MTTF (Mean Time To Failure), czyli średni czas do awarii – to wskaźnik, który określa w godzinach średni czas, przez jaki nienaprawialny zasób będzie działał przed prawdopodobnym zepsuciem się. Awaria oznacza w tym przypadku wszelkie zakłócenia na tyle znaczące, że powodują one nieplanowany przestój albo uniemożliwiają działanie zasobu zgodnie z jego przeznaczeniem. Wskaźnik MTTF dotyczy jedynie urządzeń i komponentów, których nie można naprawić. W związku z tym jest interpretowany jako ich średnia żywotność. Zasoby nienaprawialne to często niedrogie, łatwe do wymiany elementy, jak łożyska, rolki przenośników, pasy napędów, które szybko się zużywają w miarę użytkowania.
Im dłuższy MTTF, tym rzadziej zespół utrzymania ruchu musi interweniować, aby wymienić część, która się zepsuła. Ogranicza to drogie, nieplanowane przestoje. Nierzadko bowiem zdarza się, że wadliwy element, który kosztuje grosze, wymusza wyłączenie maszyny wartej tysiące złotych. To z kolei zatrzymuje całą produkcję i powoduje straty sięgające setek tysięcy i więcej.
Jak wyznaczyć MTTF?
W obliczeniach średniego czasu do awarii wykorzystuje się dane archiwalne o tym, jak długo części działały, zanim się zepsuły. Informacje takie należy zebrać dla grupy identycznych podzespołów od tego samego producenta.
Jeżeli na przykład porównujemy łożyska, trzeba się upewnić, że są tego samego typu – na przykład, że wszystkie są łożyskami kulkowymi, mają taką samą graniczną prędkość obrotową i jednakowy system uszczelnień. Przykładowo, jeśli mamy pięć łożysk, które pracowały przez: 20, 25, 35, 40, 27 godzin, po podzieleniu sumy czasu ich działania przez 5, otrzymamy MTTF tego konkretnego typu łożysk równy 29,4 godziny.
Inny przykład – załóżmy, że analizujemy żywotność pomp obiegowych. Do tej pory w zakładzie zepsuły się cztery takie same modele pomp tego typu określonej marki. Pierwsza uległa awarii po dziesięciu godzinach, druga po dwunastu, trzecia pompa obiegowa działała zaledwie sześć godzin, zaś czwarta zepsuła się już po ośmiu. Ich sumaryczny czas pracy wyniósł zatem 36 godzin. Po podzieleniu go przez 4 wiemy, że pompy obiegowe tego typu, od tego konkretnego producenta, w razie wybrania danego modelu będą wymagały wymiany średnio co 9 godzin.
W przypadku komponentów o dłuższej żywotności i dużych maszyn zebranie danych archiwalnych o awariach jest trudne. W związku z tym trzeba zwykle bazować na wskaźniku MTTF, który podaje ich producent w danych katalogowych.
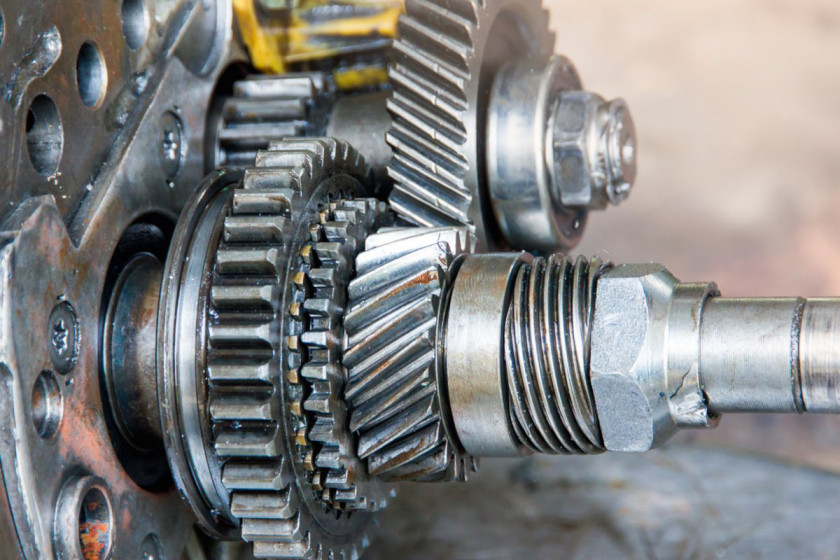
Jakie ma znaczenie MTTF?
MTTF jest wskaźnikiem niezawodności. Jego mała wartość może być wskazówką, że powinno się rozważyć zmianę dostawcy lub zakup części lepszej jakości, zwykle droższych, w zamian zyskując dłuższy średni czas do awarii, a w efekcie oszczędności w dalszej perspektywie. Generalnie ten parametr powinien być zawsze jednym z decydujących przy podejmowaniu decyzji zakupowych.
