Część 2. Efektywność energetyczna
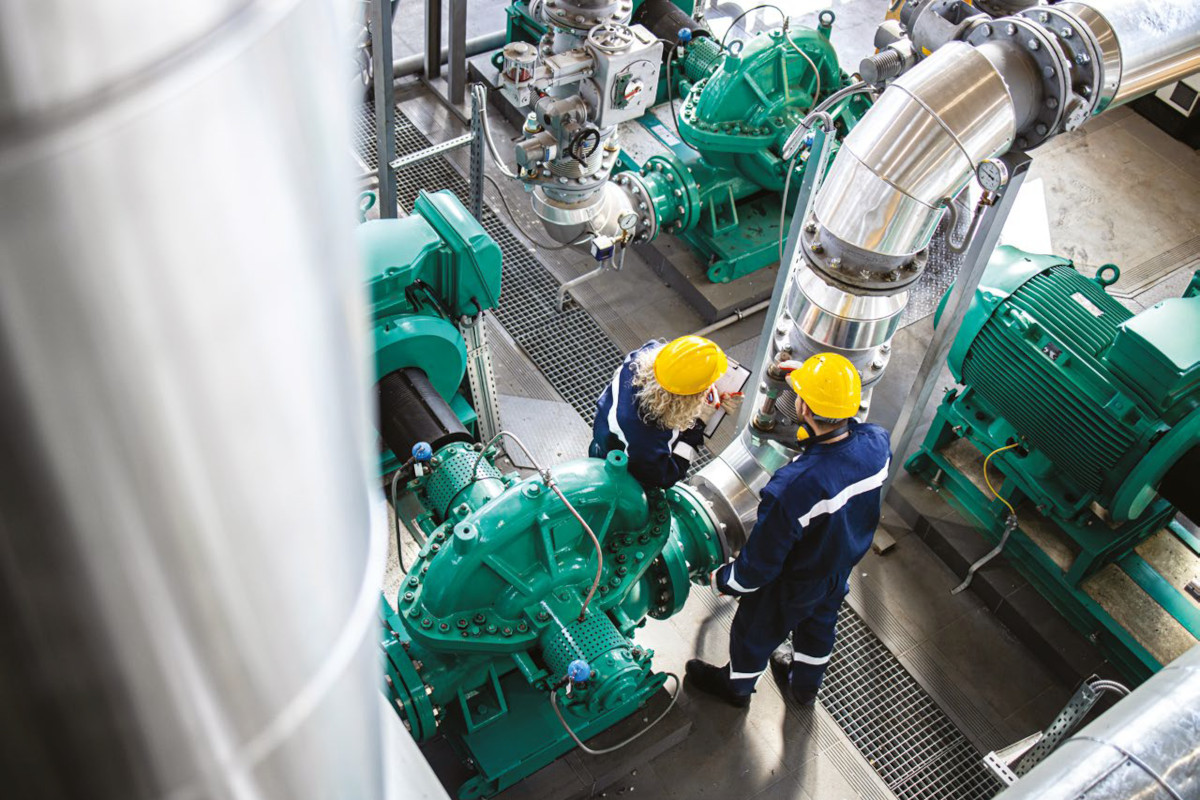
Szeroko rozumiana efektywność energetyczna obejmuje oszczędność energii w różnej formie, zarówno elektrycznej, jak i ciepła czy mediów użytkowych, jak woda. Jeżeli chodzi o tę pierwszą, jednym ze sposobów na ograniczenie jej zużycia jest korzystanie z energooszczędnych rozwiązań napędowych.
Energooszczędne napędy
Szacuje się, że udział napędów elektrycznych w globalnym zużyciu energii elektrycznej przekracza 50%, a w przemyśle sięga 70%. Można go zmniejszyć na kilka sposobów. Takim jest wprowadzenie urządzenia pośredniczącego w podłączeniu silnika do zasilania. Przeważnie jest to układ łagodnego rozruchu (softstart) albo, jeżeli wymagana jest regulacja prędkości obrotowej silnika, przemiennik częstotliwości.
