W zasadzie w każdej gałęzi przemysłu można wymienić wiele zastosowań zautomatyzowanych systemów dozowania. Na przykład w produkcji tworzyw sztucznych używa się ich do odmierzania dodatków modyfikujących ich właściwości, m.in. barwników.
W przemyśle spożywczym z kolei są częścią mieszalników, w których dozują składniki i maszyn pakujących, podobnie jak w produkcji kosmetyków i przemyśle farmaceutycznym. Poza tym używa się ich w zadaniach wymagających większej dokładności, jak dekorowanie ciastek.
W innych gałęziach przemysłu także nie brakuje zastosowań, w których systemy dozowania odmierzają precyzyjnie określone ilości materiałów, które, uzupełnione o systemy wizyjne i roboty, umieszczają w wyznaczonym miejscu z małą tolerancją położenia. Przykładem jest branża elektroniczna, a w niej m.in. produkcja paneli fotowoltaicznych, płytek drukowanych i akumulatorów.
Jeżeli chodzi o ostatnie, dozowniki używane są do: nanoszenia klejów mocujących anodę, separator oraz katodę, uszczelnień oraz napełniania akumulatorów elektrolitem. Poza przemysłem z systemów dozowania korzysta się w branży wodno-kanalizacyjnej w oczyszczalniach ścieków oraz na basenach, gdzie dawkują środki chemiczne, które uzdatniają wodę.
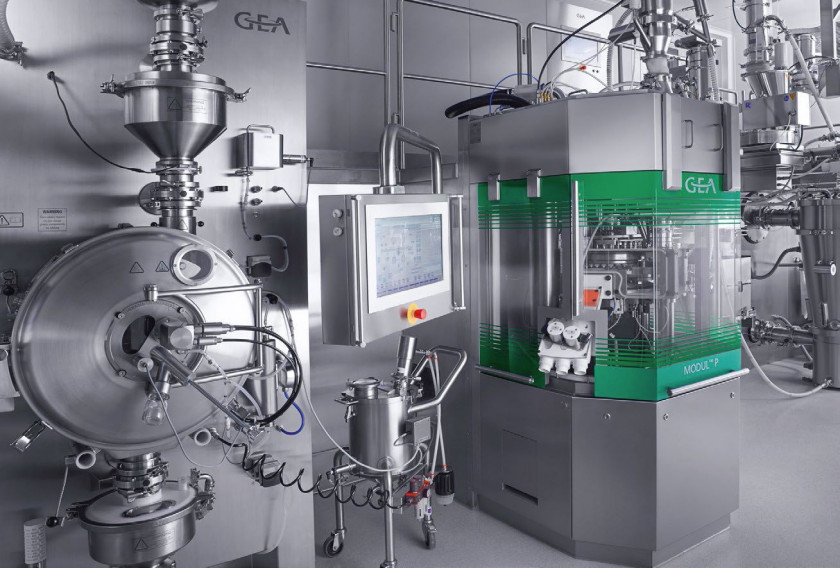
Systemy dozowania
W typowym systemie dozującym można wyróżnić kilka komponentów. Są to: zbiornik z substancją, która ma być dawkowana, pompa z głowicą dozującą, system sterowania i podzespoły pomocnicze, m.in. rurociągi, zawory, czujniki.
Pierwszy zwykle wykonywany jest z tworzyw sztucznych odpornych na działanie środków chemicznych, na przykład poliuretanów albo stali nierdzewnej. Wybierając zbiornik, należy wiedzieć, czy będzie się znajdował wewnątrz budynku, czy na zewnątrz, w związku z czym powinien być umieszczony w osłonie wykonanej z materiału odpornego na działanie promieni słonecznych i różne warunki pogodowe.
Ważne aspekty eksploatacyjne to poza tym: pojemność, którą należy dobrać pod kątem zapotrzebowania na dozowaną substancję oraz łatwość dostępu do wnętrza zbiornika dla potrzeb jego uzupełniania, inspekcji i konserwacji. Kontener powinien być także zabezpieczony przed wyciekiem i wyposażony we wskaźnik zapełnienia opierający się na wynikach pomiaru z czujnika poziomu.
