STANOWISKA PRZEŁADUNKOWE W NAFTOPORCIE ORAZ HISTORIA ICH BUDOWY
Infrastruktura terminalu Naftoportu obejmuje pięć stanowisk przeładunkowych o potencjale przekraczającym 40 milionów ton paliw płynnych rocznie. Powstawały one w różnych okresach - pierwsze w 1974 roku, zaś najnowsze - w 2015. Stanowiska pozwalają na przeładunek większości produktów, tj. benzyny, paliwa lotniczego, oleju napędowego i opałowego oraz półproduktów.
Rozkład przeładowywanych produktów jest różny na poszczególnych stanowiskach, jak również różna jest wydajność raty przeładunku co dodatkowo umożliwia większą elastyczność przy podłączaniu zbiornikowców. Stanowiska różnią się też wielkością, jeżeli chodzi o przyjmowane jednostki - największe statki mogą mieć 340 metrów długości oraz pojemność nawet do 300 tys. DWT*).
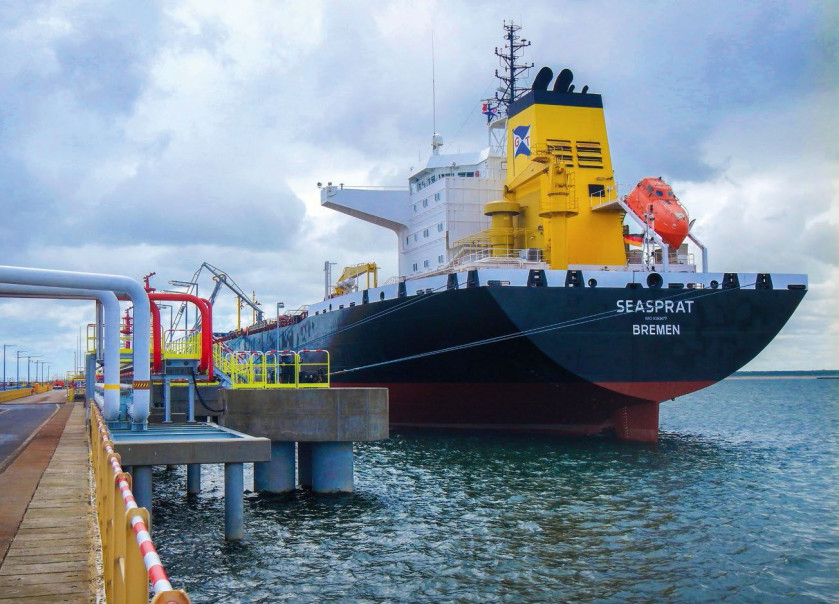
Jeżeli chodzi o instalacje terminalu, to każdy z rurociągów przeznaczony jest do przesyłania określonych produktów naftowych. Innymi słowy nie ma możliwości, aby przykładowo ropę transportować rurociągiem dla benzyny. Sumaryczne zdolności przeładunkowe szacowane są na 40 mln ton ropy i produktów naftowych. Jest to właściwie wszystko, czego potrzebuje gospodarka krajowa plus uzupełniające dostawy dla rafinerii znajdujących się w Niemczech.
JAKA JEST PROCEDURA PRZEŁADUNKU PALIW?
Po pierwsze zbiornikowiec musi być zacumowany do nadbrzeża. Procedura podchodzenia do stanowiska jest złożona i wymaga współudziału kilku holowników. Jednostka jest tak ustawiana, aby jej manifoldy, czyli przyłącza do instalacji zbiorników, znajdowały się na wprost dedykowanych dla danego produktu ramion przeładunkowych na nabrzeżu. Po zacumowaniu zbiornikowca, wykładane są trapy i wykonywane są procedury "Safety Meeting" (realizowana przez ekspedytora) i podłączenia ramion przeładunkowych (realizowana przez operatorów).
Każde ze stanowisk ma różną liczbę ramion przeładunkowych co wynika z ich struktury technologicznej . Przykładowo stanowisko P wyposażone jest w siedem ramion przeładunkowych - 16-calowe do przeładunku ropy oraz 12-calowe do przeładunku produktów ropopochodnych typu benzyna, oleje napędowe, opałowe, itp.
