Nowa norma EN ISO 14119 rozróżnia dwa rodzaje ryglowania osłony: do ochrony procesu oraz do ochrony personelu. Pierwszy typ służy jedynie do zapobiegania zakłóceniom w procesie technologicznym, dlatego w tym wypadku nie ma zdefiniowanych wymagań bezpieczeństwa związanych z funkcją ryglowania osłony, jednakże wszystkie wymagania muszą być spełnione dla funkcji ryglowania.
Maszyna nie musi zatem być zatrzymana w sposób bezpieczny, kiedy urządzenie ryglujące osłonę jest odryglowane, lecz dopiero wtedy gdy drzwi ochronne z urządzeniem ryglującym są otwarte. Urządzenia ryglujące osłonę do ochrony personelu zapobiegają wnikaniu do strefy zagrożenia maszyny do czasu, kiedy zagrożenie nie zostanie wyeliminowane. Maszyna musi być zatrzymana bezpiecznie, gdy urządzenie blokujące jest odryglowane.
WYSOKIE WYMAGANIA
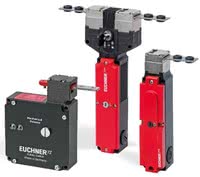
Przegląd rozwiązań firmy Euchner w zakresie elektromechanicznych czujników bezpieczeństwa z ryglowaniem osłony
Normy zawierają różnorodne wymagania dotyczące elementów bezpieczeństwa. Naturalnie podstawowym wymogiem jest niezawodne monitorowanie pozycji urządzenia ryglującego osłonę. Drugim jest zasada ryglowania. Norma EN ISO 14119 definiuje 4 różne zasady ryglowania. Dwie z nich są odpowiednie dla urządzeń ryglujących osłonę do ochrony personelu.
Pierwszą z nich jest "uruchamianie ryglowania przez siłę sprężyny - odblokowanie poprzez dostarczenie energii elektrycznej". Mechaniczna sprężyna porusza mechanizm ryglujący na pozycję zaryglowania, ryglowanie jest zwalniane poprzez przyłożenie napięcia do cewki elektromagnetycznej. Przy braku zasilania elektrycznego drzwi pozostają niezawodnie zaryglowane, jeśli przed brakiem zasilania drzwi były zamknięte.
W takim wypadku niemożliwe jest wejście do maszyny, a gdy konieczne jest niezwłoczne otwarcie osłony, np. aby wyczyścić maszynę, norma EN ISO 14119 przewiduje dodatkowe opcje odblokowujące zamek albo odwołuje się do użycia innych zasad.
ZASADA BISTABILNOŚCI
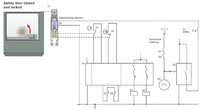
Rys. 1. Ryglowanie osłony w kategorii 3 z wykluczeniem błędów
Kolejną ze znormalizowanych zasad urządzenia ryglującego związanych z ochroną personelu możliwych do zastosowania jest: "zablokowanie przez energię, odblokowanie przez energię". W tego typu urządzeniu zespół ryglujący pozostaje w pozycji, w jakiej był, kiedy energia elektryczna została wyłączona i nie zmienia stanu.
Tak zwane bistabilne wersje tego typu urządzeń ryglujących osłonę nazywają się modelami STP-BI i są dostępne w firmie Euchner od lat. W praktyce maszyna często jest zatrzymana, gdy urządzenie ryglujące osłonę jest otwarte, nawet jeśli ochrona procesu jest właściwa. Jednakże w tym przypadku jeden z wyżej wymienionych warunków nie musi być spełniony.
Dwa następne warunki: "uruchamianie za pomocą energii, zwalnianie przez energię sprężyny" i "uruchamianie za pomocą energii, zwalnianie z wyłączeniem energii", pozwalają otworzyć drzwi i w ten sposób umożliwić czyszczenie maszyny lub wykonanie prac serwisowych, kiedy maszyna jest wyłączona lub w wypadku awarii prądu.