Zadaniem pompy jest pobranie substancji ze zbiornika i jej przetłoczenie do głowicy dozującej. Korzysta się przeważnie z jednego z trzech typów tych urządzeń. Są to pompy: membranowe, perystaltyczne albo śrubowe.
Klasyfikacja systemów dozowaniaWyróżnić można kilka trybów działania systemów dozujących. Jednym z nich jest praca ciągła, która polega zwykle na odmierzaniu jednakowych dawek danej substancji w krótkich odstępach czasu. Praktykuje się również dozowanie jednorazowo jej określonej ilości. Wówczas dozownik działa przez pewien czas nieprzerwanie albo odmierza konkretną liczbę dawek. W przypadku mieszania ze sobą dwóch albo większej liczby substancji czasem wymagane jest utrzymanie stałego stosunku ich ilości, na przykład jeżeli w systemie uzdatniania na każdy metr sześcienny wody powinno przypadać 100 ml środka chemicznego. W takim przypadku natężenie przepływu tego ostatniego powinno się zmieniać stosownie do natężenia przepływu wody. Jeżeli właściwości obu albo któregokolwiek ze składników mieszaniny lub parametry pracy systemu są zmienne, efekt końcowy może się okazać różny od zakładanego. Na przykład przy danej jakości wody dawka środka uzdatniającego może się okazać zbyt duża albo zbyt mała. Alternatywą jest uzależnienie ilości substancji dawkowanej przez dozownik, na przykład chloru, od aktualnych właściwości substancji podstawowej, w tym przypadku jakości wody. Jest to konieczne, jeżeli pochodzi ona z różnych źródeł. Z drugiej strony dozowanie proporcjonalne może okazać się lepszym rozwiązaniem, jeśli jego skutek jest mierzalny z opóźnieniem spowodowanym na przykład długością instalacji przesyłowej i/albo rozmiarami zbiorników, w opisanym przykładzie, wody pitnej. |
Pompy membranowe
W pierwszych membranę wprawia w ruch element poruszający się w sposób posuwisto-zwrotny. Z każdym jej przesunięciem zmianie ulega objętość komory roboczej pompy, a określona ilość odmierzanej substancji na przemian jest zasysana wlotem ze zbiornika do komory i wtłaczana wylotem z komory do rurociągu dozownika.
Przepływ zatem nie jest ciągły, a raczej impulsowy. Pompy tego typu są zwykle wyposażone w czujnik ciśnienia sygnalizujący przerwanie membrany. Aby zwiększyć jej wytrzymałość na uszkodzenia, wykonuje się ją jako wielowarstwową.
Membrana może być wprawiana w ruch na różne sposoby. Dostępne są na przykład pompy membranowe z napędem elektromagnetycznym. Do ich zalet zalicza się: łatwość instalacji i sterowania. Są też zwykle w porównaniu z innymi tańsze. Chociaż zapewniają duże ciśnienie tłoczenia, mają zazwyczaj niską wydajność. Ponadto w zestawieniu z droższymi alternatywami charakteryzuje je krótsza żywotność.
W pompach membranowo-tłokowych (membranowych hydraulicznych) membrana poruszana jest pod wpływem oddziaływania wypieranej przez tłok cieczy hydraulicznej. Wyróżnia je: duża dokładność, długa żywotność oraz możliwość dozowania substancji trudnych do tłoczenia, na przykład zawiesin.
Z drugiej strony są przeważnie droższe i mają ograniczoną wysokość ssania. Wymagają też częstszej konserwacji i większej uwagi z powodu obecności cieczy hydraulicznej.
Pompy membranowe z napędem silnikowym są rozwiązaniem pośrednim pod względem ceny, żywotności oraz złożoności konserwacji. W porównaniu z pompami hydraulicznymi wypadają jednak gorzej pod względem dokładności oraz zdolności tłoczenia. Maszyny te sprawdzają się najlepiej w prostych systemach dozowania, o ograniczonych wymaganiach w zakresie regulacji wydajności tłoczenia.
