Z czego korzysta polski przemysł?
Spektrum narzędzi softwarowych wykorzystywanych w przemyśle obejmuje wiele ich grup, przy czym podstawą są tu systemy SCADA/ HMI. Występują one w szerokim zakresie aplikacji – od pojedynczych maszyn i małych układów, poprzez systemy średniej wielkości, aż do dużych, rozproszonych instalacji. Pakiety te są też często wdrażane razem (lub zintegrowane) z bazami danych oraz narzędziami historian. Użytkownicy rozszerzają ich funkcjonalność o dalsze narzędzia pozwalające na analizę danych i raportowanie, których rozwój przyspieszył szczególnie w epoce Przemysłu 4.0. Do tego dochodzą aplikacje do monitorowania procesów wsadowych i oczywiście kolejny poziom oprogramowania obejmujący systemy zarządzania produkcją MES. Te ostatnie umożliwiają m.in. planowanie, harmonogramowanie i nadzór nad procesami oraz realizację innych zadań w czasie rzeczywistym. Jeżeli zaś chodzi o obszar związany z narzędziami CAD/ CAM, EDA, itd., to pomijamy go celowo, gdyż jest to tematyka wykraczająca poza ramy bieżącego badania.
Patrzenie na systemy przemysłowe przez pryzmat piramidy czy też kolejnych poziomów oprogramowania jest w branży dosyć częste, choć w praktyce trudno – głównie ze względu na zróżnicowanie pakietów proponowanych przez firmy – dokonać jednoznacznej kategoryzacji i segmentacji dostępnej oferty rynkowej. Pozostając jednak przy zarysowanym podziale, spójrzmy na popularność poszczególnych grup produktów na rynku krajowym. Przedstawiono to w statystyce na rys. 1. Dominują tu wskazania oprogramowania SCADA/ HMI – zarówno prostszego, do pracy w mniejszych instalacjach, jak też bardziej rozbudowanego. Następne pod względem liczby wskazań są: narzędzia do raportowania, bazodanowe i zintegrowane pakiety do zarządzania produkcją. Finalnie mamy narzędzia analityczne, w przypadku których, co warte odnotowania, zaobserwować można największy wzrost procentowy w stosunku do stanu sprzed dwóch i czterech lat.
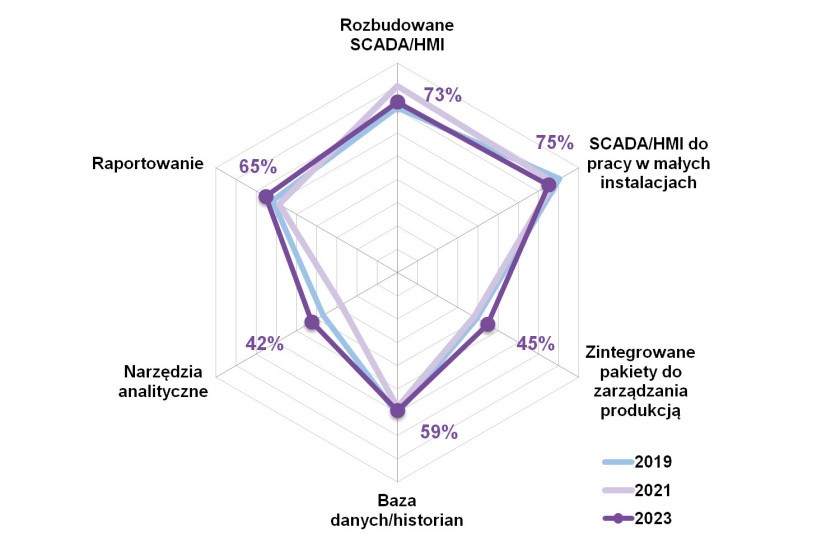
Przemysł, energetyka, maszyny
Zastosowania oprogramowania dotyczą zarówno różnych sektorów przemysłu (motoryzacja, metalowy, spożywczy, różne branże procesowe), jak też m.in. energetyki, obszaru budynkowego czy wod-kan oraz naturalnie zastosowań maszynowych. To szerokie spektrum przekłada się dużą liczbę aplikacji i zróżnicowanie potrzeb odbiorców. Również sami dostawcy działają często w kilku branżach jednocześnie, oferując oprogramowanie dostosowane do potrzeb tych rynków (w tabelach podajemy to w wierszu: "wersje rozszerzone dla konkretnych branż").
Wymienione powyżej sektory pojawiły się, choć w nieco innej kolejności, w zestawieniu wyników badań dotyczących rynku krajowego (rys. 2). W kontekście lokalnej gospodarki najważniejszymi branżami końcowymi są: energetyka, sektor spożywczy i chemiczny, branża wod-kan i maszynowa (OEM).
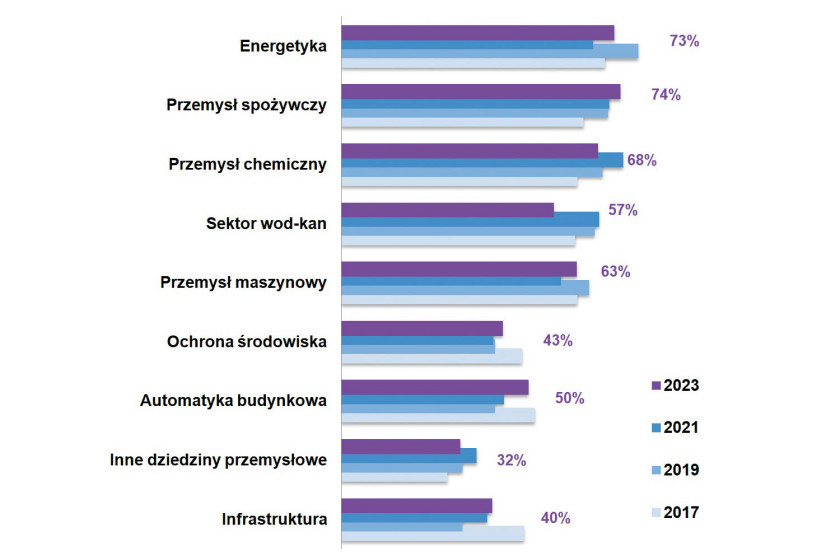
Sektor oprogramowania przemysłowego znajduje się na długoterminowej ścieżce rozwojowej, a sprzedaż pod względem wartościowym zwiększa się (z wyjątkiem okresów dekoniunktury i fluktuacji rynkowych). Tym, co w ostatnich latach odróżniało go od szerokiego rynku technologii przemysłowych – np. automatyki czy sterowania – był wpływ pandemii i jej skutków. Okres lockdown’ów miał ogromne reperkusje gospodarcze, aczkolwiek w obszarze oprogramowania przemysłowego trudno specjalnie mówić o negatywach. Wymogi pracy zdalnej i zapewniania reżimu sanitarnego niewątpliwie sprzyjały cyfryzacji, a wiele firm przyspieszało wdrożenia oraz rozbudowywało swoje możliwości w zakresie m.in. korzystania z urządzeń mobilnych czy pracy zdalnej. I działo się to wszędzie, niezależnie od sektora gospodarki.
Opisywany trend wzrostowy, na który nakłada się również wzrost inflacyjny, wyraźnie widać, gdy porównamy gromadzone przez nas od kilkunastu lat dane. O ile na początku zeszłej dekady wartość sektora związanego ze sprzedażą licencji i wdrażaniem systemów SCADA/HMI wynosiła od 35 do 50 mln zł rocznie, o tyle w ostatnich raportach publikowaliśmy kwoty wynoszące około 100 mln zł. Dokonując uśrednienia liczb proponowanych przez respondentów obecnego badania rynku, możemy podać wartość 160 mln zł, a nawet nieco większą, jeżeli uwzględnimy wskazania odstające.
Jeżeli chodzi o wartość całego rynku oprogramowania przemysłowego – od HMI i SCADA, poprzez oprogramowanie historian i bazodanowe, analityczne, aż po systemy zarządzania produkcją – to jego wielkość jest naturalnie większa. O ile? Podanie nawet przybliżonych wartości jest w tym przypadku trudne. Dwa lata temu respondenci sugerowali tu kwoty od 30 mln do miliarda, zaś średnia wyniosła 120 mln zł. W tym roku rozrzut wartości był podobny, natomiast średnia to 250 mln zł – i wartość tę bierzemy w nawias. Badanie nie miało cech poprawności statystycznej, a jego wynik można co najwyżej przyjąć jako kolejną, zgrubną informację.
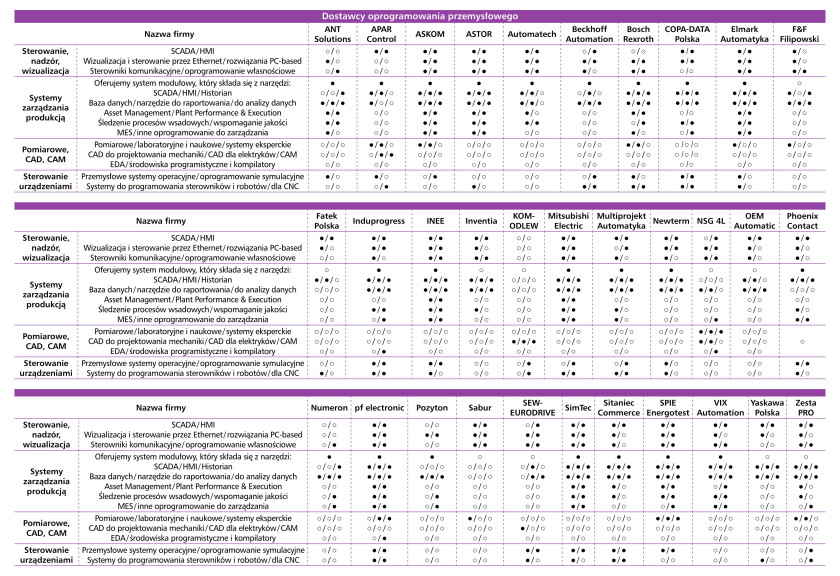
Jakie są potrzeby odbiorców krajowych?
