Roboty przemysłowe i współpracujące
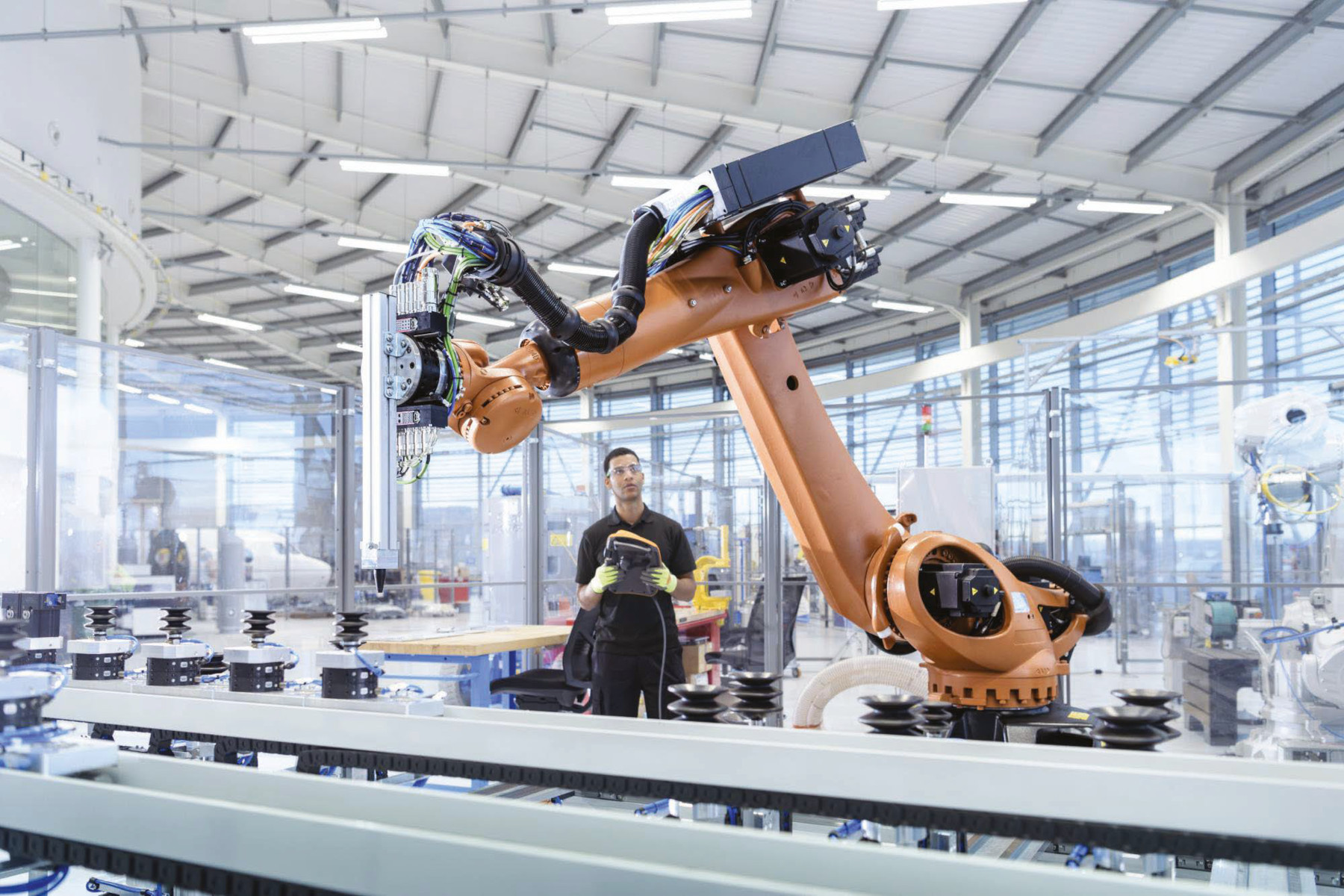
Rynek robotyki spowolnił, na co niewątpliwie wpływ miała pandemia koronawirusa. Ankietowani przez redakcję przedstawiciele firm branżowych na przełomie 2020 i 2021 roku szacowali jego wartość w Polsce na około 240 mln złotych, zaś wielkość – na 2200 jednostek sprzedawanych corocznie. Czy jest to już faza stabilnego rozwoju, czy cisza przed burzą zwiastująca gwałtowną rewolucję sztucznej inteligencji, systemów wizyjnych, cobotów oraz robotów mobilnych? Skłaniamy się raczej ku tej drugiej tezie, bowiem dzisiaj firmy robotyczne oferują coraz bardziej zaawansowane rozwiązania technologiczne, które zmieniają możliwości aplikacyjne i zastosowania robotów w przemyśle.
Robotyka w Polsce
Ankietowani przez nas przedstawiciele branży szacowali wielkość rynku na wymienione wcześniej około 240 mln złotych rocznie oraz, liczbowo, 2200 jednostek robotów. Jest to wyliczenie uśrednione, stworzone na bazie wszystkich odpowiedzi podawanych w badaniu. Na pytanie o to, co wpłynie w przyszłości na wzrost runku, odpowiadano w głównej mierze, że będzie to aktualny rynek pracy oraz stopa zwrotu z inwestycji w roboty.
