Serwonapędy wykorzystuje się do regulacji położenia, prędkości, momentu obrotowego i różnych kombinacji tych trzech wielkości. Dla każdej realizuje się pętlę sterowania, która pozwala na ich śledzenie i korygowanie. Układ sterowania serwonapędem w związku z tym zwykle ma strukturę wielopętlową, w której pętle są w sobie zagnieżdżone.
Jaka jest funkcja pętli prądowej?
W trybie regulacji momentu obrotowego pracą silnika steruje pętla prądowa. Ponieważ jest on wprost proporcjonalny do prądu, sterownik na podstawie informacji o tym ostatnim pozyskuje informację o aktualnym momencie silnika. Tę wartość rzeczywistą następnie porównuje z wartością zadaną tej wielkości i dalej na tej podstawie wyznacza sygnał sterujący, który stosownie zmienia prąd dostarczany do silnika. Sterowanie momentem jest zwykle realizowane w pętli z regulatorem PI.
Moment obrotowy determinuje przyspieszenie silnika, które z kolei ma wpływ na prędkość oraz położenie. Dlatego pętla sterowania prądem jest w serwonapędach standardem. Poza tym kontrola momentu obrotowego jest wymagana w takich aplikacjach, jak sterowanie nawijaniem, w którym należy utrzymywać stałe naprężenie wstęgi materiału podczas jej nawijania, kiedy w miarę jak zwiększa się średnica rolki materiału, rośnie jej obciążenie i bezwładność. Kolejny przykład to formowanie wtryskowe, w którym do formy powinna być przykładana stała siła docisku.

Tryb kontroli prędkości
Jeżeli w danym systemie sterowania ruchem wymagane jest utrzymanie zadanej szybkości nawet przy zmianie obciążenia, serwonapęd pracuje w trybie regulacji prędkości. Wówczas kontrolowane i regulowane jest napięcie dostarczane do silnika. Jednocześnie, ponieważ zmiana prędkości silnika, w celu przyspieszenia lub zwolnienia wymaga odpowiednio wzrostu lub zmniejszenia momentu obrotowego, w trybie regulacji prędkości wymagana jest również praca w pętli prądowej.
Informacje o aktualnej prędkości obrotów zapewnia enkoder. Na ich podstawie wyznaczana jest różnica pomiędzy rzeczywistą a docelową wartością tej wielkości. To z kolei umożliwia obliczenie prądu (momentu obrotowego) potrzebnego do korekcji tej odchyłki prędkości silnika. Sterowanie nią jest również przeważnie realizowane w pętli z regulatorem PI.
Przykładami aplikacji, w których serwonapędy pracują w trybie regulacji prędkości, są: sterowanie przenośnikami, dozowanie, procesy obróbki, jak szlifowanie i polerowanie, w których obciążenie silnika jest zmienne, ale jego prędkość powinna być utrzymywana przez cały proces.
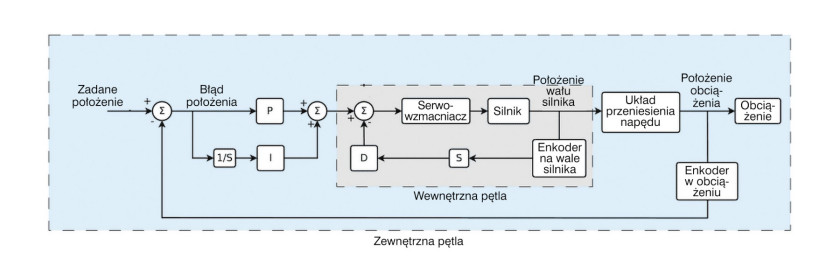
Pozycjonowanie
Serwonapędy mogą również działać w trybie pozycjonowania. To pozwala silnikowi przemieścić ładunek do określonej lokalizacji albo względem miejsca początkowego, albo w oparciu o jego położenie bezwzględne.
Aby zrealizować tryb regulacji położenia w serwosystemach, zwykle wymagane jest skorzystanie z trzech pętli sterowania: momentem obrotowym, prędkością oraz położeniem. Wynika to stąd, że prędkość silnika powinna być monitorowana, żeby można było wyznaczyć jego położenie, z kolei moment obrotowy powinien być monitorowany w celu określenia, ile prądu potrzebuje silnik, aby osiągnąć zadaną pozycję, bez niedoregulowania albo przeregulowania. Pętla regulacji położenia działa zazwyczaj w oparciu o regulator PI albo PID.
W pętli pozycjonowania, na podstawie zadanej pozycji, która jest porównywana z informacją o aktualnym położeniu, pozyskiwaną dzięki sprzężeniu zwrotnemu, jest wyznaczany sygnał różnicy. Staje się on wartością zadaną w pętli regulacji prędkości. W niej z kolei ta wartość zestawiana jest z rzeczywistą wartością prędkości zmierzoną przez komponent sprzężenia zwrotnego. Wyznaczona w taki sposób różnica staje się wartością zadaną w pętli regulacji momentu. Pętle te są zatem w sobie zagnieżdżone.