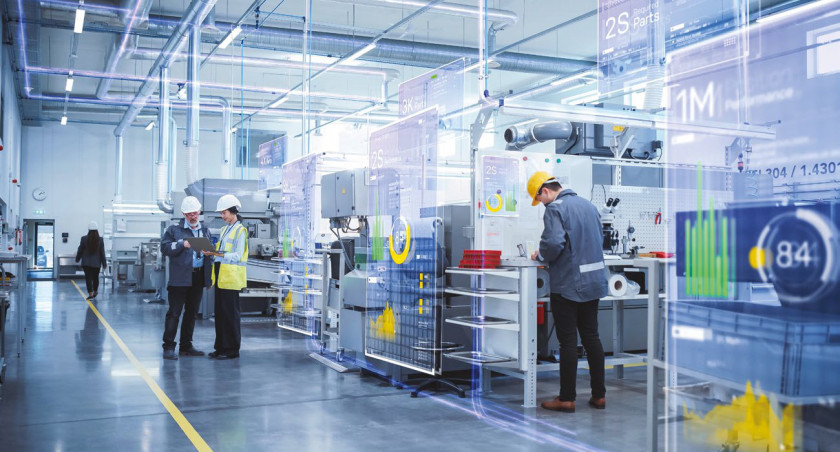
Zdaniem dostawców jedynie część klientów poszukujących oprogramowania jest w pełni świadoma tego, czego rzeczywiście szuka (rys. 3). Zazwyczaj konieczna jest obszerna rozmowa na temat potrzeb, ich precyzyjne określenie, a nieraz wręcz odkrycie – tak przyznało ponad 70% ankietowanych. Zdaniem co trzeciego respondenta wdrożenia software’u wiążą się z koniecznością zmian o charakterze sprzętowym (również na rys. 3).
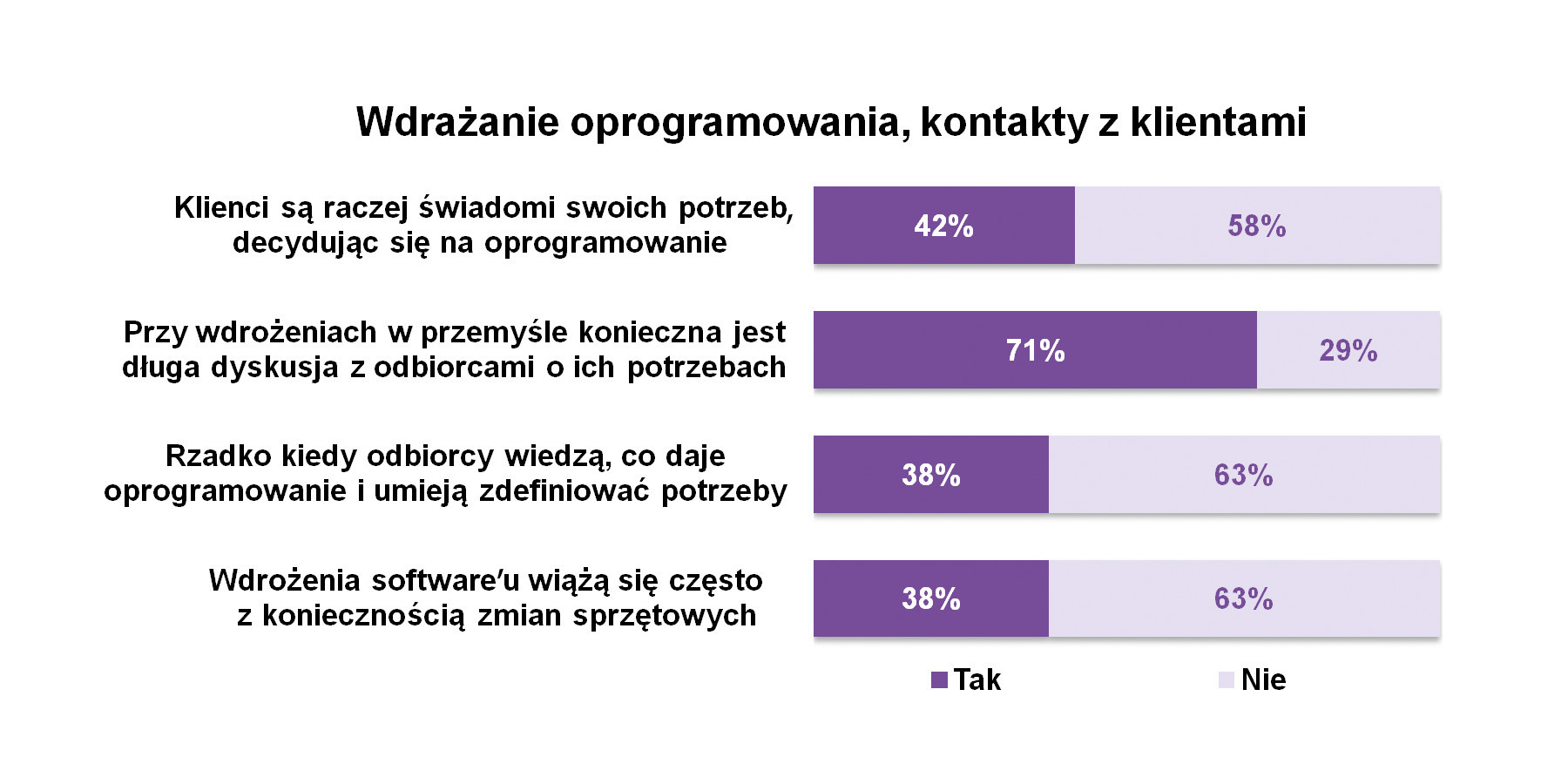
Jakie konkretnie cechy oprogramowania są najważniejsze z perspektywy integratorów, wdrożeniowców i przyszłych użytkowników? Związane z tym informacje prezentujemy na rys. 4, gdzie zestawiono wyniki z czterech kolejnych badań rynku. Jak widać, odbiorcy koncentrują się na parametrach technicznych i kosztach wdrożenia – kategorie te od dawna pozycjonują się na czele listy wymagań. Na kolejnych miejscach znalazły się wskazania dotyczące innych cech oprogramowania, jego marki oraz decyzji integratora.
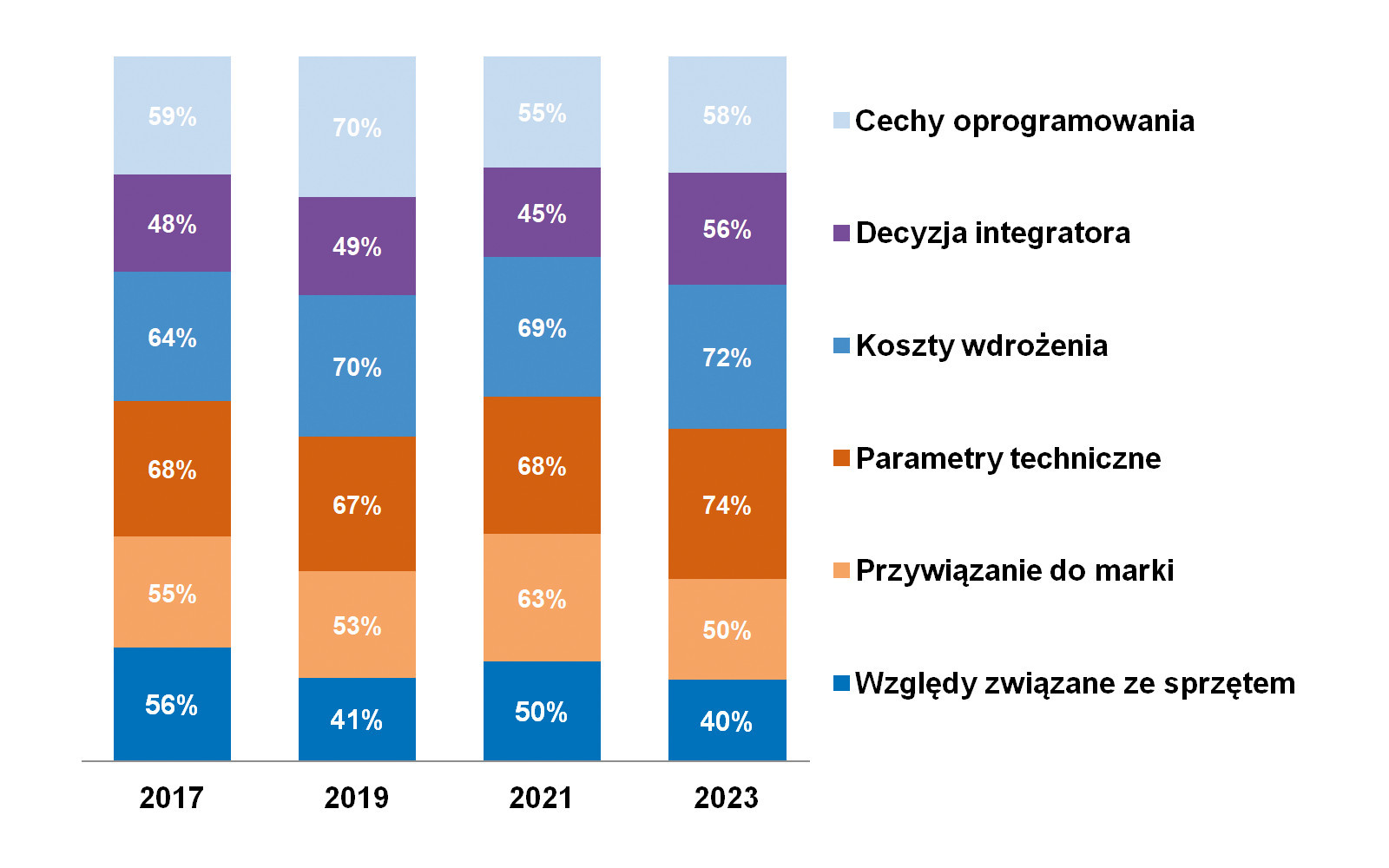
Chcąc zgłębić temat preferencji zakupowych, zadaliśmy również pytanie otwarte dotyczące tego, co jest dla odbiorców najważniejsze przy wyborze SCADA/HMI oraz systemów wspierających zarządzanie produkcją. Otrzymaliśmy tu długą listę odpowiedzi (przedstawiona w postaci chmury na rys. 5), przy czym do najczęstszych należały wskazania ceny, funkcjonalności, możliwości oprogramowania, wsparcia technicznego, marki i łatwości obsługi. Wszystko to pojawiło się już w analogicznej statystyce dwa lata temu, natomiast na wspomnianą chmurę warto spojrzeć nieco dokładniej, bowiem zawiera ona kilkadziesiąt innych, ciekawych wskazań.
