Chłodzenie powietrzem - kontrola temperatury urządzeń elektrycznych małej mocy
Urządzenia małej mocy są często chłodzone tylko przez konwekcję naturalną. Ciepło z nagrzanego obiektu jest wówczas odprowadzane pod wpływem ruchów powietrza (prądów konwekcyjnych). Powstają one na skutek różnicy gęstości tego gazu, będącej z kolei rezultatem różnicy jego temperatur: w pobliżu gorącej powierzchni oraz w pewnym oddaleniu od niej.
Im ta ostatnia jest większa, tym większa jest siła wyporu powietrza. Prądy konwekcyjne są wtedy silniejsze, a współczynnik przejmowania ciepła - większy. Na przemieszczające się powietrze działa niestety również siła tarcia o zwrocie skierowanym przeciwnie do zwrotu siły wyporu. Blokuje ona przepływ prądów konwekcyjnych, przez co ich prędkość zależy od różnicy tych obu oddziaływań. Nie da się niestety tej szybkości kontrolować - można jedynie próbować usunąć wszelkie przeszkody hamujące ruch powietrza.
Konwekcja swobodna zachodzi przez otwory wentylacyjne w obudowie. Zimne powietrze przenika nimi do jej wnętrza, a po nagrzaniu tą samą drogą ją opuszcza. Najlepiej, gdyby otwory wlotowe znajdowały się na dnie obudowy, a wylotowe na jej wierzchu.
Im będą większe, tym przepływ powietrza będzie swobodniejszy, a chłodzenie skuteczniejsze. Ze względów bezpieczeństwa obsługi oraz sprzętu otwory wentylacyjne są jednak z reguły wąskie, a umieszcza się je z boku lub z tyłu obudowy - na dole wlotowe, a wyżej te wylotowe.
Przykład: chłodzenie urządzeń elektronicznych
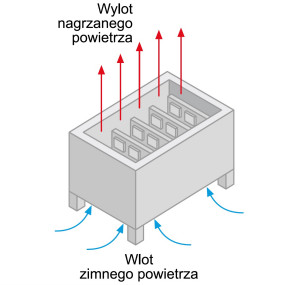
Z wykorzystaniem konwekcji swobodnej chłodzone są przykładowo urządzenia elektroniczne montowane w układzie jak na rysunku 1. Przyjmuje się, że sposób ten sprawdza się w urządzeniach o mocy od kilku do około 30 W, w zależności od wielkości płytki. Aby konwekcja naturalna była skuteczna zachować należy odpowiednie odstępy od góry i od dołu.
Powietrze między płytkami będzie się wówczas swobodnie unosić, w miarę jak jego temperatura będzie rosła pod wpływem ciepła wydzielanego przez komponenty elektroniczne zamontowane na PCB. Od dołu napływać będzie natomiast powietrze chłodne. Prądy konwekcyjne będą przepływać równoległymi korytarzami w odstępach dzielących płytki.
Aby między tymi ostatnimi nie tworzyły się "kieszenie powietrzne" blokujące przepływ tego medium, muszą być one zamontowane pionowo oraz w równych odstępach. Ważna jest również szerokość tych ostatnich. Jeżeli sąsiednie płytki będą zbyt od siebie oddalone, dostępna przestrzeń nie będzie wykorzystywana efektywnie.
Gdy z kolei będą za blisko zbyt duża rezystancja przepływu grozi jego blokadą. Przyjmuje się, że optymalna odległość nie powinna przekraczać kilku centymetrów. Uzupełnieniem konwekcji swobodnej często jest chłodzenie przez promieniowanie.
W konfiguracji jak na rysunku 1 efekt tego mechanizmu odprowadzania ciepła jest niestety marginalny. Poszczególne nagrzewające się komponenty sąsiadują bowiem z innymi, również o podwyższonej temperaturze - ciepło nie zostanie zatem swobodnie wypromieniowane.
Jak dobrać wentylator do niewielkiego urządzenia?
|
Chłodzenie urzadzeń przez konwekcję wymuszoną
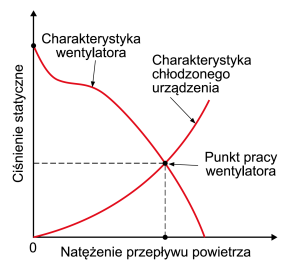
Kiedy naturalny przepływ powietrza nie wystarcza, w obudowie montuje się wentylatory. Dzięki konwekcji wymuszonej współczynnik przejmowania ciepła można zwiększyć wielokrotnie w zależności od liczby tych ostatnich i ich wydajności. Wentylatory wpływają jednak również m.in. na rozmiary, wagę, wytrzymałość oraz cenę urządzenia, które chłodzą. Dlatego ich dobór nie jest łatwym zadaniem. Najpierw wybrać należy typ wentylatora. Jest ich kilka, a każdy ma wady oraz zalety predestynujące je do konkretnych aplikacji.
