Jak wiadomo z fizyki, siła dynamiczna, inaczej niż statyczna, wiąże się z przyspieszeniem. Podobnie moment obrotowy jest statyczny, jeżeli nie towarzyszy mu przyspieszenie kątowe.
Przykładem statycznego momentu obrotowego wirującego jest ten przenoszony przez oś napędową samochodu w trakcie jazdy ze stałą prędkością, gdyż choć występuje obrót, nie ma przyspieszenia. Moment obrotowy wytwarzany przez silnik auta będzie natomiast statyczny, jak i dynamiczny w zależności od miejsca pomiaru. W przypadku tego mierzonego na wale korbowym wystąpią duże wahania dynamicznego momomentu obrotowego. Ten mierzony na wale napędowym będzie z kolei w zasadzie statyczny.
Kolejnym przykładem jest moment obrotowy wymagany do podniesienia szyb w samochodzie. Jest statyczny, ponieważ składnik dynamiczny ze względu na małe przyspieszenie i bezwładność korby będzie zaniedbywalnie mały w porównaniu z siłą tarcia podczas ruchu okna. Powyższe przykłady dowodzą, że trudno jest rozgraniczyć oba rodzaje momentu, o czym koniecznie należy pamiętać, wybierając metodę pomiaru.
Metody pomiarowe
W celu wykonania pomiarów metodą rotacyjną przetwornik umieszcza się pomiędzy elementami, które przenoszą moment obrotowy. Analogią jest włożenie przedłużki pomiędzy nasadkę a klucz nasadowy. Moment, który jest wymagany do obrócenia nasadki, będzie przenoszony bezpośrednio przez przedłużkę. W tym podejściu przetwornik znajduje się blisko źródła wielkości mierzonej. Dzięki temu unika się błędów pomiaru, których powodem są pasożytnicze momenty obrotowe, obciążenia zewnętrzne i elementy o dużej bezwładności obrotowej tłumiące momenty dynamiczne.
Wykorzystując tę metodę w praktyce, na przykład w samochodzie, dynamiczny moment obrotowy wytwarzany przez silnik można zmierzyć, wbudowując przetwornik pomiędzy wałem korbowym a kołem zamachowym. Ze względu na bezwładność obrotową charakterystyczną dla komponentów układu napędowego bezpośrednie pomiary metodą rotacyjną to często jedyny sposób prawidłowego pomiaru momentu dynamicznego. Aby z kolei zmierzyć statyczny moment obrotowy napędzający koła, przetwornik należy umieścić pomiędzy obręczą a piastą albo w wale napędowym.