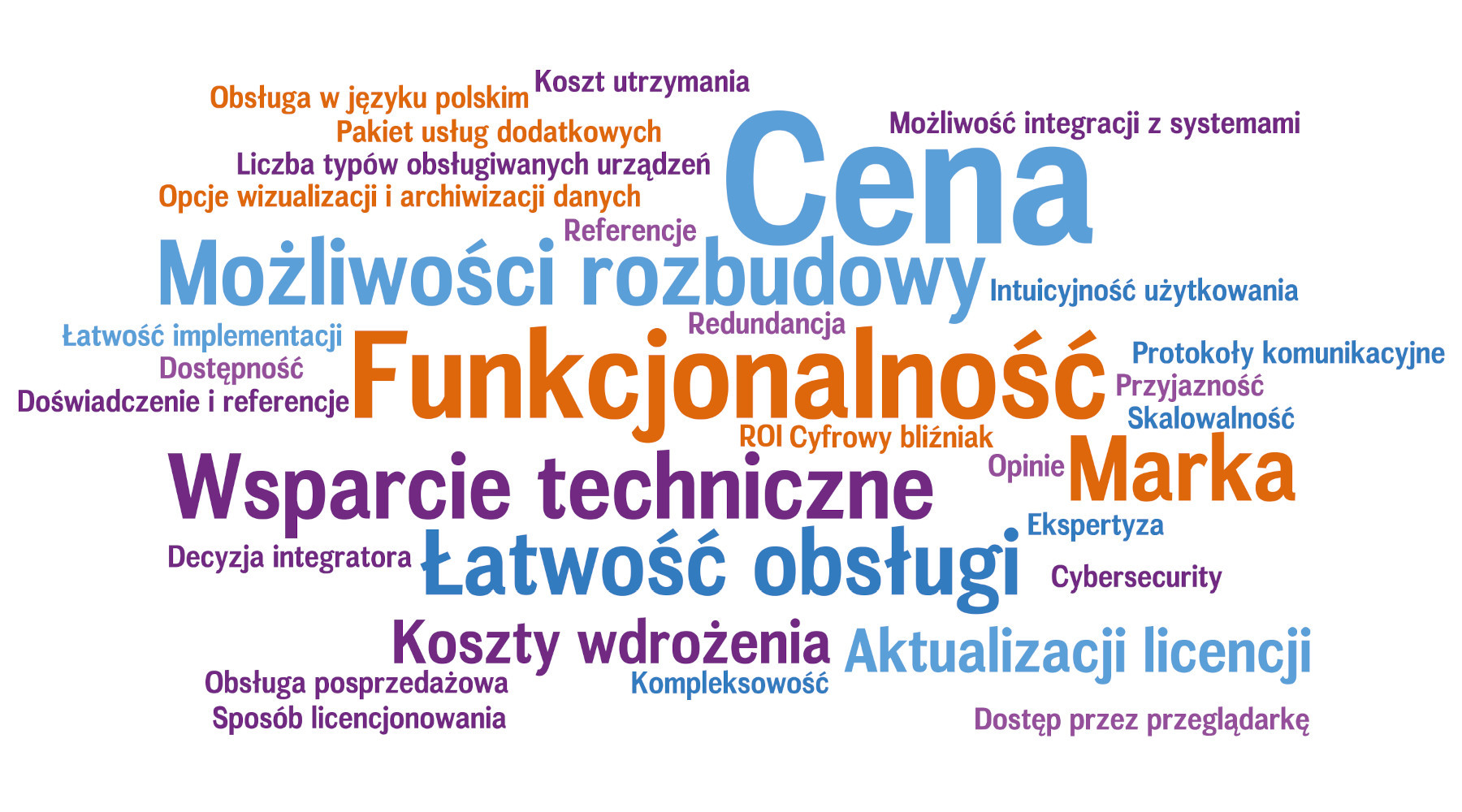
Idąc o krok dalej, można zapytać również o technologie i funkcje, które są ważne w przypadku oprogramowania stosowanego w przemyśle. Tak też zrobiliśmy, a wyniki zestawiamy na rys. 6. W tym przypadku na pierwszy plan wychodzą: chmura obliczeniowa, HTML5 i technologie webowe, obsługa protokołu MQTT, w dalszej kolejności pojawiają się m.in.: edge computing, aplikacje mobilne, zdalny dostęp i zarządzanie, OPC UA oraz technologie sztucznej inteligencji. Wiele z tych odpowiedzi widzieliśmy już w poprzednich raportach, przy czym tym razem wyraźnie wzrosła liczba wskazań dotyczących MQTT oraz AI.
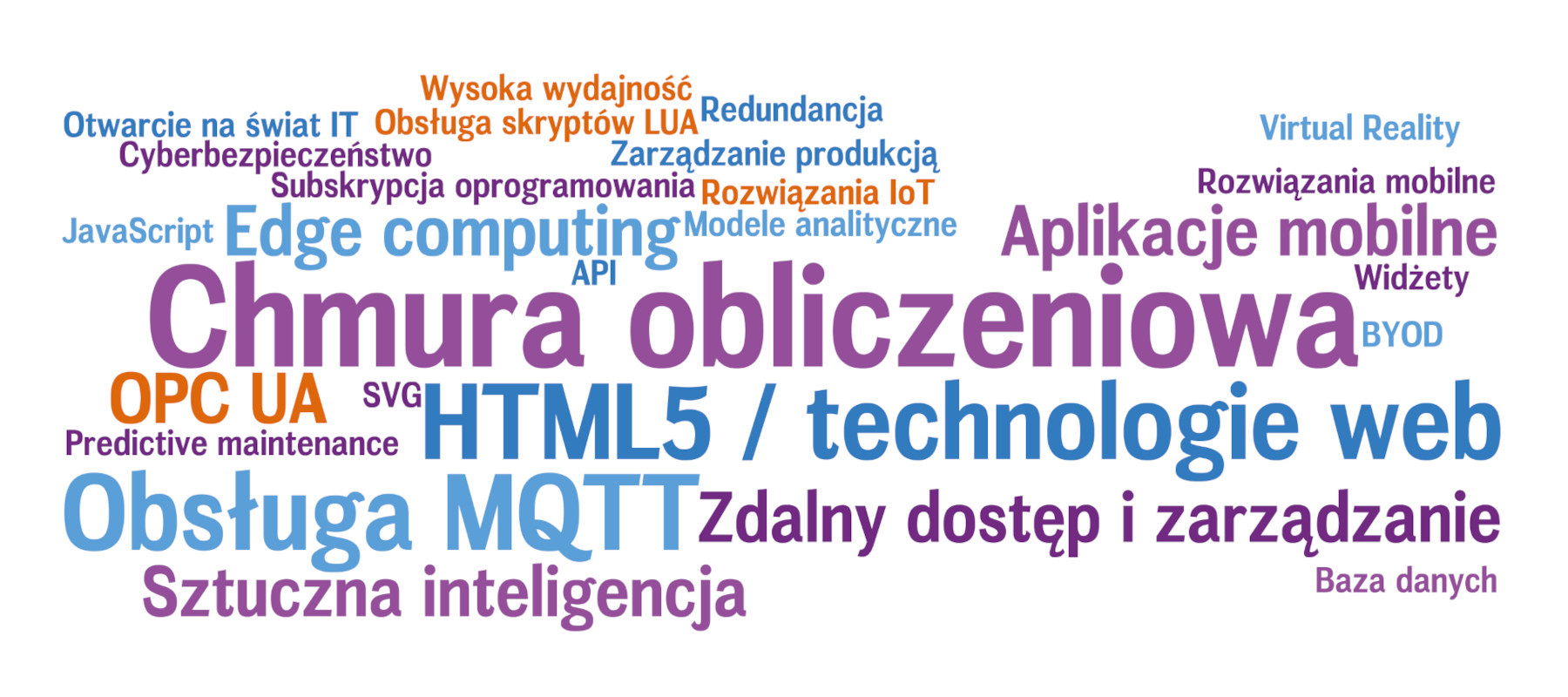
Tomasz Janiczek
ASKOM
Jakiś czas temu zaczęto forsować koncepcję Fabryki 4.0, czyli zakładu, w którym automatyzacją objęte zostały wszystkie procesy produkcyjne, a nie tylko proces bezpośredniego wytwarzania produktu. Skończyły się czasy drukowania zleceń produkcyjnych i zanoszenia ich operatorom do realizacji. Obecnie normą stało się automatyczne przesyłanie wygenerowanych w ERP zleceń na poziom systemów zarządzania produkcją MOM (Manufacturing Operations Management), gdzie w module APS są one kolejkowane i rozdzielane na konkretne maszyny czy linie produkcyjne. Obejmuje to uwzględnienie ich aktualnego obłożenia oraz parametrów technicznych (np. szybkości czy energochłonności), dostępności materiałów i zasobów ludzkich, z minimalizacją kosztów przezbrojeń. Możliwe jest natychmiastowe reagowanie na nieprzewidziane zdarzenia i awarie. Dalej produkcja powierzana jest systemom MES, które dbają o jej realizację zgodną z recepturami, a rejestrując wszystkie istotne parametry procesu produkcyjnego, umożliwiają odtworzenie pełnej genealogii produktów. Nad każdym etapem wytwarzania czuwa system zarządzania jakością QMS, który współpracując z systemami zarządzania laboratorium LIMS, dba o najwyższą jakość wyrobów oraz minimalizację ilości odrzutów produktów końcowych. Dzięki modułom BI kadra zarządzająca na bieżąco informowana jest o aktualnych wskaźnikach produkcyjnych, zasilana niezbędnymi raportami i zestawieniami. Dane o realizacji zleceń wraz z faktyczną ilością zużytych materiałów trafiają z powrotem do ERP, umożliwiając dokładne planowanie zakupów.