Wiedza o tym, kiedy można się spodziewać, że dany komponent się zepsuje, pozwala efektywniej zarządzać jego zapasami. Umożliwia to zaplanowanie zamówień części zamiennych, aby były już dostępne wtedy, gdy oczekujemy, że mogą się okazać potrzebne. Poza uniknięciem ich niedoboru, zapobiec można również zgromadzeniu ich w nadmiarze. Nadrzędnym celem powinno być zawsze posiadanie minimalnej wymaganej liczby części zapasowych aby niepotrzebnie nie "zamrażać" w nich środków ani nie podwyższać kosztów ich magazynowania. Znajomość MTTF pozwala też na rozplanowanie harmonogramów konserwacji zapobiegawczej, w ramach której przez czyszczenie i smarowanie można spróbować wydłużyć żywotność nienaprawialnych części, i umożliwia przygotowanie się na wystąpienie ich awarii, by uniknąć długich przestojów. Średni czas do awarii jest poza tym ściśle związany z innym wskaźnikiem, MTBF (Mean Time Between Failures), który w przypadku maszyn o kluczowym znaczeniu dla ciągłości pracy zakładu można znacząco wydłużyć, zaopatrując je w części zapasowe o jak największym MTTF.
MTBF
MTBF, czyli średni czas pomiędzy awariami określa, w jakich mniej więcej odstępach czasu dany zasób się psuje. Przykładowo, jeżeli jest równy 1000 godzin, dane urządzenie/komponent przez prawie 42 dni powinien działać bezproblemowo, przy założeniu, że pracuje 24 godziny na dobę. Im większa wartość tego wskaźnika, tym większa niezawodność. W przeciwieństwie do MTTF, MTBF ma zastosowanie wyłącznie do zasobów nadających się do naprawienia.
Ważne, żeby pamiętać, że średni czas między awariami nie jest wartością stałą, ale zmienia się w miarę starzenia się urządzenia/komponentu, którego dotyczy. Na wczesnym etapie jego eksploatacji prawdopodobieństwo awarii jest dość wysokie. Przez większość okresu użytkowania współczynnik awaryjności nie zmienia się znacząco. Dopiero, kiedy zbliża się do końca żywotności, to, że się zepsuje, znowu jest bardziej prawdopodobne. Dodatkowo MTBF nie uwzględnia nieprzewidzianych zdarzeń, które mogą wystąpić w miarę starzenia się sprzętu.
Jak obliczyć MTBF?
MTBF jest wyznaczany dla okresu, w którym nastąpiło kilka awarii, jako średnia arytmetyczna. W związku z tym dla zasobu najpierw należy określić całkowitą liczbę godzin operacyjnych w danym przedziale czasowym, którą następnie dzieli się przez liczbę awarii, które wystąpiły w tym okresie.
Przykładowo, pewien sprzęt produkcyjny był użytkowany przez 10000 godzin przez jeden rok. W tym czasie zepsuł się 10 razy. Jego MTBF wynosi więc 1000 godzin.
Inna maszyna była w sumie eksploatowana przez 2000 godzin w ciągu jednego roku. Przez ten czas niestety pięć razy trzeba było ją wyłączyć, ponieważ się zepsuła. W rezultacie średni czas między awariami dla tego urządzenia wynosi 400 godzin.
MTBF jest zwykle wyznaczany dla okresu, w którym nastąpiło wiele awarii pojedynczego zasobu albo doszło do pojedynczych awarii wielu zasobów tego samego typu, tak aby można było obliczyć średnią arytmetyczną. Przykładowo, trzy maszyny pracowały przez 100 godzin każda. Całkowity czas ich eksploatacji to więc 300 godzin. Przez ten czas zepsuły się sześć razy. Można w związku z tym oczekiwać, że ta grupa maszyn będzie działać przez 50 godzin bez awarii.
Ważne, aby zbytnio nie polegać na szacunkach MTBF podawanych w specyfikacji sprzętu. Wynika to stąd, że na jego awaryjność w czasie użytkowania wpływa wiele czynników, m.in: prawidłowość montażu, regularność konserwacji, błędy obsługi, jakość części zamiennych, większe obciążenie w wyniku zmian w produkcji.
Podobnie jak w przypadku MTFF, znajomość MTBF pozwala przygotować się na nieprzewidziane okoliczności, które towarzyszą awariom, lepiej planować konserwacje i zarządzać zapasami części zamiennych. Duża awaryjność może też świadczyć o nieprawidłowej konserwacji, nieskuteczności napraw, niskiej jakości części zapasowych, nieprawidłowej obsłudze urządzenia.