RÓŻNE POZIOMY ZAPEWNIENIA BEZPIECZEŃSTWA (PERFORMANCE LEVEL)
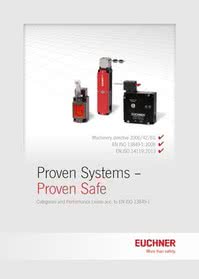
Rys. 2. "Sprawdzone Systemy - Sprawdzone Bezpieczeństwo" (Proven Systems - Proven Safe)
Drzwi bezpieczeństwa mogą być chronione zgodnie z oczekiwanym lub wymaganym poziomem zapewnienia bezpieczeństwa zgodnie z normą EN ISO 13849-1, z zastosowaniem elektromechanicznego urządzenia ryglującego dla ochrony personelu. Nie jest zatem konieczne używanie nowoczesnych urządzeń ze zintegrowaną elektroniką.
Wszystko, co jest konieczne, to właściwa technologia obwodów i prawidłowy dobór elementów bezpieczeństwa. Trzy praktyczne przykłady obrazują, jak można to osiągnąć. W wielu aplikacjach jedno urządzenie ryglujące, którego dwa styki są podłączone do systemu bezpieczeństwa, jest stosowane w celu spełnienia wymagań trzeciej kategorii tak jak jest to pokazane na rysunku 1.
Taki układ spełnia główne wymaganie tej kategorii związane z redundancją obwodu dla części elektrycznej systemu, ponieważ jest ona dwukanałowa. Funkcja diagnostyczna na pierwszy rzut oka również spełnia postawione przed nią wymagania. Co natomiast, jeśli chodzi o aspekty mechaniczne? Co jeśli, na przykład, aktywator urządzenia ryglującego zostanie uszkodzony?
Wtedy nastąpi utrata funkcji bezpieczeństwa przy pierwszym błędzie, nazywanym defektem sprzętu mechanicznego. To z kolei oznacza, że nie wszystkie wymogi kategorii trzeciej mogą być spełnione. Norma EN ISO 13849-1 uwzględnia nie tylko wymagania dla elektrycznego systemu obwodu bezpieczeństwa, ale również dla mechanicznego, hydraulicznego i pneumatycznego.
Mimo to przykład prezentuje właściwe zastosowanie urządzenia ryglującego i może również spełnić wymogi kategorii 3. Kluczem do tego jest tzw. wykluczenie błędów (fault exclusion), co znaczy, że określone błędy nie mogą wystąpić. Wykluczenia są dopuszczalne w normie EN ISO 13849-1. Część 2 tej normy zawiera długą listę dotyczącą rozmaitych koncepcji.
Dodatkowo dla mogących wystąpić błędów możliwe jest określenie, czy związane z nimi wykluczenie błędów jest dopuszczalne. W celu przeprowadzenia wykluczenia błędów podzespołów mechanicznych konieczne jest zapobiegnięcie wystąpieniu tych błędów. Przykładem jest zabezpieczenie elementu mechanicznego ryglowania przed siłami zdolnymi wywołać taką awarię i mającymi wpływ na jego poprawne działanie. Jeśli można to zapewnić, to wykluczenie błędu jest uzasadnione i zgodnie z normą dopuszczalne.
LISTA WYKLUCZEŃ BŁĘDÓW
Euchner od długiego czasu udostępnia w formie broszury znakomity przewodnik po zagadnieniu wykluczenia błędów: "Proven Systems - Proven Safe" (rys. 2). Broszura ta zawiera zestawienie wszystkich błędów, które mogą wystąpić w urządzeniach blokujących lub w urządzeniach ryglujących osłony. Ponadto przewodnik przedstawia informacje dot. oceny wykluczenia błędów zawarte w normach.
Norma EN ISO 13849-2 nie zezwala na użycie wykluczenia błędów dla usterek urządzeń mechanicznych na poziomie zapewnienia bezpieczeństwa PLe dla elektromechanicznych urządzeń blokujących. Norma ta nie jest jednak adresowana do urządzeń ryglujących osłony. Zostało to uregulowane w nowej normie EN ISO 14119.
