W planowanym czasie produkcji nie uwzględnia się przerw, w których nie zamierzano prowadzić produkcji, na przykład okresów zamknięcia zakładu, tych, w których nie ma zamówień czy przerw obiadowych itp. Jeśli całkowity planowany czas produkcji jest w pełni produktywny, wskaźnik OEE wynosi 100%. Oznacza to osiągnięcie stuprocentowej: jakości (bez produktów wybrakowanych), wydajności (produkcja tak szybka, jak to tylko możliwe) i dostępności sprzętu (bez nieplanowanych przestojów). Jest to sytuacja idealna.
Wskaźnik efektywności na poziomie 85% jest uważany za standard. Przeważnie taka wartość jest przyjmowana za cel do osiągnięcia w dłuższej perspektywie. Im mniejsza wartość wskaźnika OEE, tym większe możliwości w zakresie jego poprawy. Jego typowa wartość to 60%. Efektywność na poziomie 40% jest najczęstsza w przypadku, gdy dopiero rozpoczyna się śledzenie tego wskaźnika. Przy OEE na tak niskim poziomie, zwykle wdrażając proste rozwiązania, szybko można zauważyć poprawę.
Jak policzyć OEE?
Wskaźnik efektywności jest obliczany jako iloczyn trzech składników: dostępności A (Availability) i wydajności P (Performance) sprzętu oraz jakość Q (Quality) produkcji:
OEE = A × P × Q (1)
Dostępność jest definiowana jako stosunek czasu operacyjnego do planowanego czasu produkcji:
A = (czas operacyjny / planowany czas produkcji) × 100% (2)
Czas operacyjny to planowany czas produkcji pomniejszony o okresy nieplanowanych przestojów, podczas których proces produkcyjny powinien był trwać, ale nastąpiła niespodziewana przerwa:
czas operacyjny = planowany czas produkcji – czas nieplanowanych przestojów (3)
Dostępność uwzględnia zdarzenia, które wstrzymują produkcję na tyle długo, żeby możliwe było wyśledzenie przyczyny przestoju (zwykle kilka minut). Są to na przykład awarie sprzętu, niedobory materiałów, dłuższe niż zakładano przezbrojenia maszyn.
Kolejny składnik to wydajność, która bierze pod uwagę czynniki powodujące, że sprzęt pracuje wolniej, niż mógłby, gdyby osiągał swoją maksymalną prędkość. Do takich zalicza się: zużycie się jego części, surowce niespełniające norm, ich nieprawidłowe podawanie i blokowanie się. Jeżeli od czasu operacyjnego odejmiemy okres wolniejszej pracy, uzyskany czas operacyjny netto. Stosunek tej ostatniej wielkości do czasu operacyjnego określa wydajność sprzętu:
P = (czas operacyjny netto / czas operacyjny) × 100% (4)
Q to składnik uwzględniający to, że poza wyrobami niewymagającymi poprawek produkowane są też takie, które nie spełniają standardów i są niszczone albo wymagają dodatkowej obróbki. By ten wskaźnik obliczyć, należy odnieść liczbę wybrakowanych produktów do znamionowej wydajności sprzętu. To pozwala na wyznaczenie czasu, który stracono na ich produkcję. Po odjęciu go od czasu operacyjnego netto uzyskujemy czas dobrej jakościowo produkcji (czas w pełni produktywny). Jego stosunek do czasu operacyjnego netto określa składnik Q:
Q = (czas dobrej jakościowo produkcji / czas operacyjny netto) × 100% (5)
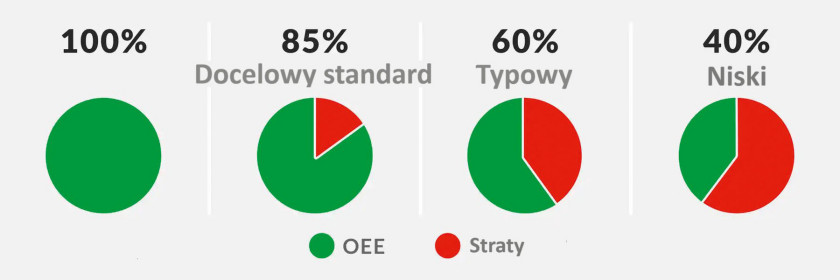
Przykład obliczeń
Jako przykład obliczymy wskaźnik efektywności sprzętu dla jednej zmiany trwającej 8 h, czyli 480 minut. W jej trakcie zaplanowane są dwie przerwy trwające po 30 minut każda. Przyjmujemy, że średnio w czasie każdej zmiany sprzęt pracuje wolniej przez kwadrans. Znamionowa wydajność maszyny wynosi 25 sztuk na minutę. Średnio w trakcie każdej zmiany łącznie przez 30 minut występuje nieplanowany przestój, a 25 sztuk produktu nie przechodzi kontroli jakości z wynikiem pozytywnym.