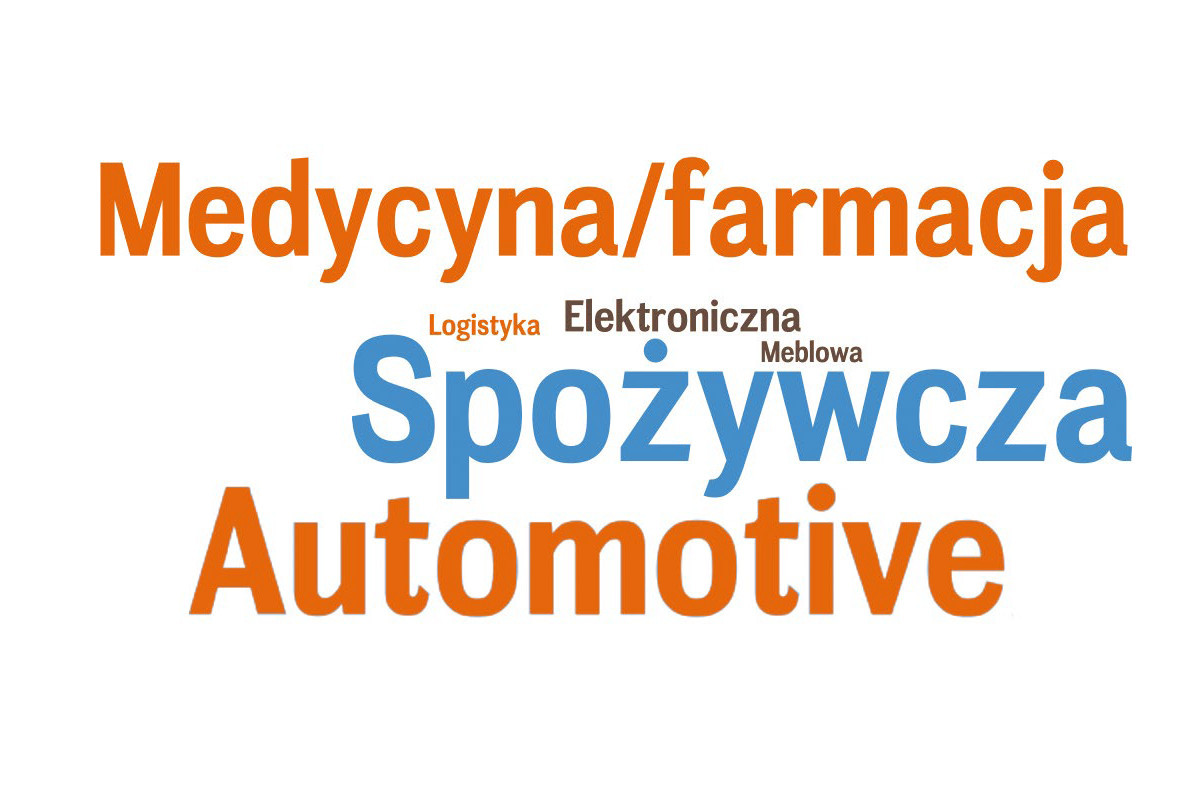
Przypomnijmy, że wartość polskiego rynku robotów szacowana była w raporcie publikowanym w magazynie APA w 2018 roku oraz informatorze IRA z tamtego okresu na 260‒290 mln zł, przy liczbie sprzedanych jednostek na poziomie 1900. Mogłoby to oznaczać, że rynek w czasie ostatnich dwóch lat nieznacznie spadł wartościowo, pomimo przyrostu liczby sprzedanych robotów. Interpretacja taka wydaje się prawdziwa, bo konkurencja na rynku robotów wyraźnie wzrosła, co mogło doprowadzić do spadku marży. Wzrósł także udział w rynku robotów współpracujących (cobotów), których ceny są niższe niż tradycyjnych robotów przemysłowych, co także mogło mieć wpływ na szacowaną przez dostawców wartość całego rynku.
Robotyzacja pakowaniaPakowanie to ostatni etap procesu produkcyjnego. Od jego przebiegu w dużym stopniu zależy efekt końcowy – zarówno jakość produktu, jak i logistyka jego dostaw. Powinno być również realizowane na tyle elastycznie, aby móc nadążać za potrzebami i oczekiwaniami klientów. Aby spełnić te wymagania, producenci prześcigają się, oferując maszyny oraz roboty w różnych wersjach i konfiguracjach. Zagadnienia te zostały omówione w kompendium "Maszyny i roboty pakujące", które znaleźć można na stronie www.automatykab2b.pl w dziale "Temat miesiąca". ![]() |
Korekta trendu wzrostowego na świecie
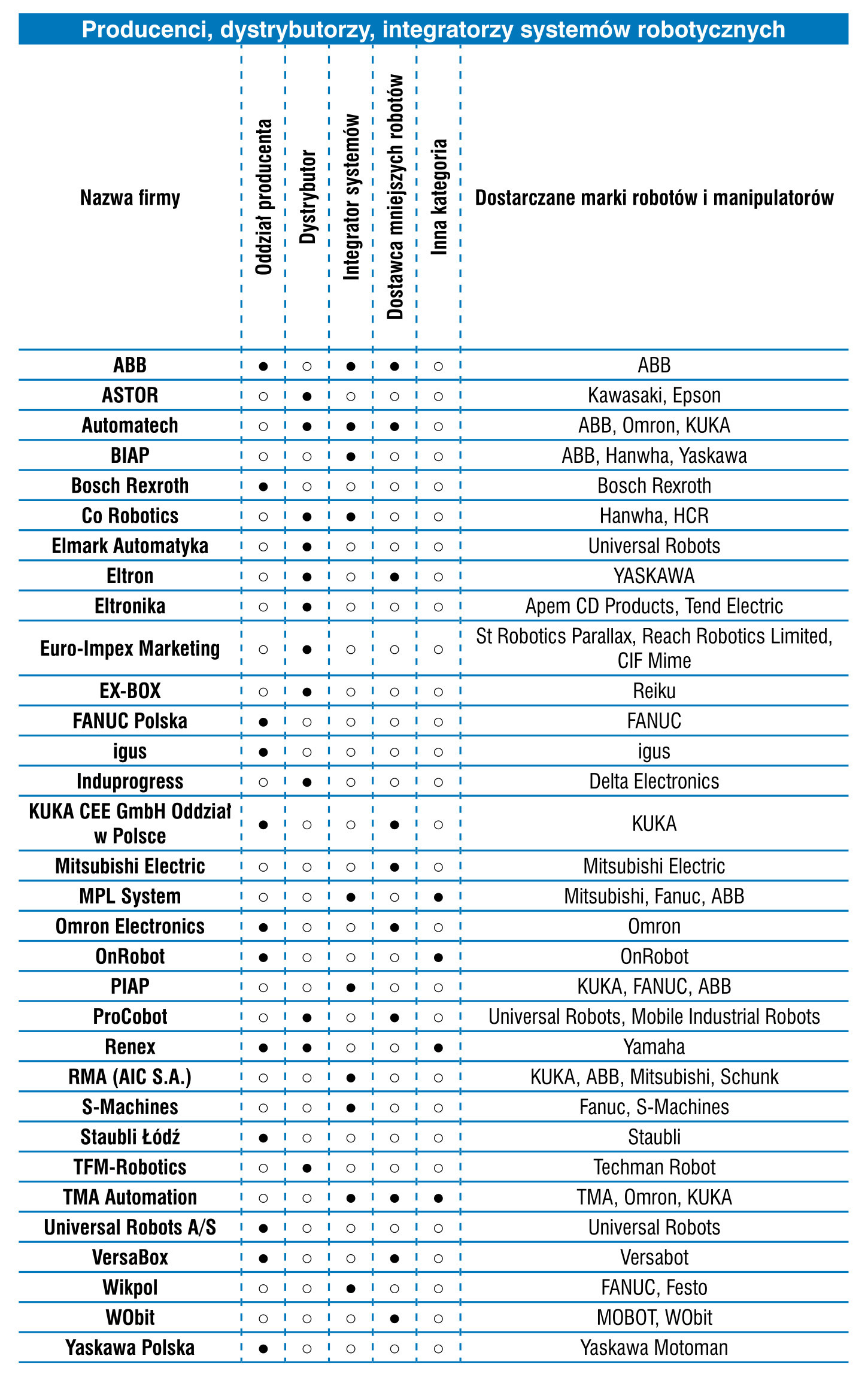