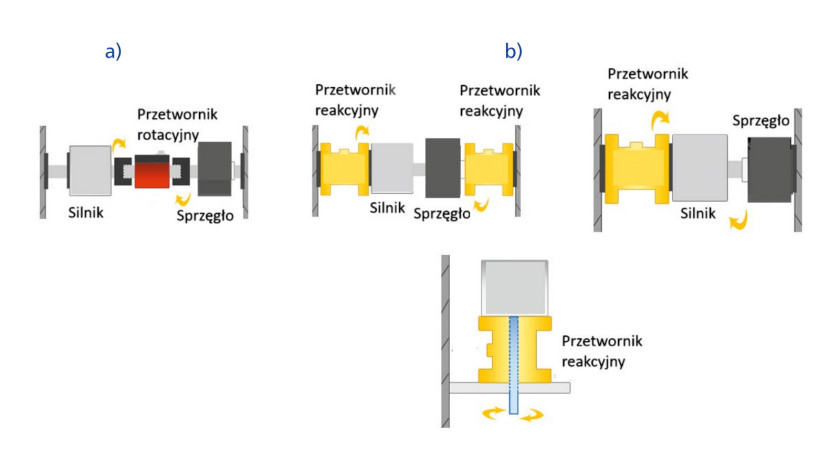
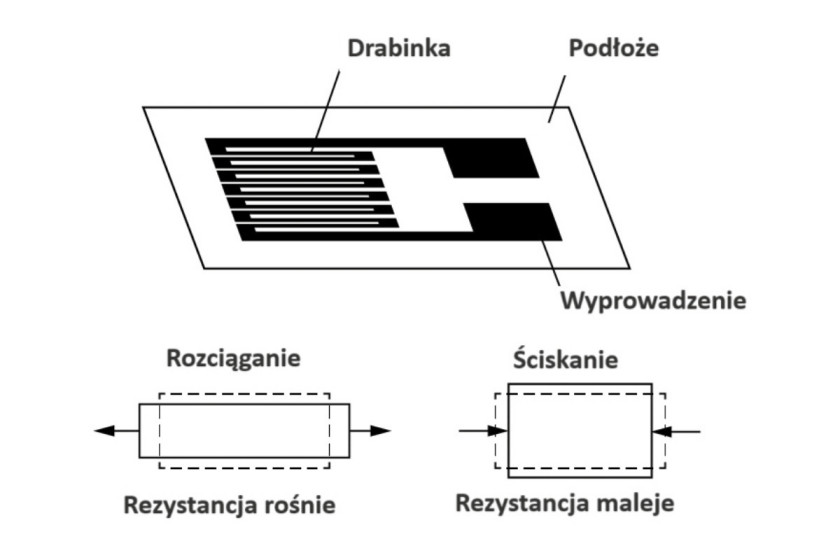
Alternatywą bezpośredniego pomiaru momentu obrotowego wytwarzanego przez silnik jest pomiar momentu, jaki jest wymagany, aby zapobiec jego obracaniu się, czyli momentu reakcji. Obie metody, rotacyjna i reakcyjna, zapewnią identyczne wyniki w przypadku statycznych pomiarów momentu obrotowego.
Przetworniki reakcyjne
Elementem pomiarowym w przetwornikach momentu obrotowego są tensometry. Są to czujniki, których rezystancja elektryczna zmienia się w zależności od przyłożonej do nich siły. Tensometry przekształcają odkształcenie, jakiemu ulegają pod wpływem siły w różnej postaci, na przykład ciśnienia, naprężania, ściskania, ciężaru czy momentu obrotowego w zmianę rezystancji, którą można zmierzyć.
Reakcyjny przetwornik momentu obrotowego typowo składa się z metalowego korpusu, do którego przyklejone są tensometry z folii metalowej. Trzon ten jest zwykle wykonany z aluminium lub stali nierdzewnej. Dzięki temu przetwornik uzyskuje dwie ważne właściwości. Po pierwsze metalowy korpus gwarantuje wytrzymałość również na duże momenty obrotowe. Oprócz tego dzięki temu materiałowi korpus zyskuje elastyczność, pozwalającą na minimalne odkształcenie oraz powrót do pierwotnego kształtu po ustaniu momentu obrotowego.
Po przyłożeniu momentu obrotowego metalowy trzon przetwornika działa jak „sprężyna” i ulega lekkiemu odkształceniu. Jeżeli nie zostanie przeciążony, powraca do swojego pierwotnego kształtu. W miarę odkształcania się korpusu tensometr również zmienia swój kształt, miejscami wydłużając się, a miejscami skracając. W konsekwencji zmienia się jego rezystancja elektryczna. To natomiast powoduje zmianę napięcia różnicowego w układzie mostka Wheatstone’a, która jest proporcjonalna do momentu obrotowego przyłożonego do przetwornika.