W pierwszym kroku obliczamy planowany czas produkcji, który wynosi 420 minut (480 – 60 minut przerw = 420). Na tej podstawie możemy wyznaczyć czas operacyjny, który jest równy 390 minut (420 – 30 minut nieplanowanych przestojów = 390). Te dwie wielkości pozwalają na obliczenie dostępności, która wynosi 92,86% (390 · 100% / 420 = 92,86%).
Czas operacyjny netto w tym przypadku wynosi 375 minut (390 – 15 minut wolniejszej pracy = 375). Wydajność zatem jest na poziomie 96,15% (375 · 100% / 390 = 96,15%).
W trakcie każdej zmiany średnio 1 minuta jest marnowana na produkcję wyrobów, które nie spełniają standardów jakości (25 sztuk / 25 sztuk/minutę = 1 minuta). Czas dobrej jakościowo produkcji wynosi zatem 374 minuty (375 – 1 = 374). Na tej podstawie składnik Q jest równy 99,73% (374 · 100% / 375 = 99,73%). Ostatecznie wskaźnik OEE wynosi 89%.
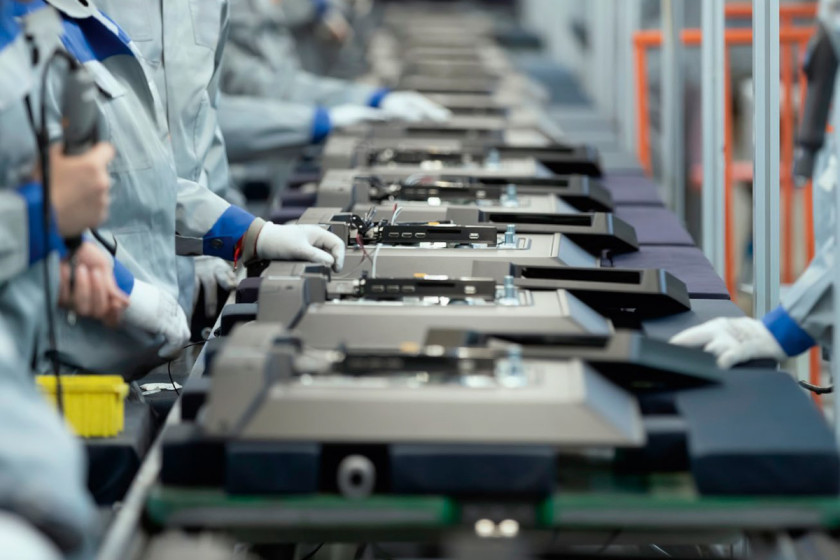
Zacznij od danych
Na to, na ile wyznaczony w ten sposób wskaźnik OEE odzwierciedla faktyczną efektywność danego sprzętu, kluczowy wpływ ma sposób pozyskiwania danych stanowiących podstawę dla obliczeń. W tym zakresie warto zainwestować w rozwiązania zautomatyzowane, ponieważ ręczne gromadzenie niezbędnych informacji ma liczne ograniczenia.
