METODY MECHANICZNE
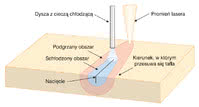
Rys. 1. Ilustracja jednej z metod cięcia szklanych paneli laserem
Mechaniczne cięcie szkła polega na zarysowaniu jego powierzchni twardym, ostrym narzędziem (na przykład ostrzem diamentowym), a następnie przyłożeniu siły, która spowoduje rozejście się tego pęknięcia wzdłuż całej grubości szkła. Metoda ta, zwłaszcza w przypadku bardzo cienkich płyt szklanych, ma kilka wad. Przede wszystkim w otoczeniu rysy powstają licznie mikropęknięcia, przez co mechaniczne cięcie bardzo cienkiego szkła (o grubości około milimetra) jest bardzo trudne.
Oprócz tego na krawędziach szkła powstają duże naprężenia, często też brzegi nie są dokładnie prostopadłe do powierzchni tafli. W efekcie, aby zapobiec późniejszemu pękaniu tafli, konieczna jest obróbka wykończeniowa - taka jak szlifowanie krawędzi. Dodatkowo szkło należy oczyścić z okruchów, które powstają, gdy ono pęka.
CIĘCIE SZKŁA LASEREM
W przypadku metod laserowych jako przykłady podać można dwie sytuacje cięcia cienkiego szkła laserem. Pierwsza przeznaczona jest głównie do tafli o grubości od 0,3 do 0,7mm. Polega na ogrzaniu promieniem lasera powierzchni szkła wzdłuż linii cięcia, a następnie na szybkim schłodzeniu tafli cieczą lub powietrzem z dyszy (rys. 1). Szok termiczny, jaki taka sekwencja zdarzeń wywołuje, skutkuje pękaniem szkła - typowo do głębokości 100 mikrometrów.
Następnie po powierzchni szklanej płyty przesuwa się wałek. Pod wpływem jego nacisku pęknięcie rozchodzi się wzdłuż całej grubości szkła. Alternatywnym rozwiązaniem przeznaczonym dla bardzo cienkich podłoży o grubości rzędu 0,2mm i mniej jest kilkukrotne wolniejsze nagrzewanie laserem linii cięcia do momentu przecięcia szklanej płytki.
Maszyny do cięcia - przegląd rozwiązańBezkontaktowe maszyny tnące dostępne są w różnych odmianach. Spotkać można zarówno ręcznie sterowane urządzenia do cięcia na przykład plazmą lub tlenowego, jak i komputerowo sterowane automatyczne systemy tnące na przykład wodą lub laserem. Te ostatnie dostępne są w różnych konfiguracjach, w zależności od tego, czy ich przeznaczeniem jest cięcie wzdłuż jednej osi, wycinanie płaskich detali czy obróbka obiektów w przestrzeni trójwymiarowej. Przykładem maszyn pierwszego typu są urządzenia pracujące jako krajarki do papieru. Przycinają one obrabiany materiał wzdłuż, by uzyskał określoną szerokość. Maszyny tego typu pracują często w połączeniu z krajalnicami poprzecznymi - na przykład w porcjowaniu ciast. Cięcie 2DMaszyny do wycinania płaskich detali z przesuwem w osi X i Y pozwalają z kolei uzyskać dowolny wzór. Najczęściej urządzenia tego typu dostępne są jako konstrukcje wspornikowe lub bramowe (fot. 1). Większość z nich ma też możliwość regulowania wysokości dyszy (ruchoma, programowalna oś Z). Poza głowicą ich częścią są komponenty takie jak stół wyposażony na przykład w stalową kratownicę do podtrzymywania obrabianego materiału, serwomotor, prowadnice liniowe oraz układ sterowania numerycznego ruchem dyszy. W przypadku waterjetów niezbędny jest też zbiornik na wodę, a w maszynach do cięcia ścierniwem także podajnik materiału ściernego.