Klienci w pełni zaakceptowali powyższy sposób działania i nie wyobrażają już sobie innej rzeczywistości. Oczekują kompleksowych rozwiązań, które zaspokoją ich wszystkie potrzeby, również te przyszłe. Dlatego ważne jest, żeby systemy MES / MOM były otwarte i miały modułowy charakter, który ułatwia dostosowanie aplikacji do wymagań klienta, nie zamykając drogi do zaspokojenia jego przyszłych potrzeb. Idealnym przykładem takiego podejścia jest platforma Opcenter firmy Siemens, która jest w stanie zaspokoić najbardziej wyrafinowane oczekiwania klientów, przy tym, dzięki skalowalności, nadaje się również świetnie dla mniejszych procesów produkcyjnych. Oczywiście systemy SCADA to nadal must have, są one niezastąpione w systemach sterowania, stanowiąc jednocześnie źródło danych dla oprogramowania wyższego rzędu. Ale w obecnych czasach to zdecydowanie za mało, żeby mówić o nowoczesnej i optymalnej produkcji. |
Kto jest kim na rynku?
Zanim przejdziemy do omawiania szczegółów dotyczących kluczowych trendów technologicznych, spójrzmy na rynek dostawców oprogramowania. W tym przypadku mamy do czynienia z relatywnie stałą grupą dobrze rozpoznawalnych firm. W raporcie, a dokładniej w tabelach z ofertami, zawarto szczegóły dotyczące ponad 30 przedsiębiorstw. Obejmuje to większość głównych dostawców branżowych działających w polskim przemyśle. Tradycyjnie do tej listy należy dodać Siemensa, który nie bierze udziału w redakcyjnych raportach.
Zestawione firmy tworzą dwie grupy podmiotów. Jedną są przedstawicielstwa producentów zagranicznych (lub producentów lokalnych) – takimi są m.in.: ABB, ASKOM, Beckhoff Automation, COPA-DATA Polska, Mitsubishi Electric, Phoenix Contact, Rockwell Automation, SEW-EURODRIVE oraz Siemens. Drugą tworzą dystrybutorzy, w przypadku których wymienić można przykładowo firmy: ASTOR, Elmark Automatyka, Multiprojekt Automatyka, RAControls, SABUR, VIX Automation. Cześć z tych przedsiębiorstw prowadzi również działalność wdrożeniową.
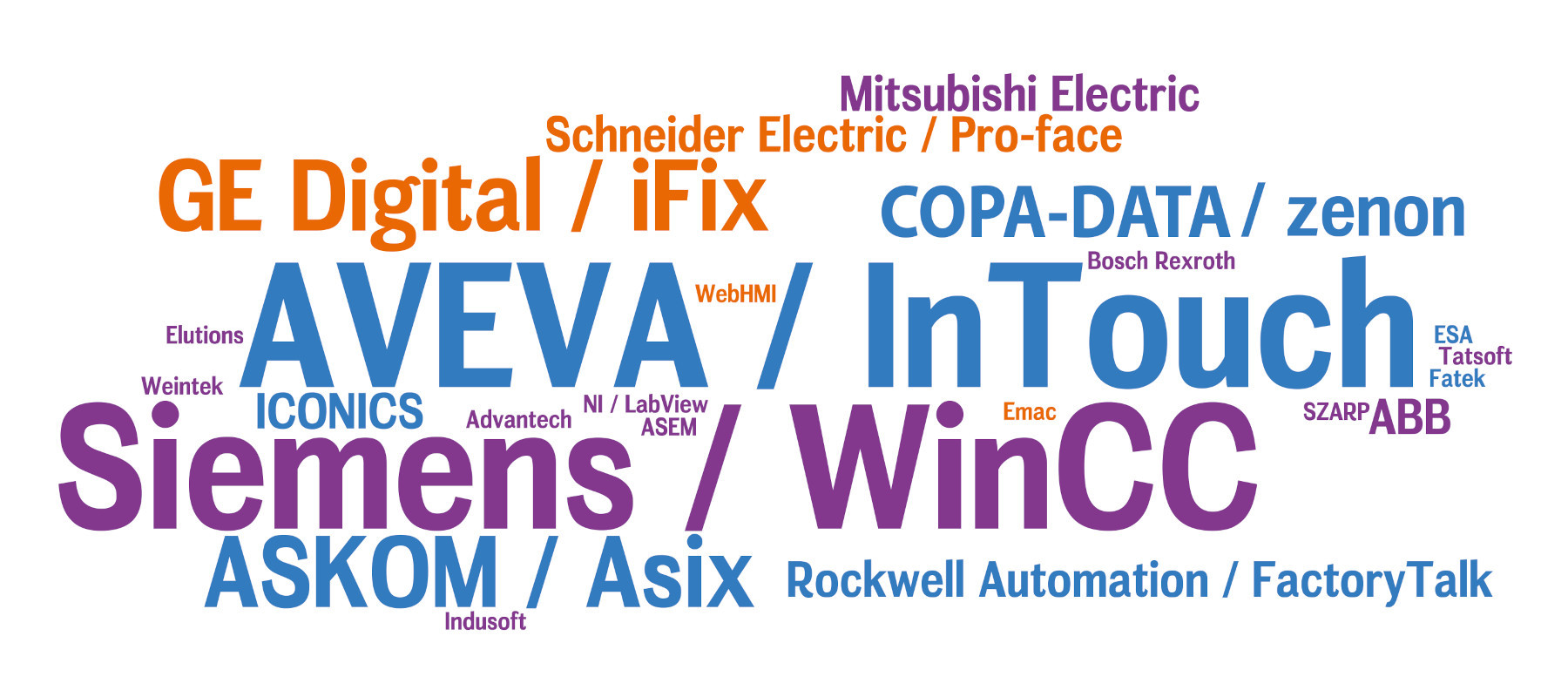
Na rys. 7 zawierającym chmurę nazw przedstawiono popularne marki oprogramowania SCADA/HMI, przy czym w przypadku części z nich uwzględniono też producentów i dystrybutorów software’u. Zestawienie tradycyjnie nie odzwierciedla wielkości sprzedaży produktów, a jedynie ich popularność na rynku w opinii ankietowanych dostawców.
W tym miejscu dodajmy jeszcze jedną statystykę – mianowicie dotyczącą biznesu związanego z oferowaniem oprogramowania (patrz rys. 8). Jej zawartość jest praktycznie identyczna jak w przypadku badania sprzed dwóch lat i można tu wyodrębnić trzy w miarę równorzędne segmenty: związane z oprogramowaniem standardowym, pakietami zaawansowanymi oraz z usługami wdrożeniowymi. Na tych trzech elementach dostawcy zarabiają najczęściej.
