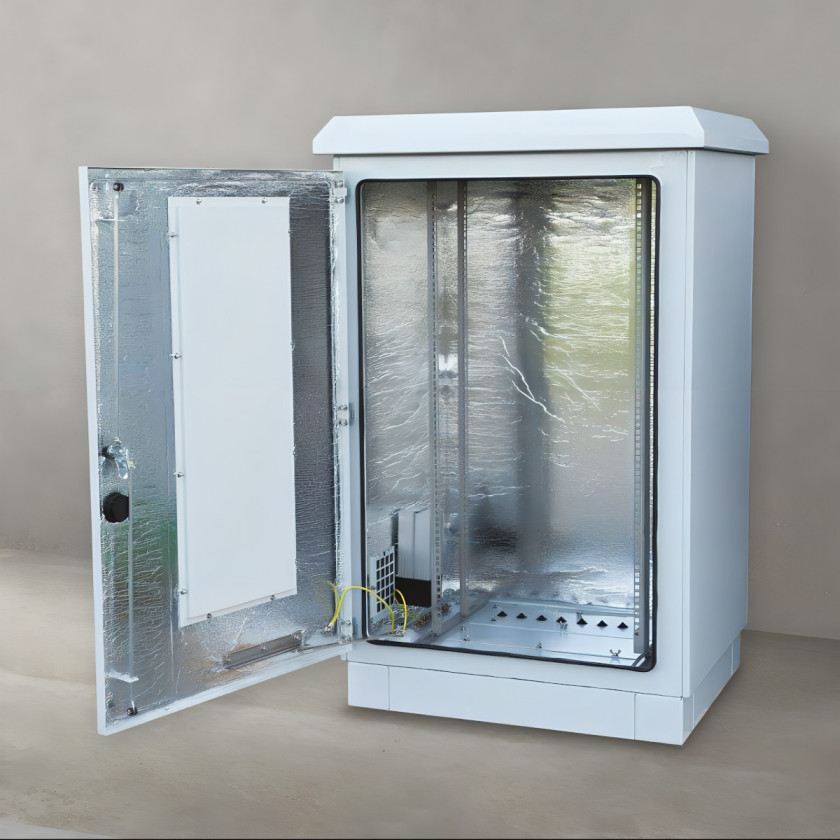
Druga cyfra, od 0 do 9, charakteryzuje z kolei stopień ochrony obudowy przed wnikaniem wilgoci. 1 oznacza ochronę przed kroplami wody padającymi pionowo, 2 – pod kątem 15°, 3 – pod kątem 60°, 4 – pod dowolnym kątem, 5 – przed strumieniem wody o małym ciśnieniu, a 6 – przed falą wody. 7 gwarantuje szczelność obudowy przy zanurzeniu przez 30 minut, 8 – przy zanurzeniu ciągłym. Dodatkowy kod IP69K charakteryzuje obudowy odporne na mycie strugą pod dużym ciśnieniem (80‒100 barów) i o wysokiej temperaturze (do +80°C). Przykładowo więc obudowa o stopniu ochrony IP58 ma zagwarantowaną pyłoodporność oraz szczelność przy zanurzeniu ciągłym, IP56 pyłoodporność i szczelność przy zalaniu falą wody, a IP67 pyłoszczelność i szczelność przy zanurzeniu czasowym.
Materiały uszczelek
Szczelność obudowy uzyskuje się przede wszystkim przez wybór właściwego materiału uszczelki. Należy ją również dokładnie dopasować do powierzchni części osłony oraz staranne zamocować. Uszczelki mogą mieć postać pasków, są wycięte w kształcie obrysu łączonych elementów lub są wylewane z zastygającego materiału na zabezpieczone przed korozją podłoże. Pierwsze są tanie, ale niestety na złączach, w rogach, szybko niszczeją. Zaletą wylewanych jest ciągłość na całym obwodzie i bardzo dobra przyczepność do podłoża. Są też tanie. Uszczelki wycięte w kształcie obrysu są z kolei zwykle nieco droższe. Materiał uszczelki powinien być odporny na te same czynniki środowiskowe, co obudowa.