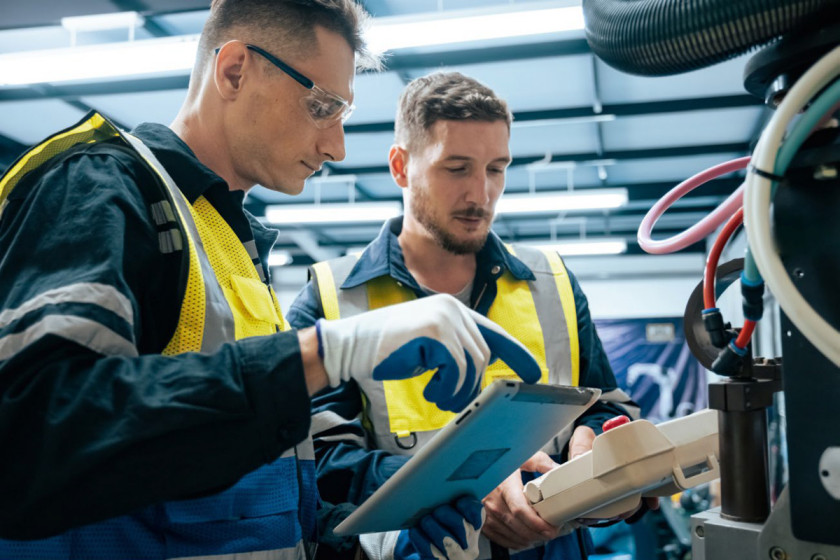
MTTR
MTTR (Mean Time To Repair), czyli średni czas naprawy, to wskaźnik określający, jak szybko zespół ds. utrzymania ruchu typowo reaguje na nieplanowane awarie sprzętu i go reperuje. Jest to sumaryczny czas od początku incydentu do momentu ponownego uruchomienia urządzenia. Obejmuje: powiadomienie techników o wystąpieniu awarii, diagnozowanie przez nich problemu, jego rozwiązanie, w tym w zależności od specyfiki sprzętu jego demontaż, montaż, wypoziomowanie, zresetowanie, przetestowanie, aż do ponownego włączenia. Nie jest w to natomiast wliczany czas oczekiwania na zamówione części zamienne. MTTR nie uwzględnia też planowanych przerw konserwacyjnych lub wyłączeń.
Średni czas naprawy jest wyznaczany jako całkowity czas nieplanowanej konserwacji podzielony przez całkowitą liczbę napraw. Przykładowo jeżeli mamy pompę, która popsuła się cztery razy w ciągu jednego dnia roboczego i technicy spędzili łącznie godzinę, aby ją naprawić, MTTR wyniesie 15 minut (60 minut / 4).
Kolejny przykład: załóżmy, że pewna maszyna uległa trzem awariom w ciągu tygodnia. Naprawa pierwszej usterki zajęła personelowi dwie godziny, drugiej trzy godziny, a trzeciej 1,5 godziny. Aby obliczyć MTTR, sumujemy czas reperacji (2 + 3 + 1,5 = 6,5 godziny) i dzielimy go przez liczbę napraw (3), co daje średni czas usuwania usterki wynoszący około 2,17 godziny.
Jak poprawić MTTR?
Analiza wskaźnika MTTR pozwala na ocenę efektywności programu konserwacji zapobiegawczej. Jeżeli na przykład średni czas naprawy danego zasobu wydłuża się, znaczyć to może, że działania podejmowane prewencyjnie, jak smarowanie i czyszczenie, nie są skuteczne. Poza tym znajomość wskaźnika MTTR jest pomocna przy decydowaniu o tym, czy wciąż jeszcze opłaca się naprawiać czy lepiej już zastąpić dany sprzęt nowym. Jeśli jego reperacja zajmuje coraz więcej czasu, bardziej ekonomiczna będzie jego wymiana.
Średni czas naprawy można skrócić na kilka sposobów, przyspieszając poszczególne etapy wliczane w całkowity czas reperacji. Okres od wystąpienia awarii do momentu, w którym technicy dowiadują się o problemie, pomaga skrócić m.in. wdrożenie zdalnego monitoringu i skuteczniejszych metod powiadamiania personelu o wystąpieniu sytuacji awaryjnej. Z kolei krótszy czas diagnozowania i rozwiązywania problemu można osiągnąć dzięki standaryzacji procedur postępowania, szkoleniom i zadbaniu o to, aby części zamienne i potrzebny do naprawy sprzęt były "pod ręką".
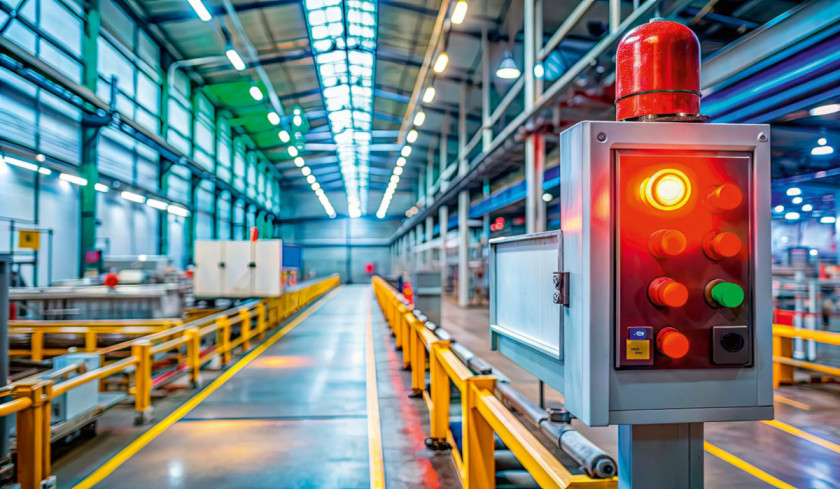
Monika Jaworowska