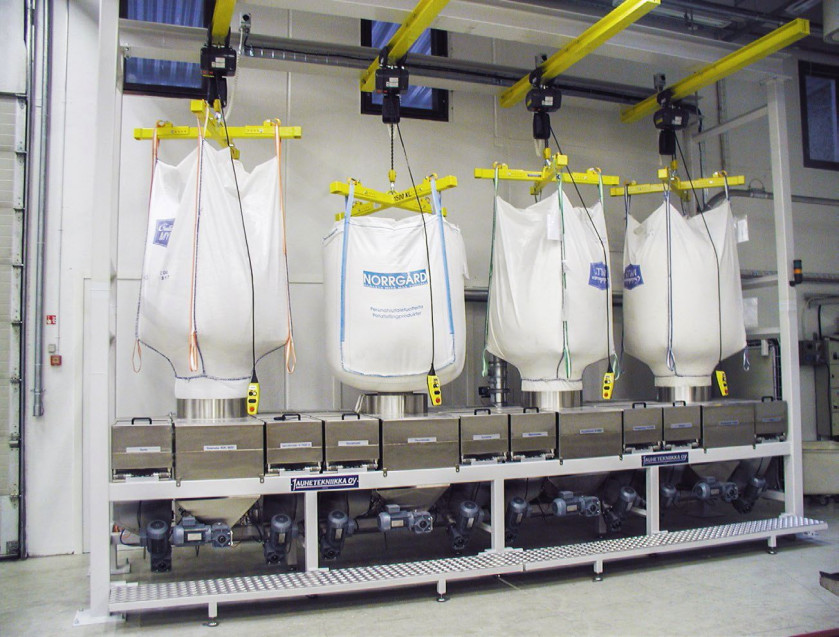
Pompy perystaltyczne i śrubowe
W pompach perystaltycznych dozowana substancja przemieszcza się elastycznym przewodem pod wpływem nacisku, jaki jest na niego wywierany przez obracające się rolki. Brak ruchu posuwisto-zwrotnego sprawia, że przepływ jest ciągły. Dzięki nieobecności wewnętrznych zaworów pompy tego typu sprawdzają się w tłoczeniu na przykład cieczy zawierających cząstki stałe i związków chemicznych uwalniających gazy.
Ponadto mają dużą wysokość ssania, co pozwala na montaż pompy powyżej zbiornika i w znacznej odległości od niego. Dzięki temu, że dozowana ciecz kontakt ma jedynie z przewodem pompy, łatwiej jest zapewnić kompatybilność między nią a materiałem, z jakiego go wykonano.
Maszyny tego typu mają również zazwyczaj wbudowane zabezpieczenie wykrywające uszkodzenie przewodu, które może doprowadzić do przecieku. Do wad pomp perystaltycznych zalicza się: ograniczone ciśnienie tłoczenia i konieczność okresowej wymiany przewodu, który z czasem ulega zużyciu.
Pompy śrubowe (ślimakowe) na tle pozostałych wyróżnia bezpulsacyjne dozowanie. Poza tym sprawdzają się w tłoczeniu ścieków, produktów silnie lepkich i zawierających cząstki stałe, jak przykładowo: sosy, lody z twardymi dodatkami, pasty o właściwościach abrazyjnych oraz tych, których struktura może ulec uszkodzeniu w czasie pompowania, m.in.: lodów, jogurtów, maślanki. Z drugiej strony charakteryzują je ograniczone możliwości regulacji wydajności oraz znaczny koszt zakupu i konserwacji.