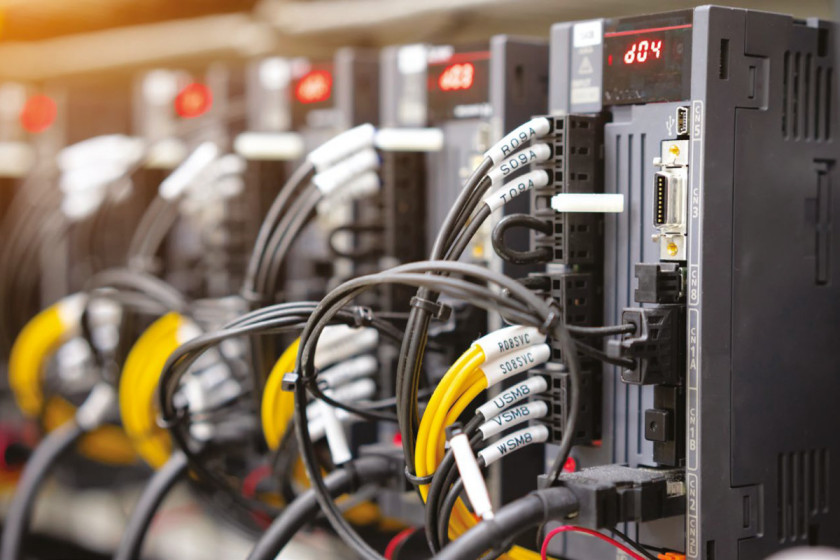
Czym jest pasmo przenoszenia?
Gdy występuje więcej niż jedna pętla sterowania łączy się je kaskadowo. Sterowanie prądem jest najbardziej wewnętrzną pętlą. Pętla sterowania prędkością jest dodawana wokół pętli prądowej. Pętla kontroli położenia jest dodawana wokół pętli prędkości, stając się tą najbardziej zewnętrzną.
Strojenie odbywa się w kolejności od wewnętrznej do zewnętrznej pętli, zatem najpierw dostrajana jest pętla prądowa, potem pętla regulacji prędkości, a jako ostania pętla regulacji położenia. Wiele zaawansowanych serwowzmacniaczy może przełączać się między trybami sterowania "w locie" – na przykład przechodząc z trybu prędkości do trybu momentu obrotowego podczas pracy systemu, bez jego destabilizowania czy zatrzymywania.
Ważny parametr pętli sterowania to pasmo przenoszenia. Jego szerokość odpowiada czasowi odpowiedzi systemu, będąc miarą tego, jak szybko reaguje on na zmieniające się polecenie wejściowe. Szerokość pasma przenoszenia pętli sterowania określa więc, jak szybko serowsystem może odpowiedzieć na zmianę kontrolowanego parametru: momentu obrotowego, prędkości albo pozycji.
W przypadku zagnieżdżenia pętli konieczne jest, aby odpowiedź pętli wewnętrznej była szybsza niż odpowiedź pętli zewnętrznej, w przeciwnym razie pętla wewnętrzna będzie miała niewielki wpływ lub nie będzie miała żadnego efektu. Najlepiej gdy pętla wewnętrzna ma pasmo przenoszenia 5‒10 razy większe niż pętla zewnętrzna. Oznacza to, że w typowym serwonapędzie pasmo przenoszenia pętli prądu powinno być 5‒10 razy większe od pasma przenoszenia pętli prędkości, zaś pasmo przenoszenia pętli prędkości musi być 5‒10 razy większe od tego parametru pętli położenia.
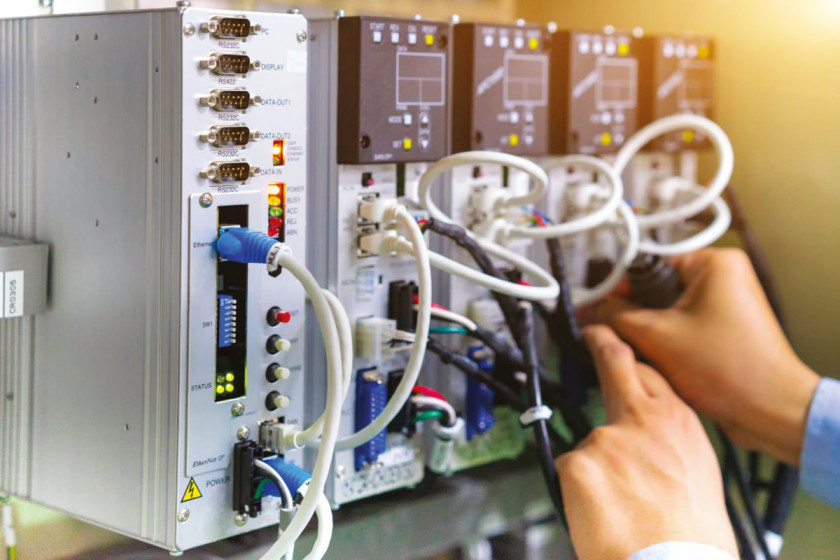
Podwójna pętla
Elementy mechaniczne i łączniki w układzie napędowym (śruby, sprzęgła) nie są idealnie sztywne i wprowadzają luzy. Powoduje to rozbieżności między informacją zwrotną o parametrach ruchu wału silnika a rzeczywistym przemieszczeniem obciążenia. Przez to nie jest osiągany cel sterowania, a napęd pracuje niestabilnie.