Cięcie 3DW zakresie cięcia 3D funkcjonują dwa rozwiązania: dyszę tnącą można zamontować na ramieniu robota lub wykorzystać przestrzenną głowicę tnącą, która ma pięć (lub więcej) osi ruchu. Przykładem urządzenia pierwszego typu jest stanowisko do cięcia laserem Jenoptic-Votan BIM (Beam in Motion) zaprojektowane wspólnie przez firmy Jenoptik oraz Stäbli Robotics (fot. 2 i 3). Jego głównym komponentem jest ramię robota o sześciu stopniach swobody, manipulujące głowicą laserową w przestrzeni roboczej o wymiarach 1,4 × 0,7 × 0,5 metra. Stanowisko wykorzystywane jest głównie do przecinania metali i elementów z tworzyw sztucznych, w tym wyrównywania krawędzi detali wytwarzanych w formach wtryskowych. Dwa w jednymPopularnym rozwiązaniem jest łączenie w jednym urządzeniu dwóch metod cięcia. Najczęściej spotykanym połączeniem są wycinarki wodne (w tym wodą ze ścierniwem) z jedną z metod termicznych. W związku z tym dostępne są wycinarki laserowo-wodne, tlenowo-wodne oraz plazmowo-wodne, na przykład Plasma Dual-Line firmy Soitaab, którą oferuje krakowskie przedsiębiorstwo Rafela oraz wycinarka Trium WPC (fot. 4) dostępna w asortymencie krakowskiej firmy Stigo. |
METODY BEZKONTAKTOWE A MECHANICZNE
Opisane metody cięcia laserem nie powodują mikropęknięć, odprysków na krawędziach oraz naprężeń w strukturze, w rezultacie czego szkło jest bardziej wytrzymałe. Oprócz tego metoda ta jest szybsza niż cięcie mechaniczne, m.in. dlatego, że można ominąć etap szlifowania krawędzi oraz czyszczenia szkła. Pozwala to, mimo dużych początkowych kosztów maszyny do cięcia laserem, zaoszczędzić na inwestycjach w dodatkowe maszyny do obróbki, które są niezbędne przy cięciu mechanicznym.
Ponadto laserem łatwiej jest wycinać różne kształty - na przykład zaokrąglenia. Cięcie szkła laserem - a zwłaszcza jego cienkich tafli - stało się szczególnie popularnym rozwiązaniem, gdy wzrosło zapotrzebowanie na płaskie wyświetlacze wykorzystywane w elektronice użytkowej - telewizorach, telefonach komórkowych, odtwarzaczach mp3 i podobnych urządzeniach.
Dąży się obecnie do zmniejszania ich grubości i wagi, głównie poprzez wykorzystywanie coraz cieńszych szklanych podłoży. Ważne jest jednocześnie, aby mimo małej grubości panele charakteryzowały się dużą wytrzymałością, co ułatwia manipulowanie nimi, a także późniejsze ich użytkowanie - na przykład w zastosowaniach takich jak ekrany dotykowe.
CIĘCIE LASEREM W PAPIERNI
Maszyny do cięcia są też ważnym elementem wyposażenia papierni i drukarni, w których są wykorzystywane na przykład do przycinania krawędzi rolek papieru, ich przecinania oraz porcjowania na arkusze, a także w cięciu tektury. Podobnie jak w cięciu szkła, także w przypadku mechanicznego cięcia papieru największym problemem jest słaba jakość cięcia, w tym na przykład chropowate krawędzie, z których wystają włókna wchłaniające wilgoć z otoczenia.
![]() Tabela 1. Wybrani dostawcy maszyn do cięcia strumieniem wody oraz podzespołów do tych urządzeń |
![]() Tabela 2. Wybrani dostawcy maszyn do cięcia tlenowego, plazmą i laserem |
![]() Tabela 3. Wybrane firmy oferujące usługę cięcia |
Oprócz tego w procesie takim powstaje dużo pyłu, który unosząc się w powietrzu, może wpływać na inne procesy realizowane w danym zakładzie - problem taki dotyczyć może na przykład drukarni. Wad tych pozbawione jest cięcie laserowe. Ponadto w przypadku wykonywania nacięć - na przykład rowków do otwierania pudełek - wykorzystując laser, precyzyjniej można kontrolować głębokość rozcięcia.