Softstart stopniowo podwyższa napięcie zasilania na zaciskach silnika. Na początku jest ono na tyle małe, że nie występuje gwałtowne szarpnięcie, a możliwa jest jedynie płynna regulacja na przykład luzów komponentów mechanicznych lub naprężenia pasów. Następnie, wraz ze zwiększaniem przez softstart napięcia zasilania, rośnie moment obrotowy silnika. To z kolei powoduje, że maszyna się rozpędza.
Softstarty poprawiają sprawność energetyczną maszyn, które często pracują na biegu jałowym. W takim przypadku powinno się je bowiem wyłączyć, a dzięki układom łagodnego rozruchu w razie potrzeby można je w każdej chwili ponownie włączyć i uruchomić, a następnie zatrzymać i wyłączyć bez nadmiernych zbędnych strat energii. Przykładami takich maszyn są piły, a poza przemysłem – schody ruchome.
Ponadto wyposażane są w styczniki obejściowe, wbudowane lub zewnętrzne, ale sterowane przez softstart. Odłączają one obwody układu łagodnego rozruchu od zasilania i bezpośrednio podłączają do niego napędzaną maszynę tuż po jej rozpędzeniu. W razie przejścia w tryb hamowania sterownik softstartu odłącza obwód obejściowy i przełącza napędzaną maszynę na zasilanie za swoim pośrednictwem. Dzięki temu w czasie normalnej pracy, między rozruchem a zatrzymaniem napędu, energia zasilająca nie jest dodatkowo tracona w obwodach softstartu. To zwiększa sprawność wypadkową napędu.
Silniki energooszczędne - jak ograniczać straty?![]() Sprawność energetyczną silników poprawia zmniejszenie strat energii na ciepło w uzwojeniach (w miedzi, obciążeniowych), w rdzeniu (w stali), na tarcie (mechanicznych) i dodatkowych. Pierwsze występują w uzwojeniach wirnika i stojana. W wyniku przepływu prądu w postaci ciepła wydziela się moc strat proporcjonalna do I²R. Straty te zmieniają się zależnie od obciążenia silnika i w wyniku zmiany rezystancji na skutek wahań temperatury otoczenia. W uzwojeniach z miedzi wzrost temperatury o 10°C powoduje zwiększenie rezystancji o 4%. Na wzrost rezystancji uzwojeń w maszynach indukcyjnych wpływa też m.in. efekt naskórkowości. Straty w uzwojeniach stanowią około 50% strat energii w silniku. By je ograniczyć zmniejsza się rezystancję uzwojeń, zwiększając pole przekroju poprzecznego uzwojeń stojana i stosując grubsze uzwojenia wirnika. Ponadto w tym drugim aluminium zastępuje się miedzią, a w przypadku stojana zmniejsza się długość czołowych połączeń uzwojeń. Straty w stali występują w rdzeniach stojana i wirnika. Wynikają ze strat energii potrzebnej do zmiany położenia domen w materiale magnetycznym zachodzących w czasie jego okresowego przemagnesowywania, co następuje zgodnie z krzywą pętli histerezy. Przyczyną są też prądy wirowe indukowane w rdzeniach przez pole magnetyczne. Straty w stali stanowią około 15% strat energii w silniku. Zmniejsza się je używając blach lepszej jakości o mniejszych stratach przemagnesowywania, jak stal magnetyczna. Straty na prądy wirowe ogranicza się, zmniejszając grubość blach rdzeni. Przyczyną strat mechanicznych jest tarcie, głównie w