W przypadku urządzeń ryglujących osłony wykluczenie błędów dla mechanizmu ryglującego tego urządzenia jest możliwe w Ple zależnie od oceny ryzyka. Jest to jednak możliwe tylko w odniesieniu do mechanizmu ryglującego, czyli rygla, który absorbuje rzeczywistą siłę mechaniczną. Nie odnosi się to do funkcji blokującej osłony w każdym urządzeniu ryglującym osłonę. Powyższy obwód, w którym zawarte są wykluczenia błędów nie może osiągnąć "PL e", ale może osiągnąć "PL d".
KATEGORIA 3 BEZ WYKLUCZENIA BŁĘDÓW
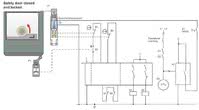
Rys. 3. Ryglowanie osłony w kategorii 3 z dodatkowym czujnikiem (bez wykluczenia błędów)
Jeśli nie ma możliwości zastosowania lub nie może być zastosowane wykluczenie błędów, konieczne jest zastosowanie dodatkowego czujnika w drugim kanale. Jego zadaniem jest wydanie co najmniej jednego sygnału więcej do wyłączenia maszyny w przypadku mechanicznego defektu w urządzeniu ryglującym osłonę.
W przypadku takiego urządzenia pojawia się pytanie, jaki typ czujnika musi być użyty dla drugiego kanału. Ostatecznie na to pytanie można odpowiedzieć tylko po analizie ryzyka. Jednakże, jednorazowe otwarcie drzwi bezpieczeństwa przy pracującej maszynie jest akceptowalne w wielu przypadkach.
Innymi słowy, jeśli urządzenie ryglujące osłonę nie funkcjonuje z powodu awarii mechanicznej, co najmniej jeden sygnał wyłączający maszynę musi być wydany, kiedy drzwi ochronne zostaną otwarte. Ta funkcja może być zrealizowana za pomocą prostego czujnika, np. przełącznik pozycji (position switch) firmy Euchner, który nie ma funkcji ryglowania lub funkcji bezpieczeństwa.
Przykład pokazany jest na rysunku 3. Dodatkowy czujnik P1 jest połączony szeregowo z jednym z dwóch styków, które monitorują pozycję urządzenia ryglującego. W rezultacie tylko jeden z kanałów zostanie wyłączony, jeśli urządzenie ryglujące jest uszkodzone - błąd jest wykrywany przez logiczną jednostkę bezpieczeństwa K1 i maszyna nie uruchomi się po tym, jak drzwi ochronne zostają otwarte.
Informacje dotyczące wyliczenia poziomu zapewnienia bezpieczeństwa PL: w tym przykładzie przedstawiony schemat blokowy użyty do określenia prawdopodobieństwa awarii jest identyczny ze schematem blokowym z wykluczeniem błędów pokazanym na rysunku 1. Dodatkowy czujnik nie jest częścią funkcji bezpieczeństwa, zatem nie wpływa na prawdopodobieństwo awarii. Czujnik jest potrzebny tylko do uzyskania odpowiedniego poziomu pokrycia diagnostycznego (diagnostic coverage).
URZĄDZENIE BLOKUJĄCE W KATEGORII 4
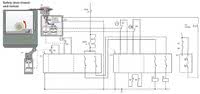
Rys. 4. Ryglowanie osłony w kategorii 4 z dodatkową bezpieczną jednostką logiczną
Wadą wyżej opisanego układu jest brak możliwości wykrycia awarii czujnika P1. Dlatego obwód osiągnie maksymalnie kategorię 3, a nie 4. Jeśli musi być wykryta awaria czujnika P1, obwód będzie zdecydowanie bardziej skomplikowany. Schemat takiego rozwiązania jest pokazany na rysunku 4. W takim przypadku będzie potrzebna druga logiczna jednostka bezpieczeństwa i kolejny styk w urządzeniu ryglującym w celu wykrycia usterki w czujniku P1.