Najpopularniejsze w tym zastosowaniu są: neopren (używany najczęściej), silikon, elastomery termoplastyczne, poliuretan i EPDM. Silikon wyróżnia się odpornością na promienie słoneczne i najszerszym zakresem temperatur pracy (–60°C... +170°C), ale jest droższy od pozostałych materiałów. Zaletą poliuretanów jest natomiast łatwość wytwarzania uszczelek o nieregularnych kształtach i najmniejsze odkształcenia przy ściskaniu. EPDM wyróżnia z kolei duża wytrzymałość na rozciąganie.
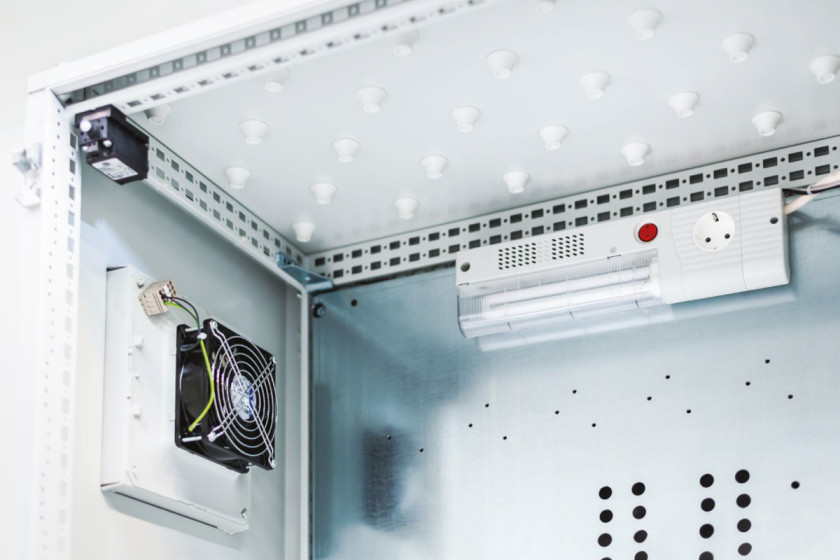
Kolor obudowy
Czynnikiem niekorzystnie oddziałującym na urządzenie jest również bezpośrednie nasłonecznienie, na które narażone są sprzęty montowane na zewnątrz budynków. By je chronić przed jego wpływem, w obudowach stosuje się różne rozwiązania. Przede wszystkim, ponieważ kolor obudowy ma bezpośredni wpływ na ilość pochłanianego promieniowania słonecznego, oferują je przeważnie w jasnych kolorach, silniej je odbijających niż te ciemniejsze.
Oprócz tego dostępne są obudowy w wersjach door-over-door, w których obudowa właściwa jest umieszczona w zewnętrznej, dodatkowej obudowie. Dzięki temu ta wewnętrzna nie jest wystawiona na bezpośrednie działanie promieniowania słonecznego. Konstrukcja ta ma także taką zaletę, że zewnętrza osłona stanowi dodatkową barierę do pokonania dla osób, które nie powinny mieć dostępu do urządzeń wewnątrz.
Podsumowanie
Wybór obudowy jest zazwyczaj ostatnim etapem projektowania urządzenia, co nie oznacza jednak, że najmniej istotnym. Podejmując decyzję w tym zakresie, pod uwagę trzeba wziąć wiele kwestii. Najważniejsze to: środowisko pracy i czynniki w nim występujące, wpływające na integralność i trwałość obudowy, jej bezpieczeństwo elektryczne i właściwości ekranujące, wymagania dotyczące chłodzenia (lub grzania), estetykę wykonania i cenę odniesioną do zakładanego czasu eksploatacji. Trzeba jednak mieć świadomość, że oszczędności początkowe osiągnięte kosztem materiału albo konstrukcji obudowy mogą generować długoterminowe wydatki z powodu problemów w pracy urządzenia spowodowanych wyborem niewłaściwej osłony.
Monika Jaworowska