By tę kwestię unormować, w miarę jak roboty współpracujące się upowszechniały, rozpoczęto prace nad stosownymi standardami. Pierwszym dokumentem, w którym zostały przedstawione wymagania bezpieczeństwa dla aplikacji robotów współpracujących, był opublikowany w 2016 roku standard ISO/TS 15066. Uzupełniał on zalecenia dotyczące bezpiecznej współpracy z cobotami przemysłowymi, które zostały już podane w specyfikacjach ISO 10218-1 oraz ISO 10218-2. Planowana na ten rok aktualizacja tych ostatnich będzie uwzględniać wytyczne przedstawione w dokumencie ISO/TS 15066.
Tryby pracy cobotów
W standardach dotyczących bezpieczeństwa aplikacji z robotami współpracującymi za nadrzędny cel uznano to, by do zetknięcia pracownika z robotem nie doszło lub gdy kontakt między pracownikiem a robotem jest dozwolony i przypadkowo albo celowo do niego dochodzi, nie powodował on u takiej osoby obrażeń ani bólu. Założenia te można osiągnąć, wdrażając na zrobotyzowanym stanowisku jeden z zalecanych przez standardy ISO trybów kooperacji cobota z jego ludzkimi współpracownikami.
W tym zakresie wyróżniono cztery scenariusze. Są to: praca z dostępną funkcją bezpiecznego kontrolowanego zatrzymania robota (Safety-rated Monitored Stop, SMS), prowadzenie ręczne (Hand Guiding, HG), praca z zapewnieniem monitorowanej prędkości i odległości człowieka i robota (Speed and Separation Monitoring, SSM) oraz praca przy ograniczonej sile i mocy robota (Power and Force Limiting, PFL).
Jako pierwsze przedstawiamy coboty, które realizują ostatni z wymienionych trybów pracy. To bowiem właśnie z nimi generalnie najczęściej utożsamiane są roboty współpracujące.
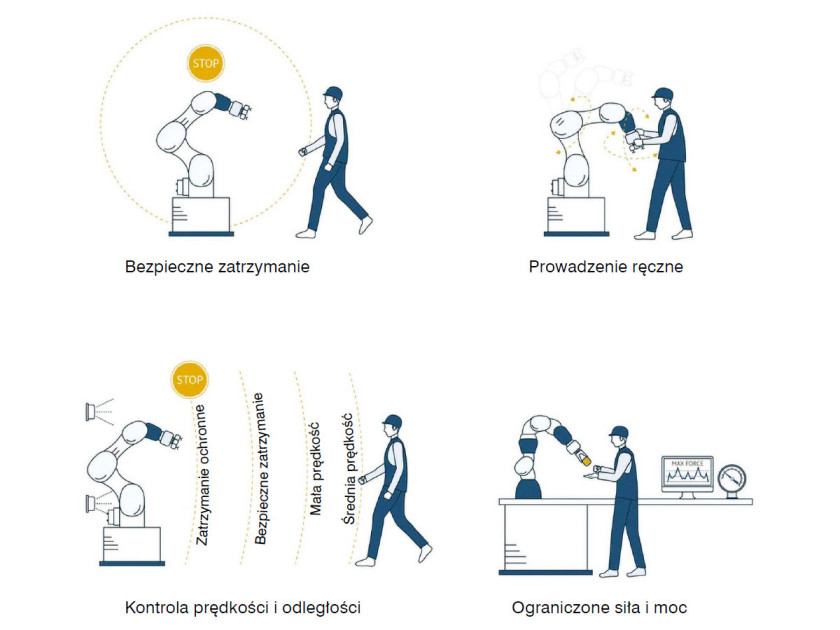
Co wyróżnia tryb PFL?
W trybie pracy z ograniczoną siłą i mocą cobota maszyna taka może bezpiecznie współpracować z ludźmi, gdyż w przypadku kontaktu z czymkolwiek zatrzymuje się. W związku z tym robot na takim stanowisku koniecznie powinien być wyposażony w czujnik dotykowy, który wykryje jego zderzenie z innym obiektem. W tym zastosowaniu wykorzystuje się sensory różnego typu.