WADY I ZALETY METOD BEZKONTAKTOWYCH
Wymienić można kilka wad i zalet, w tym cech wspólnych, które charakteryzują metody bezkontaktowe. Łączy je na przykład duża precyzja cięcia oraz gładkość i czystość krawędzi - z wyjątkiem cięcia tlenowego, które charakteryzuje mała dokładność w porównaniu z pozostałymi metodami oraz konieczność obróbki wykończeniowej. Metody bezkontaktowe różnią się natomiast pod względem poziomu hałasu, co ma istotny wpływ na organizację stanowiska pracy i komfort personelu.
Do głośnych zalicza się na przykład cięcie plazmą, natomiast cicha praca jest zaletą maszyn laserowych. Wadą cięcia plazmowego jest też emisja dużej ilości gazów i dymu, a także silne promieniowanie świetlne łuku. Z tego powodu ręczne cięcie strumieniem plazmy (oraz tlenowe) wymaga założenia przez pracownika osłony chroniącej twarz i oczy. Oprócz tego metody cięcia plazmą oraz tlenem ograniczone są do konkretnych grup materiałów, natomiast cięcie laserem oraz strumieniem wody i wody ze ścierniwem są metodami pod tym względem bardziej uniwersalnymi.
METODY TERMICZNE A CIĘCIE WODĄ
Za jedną z głównych wad cięcia tlenowego, plazmowego i laserowego uznaje się cieplne oddziaływanie na rozcinany materiał (najwęższa strefa wpływu ciepła charakteryzuje cięcie laserem). W przypadku waterjetów temperatura w obszarze cięcia wzrasta maksymalnie do 40°C, dzięki czemu nie zachodzą zmiany właściwości ani struktury materiału - takie jak na przykład odbarwienia krawędzi i ich utwardzenie. Materiał nie ulega też odkształceniu ani naprężeniom termicznym.
Problemem w przypadku maszyn do cięcia wodą jest natomiast rozcinanie bardzo grubych materiałów. Strumień tnący rozprasza się wówczas wewnątrz detalu, co powoduje nierównomierne nacięcie - szersze na spodzie, a węższe tuż przy górnej powierzchni. Nierówności na krawędziach grubych detali występują też, gdy strumień wody wchodzi w materiał pod innych kątem niż z niego wychodzi. Wpływa to też na dokładność wymiarów detalu.
Zaletą waterjetów jest natomiast możliwość jednoczesnego obrabiania kilku cienkich detali ułożonych na stosie. Zaletą metody cięcia strumieniem wody, pod tym względem podobnej do metody laserowej, jest ponadto bardzo wąska szczelina cięcia, dzięki czemu przy wycinaniu detali marnuje się niewiele materiału. Głowice waterjetów są też w porównaniu do pozostałych lżejsze, co ma znaczenie zwłaszcza w przypadku, gdy montowane są na ramieniu robota.
Oprócz tego, że sprawniej można operować lżejszą głowicą, łatwiejszy jest też wówczas rozruch, a potem zatrzymanie robota. Prostsza jest także konserwacja dysz waterjetów niż na przykład głowic laserowych, chociaż w obu przypadkach trzeba je przeprowadzać równie często. Waterjety, podobnie jak maszyny do cięcia laserem, są drogie, stąd nie zawsze inwestycja w nie znajduje ekonomiczne uzasadnienie - zwłaszcza przy masowej obróbce elementów.
Dodatkowym problemem w przypadku maszyn do cięcia strumieniem wody jest przecinanie materiałów o dużej twardości - np. stali narzędziowej. Wówczas bowiem prędkość cięcia znacząco spada, przez co wydłuża się czas obróbki, a tym samym rosną koszty. Rozwiązaniem jest uzupełnienie waterjetów szybszymi i tańszymi maszynami do cięcia plazmą, popularne jest też połączenie obu technologii w jednej maszynie do cięcia. Gdy wymagana jest większa dokładność i różnorodność ciętych materiałów waterjety są też wykorzystywane jako dopełnienie maszyn do cięcia tlenowego.
Monika Jaworowska