Według danych z raportu Międzynarodowej Federacji Robotyki (IFR) globalna sprzedaż robotów przemysłowych na świecie w 2019 roku spadła o 12% (podczas tworzenia analizy nie dysponowaliśmy jeszcze raportem za 2020 rok). Dotyczyło to między innymi Europy, w której spadek był jednak mniej odczuwalny i wyniósł 5%. Szczęśliwie nie objął też Polski, gdzie sprzedaż rok do roku praktycznie się nie zmieniła i według IFR wyniosła 2642 jednostek. Mimo nie najgorszego popytu na roboty Polska wlecze się w ogonie państw słabo zrobotyzowanych z gęstością robotów wynoszącą na dzień dzisiejszy 46, podczas gdy średnia światowa to już 113 jednostek.
IFR odnotowuje, że w Europie na niższy wynik sprzedaży robotów wpłynął mniejszy o 20% popyt ze strony przemysłu motoryzacyjnego, podczas gdy popyt pozostałej części przemysłu wzrósł o 4%. Rynek motoryzacyjny napędzał robotyzację przez wiele lat. Obecnie znajduje się on w głębokim kryzysie, z którego trudno mu będzie wyjść w krótkiej perspektywie. Do potentatów na rynku europejskim należą Niemcy. Są one także jednym z pięciu głównych rynków robotów na świecie, posiadając według IFR 28% udział w całkowitej liczbie instalacji w Europie. Na drugim miejscu na naszym kontynencie plasują się Włochy z 15% udziałem, trzecia jest Francja z 9%.
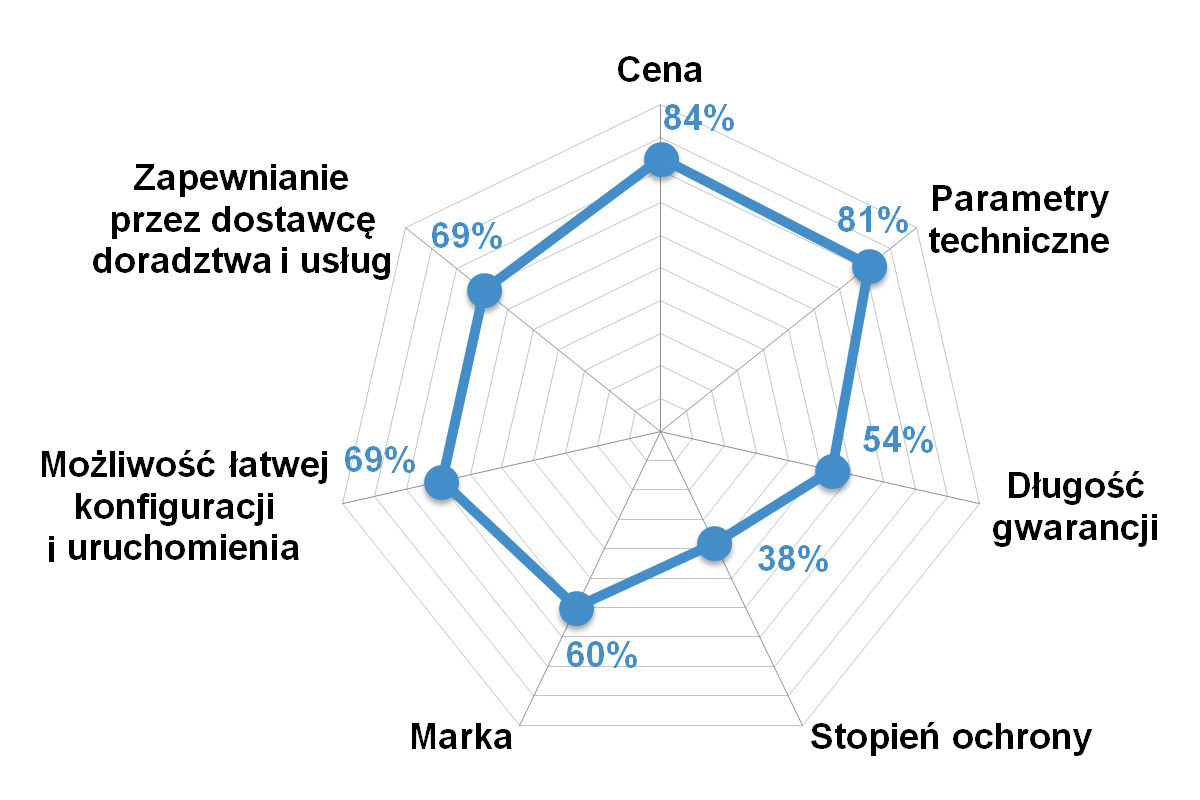
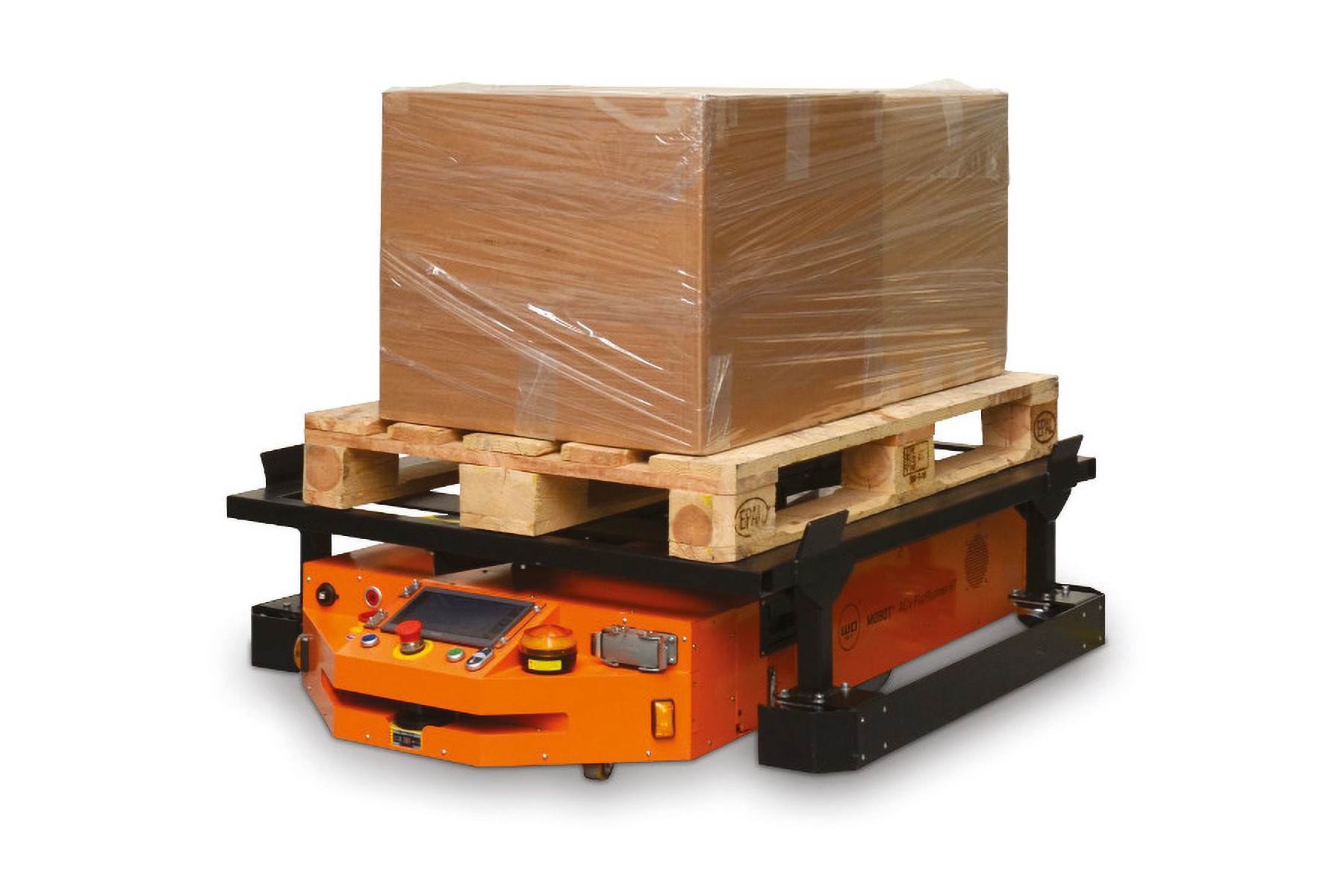
Warto przyjrzeć się też sytuacji w naszym regionie. Z uwagi na silny rozwój przemysłu motoryzacyjnego w Czechach i na Słowacji, kraje te znacznie wyprzedzają Polskę w robotyzacji. Wspomniany kryzys branży automotive odcisnął