Na przykład do zalet wentylatorów osiowych zalicza się: prostotę konstrukcji, małe rozmiary, małą wagę, niski koszt oraz duże natężenie przepływu. Niestety sprawdzają się one głównie w systemach o małej rezystancji przepływu, a ponieważ pracują zwykle z dużą prędkością, są głośne.
Wentylatory promieniowe z kolei mogą zapewnić średnie natężenie przepływu w systemach o dużej rezystancji przy stosunkowo małych prędkościach. Niestety są duże i ciężkie, ponadto ich konstrukcja jest bardziej złożona, a cena wyższa niż tych osiowych.
Kolejnym etapem jest zestawienie wydajności wentylatora z wymaganiami aplikacji. W tym celu charakterystykę jego ciśnienia statycznego, którą można znaleźć w danych katalogowych, trzeba odnieść do charakterystyki rezystancji przepływu chłodzonego urządzenia (rys. 2). Wentylator musi "pokonać" tę ostatnią, aby wtłoczyć lub wydmuchać powietrze z obudowy. Punkt jego pracy wyznacza miejsce przecięcia się obu tych wykresów.
Uwagę trzeba również zwrócić na szereg cech specyficznych dla danego modelu. Przykładowo wydajność objętościowa wentylatora o stałej prędkości obrotów będzie taka sama niezależnie od wysokości n.p.m. oraz ciśnienia, natomiast masowe natężenie przepływu jest od tych wielkości uzależnione - im wyżej, tym będzie mniejsze z powodu mniejszej gęstości powietrza.
Wybór wentylatora chłodzącego
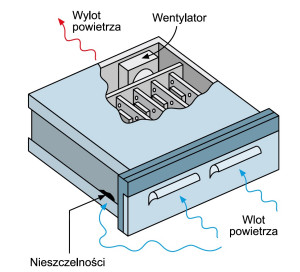
Dlatego, jeżeli na przykład na pewnej wysokości n.p.m. ciśnienie powietrza zmniejszy się o połowę również wentylator przetłoczy wtedy o połowę mniej tego gazu. Skuteczność chłodzenia będzie zatem odpowiednio mniejsza. Alternatywą są wentylatory o regulowanej prędkości obrotowej, które ją automatycznie zwiększają, gdy gęstość powietrza maleje.
Ważne jest również, aby wentylator wyposażony był w filtr, który zapobiegnie przedostaniu się do wnętrza urządzenia zanieczyszczeń z zewnątrz. Należy go tak dobrać, aby zminimalizować spadek ciśnienia powietrza, a równocześnie zapewnić jego skuteczne oczyszczenie. Inaczej pyły lub inne zanieczyszczenia, nawarstwiając się w środku, będą blokować przepływ medium chłodzącego. Taka powłoka na komponencie stanowi ponadto izolację hamującą przepływ wydzielanego się w nim ciepła na zewnątrz.
Uwagi wymaga także miejsce montażu wentylatora. Preferowanym jest wejście urządzenia. Ta lokalizacja ma kilka zalet. Wentylator wtłaczając powietrze do środka, reguluje ciśnienie wewnątrz obudowy, co uniemożliwia przenikanie zanieczyszczeń przez inne otwory.
Ponadto powietrze chłodzące jest zimniejsze, a przez to gęstsze, co zapewnia większe masowe natężenie jego przepływu. Kontakt wentylatora z chłodnym gazem pozytywnie wpływa na jego żywotność oraz niezawodność. Główną wadą tego rozwiązania jest to, że ciepło wydzielane przez wentylator stanowi dodatkowe obciążenie termiczne urządzenia.
Jeżeli wentylator jest umieszczony na wyjściu (rys. 3), tzn. wydmuchuje nagrzane powietrze, ciepło generowane w jego silniku jest od razu uwalniane do atmosfery. Niestety działając w ten sposób, wytwarza on w obudowie urządzenia próżnię, co sprawia, że powietrze z zewnątrz łatwo przenika do środka wszelkimi nieszczelnościami. Utrudnia to skuteczne filtrowanie zanieczyszczeń.