Przede wszystkim nie zapewnia w nie wglądu w czasie rzeczywistym ani precyzji i szczegółowości, jakie może zagwarantować automatyczny system rejestracji danych. Poza tym zwalniając personel z obowiązku osobistego raportowania, ich uwagę przekierowuje się na inne zadania. To ostatecznie zwykle skutkuje ich większą wydajnością.
Generalnie ręczne zbieranie informacji potrzebnych do obliczenia wskaźnika efektywności OEE, jak dane o przestojach, w najlepszym razie może dać ogólny obraz efektywności sprzętu. W najgorszym może stworzyć mylne wyobrażenie o jego działaniu.
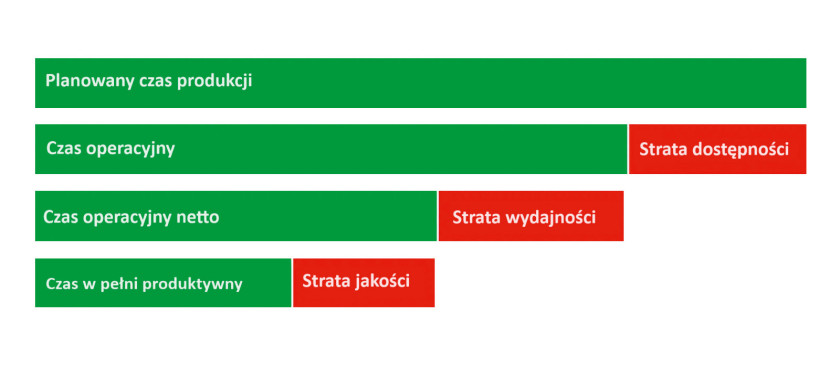
Zbieranie informacji...
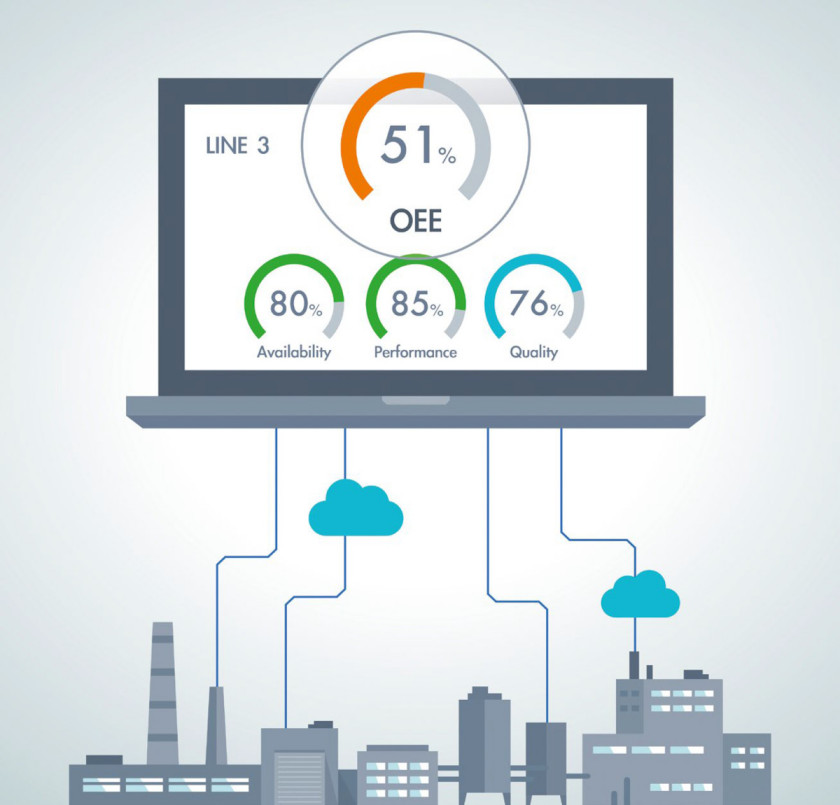
Osobiste gromadzenie danych przez pracowników może być nieefektywne i niewiarygodne z kilku powodów. Jeżeli za odnotowywanie na przykład wystąpienia przestoju jest odpowiedzialna ta sama osoba (albo zespół), której zadaniem jest rozwiązanie problemu, nie można wykluczyć, że skupiając się na tym celu później, już po fakcie, raportując o działaniu linii produkcyjnej może nie odnotować przerwy w jej działaniu z różnych powodów. Ponadto nie można oczekiwać, że taka osoba zauważy i zaraportuje o wszystkich krótkotrwałych na przykład jednominutowych przestojach. Niestety te w trakcie jednej zmiany mogą występować często i chociaż ze względu na czas trwania oddzielnie są nieodczuwalne, ostatecznie mogą się zsumować w długą przerwę. Ta może być oznaką poważnego problemu i mieć duży wpływ na wypadkową efektywność.