jednak piętno na rynku w tych krajach. W 2019 w Czechach sprzedaż robotów spadła o 4%. Mimo to, Czechom i tak możemy pozazdrościć parametru gęstości robotyzacji, który wynosi tam 147. Na Słowacji zainstalowano łącznie o 15% mniej jednostek niż w 2018, co pozwoliło finalnie uzyskać gęstość robotów 169 za rok ubiegły. Węgry, podobnie jak Polska, muszą gonić liderów. W 2019 odnotowano o 2% więcej instalacji, co pozwoliło zbliżyć się do światowej średniej i uzyskać wynik niewiele niższy – 106. Największym wzrostem w regionie może poszczycić się Rumunia gdzie odnotowano o 12% więcej instalacji niż w 2018 roku. Rumunia z tym przyrostem zajmuje jednak dopiero 36. pozycję pod względem sprzedaży robotów na świecie, a gęstość robotyzacji pozostaje tam wciąż bardzo mała i wynosi 25.
Na malejącym wartościowo rynku globalnym łokciami rozpychają się dostawcy robotów współpracujących. Według IFR roboty współpracujące (coboty) odgrywać będą coraz większą rolę w robotyzacji zakładów przemysłowych. W 2017 roku, kiedy IFR zaczęła publikować statystyki w tej kategorii urządzeń, coboty miały udział w rynku na poziomie zaledwie 2,8%. Od tego momentu przybyło dostawców robotów współpracujących. Wzbogacił się także zakres ich zastosowań. W efekcie, w raporcie IFR za 2019 rok odnotowano wzrost udziału cobotów do 4,84% wszystkich instalacji na świecie. Jak można sądzić – udział ten będzie rósł, bowiem coboty stosowane są w coraz większej liczbie aplikacji, w tym nie tylko przemysłowych.