łożyskach. Energia tracona jest też na skutek oporu aerodynamicznego, jaki napotykają wirnik silnika i łopatki zintegrowanego z nim wentylatora. Wkład strat na tarcie to około 15%. Zmniejsza się je, wybierając łożyska o konstrukcji (wymiarach, materiałach) opracowanej tak, by zmniejszyć straty na ciepło w wyniku tarcia. Ograniczają je też specjalne smary. Ponadto instaluje się mniejsze wentylatory i zapewnia swobodny przepływ powietrza w silniku. Straty dodatkowe są skutkiem harmonicznych pola magnetycznego w szczelinie powietrznej między stojanem a wirnikiem. Ich przyczyną jest jej nierównomierna grubość wynikająca ze sposobu rozmieszczenia żłobków wirnika i stojana, rozbieżności w zakresie ich wymiarów i sposobu ułożenia w nich uzwojeń. Niedokładności te są wynikiem zaniedbań na etapach projektowania i produkcji silnika. Udział dodatkowych strat to 20%. By je zmniejszyć należy z większą precyzją wykonać żłobki. Ich wymiary dobiera się tak, by grubość szczeliny powietrznej między wirnikiem i stojanem zoptymalizować pod kątem strat. |
Przemienniki częstotliwości
Gdy wymagana jest zmiana prędkości obrotowej silnika, efektywniejsze energetycznie są napędy uzupełnione o przemiennik częstotliwości. Urządzenia te zmieniają częstotliwość i napięcie prądu przemiennego zasilającego silnik, co umożliwia regulowanie jego prędkości obrotowej i momentu obrotowego. Główne bloki funkcyjne przemienników częstotliwości to: prostownik, układ pośredni (kondensator wygładzający), falownik i sterownik. Zasada ich działania jest następująca: najpierw przemienne napięcie wejściowe jest prostowane w mostku diodowym, a następnie wygładzane i przekształcane w falowniku w napięcie przemienne o zmiennej amplitudzie i częstotliwości, które zasila silnik. Przemienniki częstotliwości zapewniają szeroki zakres regulacji parametrów pracy silników, od 0 do typowo 100‒120% znamionowej prędkości obrotowej oraz do nawet 150% znamionowego momentu obrotowego przy obniżonej prędkości.
Oszczędności energii elektrycznej, jakie można uzyskać dzięki przemiennikom częstotliwości przez dynamiczne dopasowanie prędkości silnika napędu do aktualnego zapotrzebowania, zależą od tego, jaki charakter ma obciążenie, stałomomentowy czy zmniennomomentowy. W pierwszym przypadku moment obrotowy nie zmienia się wraz z prędkością. Moc pobierana przez napęd obciążenia stałomomentowego jest wprost proporcjonalna do prędkości obrotów silnika. Dlatego zmniejszenie tej ostatniej przykładowo o połowę zapewnia oszczędności energii elektrycznej także na poziomie 50%. Do grupy obciążeń stałomomentowych zaliczane są m.in.: przenośniki, mieszadła, kruszarki, pompy wyporowe oraz sprężarki powietrza.
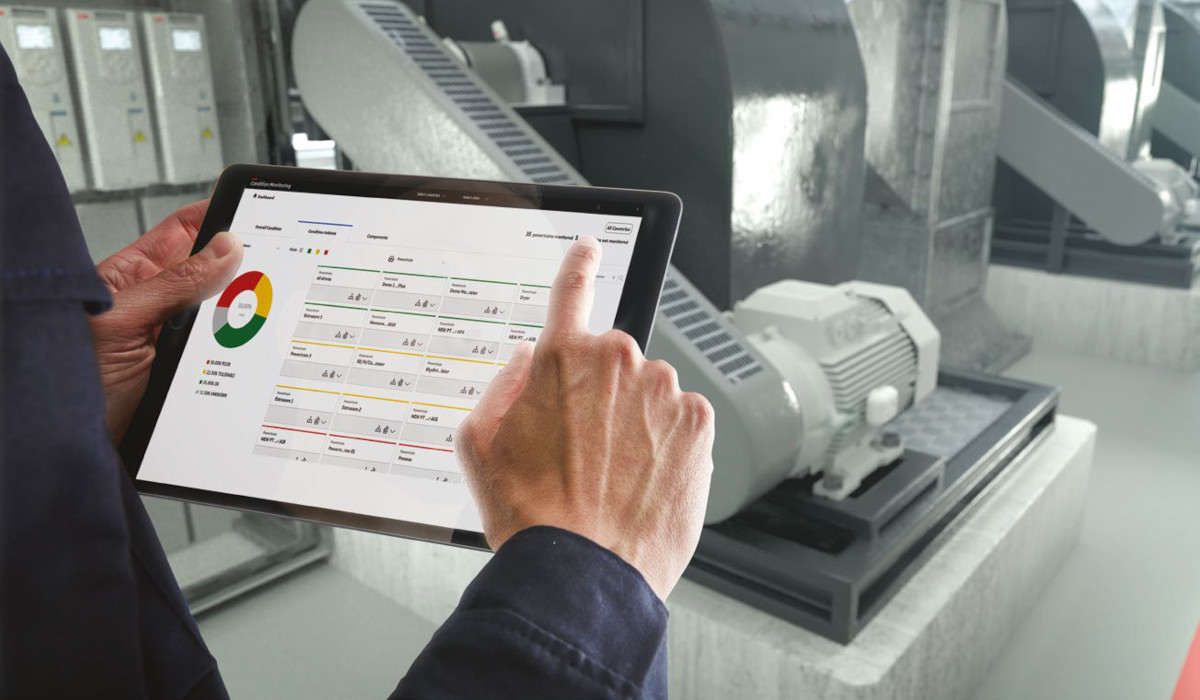
Oszczędności dzięki przemiennikom