Ramiona przeładunkowe na wszystkich stanowiskach są wyposażone w systemy awaryjnego, samoczynnego rozłączania ERS (Emergency Release System), które aktywują się automatycznie w razie przekroczenia przez podłączone do zbiornikowca ramiona przeładunkowe strefy alarmowej.
Warunki pogodowe, na wysuniętych w morze pirsach, są bardzo różne, zależą one w szczególności od kierunku wiatru - Naftoport może obsługiwać zbiornikowce przy wiatrach o sile do 9 stopni w skali Beauforta. W przypadku silniejszych wiatrów procedury przeładunkowe są przerywane, zaś ramiona odłączane.
Stanowiska P, R i T wyposażone są w instalacje automatycznego pobierania próbek ropy z rurociągów. Systemy te pozwalają na pobór nawet do 30 próbek na minutę, przy czym ich liczba jest dostosowywana do rodzaju i wielkości partii ładunku oraz wymagań firm kontrolnych.
Ramiona mają napęd elektrohydrauliczny i korzysta się z nich w różnych konfiguracjach - zależnie od rodzaju paliwa. Przykładowo w przypadku załadunku ropy używa się do trzech ramion do przeładunku, zaś czwarte służy do odbioru oparów.
OCHRONA ŚRODOWISKA Z WYKORZYSTANIEM SYSTEMU USUWANIA OPARÓW
W czasie załadunku paliw wykorzystywany jest system VRS (Vapor Recovery System), który służy do odbioru oparów węglowodorowych. Są one na instalacji VRU oczyszczane z siarkowodoru, następnie odzyskiwane drogą desorpcji próżniowej na węglu aktywnym i rozpuszczane w ropie naftowej.
Istnieje możliwość załadunku jednocześnie dwóch zbiornikowców. Emisja węglowodorów na wylocie z instalacji VRU do atmosfery nie przekracza 35 g/m³. Wielkość emisji węglowodorów do atmosfery jest na bieżąco monitorowana i automatycznie rejestrowana przez system.
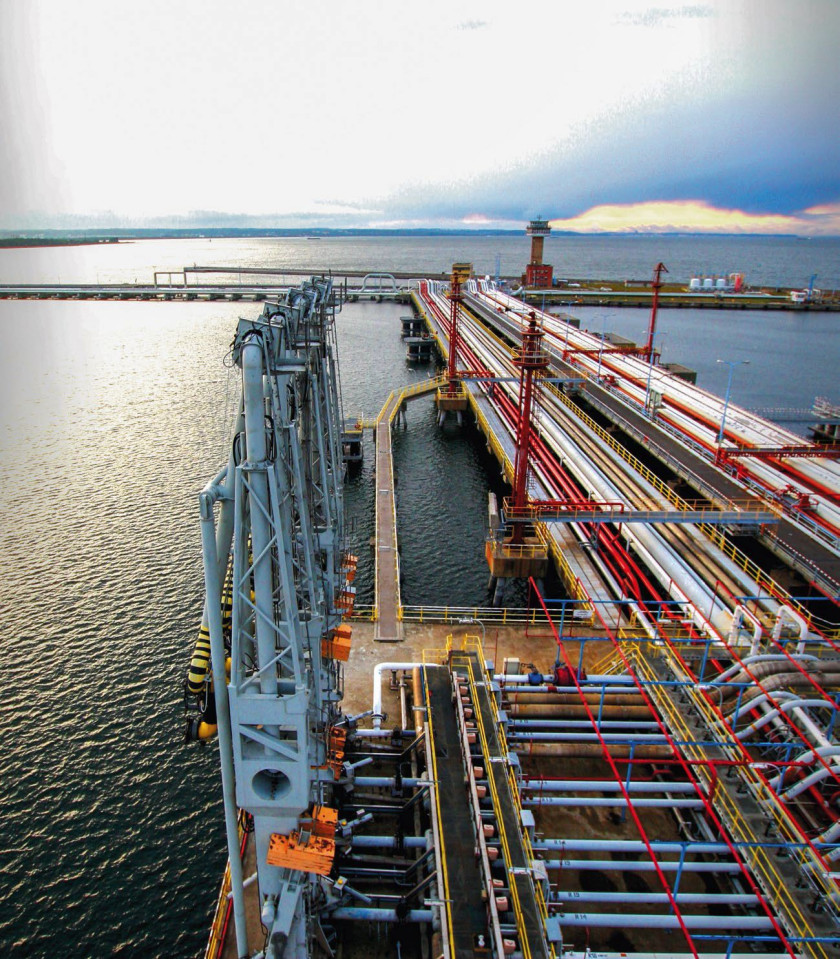
Omawiana instalacja nie jest jedyną, która służy dbaniu o ochronę środowiska. Baza Paliw Naftoport jest położona w bezpośrednim sąsiedztwie obszarów chronionych w ramach programu Natura 2000, przez co aspekt ten jest kluczowy.