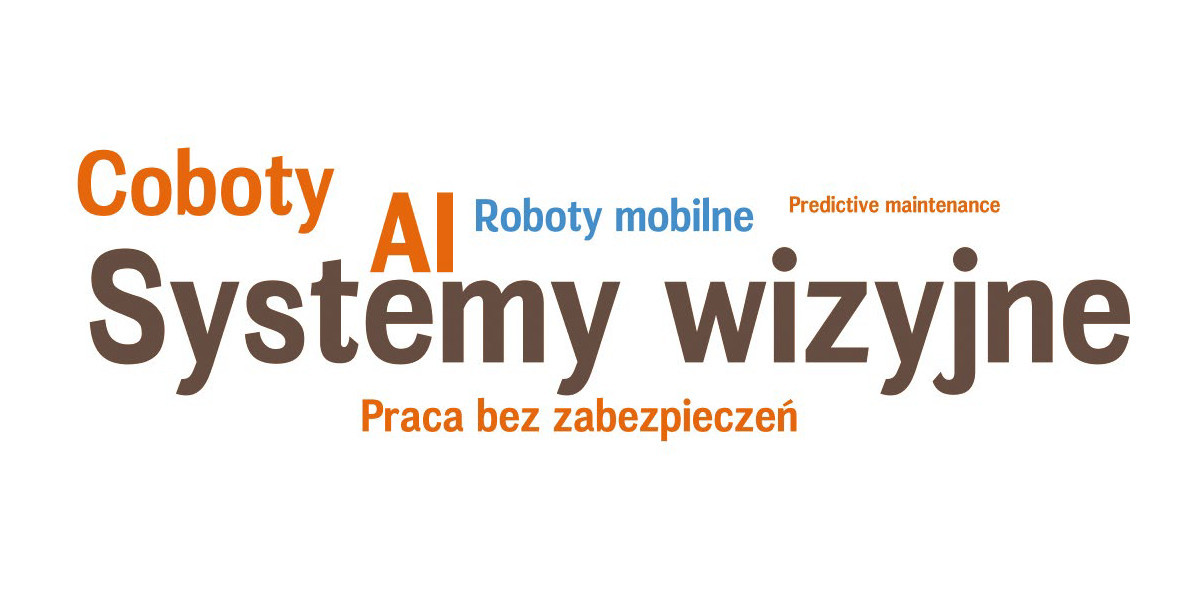
|
Innowacje w robotyce: sztuczna inteligencja i predictive maintenance
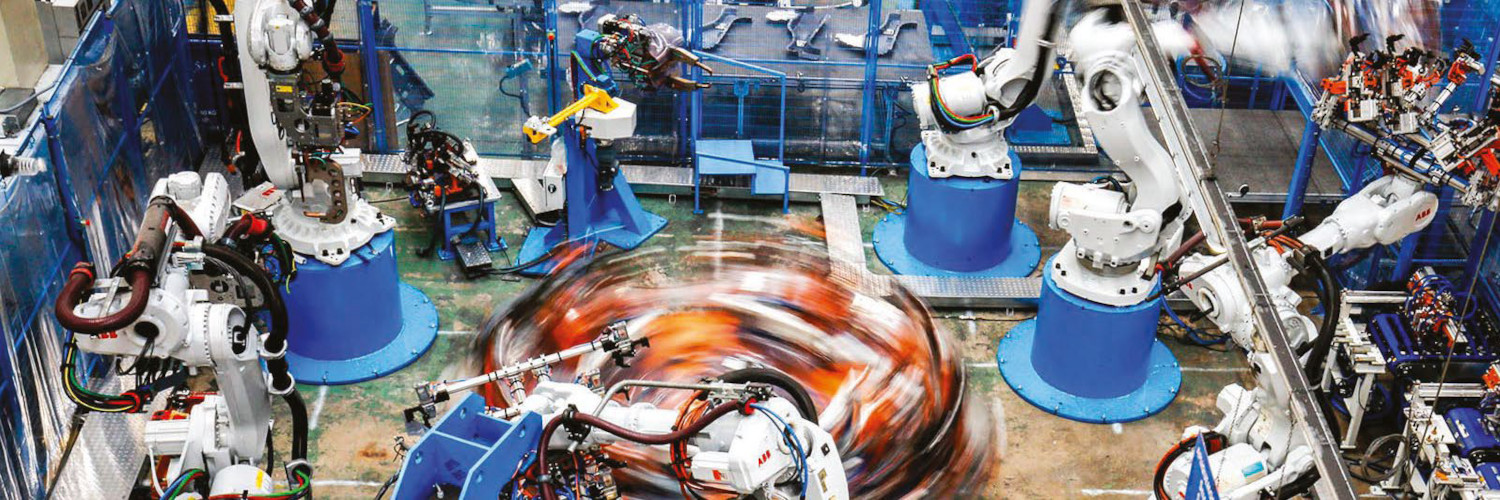
W ostatnich latach firmy zajmujące się robotyką poczyniły znaczne postępy w pracach nad zastosowaniami sztucznej inteligencji. Rozwiązania te skracają czas potrzebny do nauczenia robota, pozwalają też na szersze zastosowania tych urządzeń. Przykładem może być FANUC i jego technologia AI Bin Picking. Algorytm umożliwia pobieranie wybranego rodzaju przedmiotów z nieuporządkowanego zbioru – tzw. kosza. Może ona być wykorzystana w praktyce do uproszczenia procesu adaptacji robotów do pracy w magazynie. Uczenie w tym przypadku polega na doborze obrazów uczących robota, pozwalających odróżnić przedmioty, które ma on wybierać od tych, które ma ignorować.