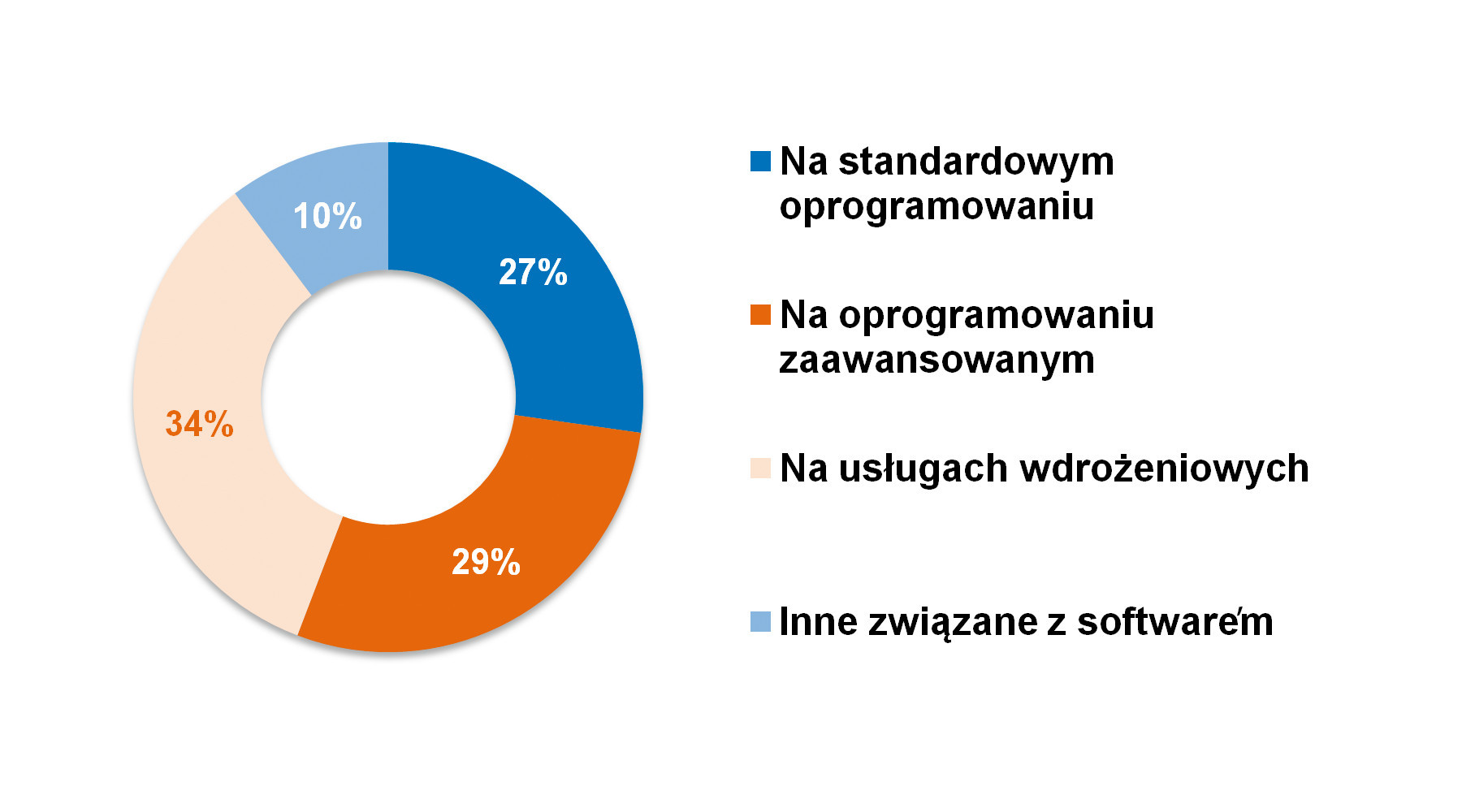
Analityka i Big Data
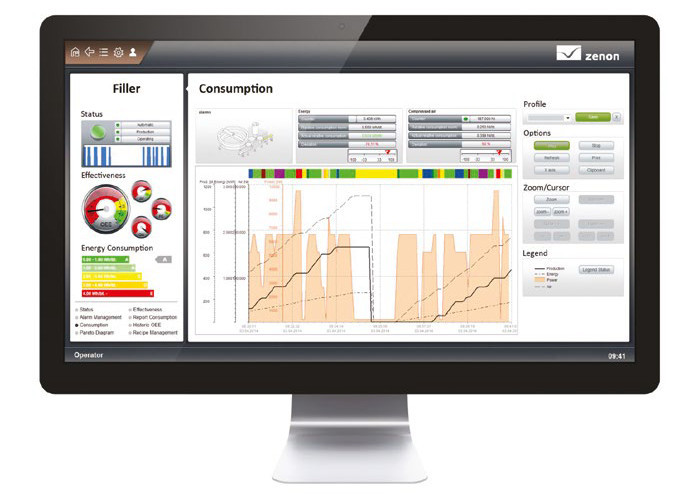
Tematykę technologiczną rozpoczynamy od omówienia kwestii przetwarzania i analizy danych. W tym zakresie niewątpliwie ważnym pojęciem jest Big Data, z którym wiąże się przetwarzanie i analiza ogromnych, różnorodnych zbiorów danych. W przypadku przemysłu pozwala ona analizować procesy, zwiększać ich efektywność i zmniejszać koszty. Czy tak się dzieje? I tak, i nie. "Rosnące zainteresowanie tematyką Przemysłu 4.0 wiąże się z poznawaniem wartości płynącej z Big Data" – zauważa jeden z respondentów. Drugi zaś dodaje: "tematy związane z uczeniem maszynowym i AI cieszą się coraz większym zainteresowaniem np. w predictive maintenance".
Obydwa spostrzeżenia są słuszne, bowiem analiza jest bardzo często tematem integralnym z Przemysłem 4.0, a rozwiązania z tego obszaru są wdrażane w konkretnych, często specjalizowanych obszarach – jak utrzymanie ruchu. I finalnie kwestia opłacalności, racjonalności wdrożeń. "Granice Big Data są na razie na tyle mało sprecyzowane, że trudno o tym mówić klientom – łatwiej przedstawiać konkretne zagadnienia i przykłady rozwiązań, niż reklamować to hasłowo jako Big Data" – to trzecia, również słuszna opinia.

Jak wyglądają statystyki? Zasadniczo niczego nowego z nich się nie dowiadujemy (rys. 9). Głosy dotyczące popularności Big Data rozłożone są nadal w stosunku 50:50, jednocześnie cały czas średnio 4 na 10 osób uznaje, że tymi zagadnieniami interesują się raczej wybrane branże. Również nikt, ani jeden z respondentów, nie poddał w wątpliwość sensowności zajmowania się tą tematyką w kontekście przemysłu. Podsumowując – moglibyśmy w tym miejscu pokazać analogiczny wykres z raportu z 2021 roku.
Można sądzić, że dzisiaj – pomimo postępów w metodach analizy danych i rozwoju Przemysłu 4.0, cały czas przetwarzanie i wnioskowanie na podstawie dużych (nie mówiąc o ogromnych) zbiorów danych nie jest powszechne. Do tej tematyki na pewno najbliżej branżom procesowym i dużym firmom, gdzie potencjalne korzyści np. z optymalizacji produkcji i przetwarzania mogą być największe. Jednocześnie w wielu "standardowych" narzędziach pojawiają się funkcje dające coraz lepsze możliwości analizy (choć nie Big Data). Być może, wraz z popularyzacją algorytmów uczenia maszynowego i sztucznej inteligencji, to właśnie one przyniosą kolejne istotne zmiany. Być może również technologie te staną się na tyle popularne i łatwe do wykorzystania, że w kolejnym raporcie nie będziemy już śledzili tematyki Big Data, a skupimy się na wnioskowaniu z wykorzystaniem AI. To wysoce prawdopodobne, patrząc na rozwój sztucznej inteligencji w ostatnich latach i miesiącach!
Igor Żukowicz-Szczepański
COPA-DATA Polska
Systemy SCADA mają szereg zastosowań w nowoczesnym przemyśle. Są szczególnie ważne w branżach regulowanych przepisami i normami prawnymi, ale również wszędzie tam, gdzie zarząd chce udoskonalić produkcję i zoptymalizować koszty. Systemy SCADA są stosowane m.in. w branży energetycznej, farmaceutycznej, motoryzacyjnej oraz spożywczej.
Klienci poszukują skalowanych systemów umożliwiających ich szybkie wdrożenie w środowisku produkcyjnym. Ważne jest, aby oprogramowanie spełniało specjalistyczne normy takie jak FDA 21 CFR część 11 czy aneks 11 do wytycznych GMP UE. Istotnym argumentem przy wyborze takiego oprogramowania są również możliwości komunikacyjne z różnymi protokołami przemysłowymi jak np.: MQTT, OPC UA, S7 TIA, Allen-Bradley ODVA, Modbus TCP, DLMS, BACnet oraz systemami jak np.: SAP ERP, Werum PAS-X. Takie możliwości zapewnia Platforma Systemowa zenon.
W tym przypadku warto sprawdzić, czy oferowane przez niego oprogramowanie umożliwia komunikację z posiadanym parkiem maszynowym. Najlepiej jest, gdy system SCADA ma nieograniczone możliwości komunikacyjne, co pozwala w przyszłości rozbudowywać park maszynowy w dowolny sposób – bez ograniczeń i tworzenia podziałów. Należy również zwrócić uwagę na archiwizowanie oraz bezpieczeństwo danych. Ważne jest, żeby system umożliwiał analizę zebranych danych za pomocą specjalistycznych raportów. Dostęp do danych powinien być możliwy z dowolnego autoryzowanego miejsca. Warto również sprawdzić referencję danego producenta w interesującej nas dziedzinie oraz to, jak długo działa na rynku oprogramowania. Wreszcie, przy wyborze oprogramowania, należy zwrócić uwagę na elastyczny i wysokiej jakości dział wsparcia technicznego, a także dopasowaną ofertę szkoleń.