Większe oszczędności energii elektrycznej można uzyskać w obciążeniach zmiennomomentowych, w przypadku których moment obrotowy zmienia się wraz z prędkością. Do tej kategorii zaliczane są m.in.: wentylatory oraz pompy wirowe mające charakterystyką kwadratową. Przy zmniejszeniu prędkości obrotowej ich zapotrzebowanie na energię maleje w trzeciej potędze. Oznacza to, że w razie zmniejszenia prędkości obrotowej na przykład o połowę obciążenie będzie wymagać zaledwie jednej ósmej mocy. Zatem już nawet niewielkie spowolnienie obrotów silnika zapewni znaczące oszczędności energii.
Sprawność energetyczna, przede wszystkim dzięki postępowi w dziedzinie energoelektroniki, w najnowszych modelach przemienników częstotliwości sięga 98%. Funkcją znacząco zwiększającą efektywność energetyczną systemu napędowego jest możliwość odzyskiwania energii hamowania. Dzięki tej opcji w czasie zatrzymywania maszyny energia hamowania nie jest tracona na ciepło w rezystorach hamujących, ale jest efektywnie zagospodarowana, przez oddanie jej z powrotem do sieci zasilającej albo współdzielenie z przemiennikami częstotliwości zasilającymi inne systemy napędowe. Opłaca się to, zwłaszcza jeżeli zachodzi potrzeba częstego hamowania, jak w napędach taśmociągów czy nawijarek.
Kolejny komponent napędów, w którym można uzyskać oszczędność energii, to silniki elektryczne. W tym celu stosowane są różne rozwiązania konstrukcyjne (patrz: ramka).
![]() Według Eurostatu w 2021 roku przemysł był trzecim największym konsumentem energii w Unii Europejskiej, z udziałem 25,6%, zaraz po transporcie i gospodarstwach domowych. Dwie trzecie zużytej przez ten sektor gospodarki energii stanowiły energia elektryczna i gaz ziemny, z udziałami odpowiednio 33,2% oraz 32,7%. Najbardziej energochłonnymi gałęziami przemysłu okazały się: przemysł chemiczny i petrochemiczny (21,5%), przemysł minerałów niemetalicznych (14,1%) oraz przemysł papierniczy, celulozowy i poligraficzny (13,6%). Ponad 10% wyniosły również udziały przemysłu spożywczego, napojowego i tytoniowego (11,65%) oraz sektora żelaza i stali (10,2%). |
Ciepło procesowe. gdzie szukać oszczędności?
Ciepło jest niezbędne w wielu branżach, na przykład w produkcji i przetwórstwie metali, tworzyw sztucznych, cementu, szkła, ceramiki. Niektóre procesy wymagają ciągłego ogrzewania surowców i dostaw ciepła w dużych ilościach, natomiast inne podgrzewania małych partii materiałów zgodnie z profilami czasowo-temperaturowymi. Wspólną cechą wszystkich systemów dostarczających ciepło procesowe jest przekazywanie energii do obrabianego materiału. Dzieli się je na bezpośrednie oraz pośrednie. Pierwsze wytwarzają ciepło w samym materiale (na przykład grzanie indukcyjne), zaś pośrednie przekazują energię ze źródła ciepła do materiału przez przewodzenie, promieniowanie, konwekcję albo kombinację tych mechanizmów. Systemy ogrzewania w przemyśle należą ponadto zwykle do jednej z następujących kategorii: spalinowych, elektrycznych, odzysku i wymiany ciepła. Za odrębną grupę uważa się często kotły i generatory pary. Dla każdej z metod można wprowadzić szereg ulepszeń poprawiających sprawność energetyczną. Rozwiązania te grupuje się na dotyczące: etapu wytwarzania ciepła, ograniczania jego strat do otoczenia, jego wymiany oraz odzysku ciepła odpadowego.