Głowice, pompy wielogłowicowe i komponenty pomocnicze
Komponentem pomp o kluczowym znaczeniu dla działania systemu dozowania jest głowica odmierzająca. Powinna ona zapewnić precyzyjne dawkowanie. Ponadto materiały, z jakich jest wykonana, muszą się charakteryzować wytrzymałością na kontakt z dozowanymi substancjami, odpowiednią do stopnia natężenia ich oddziaływania chemicznego i mechanicznego. Głowica powinna być również odporna na temperaturę i ciśnienie robocze w danej instalacji.
Jeśli za jej pośrednictwem mają być odmierzane substancje toksyczne, żrące, lotne lub jakiekolwiek inne, które nie mogą się wydostać na zewnątrz głowica musi być zabezpieczona przed wyciekiem. Jeśli w temperaturze pokojowej nie są płynne, jak na przykład tłuszcze, trzeba je podgrzewać przez ogrzewanie głowicy oraz rurociągów, którymi są przenoszone. Korzysta się w tym celu z płaszczy grzewczych, a jeżeli wymagane jest obniżenie temperatury - z płaszczy chłodzących.
Zamiast tworzyć instalację z wielu oddzielnych pomp dozujących, co zwiększa koszty inwestycji, utrzymania oraz stopień komplikacji, czasem warto jest rozważyć użycie pomp wielogłowicowych. Przykładem takiej sytuacji jest dozowanie wielu składników według określonej receptury.
Dzięki wspólnemu napędowi łatwiej jest wówczas o utrzymanie określonego stosunku ilości odmierzanych substancji, nawet w przypadku wahań natężenia przepływu, które będą jednakowe we wszystkich głowicach lub awarii silnika, która wstrzyma dopływ wszystkich substancji jednocześnie.
Częścią systemów dozowania jest także szereg komponentów dodatkowych, od których zależy ich niezawodne i bezpieczne działanie oraz łatwość konserwacji. Przykładami takich są: zawory, które chronią pompy i inne elementy instalacji przed nadmiernym ciśnieniem, przepływomierze, które kontrolują ilość odmierzanych substancji, tłumiki ze sprężonym gazem, które ograniczają pulsacje ciśnienia na wylocie pompy, rurociągi, którymi przepływa dozowana substancja, filtry, na których zatrzymują się zanieczyszczenia, które nagromadzając się, mogłyby blokować pompy i zawory oraz systemy spłukiwania, które usuwają resztki odmierzanych substancji, co pozwala na bezpieczną konserwację instalacji.
Dawkowanie wolumetryczne i wagoweDozowniki można podzielić na wolumetryczne oraz wagowe. Pierwsze odmierzają ilość substancji na podstawie jej objętości. Wartość tej wielkości jest w przypadku wielu procesów produkcyjnych mniej istotna niż masa, lecz z drugiej strony można ją wyznaczyć i dozować precyzyjniej. Ponadto charakteryzuje pojemność zbiorników i przepustowość instalacji przesyłowych. O tym, czy można skorzystać z dozownika wolumetrycznego, ostatecznie decyduje jednak gęstość substancji. Jest ona miarą jej ilości w danej objętości. W przypadku cieczy można założyć, że zmiana wartości tej wielkości przy zmianie temperatury i/albo ciśnienia jest pomijalnie mała, w gazach natomiast gęstość silnie zależy od wartości tych dwóch wielkości. W rezultacie jednostka objętości gazu przy zmniejszeniu dostępnej dla niego przestrzeni o połowę stanie się dwukrotnie cięższa. Jeżeli zaś chodzi o materiały sypkie, ich gęstość zależy od tego, jak ściśle upakowane zostaną ich cząstki. W rezultacie mocno ubity proszek będzie miał większą gęstość niż luźny. Ponadto ma na nią wpływ ich higroskopijność, od której zależy stopień zawilgocenia. W związku z tym dozowniki wolumetryczne są zwykle używane do odmierzania cieczy. Ponieważ wagowe nie wchodzi w grę, system dozowania objętościowego gazów musi uwzględniać wpływ zmian temperatury i ciśnienia lub umożliwiać ich regulację. Z kolei materiały sypkie są zazwyczaj odmierzane przez dozowniki wagowe, w których każda porcja jest oddzielnie ważona. Wyróżnia się zasadniczo dwa typy dozowników wagowych. W pierwszych kontroluje się ubytek wagi zbiornika z odmierzaną substancją (systemy loss in weight), natomiast w drugich monitoruje się przyrost wagi napełnianego pojemnika (gain in weight). |
Stan skupienia i lepkość oraz mieszaniny
Wybierając komponenty systemu dozowania, trzeba wziąć pod uwagę właściwości odmierzanej substancji. Jedną z najważniejszych jest jej stan skupienia - stały, ciekły albo gazowy. Każdy z nich ma swoją specyfikę i właściwości, na które trzeba zwrócić szczególną uwagę.
