Istnieje kilka kluczowych elementów idei Przemysłu 4.0. Jednym z nich jest zastąpienie pojedynczej, niezmiennej linii produkcyjnej sekcjami, które można dynamicznie rekonfigurować, nawet na potrzeby realizacji pojedynczych, indywidualnych zamówień. Można też stosować automatyczne pojazdy samobieżne (AGV – Automated Guided Vehicles), roboty stacjonarne, segmenty przekaźników i zautomatyzowane manipulatory – a wszystkie z nich by przenosić komponenty i podsystemy po terenie fabryki do miejsc, w których są akurat potrzebne. By zrealizować to bardziej inteligentne podejście do działania fabryki, każdy produkt musi być indywidualnie oznaczony. Obsługa, narzędzia i roboty korzystają wtedy z informacji powiązanych z danym znacznikiem, by określić, co ma się zdarzyć z produktem w kolejnych krokach jego podróży przez zakład przemysłowy. Nawet sekcje fabryki, które mogą składać się z kilku narzędzi maszynowych i robotów, mogą być w pewnym sensie wirtualne, tzn. że mogą być dynamicznie przypisywane do innych sekcji, w zależności od potrzeb.
Drugą kwestią jest możliwość interakcji narzędzi maszynowych ze sobą nawzajem. W tym celu korzystają one z wszechobecnej łączności, typowej dla zakładów przemysłowych, wpisujących się w idee Przemysłu 4.0. Systemy używają kombinacji przewodowych i bezprzewodowych technologii sieciowych by wymieniać między sobą informacje w czasie rzeczywistym, a także by przesyłać je z i do odległych serwerów w chmurze. Te zdalne serwery mogą wtedy korzystać ze swojej dużej mocy obliczeniowej, a nawet z algorytmów sztucznej inteligencji, by planować harmonogramy pracy zakładu w sposób bardziej inteligentny.
W końcu, czujniki śledzą stan wszystkiego, co znajduje się na terenie zakładu. Czytniki RFID zbierają informacje z każdego produktu, używając do tego powiązanych z wyrobami znaczników. Czujniki wizyjne i chemiczne monitorują postęp i sprawdzają jakość produktu na każdym kroku, tak by ewentualne poprawki mogły zostać wykonane zanim będzie za późno, a także celem planowania prac konserwacyjnych.
Dla przykładu, wykończenie powierzchni wyrobu zaczyna wykraczać poza specyfikację, oznacza to, że występuje potencjalny problem z maszynami, które powierzchnię przygotowywały, lub że pojawiły się wady w surowcach. Szybkie rozpoznanie tych sytuacji w Przemyśle 4.0 pozwala uniknąć marnotrawstwa i kosztów z nim związanych. W rezultacie powstaje środowisko produkcyjne, w którym wyroby mogą być dostosowywane nawet indywidualnie, w zależności od potrzeb klienta, a także można szybko zmieniać plany produkcyjne, np. jeśli okaże się, że dostępność któregoś z surowców stała się ograniczona, lub jeśli system monitorowania zamówień klientów wykryje zmiany w zachowaniu któregoś klienta.