W generowaniu ciepła dąży się głównie do ograniczenia strat spalania paliwa i zwiększenia ilości jego energii przekazywanej do materiału. Sprawność spalania poprawia odpowiedni stosunek powietrza do paliwa. Ilość tego pierwszego reguluje się tak, żeby uzyskać warunki zbliżone do idealnej reakcji spalania, w której z paliwa odzyskuje się całą energię, bez strat. Korzystne jest też podgrzewanie powietrza do spalania. W tym celu często wykorzystuje się gorące spaliny, co jest formą odzysku ciepła. Sprawność spalania zwiększa się także, zasilając ten proces powietrzem wzbogaconym w tlen. Straty ciepła do otoczenia ogranicza: izolowanie termiczne nagrzewających się powierzchni na przykład ścian pieców, uszczelnianie otworów na przykład drzwi do załadunku, izolowanie części, które są chłodzone cieczą lub powietrzem, unikanie części wysuniętych, które się nagrzewają. By z kolei zwiększyć efektywność przekazywania ciepła należy utrzymywać w czystości powierzchnie jego wymiany i poprawiać sprawność konwekcji dzięki odpowiednio dobranym palnikom oraz wentylatorom. Przykładem odzysku ciepła jest wykorzystanie energii spalin do podgrzania wsadu. Jak się w praktyce wdraża te zalecenia, wyjaśniamy na przykładzie kotłów.
Kotły. Jak poprawić ich sprawność?
Z wyjątkiem gazu ziemnego praktycznie wszystkie paliwa pozostawiają osad na rurach paleniska. Ogranicza on wymianę ciepła i zwiększa temperaturę spalin, pogarszając sprawność energetyczną. Im jego warstwa jest grubsza, tym mniejszy jest współczynnik wymiany ciepła – przykładowo przy warstwie sadzy o grubości 0,8 mm spada on o prawie 10%, a przy 4,5 mm aż o 69%. Problem osadów dotyczy szczególnie kotłów spalających paliwa stałe, jak węgiel i biomasa. W zakresie utrzymania ich w czystości stosowane są różne rozwiązania. Przykład to systemy zdmuchiwaczy sadzy, które oczyszczają palenisko w czasie pracy kotła. Osady w mniejszych urządzeniach usuwa się ręcznie. Efektywność wymiany ciepła pogarsza też kamień na rurach wymienników – jeden milimetr osadu może zwiększyć zużycie paliwa o dwa %. Ogranicza on ponadto obieg wody i powoduje uszkodzenie rur na skutek przegrzania. Postęp wzrostu kamienia sprawdza się, pobierając i badając próbki wody kotłowej. Częstość sprawdzania zależy od rozmiarów kotła. Jeżeli wyniki wskazują na obecność osadu do wody dodawane są środki chemiczne spowalniające jego wzrost. Skuteczność takiej prewencji pozwala zaoszczędzić na koniecznym w celu usunięcia osadu, okresowym spuszczaniu wody, wraz z którą również tracone jest ciepło.
Strata gorącego kondensatu w kotłach parowych zwiększa zużycie wody, chemikaliów do jej uzdatniania oraz energii potrzebnej do podgrzania wody uzupełniającej. Rozwiązaniem jest system zamknięty, który dostarcza kondensat pary pod ciśnieniem do ponownego odparowania.