Inną funkcją wykorzystującą technologię uczenia maszynowego wprowadzoną niedawno przez firmę FANUC jest AI Error Proofing. Ten algorytm zabezpieczenia przed błędami pozwala upewnić się, że proces produkcji przebiega zgodnie z planem. Zazwyczaj problemy, które mogą wystąpić podczas produkcji i skutkować wadami produktu, są znane. Działanie algorytmu polega na wykrywaniu braków już na początku produkcji całej serii i usuwaniu wad produkcyjnych jeszcze przed rozpoczęciem masowej produkcji, co pozwala zaoszczędzić czas i koszty. AI Error Proofing zostało zaprojektowane w taki sposób, by porównywać wzorcowe obrazy z obrazami bieżącej produkcji. Algorytm, po wcześniejszym nauczeniu, jest w stanie przykładowo zweryfikować obecność lub brak przyspawanej nakrętki, rozróżniając obrazy produkowanego elementu z nakrętką i bez niej. AI EP nie jest oczywiście zdolny do wykrywania wszystkich wad, takich jak zadrapania lub wgniecenia, które występują w przypadkowych miejscach produkowanego detalu.
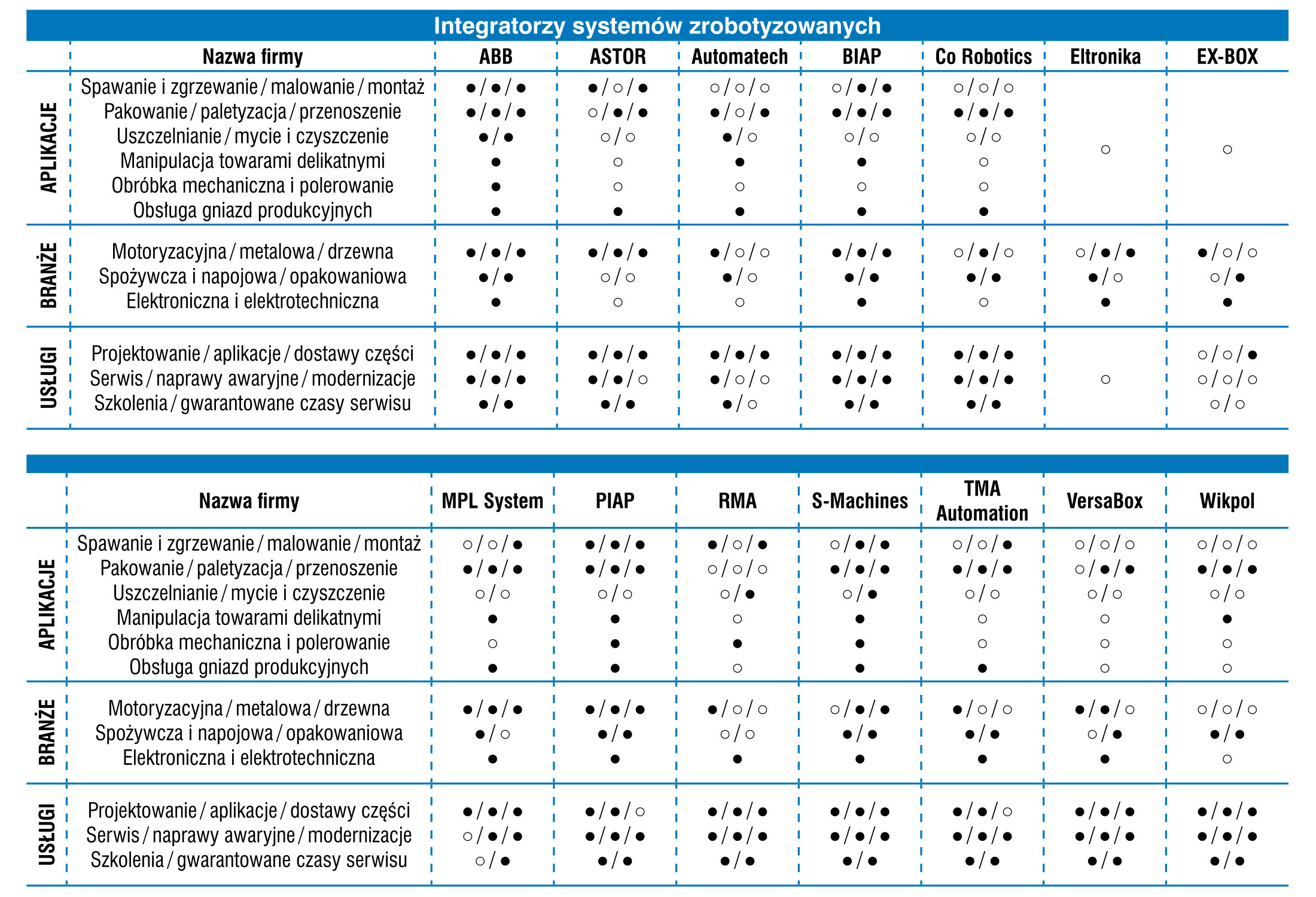
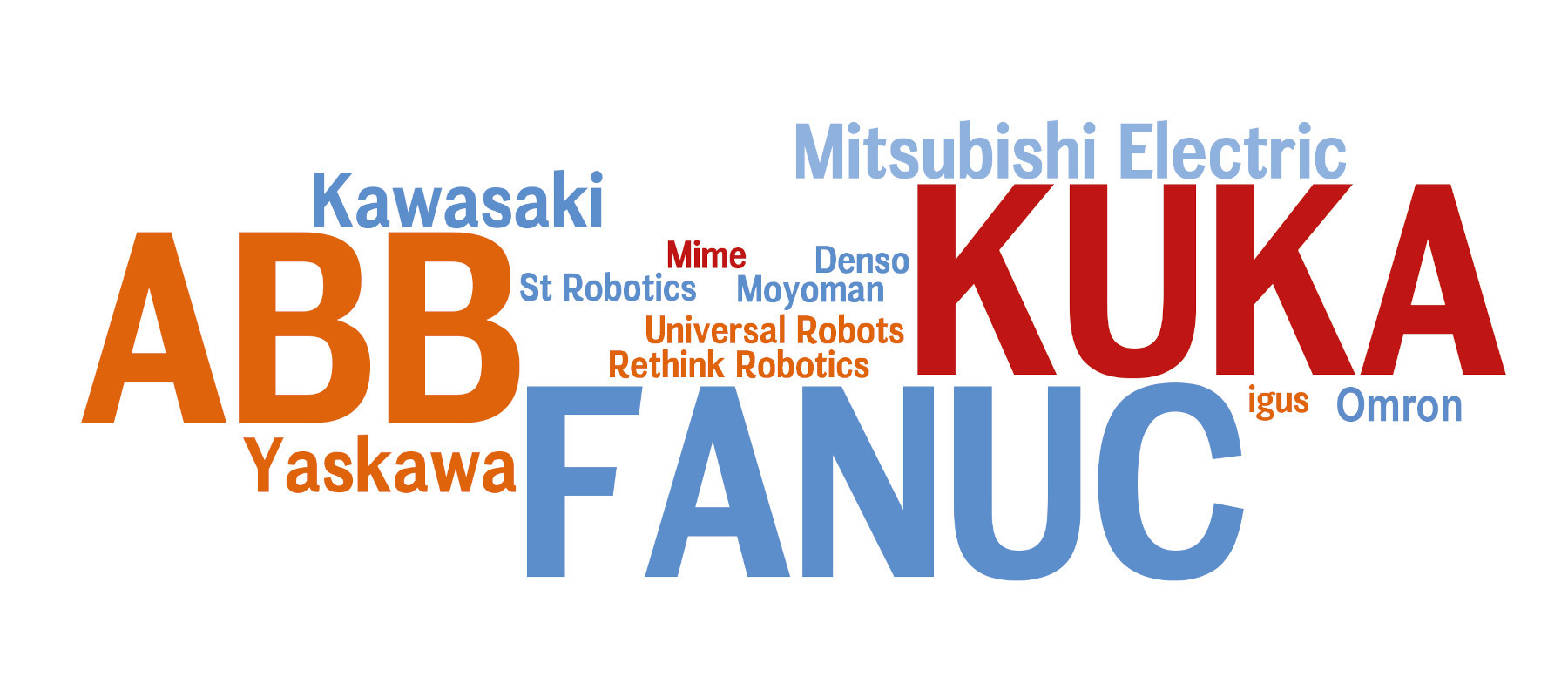
Inny przykład zastosowania to eliminacja nieplanowanych przestojów z zastosowaniem sztucznej inteligencji w obszarze diagnostyki predykcyjnej. Przykładowo rozwiązanie zaproponowane przez firmę Omron polega na autodiagnostyce i pozwala określić, kiedy robot wymaga naprawy lub rutynowego serwisu. Predictive maintenance jest strategią utrzymania ruchu zakładającą optymalne użytkowanie maszyn, w tym przypadku robotów, poprzez przewidywanie możliwości wystąpienia awarii. Predykcyjne utrzymanie ruchu (predictive maintenance) realizowane jest na podstawie bieżących danych z urządzeń i systemu analitycznego. Pozwala ono przewidywać, że może dojść do awarii na podstawie występujących anomalii w zachowaniu się urządzeń. Amerykańskie Biuro Efektywności Energetycznej i Energii Odnawialnej podaje, że dzięki utrzymaniu predykcyjnemu oszczędności wynoszą od 25 do 30 procent. Realizacja predictive maintenance jest trudniejsza w realizacji w porównaniu do tradycyjnej konserwacji, bo wymaga wdrożenia algorytmów autodiagnostycznych robota.