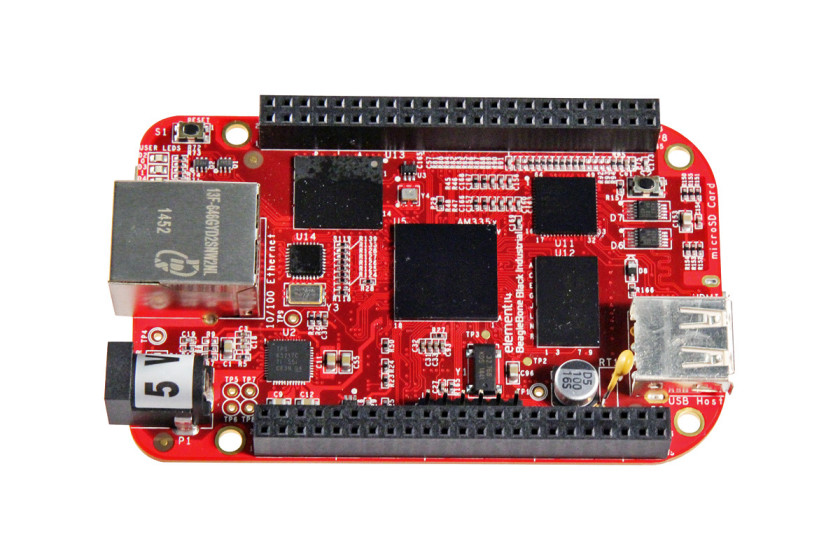
Nowa generacja komputerów jednopłytkowych stała się już dostępna i dobrze sprawdza się w aplikacjach przemysłowych. Urządzenia te zostały zaprojektowane, by czynić zakłady produkcyjne bardziej inteligentnymi i w taki właśnie sposób są coraz częściej stosowane, sprawiając że wdrażane są idee Przemysłu 4.0. I o ile Przemysł 4.0 obejmuje nowoczesne sposoby przebudowy fabryk, producenci wcale nie muszą wszystkiego wymieniać, a komputery jednopłytkowe (SBC – Single Board Computers) można z powodzeniem wykorzystać, by sięgnąć po zalety Przemysłu 4.0 na wiele nowych sposobów.
Połącz komputery przemysłowe z sieciami przemysłowymi
Producenci mogą wykorzystać wcześniej poniesione nakłady inwestycyjne na nowy sprzęt i automatyzację produkcji, by osiągnąć nowe, znaczące korzyści. Wiele z narzędzi maszynowych, z których korzystają już teraz, da się zaadaptować do użycia w środowisku Przemysłu 4.0, o ile tylko wzbogaci się je o dodatkowe funkcje komunikacyjne i obliczeniowe. Można to zrobić nie tylko efektywnie, ale i niedrogim kosztem, sięgając właśnie po komputery jednopłytkowe. W rzeczywistości może się okazać, że nie trzeba nawet zastępować niczym sterowników programowalnych, które dostarczają konkretnych rozkazów dla każdej z podłączonych do nich maszyn.
Wiele protokołów komunikacyjnych, używanych w przemyśle, zostało zaadaptowanych do pracy w ramach Ethernetu przemysłowego, by mieć pewność, że mogą przekazywać komendy z i do pobliskich jednostek obliczeniowych. Jedną z możliwości integracji tych funkcji, zarówno poprzez wdrożenie ich do istniejących instalacji, jak i do nowych maszyn, jest sięgnięcie po montowane na szynie DIN moduły Revolution Pi firmy Kunbus. Są to komputery przemysłowe, oparte o Raspberry Pi i oferowane w ramach licencji open-source. Łączą one moc obliczeniową procesora, wyposażonego w rdzeń Arm Cortex-A oraz łączność ethernetową, a także możliwość przekazywania danych z czujników za pomocą szeregu modułów wejść, wyjść i interfejsów sieci przemysłowych.
Przetwarzanie obrazów i uczenie maszynowe na rzecz kontroli jakości
Firma Industrial Shields, wiodący w Europie producent urządzeń automatyki przemysłowej, korzysta z platformy Raspberry Pi by dostarczać kolejną alternatywę, umożliwiającą wdrażanie bardziej inteligentnych i elastycznych sterowników PLC. Jedną z aplikacji dla tej generacji bardziej wydajnych sterowników PLC jest koordynacja ruchu podsystemów i materiałów na terenie fabryki. Łącze USB stanowi w tym przypadku interfejs do czytnika kodów kreskowych lub skanera RFID, który sczytuje znacznik na podjeżdżającej palecie lub na innym kontenerze. Wyświetlacz podłączony przez gniazdo HDMI może być użyty do wyświetlenia potwierdzenia dla operatora, którego zadaniem jest monitorowanie działania maszyn. Gdy odczytany kod będzie zgodny z pożądanym, sterowniki PLC oparte o Raspberry Pi wykorzystają sieci przemysłowe i łącza wejść/wyjść, by uruchomić silniki, które przesuną dane opakowanie przez serię podajników, aż do pożądanego celu. Alternatywnie, komputer może przekazać pojazdowi AGV trasę, by ten przyjechał po paczkę, odebrał ją i dostarczył na miejsce. Gdy pierwsza sekcja fabryki wykona swoje zadanie na produkcie, sterownik może następnie poprowadzić paczkę do kolejnego celu lub przekazać kontrolę innemu sterownikowi PLC, znajdującemu się bliżej wyrobu.