Na przykład ciecze i gazy są mniej lub bardziej płynne. Stopień płynności charakteryzuje lepkość - im jest większa, tym dana substancja jest mniej płynna. W systemach dozowania lepkość gazów ma mniejsze znaczenie niż ta cecha cieczy, w przypadku których od niej zależy rzeczywista osiągalna wydajność pompy dozującej.
Trzeba przy tym pamiętać, że choć na lepkość niektórych cieczy nie ma wpływu prędkość przepływu, dla wielu taka zależność występuje. Część z nich charakteryzuje duża lepkość, kiedy nie są w ruchu, zaś w przeciwnym wypadku ich płynność rośnie. W przypadku cieczy, dla których zależność ta jest odwrotna, poza tłoczeniem utrudnione może być też mieszanie.
Projektując systemy dozowania mieszanin, trzeba się orientować w specyfice roztworów, zawiesin oraz emulsji. Inaczej niż w roztworach, w zawiesinach cząstki nie są rozpuszczone, lecz unoszą się swobodnie albo mają tendencję do opadania. Z jednej strony, im większa jest prędkość przepływu zawiesiny, tym większe prawdopodobieństwo, że jej twarde drobiny mogą uszkodzić ściany pomp i innych komponentów systemu dozowania przez ścieranie.
Z drugiej strony wówczas mniej cząstek opada, gromadząc się i tworząc zatory. Emulsje powstają z kolei przez mechaniczne zmieszanie cieczy normalnie niemieszających się. Dlatego, bez dodatku emulgatorów, mogą ulec rozdzieleniu na składniki, jeżeli przez dłuższy czas nie będą mieszane.
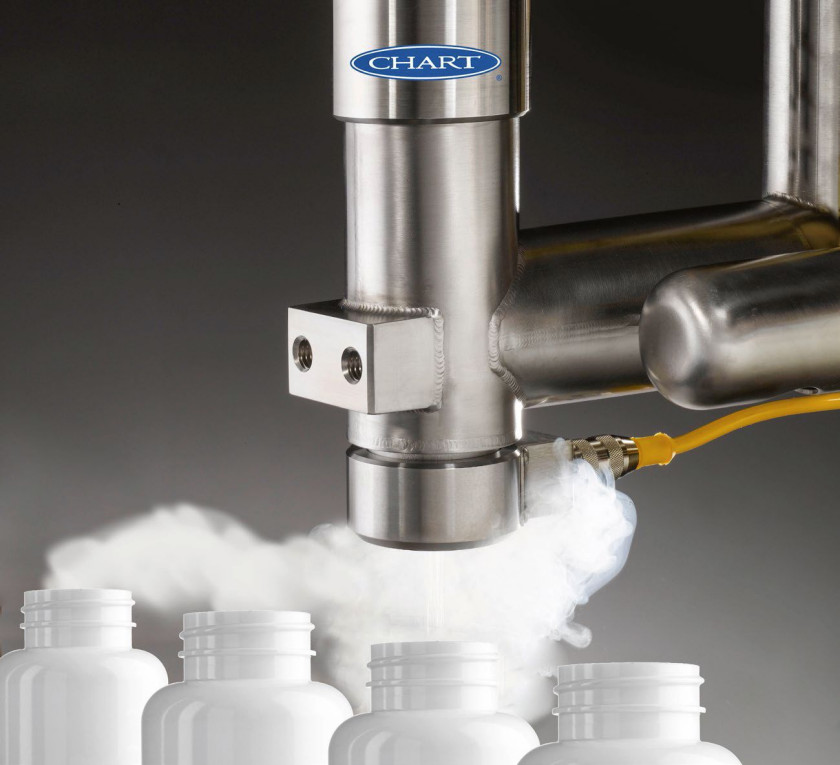
Materiały sypkie - zmiana stanu skupienia
Substancje w stanie stałym w systemach dozowania to przede wszystkim materiały sypkie. Zalicza się do nich te sproszkowane, granulaty i generalnie o średnicy cząstek nieprzekraczającej kilku milimetrów.