Innowacje w robotyce: Roboty mobilne i coboty
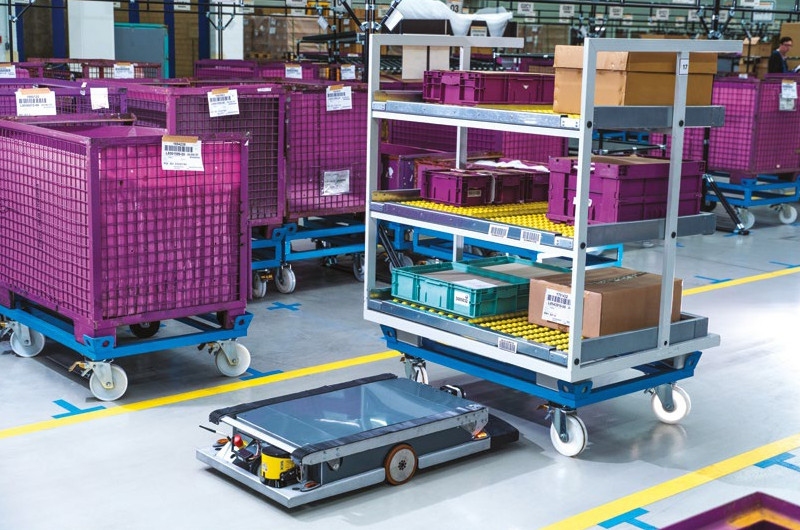
Autonomiczne roboty mobilne (Autonomous Mobile Robots, AMR) rewolucjonizują pracę w fabrykach i magazynach. Zadaniem AMR jest między innymi przemieszczanie gotowych produktów do punktów odbioru i dostarczanie surowców do zautomatyzowanej i zrobotyzowanej produkcji. Mogą one też realizować funkcje czyszczące podłogi. W zakładach zastępują kierowane przez ludzi wózki widłowe, ciągnąc ładunki o masie nawet 1000 kg. W fabryce działającej zgodnie z koncepcją Przemysłu 4.0 spełniają istotną rolę łącząc ze sobą procesy produkcyjne z logistyką
Protoplastą AMR były roboty AGV. Tradycyjnie wymagały one wydzielenia specjalnych tras np. za pomocą pasków magnetycznych umieszczanych na podłodze. Jednocześnie napotykając przeszkodę na zaplanowanej wcześniej trasie, AGV bezradnie zatrzymywały się i nie były w stanie jej ominąć, czekając, aż przejazd będzie możliwy. Konieczne było także pracochłonne zaprogramowanie dokładnej sekwencji sterowania. Autonomiczne roboty mobilne nie potrzebują już specjalnych ograniczeń znajdujących się na podłodze, by poprawnie znajdywać drogę do celu. Wyposażone w czujniki AMR (i nowe wersje AGV) poruszają się bezkolizyjnie po zadanej trasie, bez nadzoru operatora, omijając ludzi i przeszkody, dostosowując swoją ścieżkę do napotkanych warunków. Oprogramowanie robotów mobilnych polega na zdefiniowaniu map, które tworzy sam robot sterowany przez operatora i zapamiętuje zadaną trasę. Podczas uczenia trasy robot sterowany jest manualnie wirtualnym joystickiem np. w aplikacji w smartfonie. Przejeżdżając, robot korzysta z czujników wykrywających ściany oraz znajdujące się na trasie urządzenia w zakładzie. Nauczony trasy robot może być wysłany w każdym momencie przez operatora wykonując powtarzalne czynności np. podjeżdżając pod paletę, zabierając ją i przenosząc w miejsce rozładunku. Na ogół stosuje się grupę autonomicznych robotów, które na zmianę pracują i ładują akumulator.