Baseny od 1 do 3 ze stanowiskami przeładunkowymi są oddzielone od wód Zatoki Gdańskiej zaporami pneumatycznymi, których bazę stanowią położone na dnie morskim rurociągi sprężonego powietrza z dyszami. Tłoczone pod ciśnieniem powietrze tworzy na powierzchni wody wał rozpływowy, który uniemożliwia wypływ ewentualnych zanieczyszczeń poza obszar basenu.
DODATKOWE INSTALACJE ORAZ ZAUTOMATYZOWANE SYSTEMY NAFTOPORTU
Takimi są przede wszystkim systemy związane z kontrolą cumowania statków do nabrzeży. Zbiornikowiec podchodzący do stanowiska jest śledzony przez układ laserowy, a jego prędkość cały czas monitorowana. Generowane przez system informacje wykorzystują piloci i kapitanowie statków do bezpiecznego manewrowania przy stanowisku.
Przekroczenie dozwolonych parametrów prędkości dobijania jest sygnalizowane na wyświetlaczu wielkoformatowym. Jest to bardzo istotne, bowiem urządzenia odbojowe na stanowiskach są zabudowane na palach i w przypadku uderzenia o nie jednostki mogłoby nastąpić odkształcenie trwałe pali, co wiązałoby się z dużymi kosztami napraw.
Stąd też instalacje wyposażone są w systemy wizualizacyjne i rejestrujące przebieg cumowania statków, jak też ich ruchy w trakcie pobytu zbiornikowca przy stanowisku przeładunkowym. Dodatkowo wykorzystywane są układy do monitorowania naprężenia lin cumowniczych.
Dokonują one ciągłego pomiaru naciągu lin i, w przypadku przekroczenia naprężeń dopuszczalnych, sygnalizują wystąpienie niebezpieczeństwa. W ten sposób stanowią zabezpieczenie przed zrywaniem lin statków w przypadku dużego wiatru oraz falowania wody.
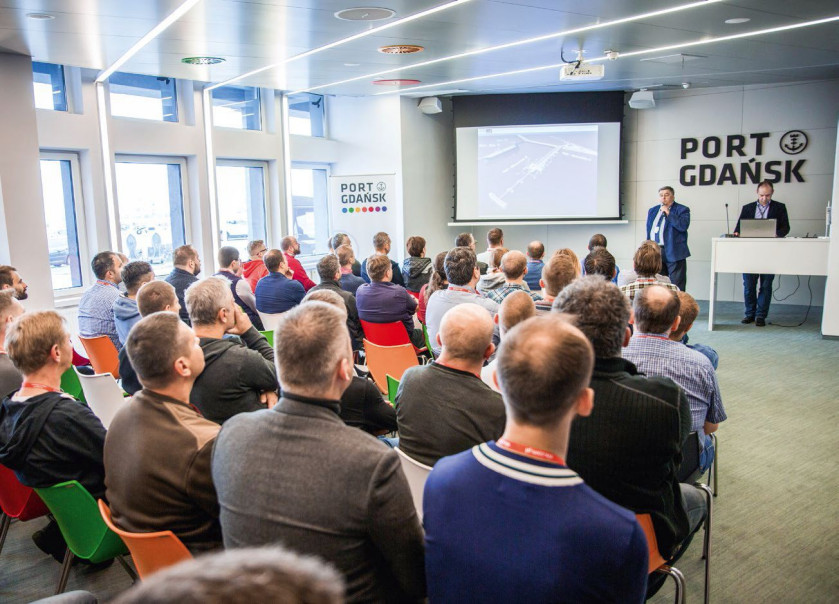
W terminalu Naftoport korzysta się z dalb odbojowych i cumowniczo-odbojowych, czyli konstrukcji hydrotechnicznych, które pozwalają na zacumowanie zbiornikowca i utrzymanie go w odpowiednim położeniu - takim, aby nie występował tzw. shifting podczas przeładunku. Jest to niebezpieczne zjawisko, bowiem ramiona przeładunkowe mają określone strefy pracy.