Przykładem są czujniki siły i momentu wbudowane w przeguby robota. Monitoruje się także natężenie prądu silników napędów w tych ostatnich. Umieszczanie sensorów w tym elemencie robota jest jednym z popularniejszych rozwiązań. Czujniki siły i momentu są ponadto montowane w podstawach cobotów. Dzięki temu na przykład, jeżeli jest on zaprogramowany do wykonywania zadania w jednym kierunku, zatrzyma się, jeżeli natknie się na przeszkodę, gdyż sensor siły wykryje jej nieprawidłową składową. Jest to podejście popularne w przystosowywaniu zwykłych robotów przemysłowych do współpracy z ludźmi. W tym celu obudowuje się je także osłonami ("skórą") wyposażonymi w sensory ciśnienia, które wykrywają zmianę tej wielkości spowodowaną odkształceniem w wyniku kontaktu z innym obiektem.
Jak wytłumić uderzenie?
W związku z tym, że w tym trybie pracy kontakt między człowiekiem a robotem jest dopuszczalny, powinien on być maksymalnie dla ludzi bezpieczny. Dlatego, by ograniczyć potencjalne obrażenia, roboty tego typu muszą poruszać się bardzo wolno i mogą pracować jedynie przy ograniczonym udźwigu. Oprócz tego mają zwykle bardziej zaokrąglone kształty niż zwykłe roboty przemysłowe. Taka konstrukcja zapewnia rozłożenie siły uderzenia na większej powierzchni, a dzięki temu zmniejszenie nacisku wywieranego na obiekt, z którym robot się zetknął.
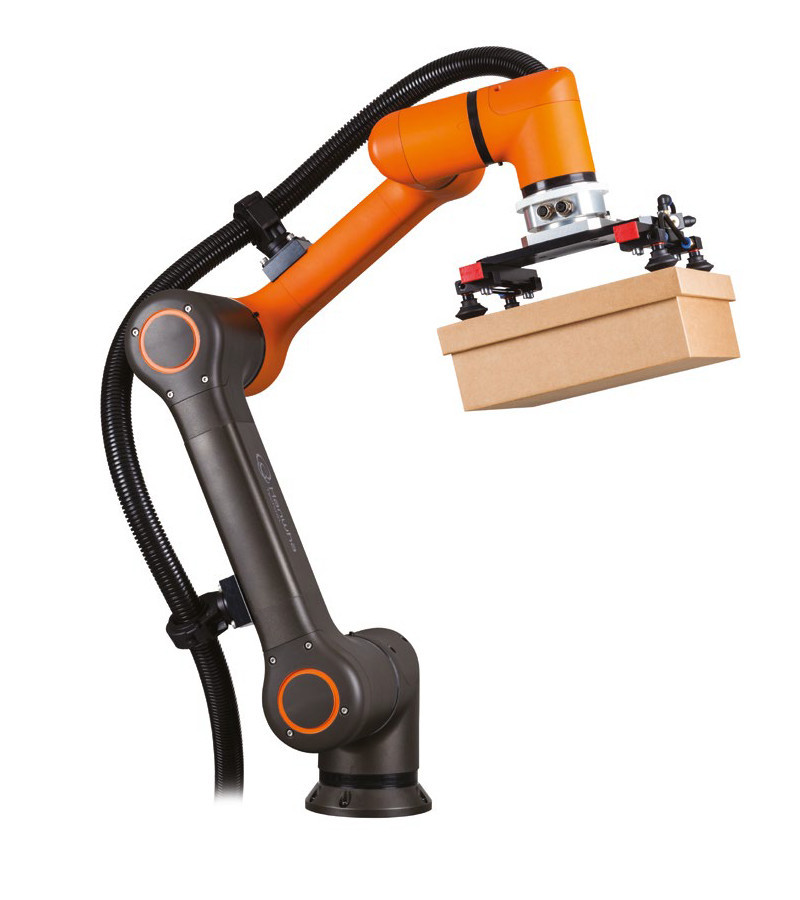
Stosowane są również specjalnie wykonane podkładki (elastyczne, grube), które amortyzują uderzenia, nie dopuszczając do przekroczenia maksymalnych dopuszczalnych poziomów siły i nacisku na ludzkie ciało. Limity te zostały podane w standardzie ISO/TS 15066. W normie tej zebrano także wytyczne w zakresie określenia maksymalnej dopuszczalnej prędkości na stanowiskach z tego typu cobotami.