Roboty mobilne w magazynach i zakładach produkcyjnychIntralogistyka i logistyka zakładowa to obszary zarządzania przedsiębiorstwem obejmujące organizację, realizację i optymalizację wewnętrznego przepływu materiałów oraz produktów w magazynach i na liniach produkcyjnych. Sprawność oraz efektywność w tym zakresie są ważnymi elementami sprzyjającymi budowaniu przez firmy przewagi konkurencyjnej, dlatego warto być zorientowanym w dobrych praktykach oraz najnowszych trendach w transporcie wewnętrznym. W artykule "Intralogistyka i logistyka zakładowa" (publikacja na stronie www.automatykab2b.pl w dziale "Temat miesiąca") przedstawiamy je na przykładach popularnych elementów systemów intralogistycznych – tych wykonawczych, jak przenośniki, wózki widłowe, wózki samojezdne AGV i układnice regałowe, ale też z dziedziny planowania i zarządzania zasobami (oprogramowanie, systemy lokalizacji i identyfikacji). |
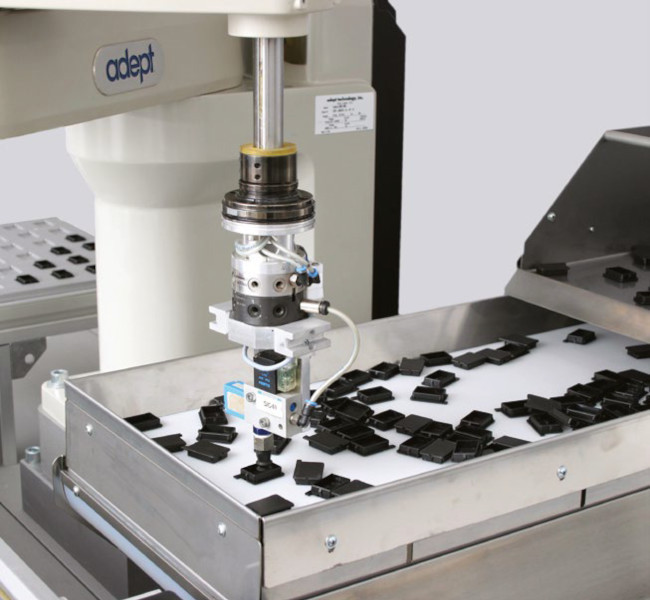
Z kolei siłą cobotów, czyli robotów współpracujących, dzięki której zdobywają coraz większy udział w rynku, jest ich elastyczność aplikacyjna. Urządzenia są lekkie i można je w każdej chwili przestawić i zaprogramować do innych zadań. Zazwyczaj umożliwiają one proste uczenie, w którym operator pokazuje kolejne sekwencje ruchów robota. W praktyce jednak metoda ta służy tylko do początkowego sprawdzenia możliwości cobota w tym zadaniu, bo ostatecznie powstający dzięki tej metodzie skrypt programu i tak jest poprawiany lub całkowicie zmieniany przez programistę. W porównaniu do klasycznych robotów programowanie robotów współpracujących jest dużo prostsze, intuicyjne. Bardzo często inżynierowie w zakładach, w których wdrażane są coboty, decydują się na samodzielne ich oprogramowanie, zazwyczaj z niewielkim wsparciem ze strony integratora.
Wśród licznych zadań wykonywanych przez coboty (aplikacji cobotów) wymienić można m.in. klejenie i dozowanie, spawanie i zgrzewanie, wsparcie w obsłudze maszyn CNC, wkręcanie, montaż, usuwanie materiału, pakowanie, przemieszczanie z miejsca na miejsce, a także wsparcie w kontroli jakości produktów.
|
Co dalej?
O robotach przemysłowych i współpracujących pisaliśmy na łamach APA oraz IRA już wielokrotnie. Wiele z tych publikacji dostępnych jest również na stronie www.automatykaB2B.pl. Osobom zainteresowanym tematyką polecamy odwiedziny serwisu, a także lekturę listopadowego wydania APA (11/2021), gdzie publikujemy nowy raport rynkowy poświęcony polskiemu rynkowi AGV i robotów współpracujących.
Michał Furmański
ABB
Rosnący trend masowej personalizacji produktów oraz rozwój rynku e-commerce przełożył się na złożoność zadań logistycznych. Konsumenci oczekują dostaw tego samego dnia oraz szybkiej obsługi zwrotów. Coraz większe zapotrzebowanie na usługi związane z obsługą klienta i realizacją wymaga ulepszonych możliwości identyfikowania, sortowania oraz przetwarzania pojedynczych paczek o różnorodnych kształtach i rozmiarach. Zapotrzebowanie na dostawy dostosowane do potrzeb zwiększa również złożoność logistyki detalicznej dla handlu, w której duże sieci wymagają od swoich dostawców dostarczania wstępnie ustawionych palet dostosowanych do każdej lokalizacji, które można rozładować bezpośrednio na półki sklepowe bez sortowania. |