Chłodzenie urządzeń elektrycznych cieczą
Ciecze mają większą przewodność termiczną oraz większy współczynnik przejmowania ciepła niż gazy, dlatego są skuteczniejszym medium chłodzącym niż powietrze. Używane są głównie tam, gdzie rekompensuje to ich istotną wadę, jaką jest możliwość wycieku.
Chłodzenie cieczą możną zrealizować w układzie bezpośrednim albo pośrednim. W tym pierwszym medium chłodzące ma bezpośredni kontakt z nagrzaną powierzchnią. Ciepło z tej ostatniej jest zatem odprowadzane wprost do cieczy. W drugiej metodzie schładzana powierzchnia ma natomiast styczność tylko z elementem pośredniczącym. Dopiero ten jest bezpośrednio omywany przez medium odprowadzające ciepło.
W chłodzeniu bezpośrednim nagrzewający się obiekt jest zwykle całkowicie zanurzony w cieczy. Przepływ ciepła następuje wówczas w wyniku naturalnej lub wymuszonej konwekcji płynu albo w konsekwencji wrzenia, w zależności od temperatury obiektu oraz właściwości medium chłodzącego. W tej metodzie używać można wyłącznie cieczy dielektrycznych, co wyklucza na przykład wodę.
W chłodzeniu pośrednim schładzane obiekty są zwykle montowane na płycie metalowej z materiału charakteryzującego się dużą przewodnością termiczną, na przykład z miedzi lub z aluminium. Do niej przymocowuje się rury, którymi przepływa ciecz chłodząca.
Inny sposób klasyfikacji to chłodzenie w obiegu zamkniętym lub otwartym. W tym drugim nagrzana ciecz jest wydalana z systemu. W obiegu zamkniętym medium chłodzące jest najpierw schładzane (zwykle przez powietrze) w wymienniku ciepła, a następnie wykorzystywane ponownie. Dzięki temu oszczędza się je oraz uzyskuje lepszą kontrolę nad jego temperaturą.
Idealne medium chłodzące
Ciecz chłodząca musi mieć określone właściwości, od których zależy skuteczność chłodzenia oraz łatwość jej transportowania i regulowania przepływu. Powinna ją charakteryzować jak największa przewodność termiczna, od której zależy współczynnik przejmowania ciepła. Przykładowe wartości tego parametru w wypadku mediów popularnych w chłodzeniu bezpośrednim z całkowitym zanurzeniem to:
- fluorochemiczna para: przy konwekcji naturalnej - od 10 do 100 W/m²·°C, wymuszonej - od 10 do 1000 W/m²·°C,
- fluorochemiczna ciecz: przy konwekcji naturalnej - powyżej 100 W/m²·°C, wymuszonej - powyżej 1000 W/m²·°C, wrząca - sięgająca 10 tys. W/m²·°C,
- olej silikonowy: przy swobodnej konwekcji - ponad 100 W/m²·°C.
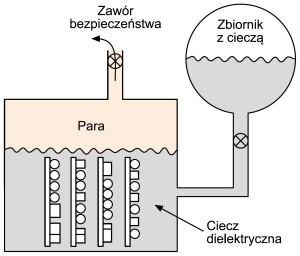
Ciecze o dużym cieple właściwym wymagają mniejszego masowego natężenia przepływu. Mała lepkość powoduje natomiast mniejszy spadek ciśnienia, dzięki czemu można użyć mniejszej pompy. Przy dużym napięciu powierzchniowym maleje prawdopodobieństwo wycieku. Ponadto im większa jest wytrzymałość dielektryczna, tym lepiej, zwłaszcza w chłodzeniu bezpośrednim.
Inne ważne właściwości to: chemiczna inercja oraz chemiczna stabilność. Dzięki tej pierwszej ciecz chłodząca nie będzie reagować z powierzchnią schładzaną, druga cecha zapewni zaś stałość jej właściwości. Ze względu na bezpieczeństwo personelu dobrze, gdy nie jest ona toksyczna. Niska temperatura krzepnięcia oraz wysoka temperatura wrzenia zagwarantują z kolei szeroki zakres temperatur pracy.
Chłodzenie urządzeń przez bezpośrednie zanurzenie - aspekty praktyczne
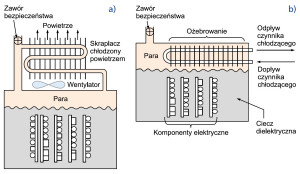
Dużą efektywność chłodzenia bezpośredniego z pełnym zanurzeniem dzięki dużemu współczynnikowi przejmowania ciepła zapewnia zjawisko wrzenia. Metodę tę stosuje się m.in. do obniżania temperatury komponentów elektronicznych dużej mocy.