Fakt, że praca w trybie PFL wymaga zmniejszenia do bezpiecznych wartości prędkości i udźwigu, sprawia, że zakres zadań, w których tego typu roboty mogą współpracować z ludźmi, znacząco się zawęża. Ponadto bezpieczeństwo kooperacji nie może być zagwarantowane, jeśli są one wyposażone w niebezpieczne narzędzia albo ładunek lub na danym stanowisku występują inne zagrożenia, jak na przykład podczas obsługi niebezpiecznej maszyny, takiej jak prasa albo wtryskarka.
Na czym polega SSM?
Alternatywą dla współpracy przy ograniczonej sile i mocy robota jest kooperacja z zapewnieniem monitorowanej prędkości i odległości człowieka i robota. W tym przypadku cobot i pracownik mogą poruszać się jednocześnie we wspólnej przestrzeni roboczej dzięki temu, że ryzyko ich zetknięcia się ze sobą jest ograniczane do minimum. Osiąga się to, ponieważ przez cały czas gwarantowane jest utrzymanie pomiędzy nimi co najmniej ustalonej bezpiecznej odległości (Protective Separation Distance, PSD).
Jeżeli dystans pomiędzy robotem, a pracownikiem zmniejszy się poniżej odległości, przy której jeszcze nic mu nie zagraża, maszyna natychmiast automatycznie wyhamowuje, do czasu, aż człowiek oddali się od niej przynajmniej na odległość równą PSD. W praktyce więc w tym scenariuszu kontakt pomiędzy robotem w ruchu a jego ludzkim współpracownikiem jest niedozwolony, ponieważ zakłada się, że poruszający się robot stanowi zagrożenie, natomiast spowolniony jest bezpieczny.
Jaki jest optymalny dystans PSD?
Aby zawsze było możliwe zatrzymanie robota przed kontaktem z człowiekiem, odległość PSD musi uwzględniać czas hamowania tej maszyny i dystans, jaki w tym czasie zdąży ona pokonać, a także odległość, jaką ludzie mogą przebyć w czasie, gdy robot będzie hamował. Co istotne, PSD jest powiązane z prędkością robota – im jest ona mniejsza, tym odpowiednio maleje też wymagany bezpieczny dystans.
Generalnie zakres zadań, w których tego typu coboty mogą współpracować z ludźmi, jest większy niż w przypadku trybu PFL, nie dotyczą ich bowiem tak rygorystyczne ograniczenia w zakresie prędkości, udźwigu, konstrukcji narzędzi. Przykładowe realizacje trybu SSM obejmują wykorzystanie systemów wizyjnych lub skanerów laserowych, które monitorują przestrzeń roboczą, w połączeniu z algorytmami przetwarzania danych pomiarowych, które analizują wzajemne położenie cobota i ludzi. Roboty obudowuje się również osłonami ("skórą") z wbudowanymi czujnikami pojemnościowymi, które wykrywają obecność człowieka w określonej odległości.
Bezpieczny stop i kontrola ręczna
Praca z dostępną funkcją bezpiecznego kontrolowanego zatrzymania robota oraz prowadzenie ręczne to tryby, w których, jak się wydaje, nie można w pełni odczuć korzyści, jaką jest w stanie przynieść współpraca na jednym stanowisku cobota z człowiekiem. W pierwszym przypadku jest on bowiem zatrzymywany, zanim operator znajdzie się albo będzie narażony na jakiekolwiek zagrożenie we wspólnej przestrzeni roboczej. Jest to równoważne funkcji bezpiecznego stopu 2 (SS2) według specyfikacji IEC 61800-5-2.