Statek może się przesuwać o parę metrów - jeżeli nastąpi większy ruch od dozwolonego, następuje automatyczne zamknięcie zaworów produktowych i przeładunek jest zatrzymywany. W sytuacji gdyby statek dalej się przemieszczał lub odchodził od kei, następuje awaryjne odłączenie ramion, co odbywa się w trybie automatycznym.
Celem działania systemu ERS jest zabezpieczenie akwenu przed ewentualnym rozlewem, a samych ramion przed ich uszkodzeniem. Położenie i stan ramion oraz zaworów są monitorowane poprzez systemy sterowania zainstalowane w sterowniach stanowisk przeładunkowych oraz systemy wizualizacyjne w dyspozytorni.
A CO, GDY NIE JEST WYKONYWANY PRZEŁADUNEK PALIW?
W 2017 roku Naftoport przyjął aż 264 statki - biorąc pod uwagę, że przeładunek wraz z operacjami pomocniczymi trwać może kilka dni, to właściwie rzadko kiedy w porcie jest rzeczywiście pusto. Nawet jednak w czasie postoju ma miejsce aktywność - podstawową działań są przeglądy i remonty. Systematycznie i zgodnie z harmonogramami realizowane działania serwisów specjalistycznych i inne zadania związane z utrzymaniem ruchu.
Dodatkowo też regularnie odbywają się ćwiczenia z zakresu ochrony ppoż. oraz ewakuacji Bazy Paliw. W ramach ćwiczeń testowane są systemy przeciwpożarowe. Te ostatnie stanowią bardzo rozbudowane instalacje, które pozwalają na ochronę stanowisk przeładunkowych z lądu.
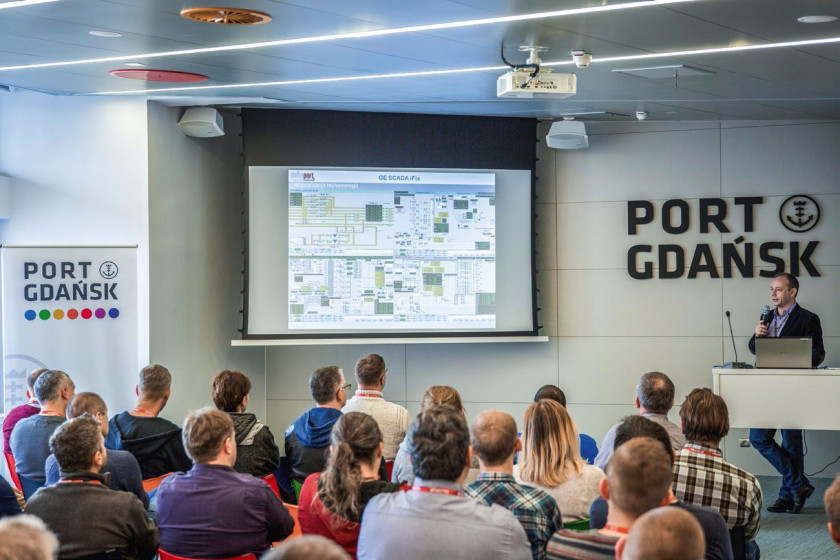
Systemy przeciwpożarowe wyposażone są w stałe instalacje gaśnicze wodno-pianowe zapewniające możliwość podawania środków gaśniczych dla największego zbiornikowca i pomostów przeładunkowych. Używane są tu m.in. pompy wysokiego ciśnienia (16 barów) oraz pompy systemów zraszania pracujące pod ciśnieniem 6 barów.
Dodatkowo dla potrzeb ochrony obiektu wykorzystuje się samochody gaśnicze i statki pożarnicze. Cały system obrony przeciwpożarowej jest sterowany komputerowo, przy czym korzysta się ze zintegrowanej z nim telewizji przemysłowej, kilku równoległych systemów miejscowego i zdalnego sterowania urządzeń, układów monitorowania stanu urządzeń i aparatury, a także instalacji wykrywania oraz sygnalizacji wystąpienia pożaru. Całość systemów połączona jest siecią światłowodową. Z racji charakteru działalności układy te są regularnie sprawdzane i utrzymywane w stanie ciągłej gotowości.