Jako producent oprogramowania opieramy nasz model biznesowy na współpracy z wykwalifikowanymi i zaangażowanymi organizacjami w globalnej sieci najróżniejszych specjalistów. Integratorzy systemów, producenci OEM i konstruktorzy maszyn zapewniają najlepsze możliwe wdrażanie oprogramowania zenon dla naszych klientów końcowych i tworzą fundament wspólnego sukcesu. |
Chmura coraz popularniejsza, ale nie wszechobecna
Kwestia przetwarzania chmurowego wygląda nieco inaczej niż w przypadku Big Data. Z pewnością przemysł rok po roku staje się coraz bardziej otwarty na usługi chmurowe, choć podejście potencjalnych użytkowników w dużym stopniu zależy od branży, rodzaju zakładu i innych uwarunkowań. Jednak nawet w przypadku dawniej niechętnych osób postrzeganie tematu zmienia się in plus – stwierdzają respondenci. Cytując jednego z nich: "nastąpiło przejście ze stanu ‘chmura absolutnie nie’ do ‘może być’". Z kolei inni dodali, że: "obserwujemy mocną rozbudowę funkcjonalności chmury obliczeniowej w sektorze oprogramowania przemysłowego", a możliwości z nią związane są interesujące, bowiem "nie wymagają utrzymywania własnej infrastruktury oraz zarządzania nią".
Ostatnie zdanie jest bardzo ważne, bowiem do chmury można przenieść nie tylko dane, ale też obliczenia i procedury związane z analizami dużych ilości informacji. A gdy trafiają one poza serwery firmowe, odciąża się tym samym infrastrukturę IT przedsiębiorstwa. Dodatkowo chmura zapewnia coraz częściej możliwości prowadzenia zaawansowanych analiz z wykorzystaniem algorytmów sztucznej inteligencji. Jest ona również istotna w kontekście wdrożeń Internetu Rzeczy, stanowi też atrakcyjną propozycję dla dużych producentów, tj. firm z wieloma lokalizacjami jednostek produkcyjnych.
Warto zauważyć, że rozwiązania chmurowe od lat rozwijają zarówno dostawcy oprogramowania dla przemysłu, jak też tego typu ofertę mają firmy z branży IT. Te ostatnie kierują ją do odbiorców często wraz z pakietami ERP czy MES. Jednakże przemysł ma wciąż zastrzeżenia wobec chmury, co jest głównie związane z kwestiami bezpieczeństwa. Był to najczęściej wymieniany czynnik hamujący popularyzację cloud computingu. "Odbiorcy chętnie przyjmują systemy chmurowe, gdy rozwieje się ich wątpliwości – głównie co do bezpieczeństwa systemów" – stwierdza jeden z naszych respondentów. Stąd też, jeżeli firmy próbują swoich sił z technologiami chmurowymi, robią to początkowo często w ograniczonym zakresie. Jeden z przedstawicieli podsumował to stwierdzeniem: "do chmury wypuszczane są wybiórcze, mało wrażliwe dane".
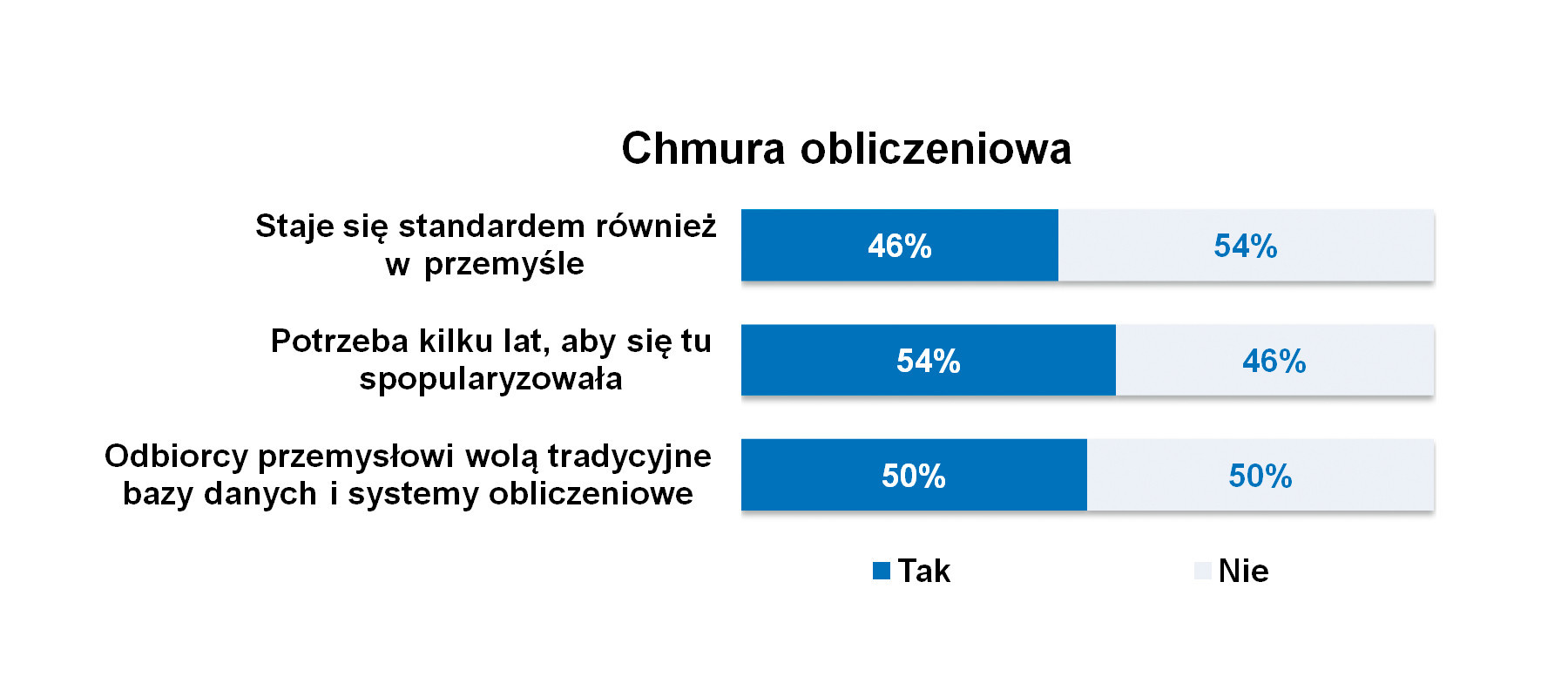
Ogólne zmiany w percepcji i wykorzystaniu chmury obliczeniowej potwierdzają nasze badania. O ile cztery lata temu co czwarty ankietowany uznawał, że chmura staje się w przemyśle czymś standardowym, zaś dwa lata temu był to już co trzeci z respondentów, o tyle dzisiaj tak stwierdza blisko połowa osób. Chociaż w omawianej kategorii wystąpiły wzrosty, to w przypadku dwóch pozostałych (na rys. 10) wskazania zmieniły się bardzo nieznacznie. Nadal wiele osób uznaje, że droga do pełnej popularyzacji chmury jest jeszcze odległa. Również użytkownicy przemysłowi w dużej części preferują tradycyjne bazy danych i systemy obliczeniowe.