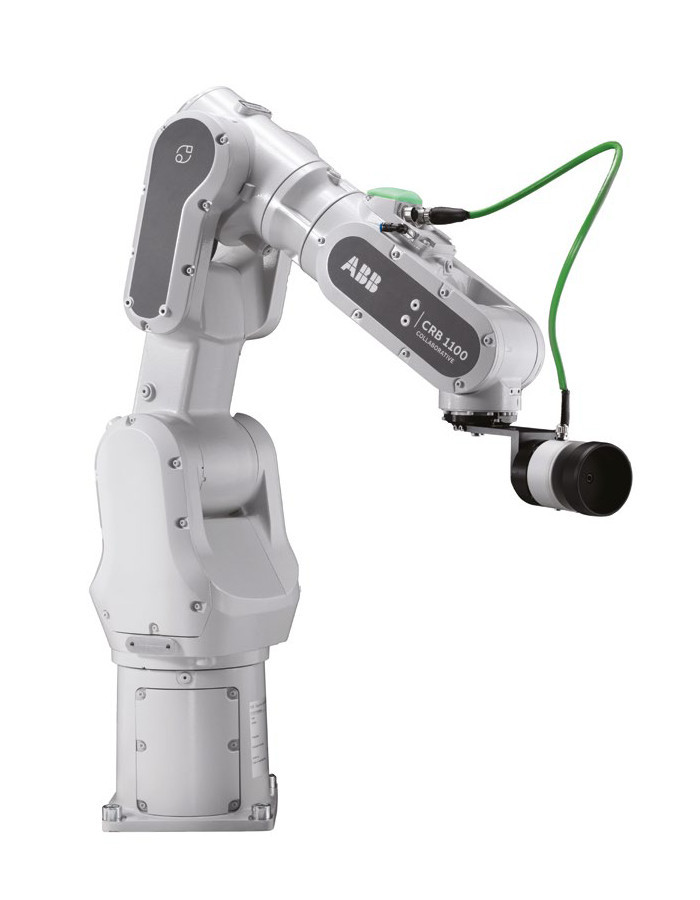
Z kolei w trybie kontroli ręcznej ruch robota jest wymuszany przez operatora, poruszającego ramieniem cobota, posługującego się manipulatorem albo aktywującego stosowne elementy sterownicze. Prędkość ruchu cobota jest wówczas bezpieczna dla człowieka.
Za podstawową aplikację trybu prowadzenia ręcznego uważa się poruszanie robotem w celu wskazania mu punktów albo poprowadzenia go ścieżką, które są niezbędne do zrealizowania wykonywanych przez niego operacji na etapie jego programowania. Jest to ważne zastosowanie tej funkcji, lecz niejedyne. Innym przykładem jest stanowisko przenoszenia obiektów, na przykład z miejsca ich składowania na stanowisko ich dalszej obróbki.
W tym przypadku robot na początku każdego cyklu pracuje autonomicznie, pobierając ładunek na przykład z regału, dzięki czemu odciąża operatora na tym powtarzalnym i wymagającym wysiłku fizycznego etapie. Następnie cobot przechodzi w tryb pracy prowadzenia ręcznego, pod kontrolę operatora. Ten prowadzi go na stanowisko montażu, gdzie ładunek jest pozostawiany. Tam operator może zająć się jego obróbką, w czasie gdy robot, ponownie po przełączeniu w tryb autonomiczny, powraca do regału. Dzięki temu, że operator nie musi samodzielnie pobierać części ze składu, może poświęcić więcej czasu i sił na wykonanie właściwej pracy, a jednocześnie prowadząc cobota, reguluje tempo dostaw detali do obróbki stosownie do swoich możliwości.
Podsumowanie
Roboty współpracujące mają wiele zalet. Cenione są przede wszystkim za łatwość programowania, szybki montaż i konfigurację, łatwość przestrojenia, a ponieważ często są lekkie i mają niewielkie rozmiary w porównaniu ze "zwykłymi" robotami przemysłowymi, zajmują też mniej miejsca. To pozwala lepiej zagospodarować dostępną przestrzeń roboczą. Poza tym dzięki temu łatwo jest je przenieść z jednego stanowiska na drugie, bez konieczności wprowadzania większych zmian w istniejącej konfiguracji wyposażenia. Oprócz tego pozwalają na zrezygnowanie z barier, klatek i innych środków bezpieczeństwa.
Tutaj jednak ważna uwaga – eksperci ostrzegają, że nie robot decyduje o tym, że pracownik może się znaleźć w jego bezpośrednim sąsiedztwie bez obawy o swoje zdrowie i życie, lecz aplikacja. Dlatego, żeby zapewnić bezpieczne środowisko pracy, najpierw powinno się przeprowadzić staranną oraz poprawną analizę ryzyka, która potwierdzi, że współpraca na linii robot–człowiek w realizacji danego zadania będzie naprawdę bezpieczna.
Monika Jaworowska