ROZWÓJ SYSTEMÓW STEROWANIA I NADZORU UŻYWANYCH W NAFTOPORCIE
W Naftoporcie wykorzystywane jest przede wszystkim oprogramowanie GE iFix, przy czym początki jego użycia sięgają ponad 20 lat wstecz. Zostało ono wybrane m.in. ze względu na łatwość jego instalacji oraz uruchomienia, a następnie było wdrażane stopniowo, obejmując różne instalacje i przejmując określone funkcje.
Pierwszą koncepcją było stworzenie systemu, w przypadku którego każde ze stanowisk byłoby obsługiwane oddzielną, niezależną stacją roboczą. Projekt ten powstał jeszcze w latach 90. zeszłego wieku, przy czym głównym powodem takiej decyzji było zapewnienie bezpieczeństwa inwestycji. Uznano, że ewentualne problemy z oprogramowaniem na jednym stanowisku nie wpłynęłyby na pracę reszty instalacji. Taka sytuacja jednak w praktyce nie wystąpiła.
Systemy SCADA/HMI są wykorzystywane do różnych zadań. Zarządzają one przede wszystkim instalacjami technologicznymi i pozwalają na wizualizację ich stanu. Obejmuje to konfigurację stanowisk, nadzór nad procesami i kontrolę przeładunku surowców. Dodatkowo oprogramowanie służy do kontroli pracy instalacji odzysku węglowodorów VRS, sterowania oświetleniem wysokim oraz prezentacji stanu systemu PPOŻ.
W kolejnych latach podejście bazujące na użyciu wielu systemów zostało zrewidowane i podjęto decyzję o modernizacji. Obecnie w dyspozytorni korzysta się z systemu czteromonitorowego, który jest obsługiwany przez dwa komputery pracujące w systemie redundantnym i obsługujące całość Bazy Paliw.
JAK WYGLĄDAŁA INTEGRACJA ODDZIELNIE DZIAŁAJĄCYCH SYSTEMÓW STANOWISK DO JEDNEGO OPROGRAMOWANIA?
Początkiem zmian było stwierdzenie faktu, że nie ma u nas takiego czegoś jak "stanowisko samodzielne". Rurociągi przechodzą przez różne obszary Naftoportu, często pojawiają się relacje obejmujące dwa stanowiska, zaś dyspozytorzy i inne osoby muszą mieć jednoczesny wgląd w informacje z różnych instalacji. Wcześniej stosowane systemy komputerowe i wizualizacyjne wprawdzie dawały możliwość podglądu pracy obiektów na ich stacjach klienckich, ale już np. z poziomu zarządu, gdy chciano porównywać zależności występujące w różnych instalacjach, to takie rozproszenie było wysoce problematyczne.
Rozwiązaniem było zastosowanie oprogramowania typu historian, które zostało wdrożone na początku tego wieku. Była to wersja 1.0 i jednocześnie jedna z pierwszych instalacji GE Historian w Polsce. System działał na jednym, redundantnym serwerze i znacznie ułatwił służbom zarządzanie w przypadku występowania współzależności zdarzeń na różnych stanowiskach. Dodatkowo uprościły się też sprawy z weryfikacją danych i ich zestawieniami, a także prezentacją zdarzeń alarmowych.