Najprostszy przykład jej realizacji przedstawiono na rysunku 4. Ciecz chłodząca jest doprowadzana do obudowy urządzenia ciągle, z zewnętrznego zbiornika, natomiast para wydzielana podczas jej wrzenia jest uwalniana do atmosfery.
Ciśnienie wewnątrz regulowane jest zaworem bezpieczeństwa. Zaletą tego układu z otwartym obiegiem jest prostota konstrukcji. Zewnętrzny zbiornik sprawia jednak, że całość jest ciężka i zajmuje dużo miejsca. Należy go również stale uzupełniać, co podwyższa koszty. Ponieważ para wydzielana jest do otoczenia użyć można wyłącznie cieczy bezpiecznych dla ludzi.
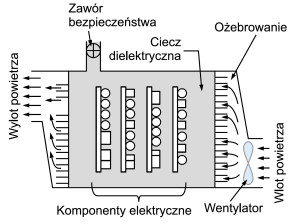
Alternatywę z zamkniętym obiegiem medium chłodzącego przedstawiono na rysunku 5. Para uwalniana w wyniku jego wrzenia ulega kondensacji i jest wykorzystywana ponownie. Częścią układu na rys. 5a jest zewnętrzny skraplacz, w którym para jest schładzana przez powietrze na zewnątrz obudowy. W konstrukcji na rys. 5b skraplacz jest wbudowany w tę ostatnią.
Para schładzana jest w tym wypadku przez czynnik przepływający jego rurami. Skrapla się na nich i skapuje, uzupełniając zapas medium chłodzącego wewnątrz obudowy. Współczynnik przejmowania ciepła (a zatem i wydajność chłodzenia) zależy od zawartości gazów nieskraplających się w cieczy chłodzącej - jest tym większy, im ta ostatnia jest mniejsza. Dlatego ciecz trzeba odgazować, a w procesie napełniania zbiornika unikać jej napowietrzenia.
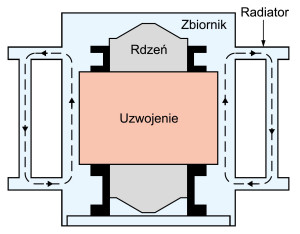
Na rysunku 6 przedstawiono modyfikację układu chłodzenia z pełnym zanurzeniem. Ciepło wydzielane przez komponenty elektroniczne jest w tym wypadku po zaabsorbowaniu przez medium chłodzące wydzielane do otoczenia przez ściany obudowy. Taka konstrukcja nie wymaga ingerencji wewnątrz tej ostatniej, która może być dzięki temu hermetycznie zamknięta.
W wielu aplikacjach jest to zaletą. Zakres jej zastosowania jest niestety ograniczony do chłodzenia komponentów elektronicznych średniej mocy. Aby zwiększyć wydajność odprowadzania ciepła, stosuje się ożebrowane obudowy oraz zewnętrzne wentylatory.
Przykład: chłodzenie transformatorów
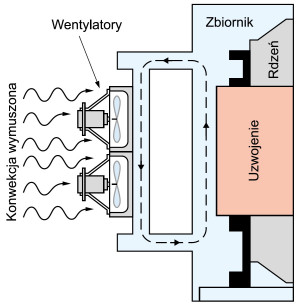
Na rysunku 7 przedstawiono przykład realizacji metody chłodzenia cieczą w transformatorach energetycznych. Jest to najprostszy układ, w którym do odprowadzania ciepła wykorzystuje się zjawisko naturalnej konwekcji gorącego oleju.
Ten ostatni unosi się samoistnie w górę zbiornika, dół którego jest od razu uzupełniany zimnym olejem. Gorące medium tymczasem oddaje ciepło do otoczenia przez przewodzenie lub promieniowanie, a po schłodzeniu spływa na dół. Dzięki temu olej cały czas krąży w zamkniętym obiegu w zbiorniku transformatora.
Aby przyspieszyć oraz zwiększyć skuteczność odprowadzania ciepła gorącego medium do otoczenia, można wykorzystać mechanizm konwekcji wymuszonej, montując na obudowie transformatora wentylatory, jak na rysunku 8. Jeszcze efektywniejsze i szybsze chłodzenie uzyskuje się, wymuszając przepływ oleju przez jego pompowanie.
Monika Jaworowska