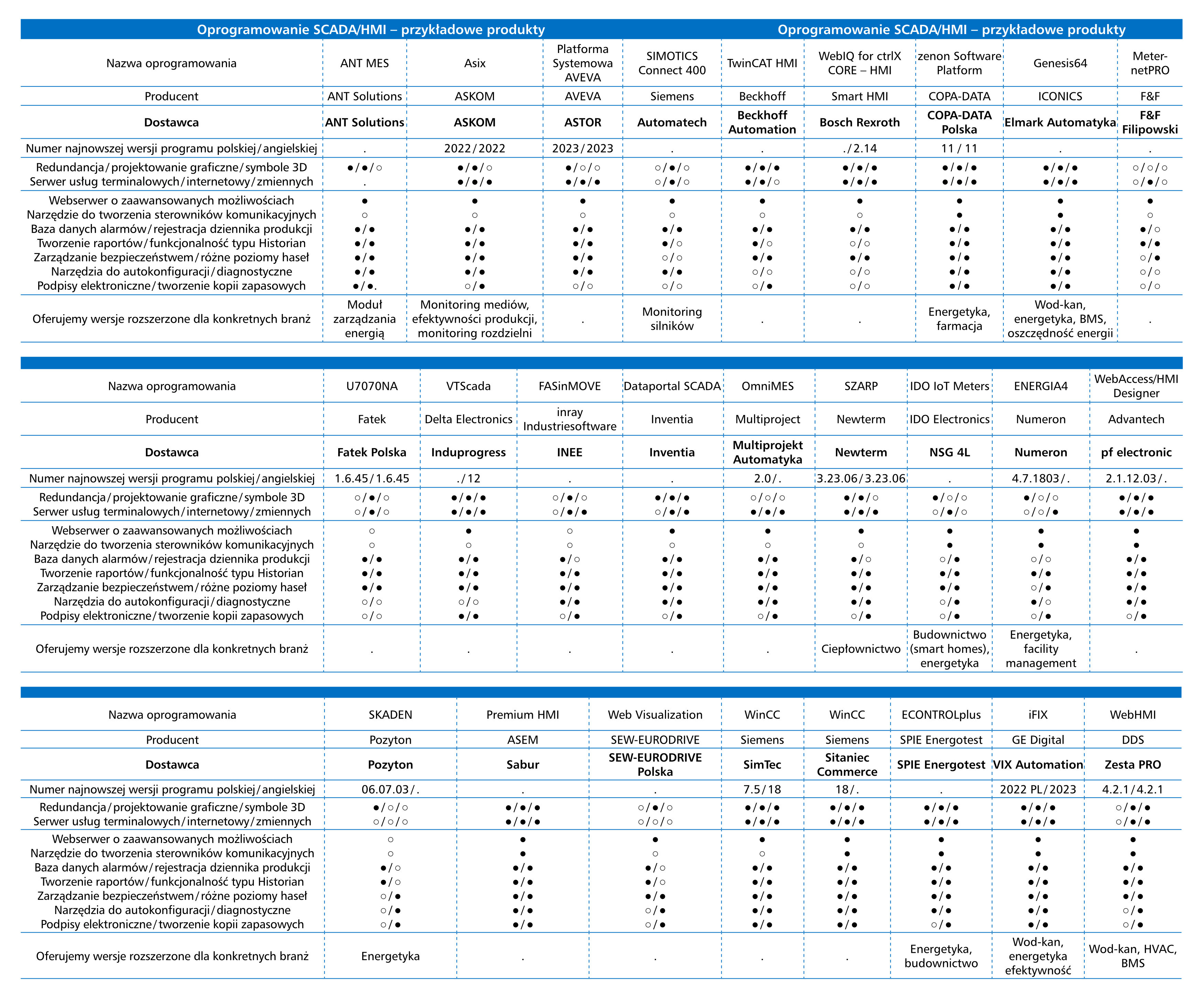
Dostęp z wykorzystaniem urządzeń mobilnych
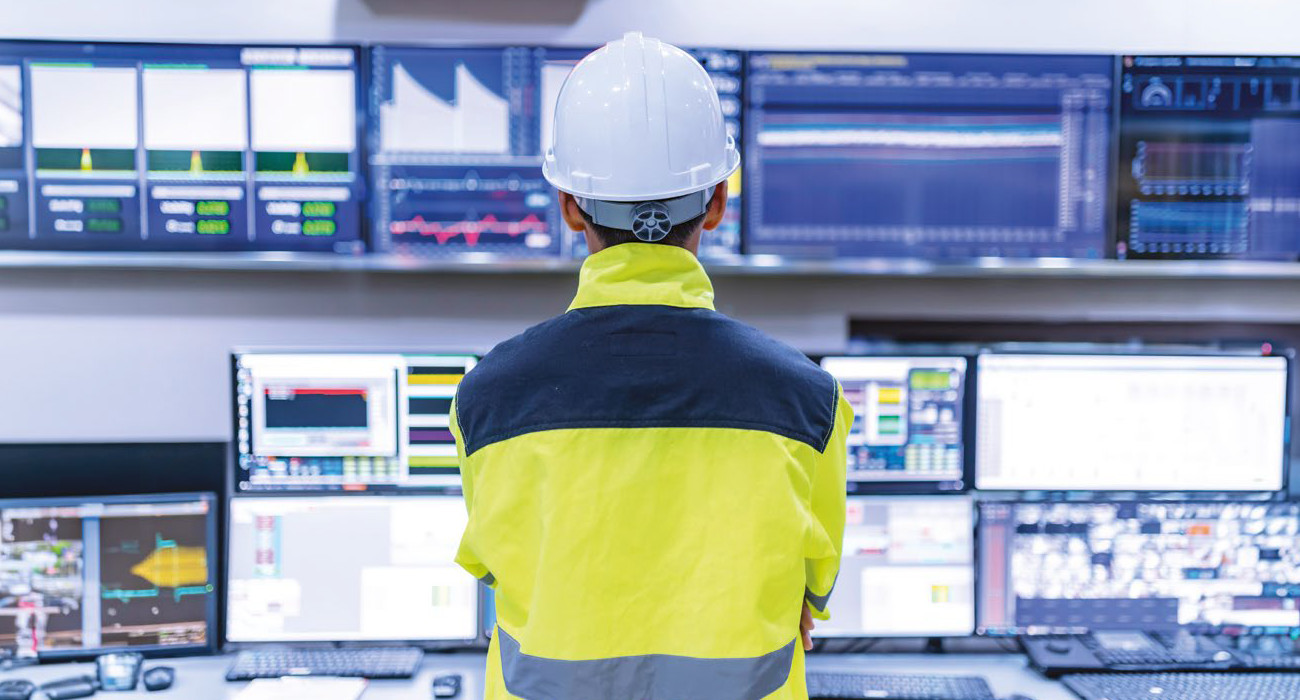
"W dobie ogólnej dostępności informacji wszyscy chcą mieć dostęp do danych z dowolnego miejsca i urządzenia" – stwierdził jeden z naszych respondentów. To prawda. Potrzeby te są nie tylko powszechne, ale też coraz bardziej widoczne w branży przemysłowej. Tablety i smartfony są codziennymi narzędziami tutejszych pracowników, w tym automatyków i personelu utrzymania ruchu. Mobilny dostęp umożliwia im przeglądanie informacji, wykonywanie zadań związanych z kontrolą stanowisk pracy, a także serwisowanie i zdalną obsługę. Stąd również narzędzia webowe zapewniające dostęp do danych poprzez standardową przeglądarkę internetową to dzisiaj coraz powszechniejsze składniki systemów SCADA/HMI.
W statystykach sytuacja jest podobna do ocen dotyczących chmury obliczeniowej. Rok po roku, raport po raporcie wzrasta odsetek osób przychylnych tego typu rozwiązaniom. Tym razem blisko 2/3 respondentów uznało, że interfejs webowy i mobile HMI są dzisiaj czymś standardowym, zaś niewiele mniej było zdania, że tak być powinno (rys. 11). "Nowe pokolenie pracowników wymusi zmiany w systemach w tym obsługę z urządzeń przenośnych" – stwierdził jeden z respondentów. Jednocześnie nikt nie był zdania, że jest to przeceniany lub niepotrzebny aspekt w przypadku oprogramowania przemysłowego.

Również podobnie jak w poprzednim rozdziale należy zwrócić uwagę na fakt, że wykorzystanie omawianych rozwiązań nadal warunkują (i słusznie) kwestie zapewniania bezpieczeństwa. Użycie urządzeń mobilnych jest często ograniczane polityką dostępu oraz zabezpieczeniami przed możliwością nieautoryzowanej ingerencji. Aczkolwiek i tutaj zaszły spore zmiany postrzegania tych tematów. Katalizatorem była pandemia, gdy zdalny czy mobilny dostęp okazał się dla firm nie tyle dodatkową, bonusową opcją, ale podstawowym warunkiem utrzymania ciągłości ich funkcjonowania.
Energetyka, wod-kan, przemysł motoryzacyjny i spożywczy
Koniunktura w omawianej branży jest zdecydowanie pozytywna – i takie jej oceny uzyskujemy już od lat. W szczególności w epoce transformacji cyfrowej przemysłu zapotrzebowanie na oprogramowanie oraz projekty wdrożeniowe utrzymuje się na wysokim poziomie. Aż 86% badanych oceniło sytuację rynkową w 2023 roku jako dobrą, pozostali jako bardzo dobrą (rys. 12). Jest to wynik lepszy niż dwa i cztery lata temu. Prognozy są również optymistyczne – ponad połowa ankietowanych uznała, że zmiany idą we właściwą stronę.
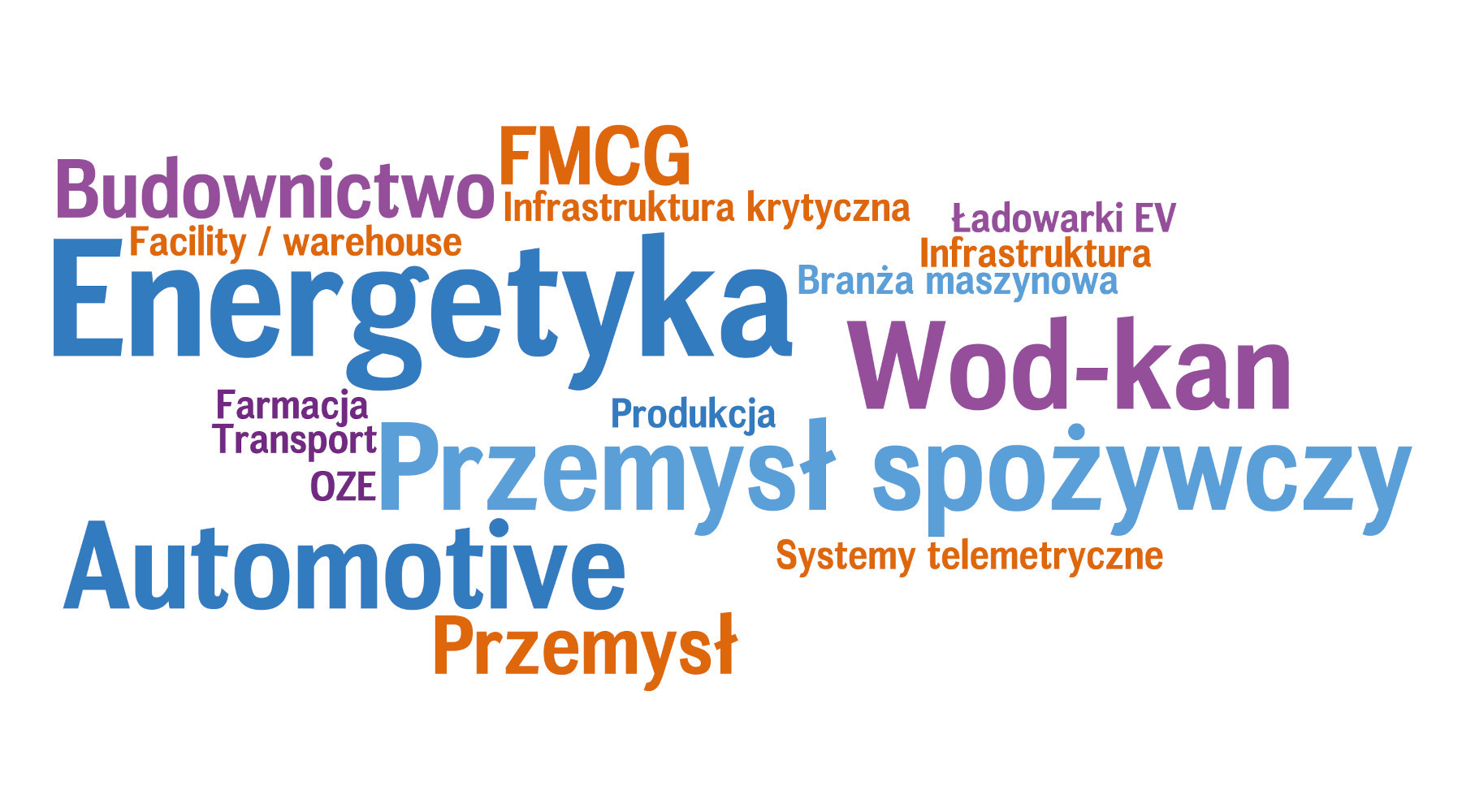
Sektorami rynku, które będą w przyszłości dla krajowych dostawców oprogramowania najważniejsze, są przede wszystkim: energetyka oraz branża spożywcza, motoryzacyjna i wod-kan. Wskazania z nimi związane otrzymały najwięcej głosów (rys. 13) i, co warto zauważyć, o ile dwa pierwsze to powtórka sprzed dwóch lat, o tyle dwa kolejne są nowością. Natomiast nowość ta nie dziwi, jeżeli weźmiemy pod uwagę, że poprzedni raport tworzyliśmy w 2021 roku, a więc w trakcie pandemii.