Aby odzyskać ciepło z nagrzanych spalin, wykorzystuje się wymienniki ciepła do podgrzewania wody zasilającej kocioł, tzw. ekonomizery lub powietrza do spalania, wykorzystując nagrzewnice. Poprawiają one sprawność energetyczną kotła nawet o kilka procent. Przykładem są ekonomizery kondensacyjne, które chłodzą gazy wylotowe do temperatury poniżej punktu rosy. W ten sposób odzyskuje się ciepło ze spalin, jak i ciepło utajone z kondensującej się wilgoci. Wymienniki tego typu muszą być wykonane z materiałów, które nie będą korodować.
Źródłem strat są przewymiarowane rury rozprowadzające gorące medium, niesprawne odwadniacze i niedostateczne odpowietrzanie wody zasilającej kocioł. Trzeba też pamiętać, że sprawność, z jaką kotły przetwarzają energię paliwa na parę lub gorącą wodę, znacznie spada przy małym obciążeniu. Dlatego należy dobierać je, uwzględniając jego zmienność – ekonomicznie jest zainstalować mały kocioł pracujący przy maksymalnym dla niego obciążeniu w okresach małego zapotrzebowania i większy, który obsłuży obciążenia szczytowe. Wypadkową sprawność energetyczną poprawi także kaskadowanie ciepła, które odprowadzane z jednej części procesu można wykorzystać do ogrzania innej.
Nie tylko grzanie, ale również chłodzenie jest energochłonne. Sprawność energetyczną tego procesu można poprawić na kilka sposobów.
Marcin Panek
Emit S.A.
Mamy klientów, którzy doskonale zdają sobie sprawę z przewagi nowoczesnych silników energooszczędnych, w związku z czym podejmują analizy i działania dotyczące wymiany maszyn obecnie pracujących na nowe, cechujące się wyższymi klasami sprawności i oszczędnościami z tym związanymi. Są jednak firmy, których wiedza w tym zakresie jest mniejsza i dlatego też potrzebne jest przekazywanie odpowiednich informacji, pokazywanie oszczędności wynikających z mniejszego zużycia energii przez stosowane przez nich silniki. Sądze, że najbardziej swiadome są dzisiaj te branże, które wykorzystują wiele urządzeń elektrycznych i w związku z tym zużywają duże ilości energii. Dla takich firm każda oszczędność energii to są realne pieniądze, które mogą być spożytkowane na kolejne inwestycje w tym zakresie. Wsparcie, którego możemy udzielić klientom, to informowanie o korzyściach płynących ze stosowania urządzeń energooszczędnych i realnych kwotach, które mogą być zaoszczędzone.
Zużycie energii i mediów można minimalizować stosując urządzenia energooszczędne – nie tylko silniki, ale też układy napędzane przez nie, takie jak: pompy czy wentylatory. Z punktu widzenia klienta wybór dostawców powinien wiązać się z analizą sprawności proponowanych rozwiązań, czasem życia aplikacji (zużycia energii z tym związanej), następnie z ich ceną i weryfikacją opłacalności zastosowania urządzeń. Te ostatnie musza oczywiście spełniać wymagania związane z odpowiednimi regulacjami. Dodam, że w przemyśle warto dopasowywać stosowane urządzenia do rzeczywistych potrzeb wynikających z procesów technologicznych. Innymi słowy chodzi o to, aby ich nie przewymiarowywać, bowiem powoduje to większe zużycie energii niż rzeczywiście jest to wymagane.
Jak wiemy minimalne wymogi dla silników niskiego napięcia o mocy do 1000 kW to klasa sprawności IE3, a w pewnym zakresie to IE4. Regulacje unijne wymagają od dostawców urządzeń spełnienie wymagań w nich zawartych, w związku z czym każdy z dostawców powinien posiadać w swojej ofercie takie silniki. Z punktu widzenia dalszego rozwoju wydaje się, że jest małe pole manewru związanego z uzyskiwaniem większych sprawności produkowanych silników. W grę wchodzić może stosowanie w silnikach magnesów trwałych podnoszących sprawność, ale niestety też zwiększających koszty wytworzenia. |
Oszczędności w agregatach chłodniczych
Główne komponenty agregatów chłodniczych to: parownik, sprężarka, skraplacz i zawór rozprężny. W parowniku następuje przekazanie ciepła ze schładzanej cieczy do czynnika chłodniczego, którym jest na przykład glikol etylowy. W tym komponencie agregatu zachodzi przemiana fazowa, gdy pod wpływem ciepła pochłoniętego z procesu wrze czynnik chłodniczy. Po odparowaniu trafia on do sprężarki. Jej zadaniem jest zwiększenie ciśnienia i temperatury czynnika chłodniczego do wartości, przy których będzie można usunąć ciepło pochłonięte z procesu, jak i ciepło sprężania. Gaz o takich właściwościach trafia do skraplacza, w którym ulega kondensacji pod wpływem, w zależności od tego, jak jest chłodzony agregat, zimniejszego powietrze z otoczenia albo wody o temperaturze niższej niż temperatura skraplania czynnika chłodniczego. Następnie ten ostatni, schłodzony i w ciekłej postaci, trafia przez zawór rozprężny ponownie do parownika i cały cykl się powtarza.