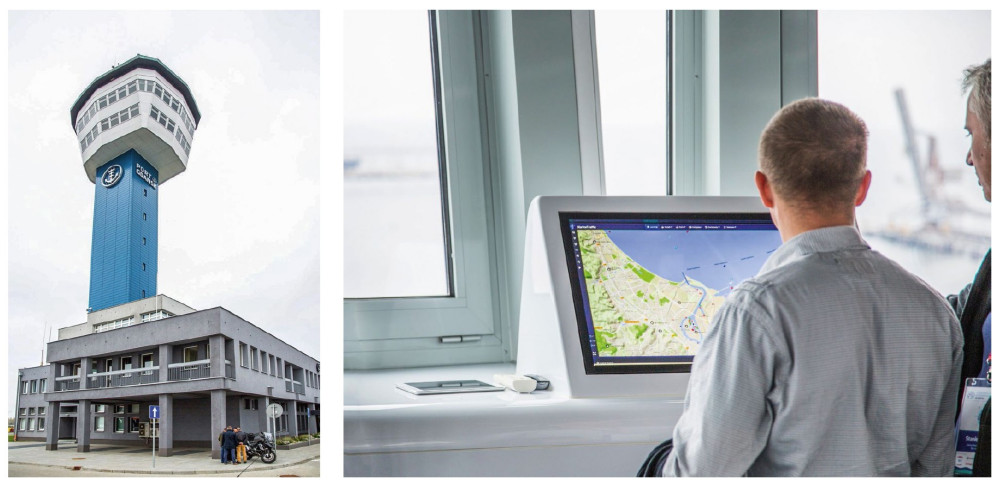
Chociaż Naftoport nie jest zakładem przemysłowym wytwarzającym towary, jego systemy i tak generują spore ilości danych. W oprogramowaniu Historian wykorzystywane jest około 1500 tagów - każdy rurociąg, a właściwe każdy odcinek rurociągu pomiędzy zaworami jest monitorowany. W każdym z przypadków wykonywane są pomiary ciśnień, temperatur, kontrolowany stan zaworów, itd. Wszystko generuje ogromne ilości danych, które można zbierać i prezentować dzięki wykorzystywanym systemom.
POZOSTAŁE NARZĘDZIA SOFTWARE’OWE DLA PRZEMYSŁU WYKORZYSTYWANE W NAFTOPORCIE
Trzecim i najmłodszym z wykorzystywanych elementów pakietu Proficy jest Webspace. Firma wdrożyła go w celu zastąpienia klasycznych stacji klienckich rozwiązaniem webowym. Możliwość dostępu do danych przez sieć Ethernet/Internet rozwiązała wiele problemów organizacyjnych, w szczególności nie było konieczne powiązanie danej stacji klienckiej z konkretnym komputerem oraz zarządzanie kluczami programowymi.
Webspace dał jeszcze jedną możliwość - łatwej dywersyfikacji wyświetlanych informacji. Przykładowo dysponenci i operatorzy na stanowiskach korzystają ze swoich ekranów z informacjami technologicznymi, ochroną PPOŻ i innymi podstawowymi dla nich informacjami. Nie są oni natomiast zainteresowani zagadnieniami takimi jak energetyka, ogrzewanie, itd., choć te systemy są również objęte przez oprogramowanie SCADA.
Takimi danym są zainteresowani zarządzający firmą oraz eksploatacją. Korzysta się tu właśnie z możliwości Webspace w zakresie prezentacji dostępnych danych. Do tego dochodzą dodatkowe obszary jego użycia - m.in. związane z generowaniem raportów.
NA KONIEC SPOJRZENIE NA CAŁY PORT GDAŃSK I JEGO PRZYSZŁOŚĆ
Ten temat omówił na koniec wizyty referencyjnej Krzysztof Zalewski, specjalista ds. marketingu i relacji zagranicznych w Porcie Gdańsk:
Jesteśmy największym portem w kraju - odpowiadamy za około połowę wszystkich przeładunków i prawie 70% rodzimego rynku kontenerowego. Staliśmy się również hubem, czyli portem przeładunkowym dla tego regionu Europy. Około 30% przybywających do nas kontenerów jest przeładowywanych i wypływa dalej na basen Morza Bałtyckiego.
Biorąc pod uwagę wszystkie porty na Bałtyku, po pierwszym półroczu 2018 roku plasowaliśmy się na czwartej pozycji pod względem przeładunków ogółem - do tej pory zajmowaliśmy miejsce 6. Aczkolwiek, z perspektywy obrotu kontenerowego, dwa porty - tj. Gdańsk i Gdynia, które są oddalone od siebie o kilkanaście kilometrów, funkcjonują praktycznie jak jeden - a to już daje na naszym akwenie pozycję wiodącą.
Obsługujemy największe statki, czyli o zanurzeniu do 17 metrów. Dzięki temu mogą do nas zawijać wszystkie jednostki pływające po Bałtyku. Dodatkowo nie występują tutaj pływy, czyli nie zmienia się poziom wody. Mamy również przewagę związaną z niezamarzaniem w okresie zimowym. Ewentualne lekkie zamrożenie wody nie wymaga żadnych operacji. To spora przewaga w stosunku np. do portu w Petersburgu, który może być zamrożony nawet przez kilka miesięcy w roku.