Rozwiązaniem jest wykorzystanie dwóch czujników sprzężenia zwrotnego: mierzącego ruch wału silnika oraz drugiego, który monitoruje obciążenie. Na tym polega sterowanie w podwójnej pętli. Realizuje się je na kilka sposobów.
W popularnym podejściu sterownik najpierw zamyka pętlę sterowania prędkością, która otrzymuje informację zwrotną z enkodera w silniku. Następnie zamykana jest pętla położenia w oparciu o sygnał zwrotny z enkodera w obciążeniu. Termin "sterowanie w podwójnej pętli" odnosi się właśnie do tych dwóch pętli, położenia i prędkości, które otrzymują bezpośrednie sprzężenie zwrotne z czujników, nawet jeżeli zrealizowana jest również trzecia wewnętrzna pętla prądowa do sterowania momentem.
Ważne, że w konfiguracji z podwójną pętlą odpowiedź pętli prędkości jest niezależna od sprzężenia zwrotnego od obciążenia, a tym samym rozdzielczości enkodera śledzącego jego przemieszczenie. Analogicznie odpowiedź pętli położenia jest niezależna od sygnału zwrotnego z enkodera na wale silnika.
Zwykle wykorzystuje się dwa enkodery obrotowe lub jeden obrotowy i jeden liniowy. Kombinacja obrotowo-liniowa jest najczęściej spotykana w systemach ruchu liniowego. W takim przypadku w silniku montuje się enkoder obrotowy, a enkoder liniowy umieszcza się w osi liniowej.
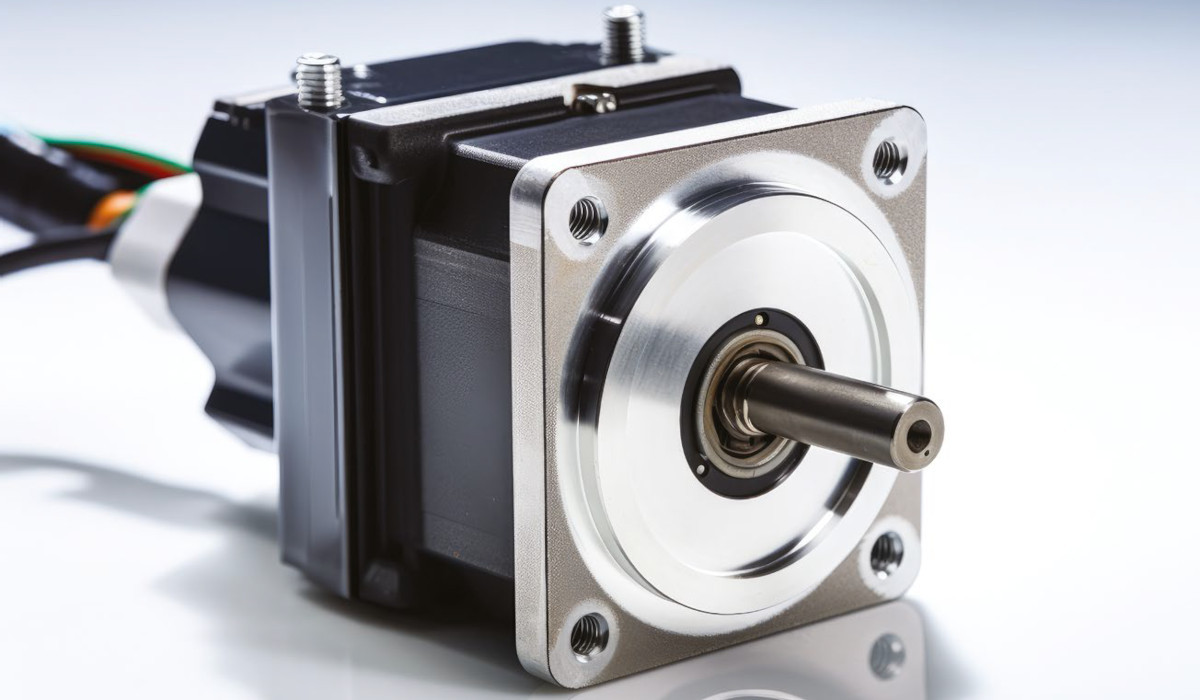
Monika Jaworowska