Na wypadkową sprawność energetyczną agregatów chłodniczych wpływają ich wszystkie komponenty. Na przykład można ją poprawić, wykorzystując sprężarki sterowane za pośrednictwem przemiennika częstotliwości, w oparciu o pomiar temperatury chłodzonego procesu. Im jest niższa, tym wolniej może pracować sprężarka, co pozwala zaoszczędzić energię. Monitorowana jest także temperatura otoczenia, dzięki czemu agregat można wyłączyć, jeśli warunki pracy są niesprzyjające. W napęd o zmiennej prędkości obrotowej wyposażone są także wentylatory skraplacza. Poza tym wysokosprawne agregaty chłodnicze mają elektroniczne zawory rozprężne zamiast stratnych zaworów mechanicznych.
W ramce wyjaśniamy też, jak uzyskać oszczędności w instalacji sprężonego powietrza, zwykle jednej z bardziej energochłonnych w zakładzie.
Oszczędności energii w instalacji sprężonego powietrza![]() Na wstępie warto zweryfikować rzeczywiste zapotrzebowanie na to medium, często bowiem jest wykorzystywane dlatego, że jest "pod ręką". Jeśli nie można z niego zrezygnować, trzeba się upewnić, że jest użytkowane efektywnie. Nie jest tak na przykład, jeżeli średnie zapotrzebowanie na nie jest ułamkiem szczytowego. Sprężarka jest wtedy przewymiarowana i lepiej ją wymienić na model o mniejszej wydajności, ale ze zbiornikiem o większej pojemności, odpowiedniej do szczytowego zapotrzebowania. Instalacja sprężonego powietrza działa też efektywniej, gdy profil obciążenia jest równomierny. Oznacza to, że większe obciążenia najlepiej załączać naprzemiennie, unikając w ten sposób kumulacji zapotrzebowania. Głównym źródłem strat w instalacjach sprężonego powietrza są wycieki. Mogą wystąpić w wężach, złączkach, rurach, na złączach rurowych, w regulatorach ciśnienia, otwartych zaworach, uruchomionym i niezaizolowanym sprzęcie, na złączach gwintowanych bez odpowiedniego uszczelnienia albo brudnych. Najefektywniejszym sposobem ich wykrycia są pomiary ultradźwiękowe. |
Systemy zarządzania energią
Aby poprawić efektywność energetyczną zakładu, najpierw należy sprawdzić, które procesy, linie produkcyjne, maszyny są najbardziej energochłonne i z czego wynika ich nieefektywność. W tym celu monitoruje się ich zużycie energii przez dłuższy czas, co pozwala wykryć trendy i skorelować wyniki ze zdarzeniami w produkcji. Pomagają w tym systemy zarządzania energią (Energy Management System, EMS) stanowiące połączenie czujników mierzących zużycie mediów i oprogramowania, które przetwarza i analizuje wyniki pomiarów.
Zakres możliwości systemów EMS jest różny. Mogą monitorować zużycie różnych mediów (gazu, energii elektrycznej, pary wodnej, sprężonego powietrza, wody) w czasie rzeczywistym i poddawać analizie dane archiwalne. Przydatną opcją jest przedstawianie poboru energii w przeliczeniu na obszary (działy, linie technologiczne, maszyny) i ilość wyrobów (zamówienie, sztukę). Dzięki powiązaniu zużycia energii z danymi procesowymi można rozróżnić koszty produkcji i pozaprodukcyjne.