Kluczowe korzyści płynące z korzystania ze sprzętu takiego jak Raspberry Pi to prosta ścieżka do kolejnej rozbudowy systemu. Wiele z istniejących rozwiązań sterowania przemysłowego bazuje na trzeciej generacji modułu, podczas gdy teraz nowe systemy są budowane w oparciu o najnowszą wersję płytki: Computer Module 4. Zaletą jest zwiększona moc obliczeniowa tego modułu, bazującego obecnie na procesorze z czterema rdzeniami Arm Cortex-A72, a także do 8 GB szybkiej pamięci DRAM i 32 GB nieulotnej pamięci eMMC.
Poziom wydajności, uzyskiwany dzięki płytce Computer Module 4 pozwala działać z intensywnymi aplikacjami uczenia maszynowego i przetwarzania wizji. Dodatkowo, Computer Module 4 pracuje pod kontrolą systemu operacyjnego Linux. System ten obejmuje mnóstwo narzędzi i środowisk deweloperskich (takich jak np. Tensorflow, PyTorch i OpenCV), które zapewniają łatwy dostęp do wysoce wyrafinowanych technik, używanych choćby do analizy komponentów i podsystemów, np. celem sprawdzenia czy spełniane są standardy jakości wyrobów w zakładzie przemysłowym. Subtelne zmiany w kolorze lub budowie powierzchni, które sztuczna inteligencja jest w stanie zidentyfikować, umożliwiają wyzwalanie alertów i przekazywanie ich do centralnych systemów, by podjąć odpowiednie działania naprawcze.
Systemy nadzorujące mogą też korzystać z mocy obliczeniowej ekosystemu firmy Intel. Rodzina Intel NUC obejmuje modele, które pod względem wydajności zaczynają się od energooszczędnych, niedrogich układów, a kończą na potężnych procesorach, takich jak Core i7-8665U – czterordzeniowy układ pracujący z częstotliwością kilku gigaherców. Płytki i systemu NUC świetnie nadają się do systemów nadzorowania. Wielokanałowe interfejsy wideo pozwalają uruchamiać kilka wyświetlaczy jednocześnie. Komputery oparte o płytki NUC mogą więc realizować bardziej złożone algorytmy lokalnie, reagując na powiadomienia zgłaszane przez sterowniki programowalne czy inne komputery jednopłytkowe, znajdujące się na terenie zakładu przemysłowego. Mogą też prezentować graficzne komunikaty dla załogi zakładu, dzięki czemu personel wie, czy pojawiają się nowe problemy i co wymaga uwagi pracowników.