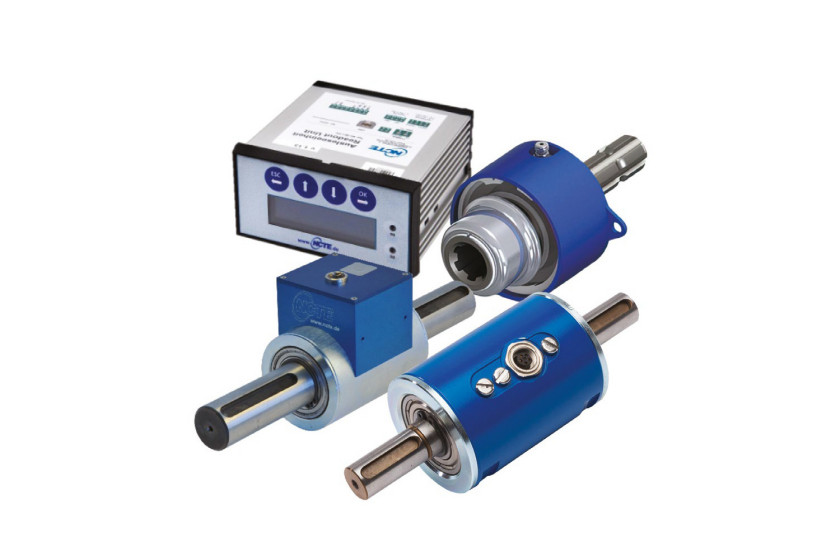
Rotacyjne przetworniki momentu
W przetworniku rotacyjnym czujnik tensometryczny przymocowuje się do obrotowego wału, który pod wpływem momentu obrotowego ulega nieznacznemu odkształceniu. Jego ugięcie się powoduje naprężenie w tensometrze, co zmienia jego rezystancję. Jak w przypadku przetwornika reakcyjnego tensometr (lub kilka czujników tego typu) pracuje w układzie mostka Wheatstone’a, który przekształca zmiany rezystancji w mierzone napięcie wyjściowe.
Przetworniki momentu obrotowego w wersji rotacyjnej wymagają połączenia czujnika na wale z elektroniką pomiarową. Najpowszechniej stosowaną metodą w tym zakresie jest wykorzystanie pierścieni ślizgowych. Połączenie składa się wówczas z zestawu pierścieni przewodzących, które obracają się wraz z czujnikiem oraz szeregu szczotek, które stykają się z pierścieniami i przekazują sygnały z sensorów. Jest to proste i ekonomiczne rozwiązanie sprawdzające się w szerokiej gamie zastosowań.
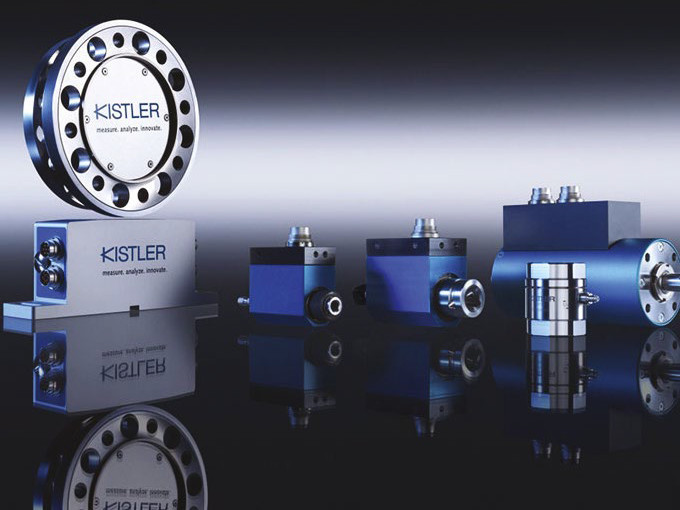
Szczotki i pierścienie ślizgowe (chociaż w mniejszym stopniu) to jednak elementy zużywające się o ograniczonej żywotności, więc nie sprawdzą się, jeśli nie będzie możliwa ich regularna konserwacja. Poza tym przy większej prędkości obrotowej szumy wpływają na jakość połączenia elektrycznego między pierścieniami a szczotkami. Maksymalna dopuszczalna prędkość obrotowa pierścienia ślizgowego jest określona przez prędkość powierzchniową na styku szczotka–pierścień. Będzie zatem mniejsza w przypadku większych czujników do pomiaru większych momentów obrotowych ze względu na fakt, że pierścienie ślizgowe będą musiały mieć większą średnicę, a więc będą miały większą prędkość powierzchniową przy danej prędkości obrotowej. Typowo maksymalne prędkości sięgają 5000 obr./min w przypadku czujników momentu obrotowego o średniej wydajności.