Przykładowe funkcje dostępne typowo w systemie zarządzania energią to: podgląd na żywo poboru mediów, monitorowanie wskaźników efektywności, na przykład zużycia energii w danej formie na tonę wyrobu, obliczanie rzeczywistych kosztów mediów wykorzystanych do produkcji danego towaru, godzinowy rozkład ich zużycia i pobór energii na dział. Dzięki temu łatwiej jest wykryć i zdiagnozować awarie, wycieki i inne anomalie powodujące marnotrawstwo energii. Systemy EMS mogą także prognozować jej zużycie i z wyprzedzeniem generować alarmy w razie możliwości przekroczenia limitów. Często integrują też moduły zarządzania budynkiem BMS (Building Management System). Dzięki nim można kontrolować zużycie energii przez systemy wentylacji, klimatyzacji, ogrzewania i oświetlenia zakładu.
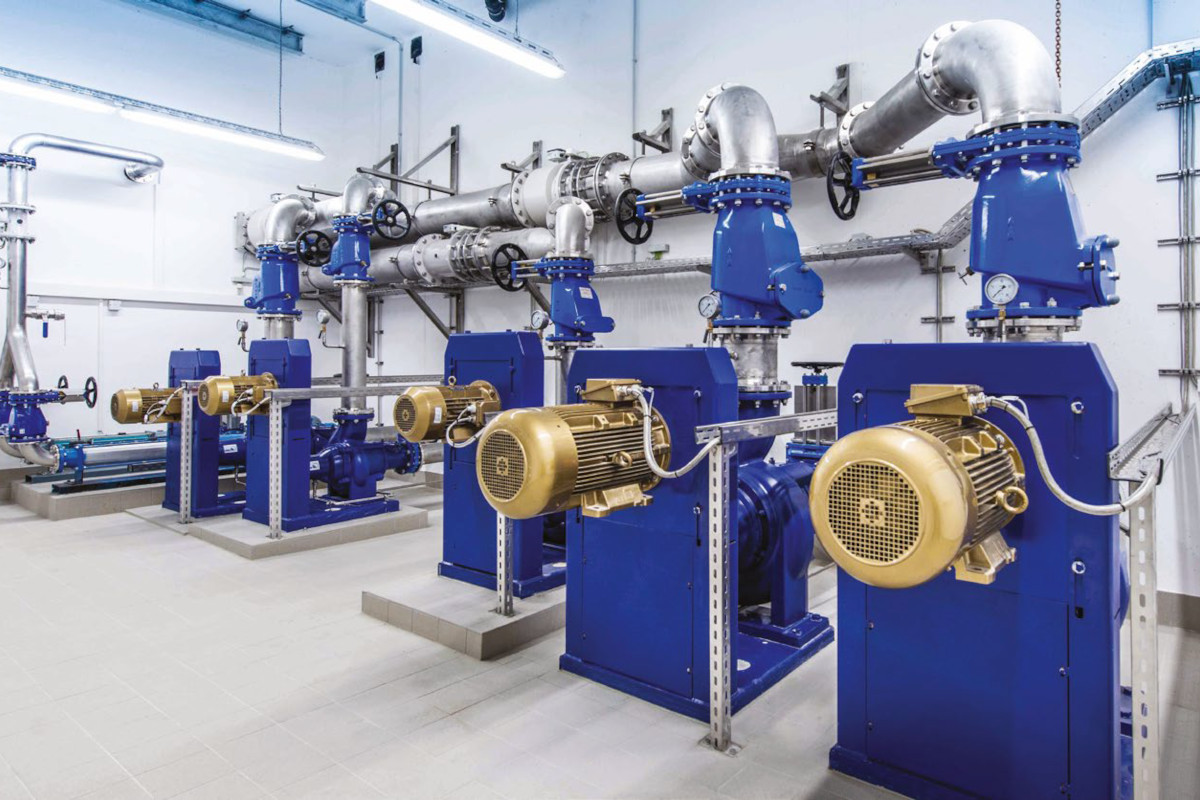
Monika Jaworowska