Jednostka logiczna bezpieczeństwa K1 zapewnia wykonanie tej funkcji w tym przykładzie. Logiczna jednostka bezpieczeństwa K2 monitoruje położenie urządzenia ryglującego osłonę, używając dwóch kanałów. Jako że ten układ jest bardzo skomplikowany, ten sam rezultat o wiele łatwiej uzyskać, stosując bezpieczny sterownik, ponieważ i czujnik (P1), i urządzenie ryglujące osłonę można bezpośrednio połączyć z układem sterowania.
RYGLOWANIE OSŁON W CELU OCHRONY PERSONELU
O normach EN ISO 14119 i EN ISO 13849-1 już wspomniano w powyższych przykładach. Norma EN ISO 13855 jest kolejną odnoszącą się do urządzeń blokujących i do urządzeń ryglujących osłonę. EN ISO 14119 określa, kiedy do ochrony personelu konieczne jest użycie urządzenia ryglującego osłonę a kiedy wystarczającym będzie zastosowanie jedynie urządzenia blokującego. Wyboru dokonuje się za pomocą prostego schematu blokowego (rys. 5).
MONITOROWANIE POZYCJI ZARYGLOWANIA
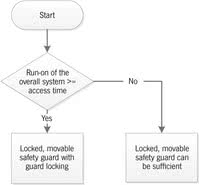
Rys. 5. Ryglowanie osłony przeznaczonej dla ochrony personelu
Jak to zostało pokazane wcześniej, pozycja urządzenia ryglującego musi być monitorowana w urządzeniach ryglujących osłonę do ochrony personelu. Oznacza to, że pozycja sworznia blokującego jest monitorowana. Jak również zostało wspomniane, każde urządzenie ryglujące ma również funkcję blokowania (bez ryglowania).
Podstawą do tego są dwie kompletnie różne funkcje bezpieczeństwa, które są zrealizowane w tym samym komponencie. Podstawowa funkcja, która jest oczywista, to taka, że maszyna jest wyłączana, kiedy urządzenie ryglujące jest otwarte. Inną funkcją jest funkcja związaną z blokowaniem i jest stosowana do zapobiegania nieoczekiwanemu uruchomieniu maszyny.
Tak długo, jak drzwi ochronne pozostają otwarte, maszyna musi być niezdolna do uruchomienia. Tzw. ochrona przeciwko przypadkowemu zamknięciu jest w większości tego typu urządzeń ryglujących, choć nie we wszystkich. Ta mechaniczna funkcja zapewnia, że urządzenie ryglujące osłonę może ją zaryglować, tylko jeśli drzwi są aktualnie zamknięte.
To zapewnia, że drzwi są zamknięte i zaryglowane, nawet jeśli urządzenie ryglujące zostało aktywowane w niewłaściwym czasie. Z drugiej strony ta funkcja zapewnia również, że funkcja blokowania jest aktywna, ilekroć urządzenie ryglujące jest aktywne. Z tego powodu jest wystarczające, jeśli styki do monitorowania zaryglowania są zintegrowane w obwodzie bezpieczeństwa.
Pozycja ryglowania jest więc w rzeczywistości automatycznie kontrolowana. Tylko urządzenie ryglujące z taką funkcją jest odpowiednie do zastosowania jako system blokujący bez konieczności podjęcia dodatkowego działania. Elektromechaniczne urządzenia ryglujące osłonę są wciąż unowocześniane i oferują wiele zalet. Jednorazowy wysiłek wymagany do prawidłowego zintegrowania i oceny tych podzespołów bezpieczeństwa na pewno jest większy niż wymagany przy rozwiązaniach elektronicznych. Jednak niezawodność sprzętu mechanicznego i jego efektywność mówią same za siebie.
Zainteresowanych zapraszamy do odwiedzenia naszej strony internetowej lub kontaktu z firmą Eltron.
Karol Węgiełek
Product Manager ds. produktów dla bezpieczeństwa maszynowego
Eltron
www.eltron.pl