Z roczną produkcją na poziomie około 765 milionów litrów, grupa Hassia jest jednym z największych wytwórców wody mineralnej. W samym tylko macierzystym zakładzie w Bad Vilbel, znajduje się sześć stacji napełniania, pracujących równolegle na trzy zmiany. Napędy o wysokiej wydajności transportują butelki na odcinku kilkuset metrów poprzez indywidualne stacje: mycia, napełniania, kapslowania, etykietowania i wysyłki.
Kiedy butelki przejeżdżają z jednego przenośnika taśmowego do drugiego, dotykają nie tylko siebie wzajemnie, ale także prowadnicy. Uderzenia sumując się - poprzez setki butelek - tworzą silne i nieregularne wibracje na napędzie. Dlatego łożyska w przekładni i silniku muszą być dokładnie monitorowane, by w porę przewidzieć ich graniczne zużycie i z odpowiednim wyprzedzeniem przeprowadzić konieczną konserwację.
W celu zapobieganie nieplanowanym przestojom w pracy firma wykorzystuje system ciągłego monitorowania drganiowego Octavis w stacji napełniania butelek. Inwestycja spłaciła się już w fazie pilotażowej, podczas której wykryto i usunięto poważne uszkodzenie napędu. Dzięki temu udało się uniknąć kosztownej awarii.
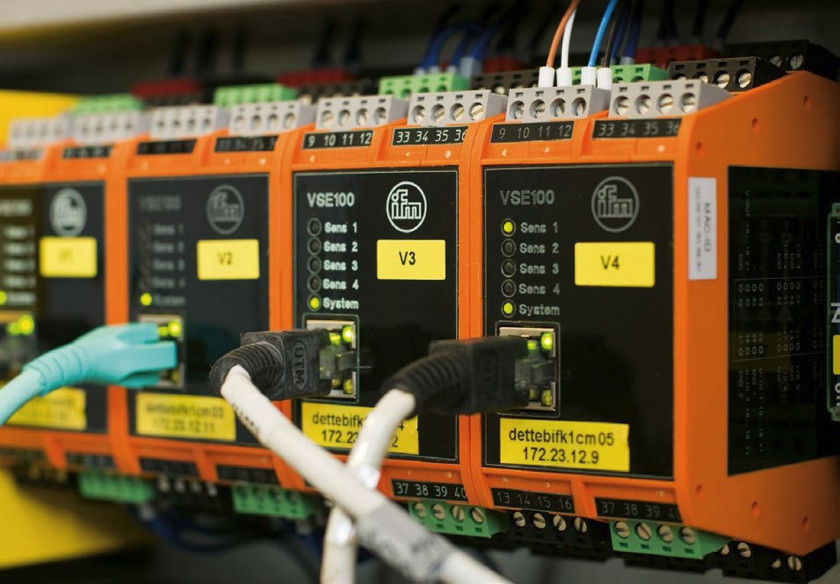
AKUSTYCZNA DETEKCJA DŹWIĘKÓW TO PRZESZŁOŚĆ
Typową metodą monitorowania drgań jest akustyczna detekcja przy pomocy stetoskopu. "W przeszłości kontrolowaliśmy drgania akustycznie wysyłając jednego z pracowników do maszyny, aby słuchał dźwięku jej silnika" - mówi Gerhard Simon, kierownik utrzymania ruchu w Hassia Mineralquellen.
"Było to raczej subiektywne odczucie. Trzy osoby słuchające napędu, silnika czy przekładni słyszą kompletnie różne rzeczy. Podczas trzykrotnego obsłuchiwania nigdy nie ma tych samych warunków działania. Należy obsłuchać maszynę podczas jej pracy, ale nie można tego robić podczas napełniania butelek ze względów mikrobiologicznych. Z kolei na biegu jałowym charakterystyka drgań jest inna. Ponadto są obszary, jak na przykład w maszynie do etykietowania, gdzie wałki napędów obracają się, a silniki i przekładnie są bardzo blisko siebie i po prostu nie można się tam dostać."
Konieczne było więc zastosowanie innego systemu diagnostyki maszyn. W firmie wdrożono system diagnostyki drgań Octavis, z oferty ifm electronic. Składa się on z czujników drgań VSA001 oraz modułu diagnostycznego VSE100. Czujniki w obudowach cylindrycznych są wkręcone bezpośrednio w otworach montażowych silnika lub przekładni.
Mierzą drgania w sposób ciągły na niewirujących częściach maszyn. Umożliwiają diagnostykę także w miejscach, gdzie ze względów bezpieczeństwa nie ma dostępu podczas pracy. Wyposażono w nie maszyny do mycia, usuwania starych etykiet, kapslowania i obszaru napełniania.