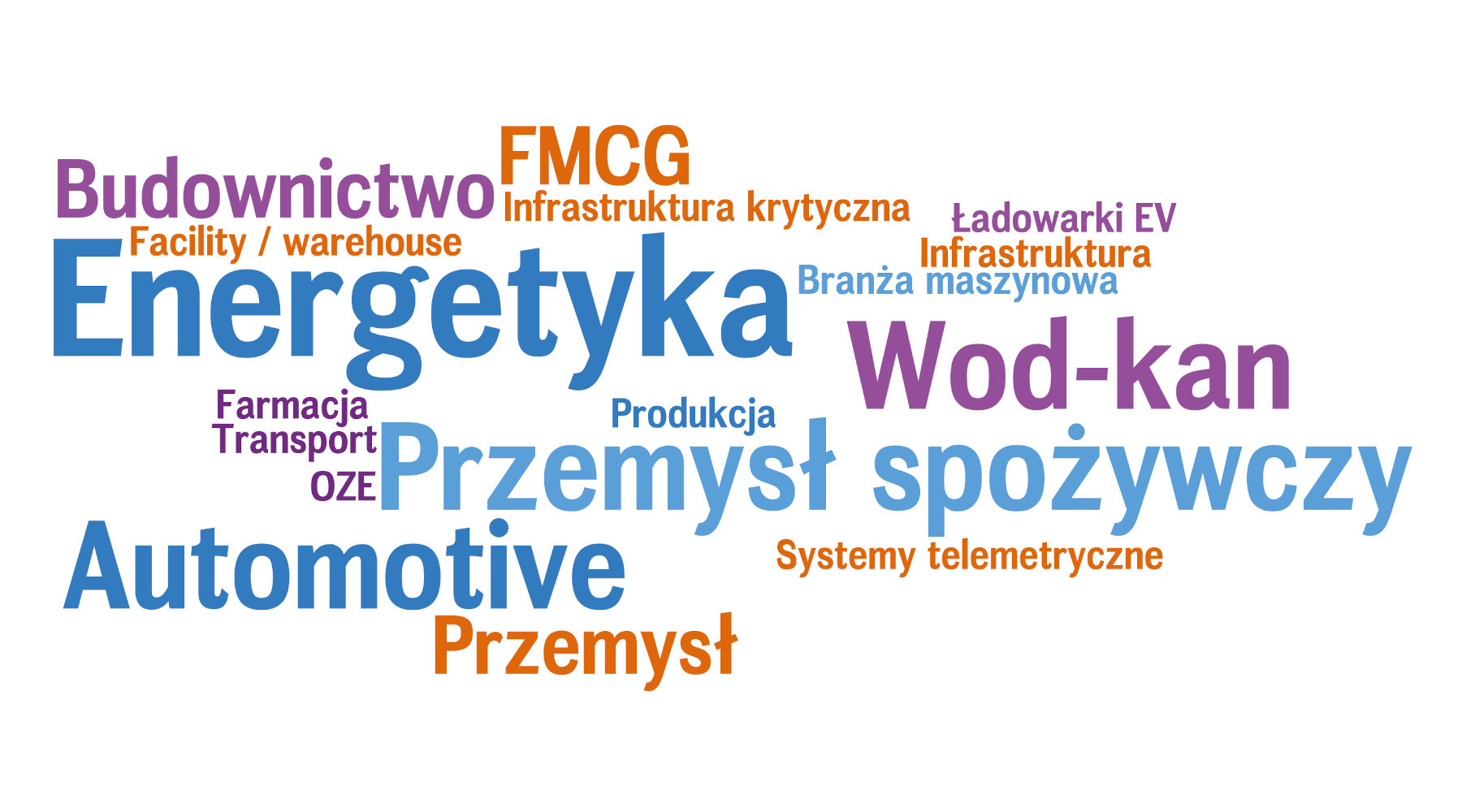
Do kolejnych, rzadziej wskazywanych perspektywicznych obszarów należały w tym roku m.in.: FMCG, budownictwo, ogólnie przemysł i produkcja oraz infrastruktura. Finalnie, można zauważyć, że lista wskazań obejmuje praktycznie wszystkie omówione wcześniej zastosowania oprogramowania, przez co na rynku zostanie utrzymane status quo.
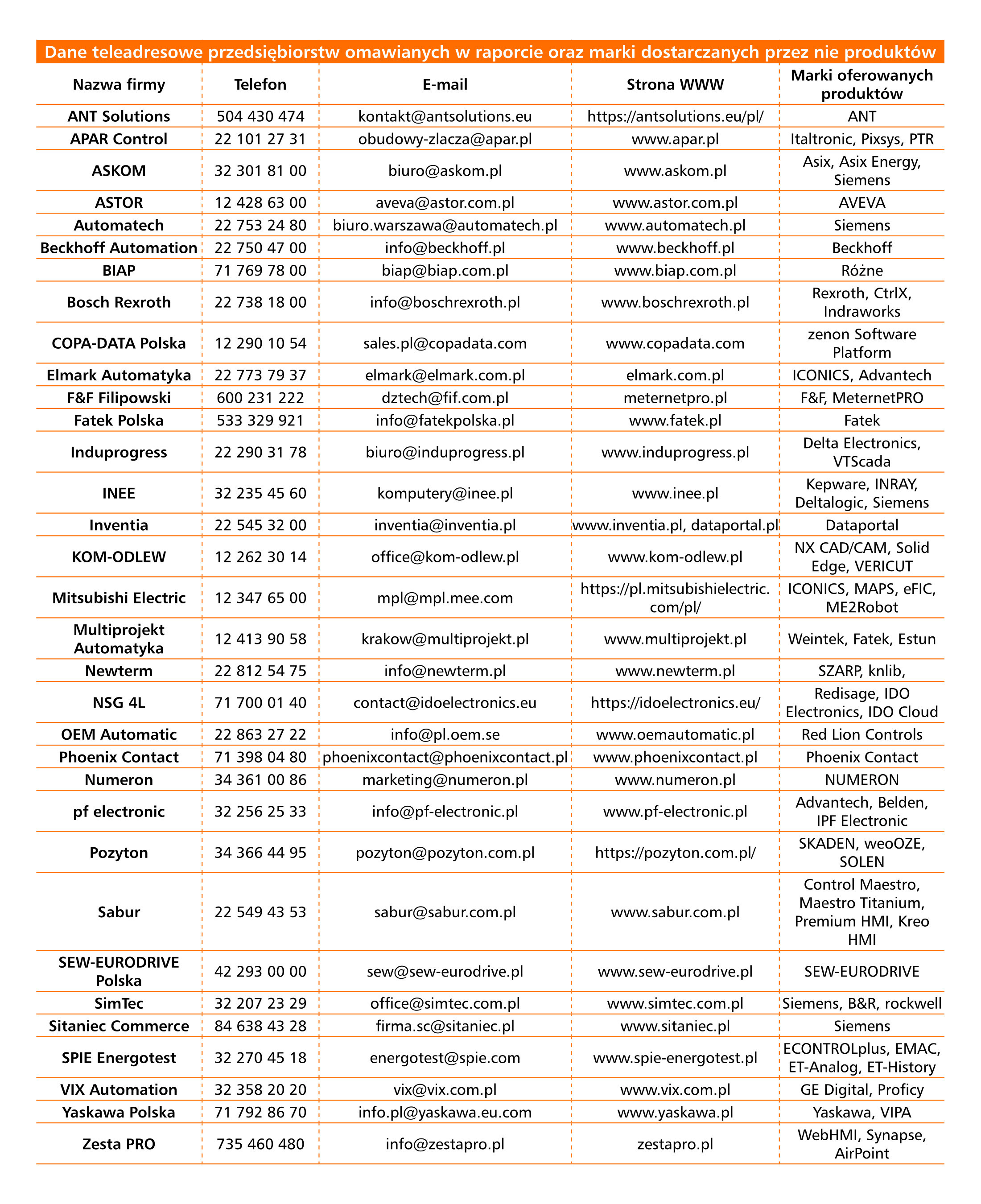
Źródłem wszystkich danych przedstawionych w tabelach oraz na wykresach są wyniki uzyskane w badaniu ankietowym przeprowadzonym w czerwcu 2023 roku wśród firm działających w Polsce w branży związanej z oprogramowaniem przemysłowym.