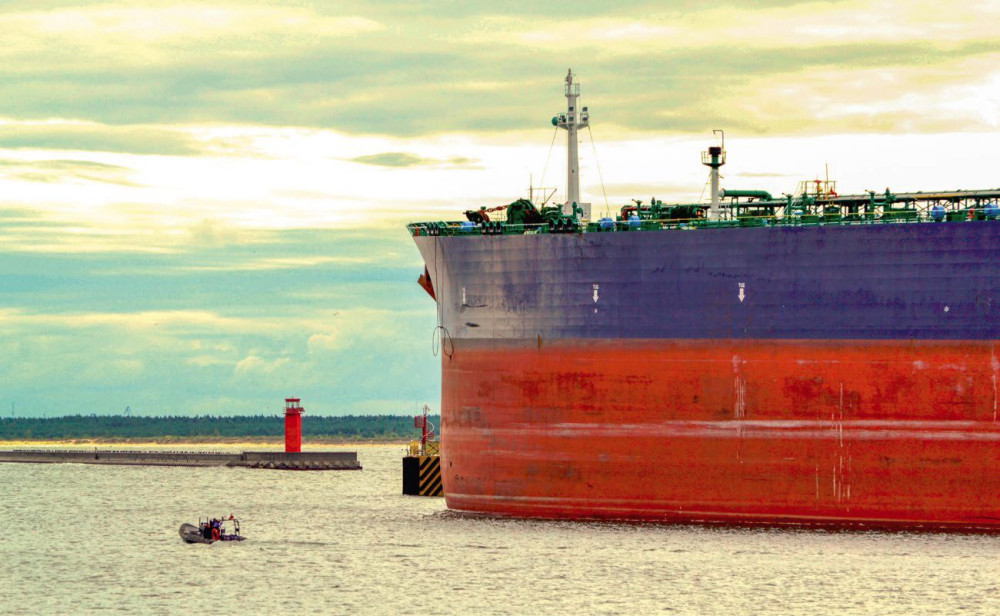
Port Gdańsk sukcesywnie zwiększa swoje przeładunki. W 2017 roku przekroczyliśmy historyczną granicę 40 mln ton przeładowanych towarów, zaś po 6 miesiącach 2018 roku zanotowaliśmy najwyższą w Europie dynamikę wzrostu na poziomie 35%.
Jesteśmy portem zróżnicowanym: drobnica to u nas około 44%, zaś paliwa płynne stanowią 1/3 naszych przeładunków. Bardzo prężnie rozwijamy branżę automotive - w 2016 roku przeładowaliśmy 14 tys. samochodów, a w 2017 było ich już ponad 80 tysięcy. Ta dywersyfikacja daje nam stabilną pozycję na rynku.
Jeżeli chodzi o paliwa płynne, to roczna zdolność przeładunkowa Naftoportu wynosi około 40 mln ton, zaś obecnie firma działa na poziomie 12-13 mln ton rocznie - tyle bowiem zostało przeładowane ropy naftowej i jej produktów w 2017 roku. Oznacza to, że istnieje spory zapas w zakresie przepustowości, co daje też ogromne zaplecze do dalszego wzrostu koniunktury.
Aby wyjść naprzeciw przyszłym wzrostom, zarząd Portu Gdańsk podjął działania w celu budowy Portu Centralnego. Maksymalna powierzchnia terenu na to przeznaczonego wyniesie 500 ha, zaś w efekcie inwestycji zdolność przeładunkowa portu się podwoi.
Chcemy przy tym wdrożyć wiele nowości technicznych - np. pracujemy z firmą Siemens nad elektrycznym ładowaniem statków, mamy też wszystkie badania i studium wykonalności systemu tankowania statków skroplonym gazem. W 2019 roku odbierzemy koncepcję inwestycji, terminale będą powstawać etapami, w zależności od potrzeb prywatnych partnerów, zaś w 2027 mamy ambicję zakończyć budowę.
Zbigniew Piątek
*) DWT (deadweight tonnage) - nośność statku, podstawowy parametr określający wielkość statku oznaczający jego zdolność przewozową. DWT to łączna masa ładunku, załogi, paliwa, wody, prowiantu, części zamiennych, itd., jaką statek może przyjąć na pokład, nie przekraczając dopuszczalnego zanurzenia.