Osobiste nadzorowanie występowania przestojów w rozległych liniach technologicznych jest również wyczerpujące fizycznie. Poza tym śledzenie przerw w produkcji przez pracowników nie dostarcza z rzetelnością porównywalną do tej systemów automatycznego raportowania informacji o innych ważnych dla efektywności zdarzeniach i wskaźnikach (spowolnieniach, czasach powrotu do pełnej prędkości podczas rozruchu po przezbrojeniu, maksymalnej osiągalnej wydajności).
...i ich interpretacja
Koszt wdrożenia automatycznych systemów rejestracji parametrów maszyn stale spada. Przyczynia się do tego głównie rozwój Internetu Rzeczy. Dzięki temu urządzenia wyposaża się w coraz więcej czujników monitorujących ich stan i wydajność oraz interfejsy komunikacyjne, za pośrednictwem których dane są transmitowane do repozytoriów, gdzie są poddawane analizie.
Postępowi w dziedzinie gromadzenia danych potrzebnych do wyznaczenia wskaźnika efektywności dorównuje tempo rozwoju narzędzi do ich przetwarzania i interpretowania. Głównym wyzwaniem w tym przypadku jest to, że informacje te zwykle pochodzą z różnych źródeł (systemy zarządzania produkcją, Internet Rzeczy) – na przykład dane o przestojach z systemów MES, a ustawienia konfiguracyjne maszyn z historii procesu. Z powodu ich rozproszonego charakteru trudno jest znaleźć między nimi korelacje bez złożonego i czasochłonnego manipulowania tymi danymi. Naprzeciw temu wyzwaniu wychodzą dostawcy narzędzi analitycznych, które zapewniają dostęp do danych z wielu źródeł z poziomu centralnego repozytorium.
Częste błędy
Jeśli osiągnięcie określonego wskaźnika efektywność jest traktowane jako cel sam w sobie, pojawia się pokusa manipulowania danymi, w oparciu o które oblicza się OEE. Przykładowym sposobem na zawyżenie tego parametru jest błędne sklasyfikowanie niespodziewanych przestojów w produkcji jako zaplanowanych przerw.
Ważna jest też prawidłowa interpretacja tego parametru – choć OEE wyraźnie wskazuje na to, co jest z maszyną nie w porządku, nie ujawnia dlaczego tak się dzieje. Rzeczywiste korzyści ze śledzenia tego wskaźnika zapewnia dopiero określenie przyczyn pogorszenia się jej dostępności, wydajności i/lub jakości produkcji. Dopiero ich znajomość pozwoli na podjęcie działań naprawczych, a w efekcie poprawę wskaźnika OEE.
Trzeba też pamiętać, że wskazuje on na potencjał lokalnej optymalizacji efektywności pojedynczej jednostki produkcyjnej, zaś ostatecznym celem powinno być zawsze ulepszenie całego systemu. To jednak wymaga wzięcia pod uwagę szerszego kontekstu.