Poza tym trzeba pamiętać, że połączenie szczotka–pierścień jest źródłem momentu oporu, który może stanowić problem, szczególnie w przypadku pomiarów o bardzo małej przepustowości albo zastosowań, w których moment napędowy będzie zbyt mały, by pokonać opór szczotki.
Rotacyjne przetworniki momentu obrotowego muszą być też zaprojektowane tak, aby eliminować obciążenia pozaosiowe (boczne, inaczej momenty obce). Opcjonalnie integruje się je z enkoderami mierzącymi kąt i prędkość obrotów wału.
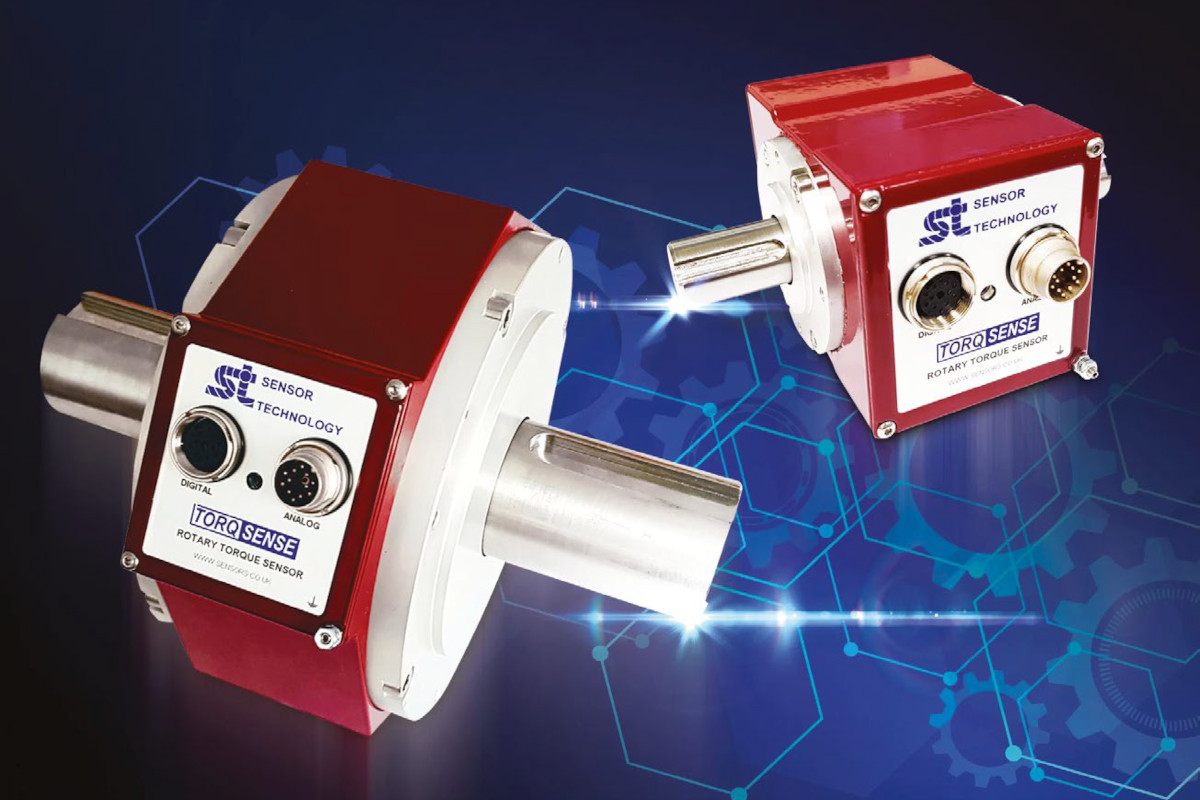
Monika Jaworowska