Monitorowanie wyposażenia i analiza informacji
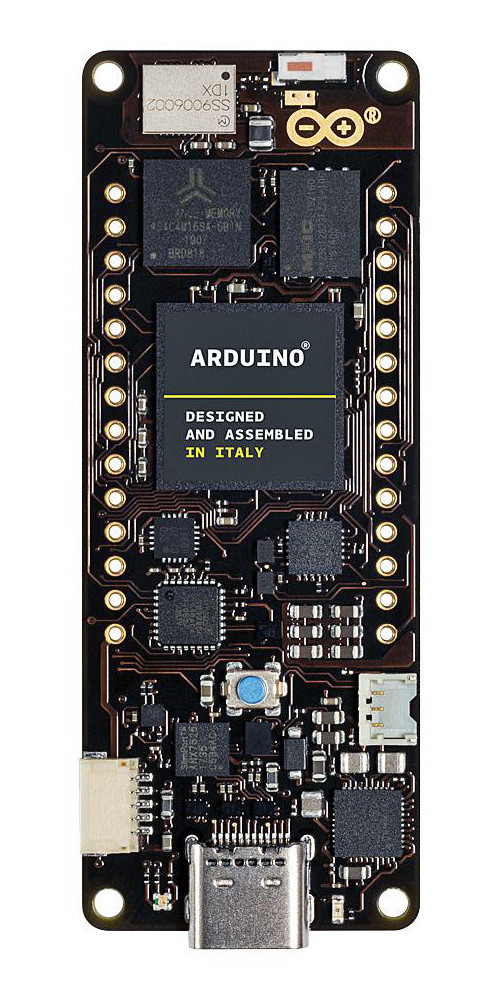
Na drugim końcu skali znajdują się elastyczne procesy, które wymagają responsywnej, łatwej w programowaniu, niskopoziomowej kontroli. Można je zrealizować za pomocą choćby platformy Arduino – czyli połączenia sprzętu mikrokontrolerowego ze zoptymalizowanym środowiskiem do rozwoju oprogramowania, które wspiera błyskawiczne prototypowanie i testowanie algorytmów. Płytka Arduino Pro Portenta to dobry przykład niedrogiego, ale mocnego sprzętu, w którym użyto dwurdzeniowy układ z rdzeniami Arm Cortex-M7F i M4F. Oba z tych rdzeni mogą przetwarzać zarówno liczby całkowite, jak i zmiennoprzecinkowe. Dzięki temu Arduino Pro Portenta dobrze sprawdza się w modelowaniu matematycznym i w sterowaniu za pomocą algorytmów pracujących w zamkniętej pętli.
Aby zwiększyć wydajność, przy zachowaniu niedużych rozmiarów obudowy, powstał komputer DFRobot LattePanda, który łączy w sobie kompatybilny z Arduino mikrokontroler wraz z czterordzeniowym procesorem Intela, taktowanym zegarem 1,8 GHz. Co ciekawe, układ ten pozwala na uruchomienie systemu Windows 10. Stosując takie połączenie, komputer może wykonywać zadania takie jak wspierane przez sztuczną inteligencję monitorowanie wyposażenia lub przetwarzanie obrazów, a także sterowanie obrabiarkami CNC. Dzięki takim cechom DFRobot LattePanda idealnie nadaje się do budowania dostosowanych do potrzeb klienta narzędzi maszynowych.
BeagleBone AI to kolejne rozwiązanie, które pozwala na dodanie obsługi uczenia maszynowego, inteligentnych czujników i przetwarzania obrazów w czasie rzeczywistym. Stosując różnorodne czujniki, pozwala na niedestruktywne testowanie w czasie rzeczywistym oraz monitorowanie wyposażenia. Wbudowany procesor z dwoma rdzeniami Arm Cortex-A15, taktowanymi zegarem 1,5 GHz, współpracuje z dwoma procesorami sygnałowymi TI C66 i z czterema układami Embedded Vision Engine, które obsługują oprogramowanie firmy Texas Instruments, przeznaczone do głębokiego uczenia maszynowego.
Podsumowanie
Droga do Przemysłu 4.0 dla integratorów systemów, twórców narzędzi maszynowych i właścicieli fabryk staje się coraz łatwiejsza, a to za sprawą wsparcia ze strony bogatego i rosnącego wyboru komputerów jednopłytkowych. Te niedrogie, a zarazem wydajne komputery oraz platformy rozwojowe, jakie się z nimi łączą, pozwalają na ulepszanie dotychczas zainstalowanych narzędzi i wbudowywanie ich w sieć, w której znajdą się też nowe roboty i systemy produkcyjne. W rezultacie uzyskujemy znacznie bardziej inteligentne zakłady przemysłowe.
Romain Soreau - Head of Single Board Computing w firmie Farnell
Źródło: Farnell