Zgromadzone w dużej ilości zachowują się w uproszczeniu jak ciecze, przypominając je tym bardziej, im szybciej się przemieszczają. Wówczas jednak należy się liczyć z nasileniem się ich niszczącego działania na ściany wewnętrzne instalacji dozowania. Inaczej niż ciecze materiały sypkie mają też tendencję do zlepiania się oraz tzw. mostkowania, co blokuje przepływ.
W takich sytuacjach stosuje się specjalne rozwiązania, które pozwalają na przywrócenie płynności ich przemieszczania się, na przykład przez wstrząs, wymieszanie albo przedmuchanie powietrzem lub gazem neutralnym, na przykład azotem. Mogą być też higroskopijne. Absorpcja wody może powodować ich sklejanie się, również blokując przepływ, zaś wilgoć dodatkowo sprzyja korozji elementów systemu dozowania.
Trzeba pamiętać, że w zależności od warunków, temperatury i ciśnienia, stan skupienia się zmienia. Jak wiadomo, przykładowo woda przy ciśnieniu atmosferycznym w temperaturze niższej niż 0°C zamarza, w zakresie od 0 do +100°C jest cieczą, zaś powyżej +100°C odparowuje. Niestety nie zawsze przedziały te są tak jednoznaczne - sprawa komplikuje się m.in. w przypadku mieszanin, ich składniki mogą bowiem odparowywać i krzepnąć w różnych temperaturach.
Znajomość warunków, w jakich te zjawiska zachodzą, jest ważna przy wyborze pompy dozującej. Na przykład temperatura i ciśnienie wrzenia determinują wysokość ssania, a wiedząc, czy w razie wycieku ciecz odparuje, można lepiej przewidzieć jego skutki, a na tej podstawie zdecydować o wymaganym stopniu szczelności pompy.
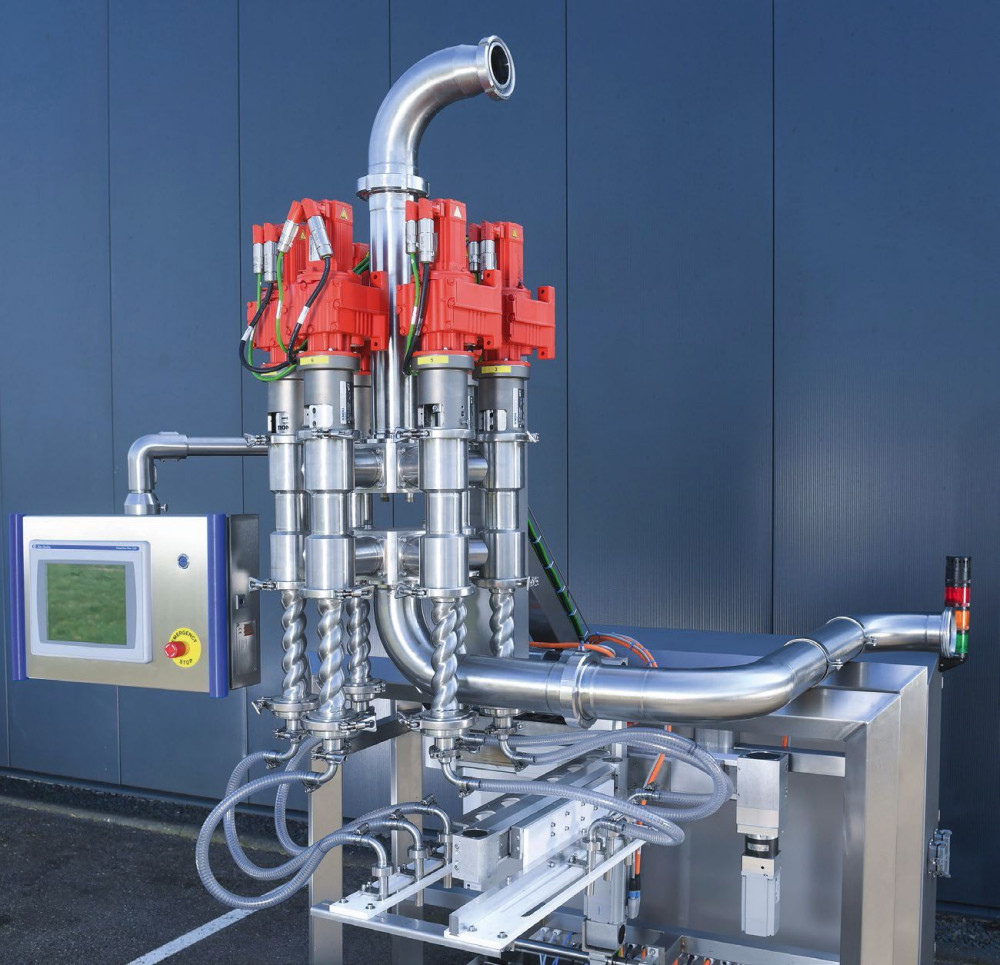
Reaktywność i wybuchowość dozowanych substancji