Z drugiej strony nie ma sensu obliczanie wskaźnika OEE dla całego zakładu produkcyjnego. Taka wartość, choć charakteryzuje wypadkową efektywność, nie wskaże na żadne konkretne możliwości wprowadzenia ulepszeń. Tych najlepiej szukać od najniższego poziomu operacyjnego w górę.
Nie warto również ulegać pokusie porównywanie ze sobą wskaźników OEE dla różnych zasobów produkcyjnych. Zestawianie wskaźników efektywności ma sens wyłącznie wówczas, gdy ocenia się równoważne jednostki, które są wykorzystywane do wytwarzania tego samego produktu w taki sam sposób.
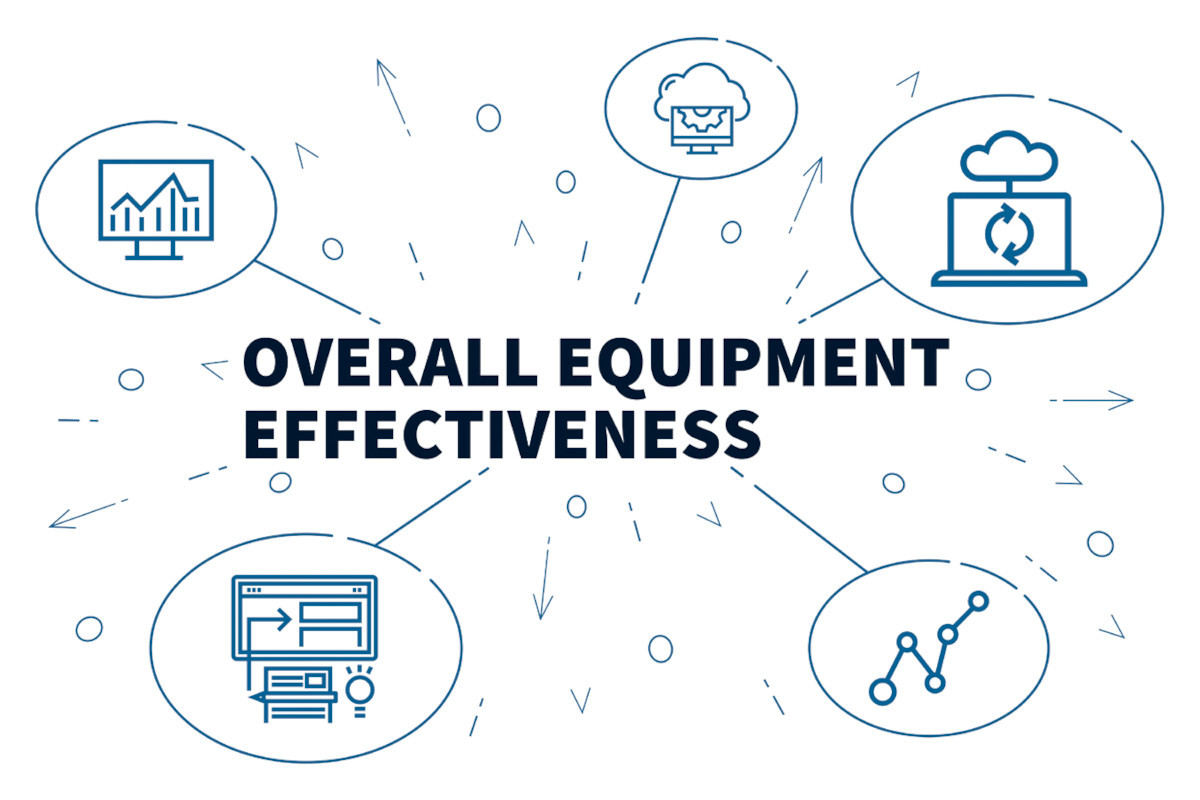
Monika Jaworowska