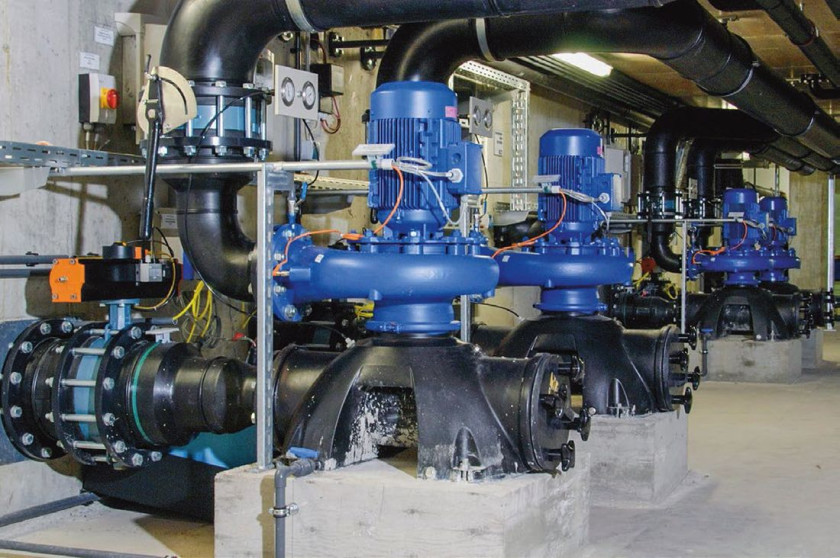
CZUJNIKI DRGAŃ NA NAPĘDACH WYKRYWAJĄ NAWET NAJMNIEJSZE DRGANIA
Dzięki technologii MEMS czujniki VSA nie ulegają nasyceniu oraz są odporne na zakłócenia. Zintegrowany autotest zapewnia dodatkową ochronę. Z kolei moduł diagnostyczny VSE może monitorować nawet 32 obiekty z maksymalnie czterech różnych punktów pomiarowych, w których zainstalowano czujniki drgań VSA.
Alarm wstępny i główny sygnalizowane są poprzez wyjścia przełączające i wyświetlane na kolumnach sygnalizacyjnych. Natomiast moduł diagnostyczny VSE komunikuje się ze sterownikiem maszyny lub systemem sterowania procesu poprzez Ethernet TCP/IP.
Drgania charakterystyczne można przedstawić na wizualizacji na komputerze w sterowni. Ponadto operator może ustawić wartości graniczne (żółte linie dla alarmu wstępnego i czerwone dla głównego).
"Wreszcie mamy elastyczny system, gdzie możemy definiować własne wartości" - twierdzi Gerhard Simon. "Kiedy zostaną przekroczone, interweniujemy i wprowadzamy mechaniczne poprawki, np. smarujemy lub wymieniamy części. Wcześniej było to niemożliwe. Tym samym mamy możliwość zapobiec awarii nawet w najbardziej newralgicznych odcinkach linii produkcyjnej, która mogłaby mieć fatalne konsekwencje dla 3-zmianowej pracy oraz kosztować ogromne pieniądze."
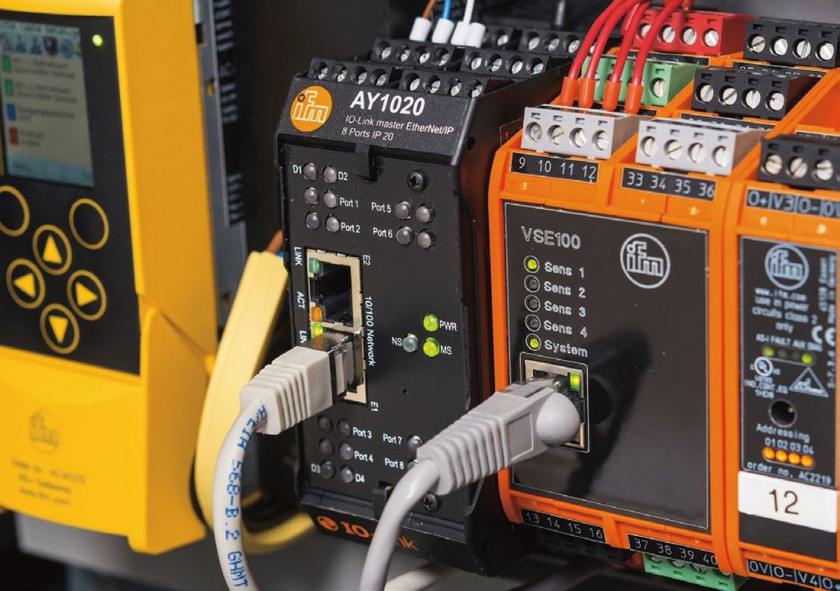
NIEZAWODNA PRODUKCJA MNIEJSZYM KOSZTEM
W planach Hassia Mineralquellen jest monitorowanie całego zakładu za pomocą elektronicznych urządzeń diagnostycznych, a także dokumentacja, co i z jakim rodzajem uszkodzenia zostało wymienione, aby produkcja mogła być optymalizowana. Rejestrowane będą także koszty, aby udowodnić, że inwestycja w system diagnostyczny się opłaciła.
Nie można zapobiec zużyciu elementów maszyn, jednak permanentna diagnostyka drganiowa pozwala na niezawodne wykrycie uszkodzeń na czas. Dzięki niej można zaplanować naprawy i zapobiec kosztownym zatrzymaniom produkcji przy stosunkowo niedużym nakładzie finansowym.
ifm electronic sp. z o.o.
Więcej na www.ifm.com