Kolejną ważną cechą dozowanej substancji jest agresywność chemiczna charakteryzująca zdolność do korodowania powierzchni, z którymi ma kontakt. Koniecznie trzeba ją uwzględnić, wybierając pompy, rurociągi oraz armaturę systemu odmierzania.
Miarą reaktywności jest m.in. wskaźnik pH. Jeżeli wynosi około 7, jest neutralne, gdy jest mniejsze niż 7, świadczy o odczynie kwasowym, zaś większe - zasadowym. Przykładowe wartości dla różnych cieczy to: kwas solny - 0, sok cytrynowy - 2,4, piwo - 4,5, mleko - 6,5, mydło - 9‒10, woda amoniakalna - 11,5, soda kaustyczna - 14.
Szczególnej uwagi z dwóch powodów wymagają także ciecze, które uwalniają gazy. Pierwszym z nich jest troska o bezpieczeństwo osób przebywających w pobliżu w razie nieszczelności instalacji dozowania, jeżeli wydzielany gaz jest dla ludzi szkodliwy. Poza tym, jeżeli pompy, rurociągi i inne komponenty są przystosowane do transportu tylko cieczy, gazy mogą zablokować ich działanie.
Wybuchowość ma z kolei kluczowe znaczenie dla bezpieczeństwa pracy systemu odmierzania. Gdy wiadomo, że dany gaz, pary cieczy, pył tworzą z powietrzem wybuchową mieszankę lub dozowana substancja jest w takiej postaci, w której nadmierny wzrost temperatury albo silne uderzenie mogą zapoczątkować pożar lub wybuch, powinno się korzystać z maszyn przystosowanych do pracy z takimi materiałami, czyli spełniających wymogi normy ATEX dla danej kategorii zagrożenia. Pod kątem wymienionych właściwości powinno się wybierać sprzęt systemu dozowania, z kolei sposób odmierzania determinuje przede wszystkim aplikacja. Omówienie tego zaprezentowano w ramkach.
Monika Jaworowska
Zdjęcie tytułowe: Nowa linia do produkcji detergentów firmy Henkel znajdująca się w zakładzie działu Laundry & Home Care w Raciborzu (źródło: Henkel)